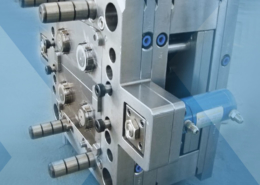
What are 2K Injection Molding and 2K Molding Equipment ... - 2k molding
Author:gly Date: 2024-10-15
Our extensive experience in injection molding services began with molding engineered resins in 1988 and expanded into highly contoured silicone components using liquid injection molding (LIM) in 2006. Since 2009, we have built expertise in true micro molding, and today we regularly produce molded components that are smaller than the resin pellet itself. Our state-of-the-art facilities support continued innovation in our injection molding services, including specialized tools, techniques and materials.
The quality of a product is only as good as the quality of its tooling. Your SMC tooling plan will support the needs of the project for your short-term requirements, your long-term expectations and your speed-to-market and scale-up goals. All tools built by SMC run in an SMC molding facility, and every SMC molding facility provides ongoing maintenance for the tools. More about our tooling capabilities.
Injection molding is a core strength of our end-to-end medical manufacturing capabilities, allowing us to provide all necessary injection-molded components for your medical device. Along with in-house expertise in design for manufacturability (DFM) and part processing, we design and build injection molding tools in-house.
Our advanced medical injection molding capabilities allow us to mold precision parts with complex geometries, provide rapid prototyping, scale up manufacturing to high volume with state-of-the-art automation and assembly, and deliver it all efficiently. As an engineering-driven company providing custom manufacturing solutions for the healthcare industry, we have invested in the right people, processes and facilities to de-risk the process of manufacturing the highest-quality injection-molded components.
Precision matters when it comes to manufacturing micro molded medical parts, from tooling design through inspection and integration into the device. SMC manufactures even the smallest parts while holding precise tolerances. Our in-house tooling department is equipped to provide custom micro-prototyping and production molds, and our efficient material and tooling techniques deliver exceptional yields of 10,000 parts per pound, including the runner. More about our micro/mini capabilities.
The overmolding injection molding process involves adding material (overmold) to a rigid part (substrate) such as metal or plastic to form around it.
Copyright ©2023 SMC Ltd. All rights reserved. SMC and the SMC logo are registered trademarks of SMC Ltd. Privacy and Cookie Policy UnitedHealthcare’s Transparency in Coverage
Delmon Group has almost 60 years of experience in researching and producing new and innovative solutions for all kinds of industries.
At SMC, we have repeatedly proven that complex silicone parts can be produced in nearly half the lead time of traditional silicone molding options. With capabilities that range from up-front product development through the introduction of finished devices, we can bring your silicone program to market in the shortest time with the most predictable outcome. More about silicone capabilities.
The advantages of this process are multiple. They can be seen both in the production process and in the quality of the final product.
– In terms of product durability, overmolding is recommended because its process creates a chemical bond between the substrate and the material called « bonding ». This effect allows to create a better link between a substrate and a material. Bonding replaces gluing or fixing and guarantees optimal durability.
Thermoplastics are the basis of every single-use device we manufacture. We specialize in components with complex geometries and challenging quality requirements, and our molding processes are validated using IQ/OQ/PQ protocols. Using scientific molding practices, we assure premium components with each press cycle. More about our thermoplastics capabilities.
– Overmolding considerably reduces the need for secondary operations by avoiding manual assembly between two molded parts. Operators then have more time to perform other tasks, which lowers production costs.
GETTING A QUOTE WITH LK-MOULD IS FREE AND SIMPLE.
FIND MORE OF OUR SERVICES:
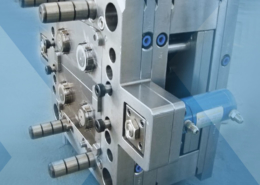
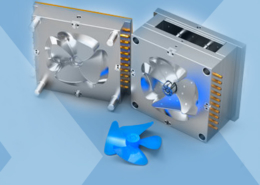
Plastic Molding

Rapid Prototyping
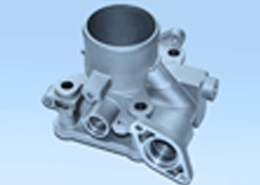
Pressure Die Casting
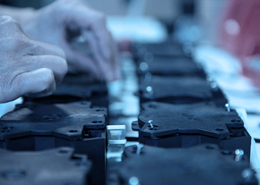
Parts Assembly
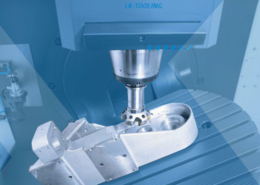