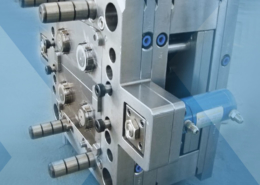
What are 2K Injection Molding and 2K Molding Equipment ... - 2k injection moldin
Author:gly Date: 2024-10-15
A different approach to dual-material molding is co-injection molding, which involves injecting two materials into a mold cavity. One material forms the "skin" or outer layer, while the other forms the internal "core." Unlike two-shot molding or overmolding, co-injection molding only requires a single mold cavity.
Engineers often need different material properties in different regions of a part, and they can achieve this in various ways. Traditionally, parts are designed as separate components that can be assembled using glue or fasteners. For example, one component may be made from a soft, pliable material, while another might be made from a rigid thermoplastic. In the realm of injection molding, a useful technique is overmolding, where one layer of material is molded over another, resulting in a two-part molding with different materials or colors.
Enhanced Part Performance: One of the most significant benefits is the range of engineering possibilities that can improve part performance. Combining two sets of material properties in a single molded part can address various functional needs. Examples include parts with a foam core to reduce weight and provide acoustic insulation or parts with a glass-filled core for increased strength and stiffness.
These micro medical components were injection molded using Ultem, an amorphous thermoplastic polyetherimide (PEI) resin with a high melt temperature. Ultem is a high-strength polymer that flows better than PEEK, but not as easily as Polycarbonate.
Material Compatibility: Not all polymers are suitable or mutually compatible for co-injection. The core material typically needs to be more viscous than the skin material.
This article covers the basics of co-injection molding, explaining how the process works, its main advantages and challenges, and common applications.
Cost Efficiency: Parts can be made with a high-quality skin material and a low-cost core, significantly reducing unit costs. While setup costs for co-injection can be high, these savings become significant during high-volume production.
Aesthetic Possibilities: Co-injection allows for aesthetic enhancements, as the skin can be made from a cosmetically appealing material while the core serves a functional purpose. It also enables unique effects such as color gradation, useful in producing eye-catching packaging.
Limited Material Placement: Unlike two-shot molding or overmolding, co-injection molding cannot selectively place material regions. The skin must cover the entire outer surface of the part.
Co-injection molding (sometimes called sandwich molding) is a form of injection molding where two injection units inject different materials into one mold. When a suitable combination of materials is used, one forms the outer skin, and the other forms the internal core. This method allows the creation of parts with distinct materials in the same mold, enabling a range of possibilities while maintaining short cycle times.
The co-injection process requires a multi-material injection molding machine or an additional injection unit for the second material. The best results are usually achieved using a hot runner system, which allows precise metering and temperature control to inject the two materials into the mold cavity sequentially. A cold runner system with a manifold can also be used.
Complex Setup: Co-injection molding requires a multi-injection setup, which can be expensive and demands a high level of expertise to operate.
Cycle Time Efficiency: Co-injection molding is typically faster than overmolding or assembling two separate components. Despite comprising three injection phases, it offers excellent production efficiency for multi-material parts.
First Injection: The first injection unit injects the skin material into the mold. This material cools and hardens when it reaches the mold walls. Second Injection: The second injection unit injects the core material into the mold, pushing the skin material further towards the mold walls. Since the materials are immiscible, they do not blend but form distinct layers. Optional Third Injection: The first injection unit may inject more skin material, pushing the core material inwards and sealing off the gate area with skin material, creating a sandwich molding.
Co-injection molding is a sophisticated process that offers numerous advantages in terms of part performance, aesthetics, cost, and production efficiency. However, it requires careful consideration of materials and setup costs. When executed correctly, co-injection molding can be a powerful technique for producing high-quality, multi-material parts.
GETTING A QUOTE WITH LK-MOULD IS FREE AND SIMPLE.
FIND MORE OF OUR SERVICES:
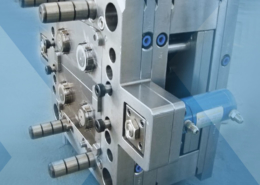
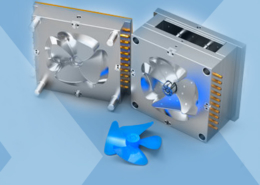
Plastic Molding

Rapid Prototyping
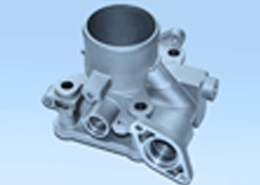
Pressure Die Casting
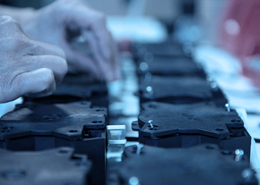
Parts Assembly
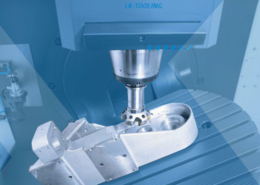