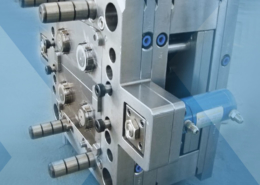
Warner Represented Century Mold in its Acquisition of ... - integrity injection
Author:gly Date: 2024-10-15
1. When cooled with water after ejection, increase the temperature of the cooling water or reduce the water-cooling time
These are the cracks that occur on the surface or the contact surface with the insert of a product. When viewed from a certain angle, it will flicker and emit light. The causes of this defect are relatively complicated, which, however, can be prevented by taking the following measures:
6. Is there any soot or dust mixed in from the vents of the hopper loader, or whether there are foreign substances generated by the hopper loader itself?
These are the voids that occur where the product wall is thick. For transparent PMMA products, they will become an exterior defect that cannot be remedied later. Insufficient drying before molding or excessive barrel temperature may cause voids to occur in areas other than the center of the thick wall. If the shrinkage is concentrated in the thick wall, voids will appear in the center of the thick wall. It can be solved by the prevention of shrinkage, or by the following measures:
When the multiple parts come out of the mold, there is a lot more handling needed to separate the parts. That typically involves a greater level of manual labor since automation doesn’t work as well in the separation process.
5. Does the strong friction between the metal wall of the hopper loader and the acrylic pellets cause the metal wall to peel off?
PMMA acrylic are widely used in all aspects of the optical field, so it is extremely necessary to prevent the mixing of impurities. Usually, there are many ways for foreign substances to be mixed in. It is time-consuming to find out the reason, but you can start with the following aspects:
This is caused because the resin does not fill the cavity fully. To prevent its occurrence, we can take the following measures:
5. Increase the cross-sectional area of the gate (main runner, branch runner, and feed port), and reduce its length, to allow the resin to flow more easily
These are the ring-shaped stripes that occur on the surface of a product and are centered around the feed port. It can be prevented by taking the following measures:
A mold is a hollow form typically made from stainless steel that has plastic injected into it to manufacture a plastic part. The plastic is inserted into the mold cavity, which is a hole in the mold shaped like the desired part. Molds are only used in mass production because of the cost involved in designing and manufacturing them. Because molds are critical to the production process, it is essential they are accurately made.
However, family molds usually aren’t balanced when they are filling out because the parts often have different shapes, which can lead to an increase in molding defects. This is one of the primary reasons why we do not build family molds at The Rodon Group.
Multi-cavity molds also allow you to make more efficient use of the cycle time and produce more parts from the same mold within the shot guarantee. At The Rodon Group, our multi-cavity molds ensure you get quality parts while maintaining precision tolerances and optimizing cycle times.
3. Are there any other resins mixed in the pre-dryer, or are there any foreign substances caused by friction between the dryer and the receiver?
The defects in the injection molding of acrylic PMMA usually include: short shot, silver streaks, sink marks, voids, jetting, weld marks, gray / black specks, cracking, warpage, and material impurity, while the preventive measures against them are usually:
A multi-cavity mold has more than one cavity of the same part, and it produces more than one part per production cycle. Because of the shorter lead time per batch, using a multi-cavity mold results in a faster completion of the desired number of parts. This increases productivity and produces a better yield rate for higher volume runs.
7. Increase the cross-sectional area of the gate (main runner, branch runner, and feed port) and reduce its length, to allow the resin to flow more easily and reduce the barrel temperature.
Next time you’re in the market for multi-cavity injection mold, consider The Rodon Group. We are a second-generation, family-owned-and-operated custom injection molder, and have been in business since 1956. With over 63 years of experience, our team has the background you need when selecting a company for your plastic injection molding project.
A family injection mold has more than one cavity cut into the mold, allowing multiple various parts with the same material to be formed in a single cycle. Each cavity usually forms a different part, which is ideal for prototype molds because of the fast molding cycles.
These are the silver-white streaks on the product surface which are generated in the feed port along the flow direction of the resin. Caused by multifaceted factors, silver streaks can be prevented by taking the following measures:
A quality mold built to last for many years is an investment. The Rodon Group fabricates the top tooling and molding capabilities in the industry. All our products are made with the strictest specifications, so you’ll never need to worry about spending extra money on repairs or maintenance. We construct mold bases and cavities from stainless steel to provide the durability you need for high performance runs.
Posted by The Rodon Group Marketing Team | 08 / 22 / 19 1 Comment
9. Increase the cross-sectional area of the gate (main runner, branch runner, and feed port) and reduce its length, to allow the resin to flow more easily.
GETTING A QUOTE WITH LK-MOULD IS FREE AND SIMPLE.
FIND MORE OF OUR SERVICES:
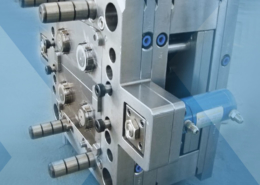
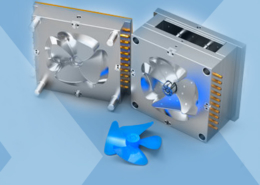
Plastic Molding

Rapid Prototyping
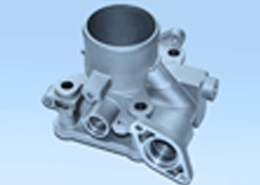
Pressure Die Casting
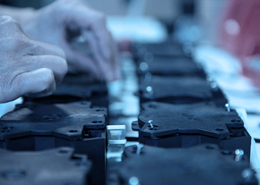
Parts Assembly
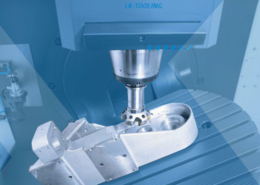