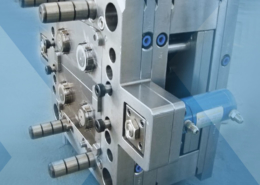
Understanding Injection Mold Costs: A Comprehensive ... - custom injection moldi
Author:gly Date: 2024-10-15
According to testing, the maximum temperature at which PEEK may be used continuously is 260 degrees Celsius, and its melting point is 341. Because of this, you can use it widely in sectors subject to high temperatures, such as the oil and gas and automotive sectors.
The volume and weight of the packaged plastic products, as well as the method of transportation, will affect transportation costs.
Among these qualities, PEEK excels in mechanical, wear, heat, and chemical strength. It can be recycled and repurposed without much hassle. High purity, corrosion resistance, and electrical insulation are additional features.
PEEK may react with several acids, including nitric solid, sulphuric, and chromic acid. This eliminates its usefulness in a few situations.
PEEK may serve dependably within the human body for long periods since it is non-toxic and does not harm living tissue. The quality makes it so useful for usage in medical implant components. However, due to its chemically inert and physiologically unresponsive nature, PEEK has a limited ability to attach to bone tissue after implantation in vivo.
The packaging of plastic injection molded products generally includes plastic bags and cardboard boxes for semi-finished parts. For assembled components, there is the cost of assembly equipment. The more complex the product, the longer the assembly time, which may result in higher costs and affect the overall expense.
Because this process produces semi-finished products that require further processing, there may be an increased risk of defects in the coating process. An economically viable suggestion is, if you want to save costs and achieve a beautiful finish, consider adding colorants directly to the raw material. This eliminates the need for secondary processing while still allowing for the production of products in various colors.
Factors affecting the cost of plastic molds include: size, complexity, material, expected quantity, and different mold cavity numbers and tolerance requirements also affect cost. For detailed mold costs, please refer to the article “Injection Mold Costs”.
We have previously detailed the costs of injection molds. For product design companies or companies outsourcing plastic part production, they are more likely to commission injection molding factories to provide plastic injection molding services for their products, rather than just commissioning the factory to produce injection molds. After all, the mold is one part of the entire injection molding production process. Therefore, they are more concerned with the injection molding costs.
PEEK may still be utilized in certain airplanes despite aluminum being the material of choice in the aerospace industry due to its reduced weight. PEEK has better recyclability than aluminum, but it is more expensive to make, which is the material’s only real drawback.
It is also important to note that there is a basic operation time for mold setup and removal. The time required depends on the size and function of the mold. If the order quantity is lower than the cost of changing the mold, there may be additional costs. However, plastic injection molding manufacturers usually clarify the minimum purchase quantity in advance.
PEEK injection molding, compared with other plastic injection moldings, needs to provide higher injection pressure, injection speed, and stable heating. In addition, you must pay attention to the mold design, so it’s best to find a professional special plastic injection factory to produce what you want. It would be better if all of these were effectively controlled from the beginning of the mold design, which can avoid unnecessary risks in production. This article is a thorough introduction to PEEK injection molding, including its types, applications, considerations, and other aspects.
I am Li Yang. If you are interested in the injection molding service quotation from FirstMold, please click “Injection Molding Service Quotation“.
Employee wages are a relatively easy part to calculate. The wages of employees involved in mold design, mold processing, etc., are calculated as part of the mold cost. However, the wages of employees in the injection molding production workshop are only calculated as part of the company’s operational costs when the customer commissions injection molding production. For example, depending on the characteristics of different products, some products may require workers to be stationed at the injection molding discharge position for processing. Common processing steps include trimming runners, visual inspections, packaging, etc.
PEEK is impervious to moisture and many different solvents (even when subjected to them in high-temperature and high-pressure steam conditions). Thus PEEK is ideal for use in the oil and gas industry, where chemicals can eat away at subsea pipes, gears, and machinery. It is resistant to jet fuel, hydraulic fluids, and de-icers, all of which are used in the aerospace industry.
It is worth mentioning that if the quantity of plastic parts produced is not large, the cost of the mold will account for a relatively large proportion of the total price; if the quantity of plastic parts produced is large enough, many factories may even waive the mold cost.
As for other complex company operational costs, each company will have its own calculation standards. These costs are usually calculated by the factory’s finance department, with a rough formula to distribute the results evenly among each injection molded part.
The operational costs of a company are very complex and include employee wages, rental costs, electricity bills, administrative expenses, etc.
Note: If the mold used for injection molding has a cold runner system, there will be residual material in the runners after each injection molding cycle. When calculating, the weight of the runner material should also be included.
The PAEK (PolyArylEtherKetone) category is the most prominent of the few high-performance polymers, with PEEK (PolyEtherEtherKetone) being the most prevalent.
The more cavities on a mold, the higher the complexity and precision of mold development, and consequently, the mold price will be higher.
With high-performance features, PEEK is one of the most popular plastic injection molding materials today because of its excellent all-around properties, which may allow it to replace traditional materials like metals and ceramics in many applications. Presently, its most common applications are in the aerospace, automotive, electrical, electronic, and medical device industries.
Of course, there is also a certain percentage of waste (e.g., 3%) during the injection molding process, but because the proportion is relatively small, it can be ignored when estimating costs.
Controlling injection molding costs is a shared responsibility between factories and product designers. The majority of methods to save on injection molding costs come from the injection molding factory. Here are some suggestions for reducing injection molding costs provided to injection molding factories as peers.
Some clients who frequently outsource injection molding production also often feel confused about how to evaluate the cost of plastic injection products, and they may doubt whether the quotations from plastic injection manufacturers are reasonable. This confusion stems from a lack of understanding of the cost structure of plastic injection products, leading to clients spending a lot of time and energy when asking for quotes from manufacturers, and sometimes they have to pay the cost of trial and error to gain experience.
If the product needs to be produced in large quantities, it is recommended to develop a mold with multiple cavities. Although the cost of mold development may be relatively higher, the production efficiency will be faster. Additionally, due to large-scale production, the unit price of the product can be reduced. Comparisons based on the number of cavities can be seen in the table below: The number of cavities represents the quantity of products produced at once, with lower costs for higher production quantities. If you are still unsure, just tell the plastic injection molding factory the estimated production volume, and an experienced plastic injection molding factory will help you calculate the most suitable number of mold cavities.
Some plastic injection molding factories also provide finishing services, including surface treatments such as coating, printing, painting, and electroplating.
Tensile strengths of 29000 psi at 299°C are possible for PEEK-based composites reinforced with carbon fibre. In this way, it outperforms nylons, acetal (PolyOxyMethylene or POM), polyesters, and polycarbonates in terms of strength and stiffness.
The cost of plastic injection molding depends on the size of the machine and the molding cycle. There are differences in processing costs, so injection molding costs can also be said to be part of the injection molding machine’s cost. The larger the machine, the more energy it consumes, which can increase the molding cost. Additionally, the shorter the production cycle, the faster the production speed.
Nave ISK-8, Parque Industrial y Logístico Sky Plus, Avenida Mineral de Cinco Señores No.100, del Parque Industrial Santa Fe, Silao de la Victoria, Guanajuato, México
You should calculate how much of a return on investment PEEK injection molding will deliver in light of its more excellent price, even though it will enable you to make lighter, stronger, and more chemically resistant components that will last longer. Prototool‘s material selection experts are here to provide a hand. With our help, even the most complex products may be designed and manufactured in weeks and brought to market.
General-purpose plastic raw materials are relatively inexpensive. If the plastic raw material has high strength and strong chemical resistance, the cost will be higher (including some modified materials).
The cost composition of injection molding is actually quite transparent in the industry, mainly including: plastic mold costs, molding costs, secondary processing costs, raw material costs, packaging and transportation costs, and factory operation costs.
PEEK is a semi-crystalline, opaque substance that belongs to the family of polymers known as PAEK, which comprises aryl, ether, and ketone chemical groups. PAEK is a subset of the PolyKetone family of polymers. PEEK’s high melting point and excellent mechanical properties come from the aryl and ketone components in its composition. PEEK’s ether group allows it to be both malleable, which contributes to its toughness, and chemically inert, providing resistance to chemical exposure.
Assuming the price of an injection molding machine is $100,000, then the daily machine cost is $100,000 / 5 / 180 = $111. If the injection molding machine works 22 hours per day, the hourly cost is approximately $5. Based on the hourly output of one injection molding machine (related to the layout of the mold and the molding time), the injection molding cost per part can be calculated.
We can calculate the annual injection molding cost based on a 5-year depreciation of the injection molding machine. For example, if the industry’s startup rate for the injection molding machine is 50% (i.e., 180 days per year), divide the annual depreciation of the injection molding machine by 180 days to calculate the daily machine cost.
The cost of raw materials depends on the functionality and requirements of the product. Common plastic raw materials include PP, PE, PC, ABS, PBT, and dozens of others. All plastic raw materials are influenced by fluctuations in the price of petroleum raw materials. If the product requires blending or colorants, the costs will be calculated separately.
Because of its large volume and surface resistivity, PEEK can maintain its excellent insulating performance even when subjected to wide swings in temperature and other environmental factors.
For example, for a mold with a 1-to-1 layout and a molding time of 60 seconds, only 60 parts can be produced in one hour. So, the machine cost per part is $100,000 / 60 = $0.08.
Several types of high-performance polymers may only fulfill a single need, such as resistance to chemicals or extreme temperatures. On the other hand, most of them fall short of meeting different standards, such as resistance to wear or mechanical strength.
PEEK has several uses in electrical engineering since it is a high-performance material that retains its mechanical properties even when heated. Therefore, we might utilize it in high-temperature electrical tools like soldering irons.
Medical analysis instruments, such as endoscope components and dental instrument cleaners, can all be made from autoclave-safe PEEK. With its high strength and low solubility, PEEK has also been used in liquid chromatography columns, tubes, and instrument analytical accessories. Due to its biocompatibility, PEEK has also primarily supplanted titanium as the metal of choice for artificial bone.
Our experts have compiled the following information about PEEK to help you decide whether it is suitable material for your project.
PEEK may be reprocessed several times without changing in any noticeable way because of the extreme stability of its molecules. Companies may reduce their waste management costs while still accomplishing their environmental goals.
Today, we will mainly introduce the cost structure of injection molding factories. If you are a peer in the injection molding industry, you are also welcome to read the latter part of the article about how injection molders can reduce injection molding costs.
While PEEK naturally has poor resistance to ultraviolet (UV) radiation, this may be remedied by using a carbon addition in the material’s composition.
With a flammability grade of UL 94 V-0, PEEK is safe to use in environments where temperatures reach over 600 °C during combustion. When burnt at high temperatures, it also creates less smoke. This is why it is so famous for making components for passenger planes.
In place of metal, PEEK resin may make lighter, fatigue-resistant, and oil-free components. This includes the separating claws of copiers, special heat-resistant bearings, chains, gears, and so on.
Studies have demonstrated that PEEK is more durable than other polymers and certain metals. PEEK is resistant to creep deformation under extreme loads and temperatures. Its low friction coefficient resists wear and tear and generates less commotion. Because of these advantages, it is an excellent option for use in automotive parts. PEEK also performs very well when tested for fatigue from repeated pressure and stress, another wear indicator. Because of its lower weight compared to comparable metals, it finds use in the transportation industry and beyond, particularly in cars and planes, where it helps save fuel. PEEK’s exceptional durability makes it an excellent choice for creating artificial organs and other medical devices.
With the development of digital marketing, the prices of injection molding processes online are becoming more transparent. Understanding the costs of injection molding processes helps product design companies create better products and encourages injection molding factories to adhere to industry standards, creating a positive atmosphere for the injection molding industry.
If the product structure is simple and the quantity to be produced is small, a one-to-one cavity mold can be used, which will be relatively cheaper.
The automotive components industry in Europe is seeing the most significant growth in using PEEK resin. Components around the engine, variable speed transmission parts, steering elements, and so on were all manufactured using a PEEK plastic injection mould instead of some customary expensive metals. As the automobile industry adapts to the needs of miniaturization, low weight, and cost reduction, the demand for injection moulded PEEK resin will grow.
Regarding the specific cost of raw materials consumed by injection molded products, this part of the raw material cost can be deduced from the weight of the molded shells in injection molding.
For example: Assuming ABS plastic pellets cost $1500 per ton (this is an example, please refer to the actual local price). If the shell weight of a product after injection molding is 200 grams, then the raw material cost of the product is $1500 / 1000000 * 200 = 0.0015 * 200 = $0.3.
Additionally, PEEK does not require metal machining or thermoset curing to be mass-produced via injection molding, which reduces the number of processing steps required. In the end, you’ll save money and time thanks to this. In harsh environments, PEEK injection molding typically performs better than metal. Because of this, it is used frequently in the manufacture of the airplane and car parts, as well as medical and industrial components, semiconductors, and electrical and electronic gadgets.
Common raw material prices: PEEK > PA66 > PC > PA6 > ABS > PS > LDPE > HDPE > PBT > PET. Specific prices can be referenced based on local market prices.
The cost of plastic molds, like all products, is “you get what you pay for.” The more complex, precise, and durable the mold, the higher the cost.
PEEK injection molding will be at the top of your list if you’re looking for an injection molding material that balances your performance needs, financial constraints, and environmental and sustainability goals.
A more complex example: Assuming the cost of ABS plastic pellets is $1500 per ton. A mold produces parts in a 1-to-4 ratio, with each part weighing 200 grams and the runner material for 1-to-4 being 100 grams. What is the cost of raw materials per part? The calculation method is to account for each part’s weight as 200 grams + 25 grams of runner material, totaling 225 grams, and then calculate the cost as described above.
Different products have different tolerance standards, with higher precision leading to higher costs. The cost of a mold with a tolerance of ±0.2mm will certainly differ from that of a mold with a tolerance of ±0.02mm.
PEEK, or polyetheretherketone is a semi-crystalline polymer and a high-performance engineering plastic. This material is biocompatible, has a high melting point (343°C), and has excellent mechanical properties. It is presently a popular research injection molding material. The advantages, features, and potential uses of PEEK injection molding are briefly discussed in this post.
GETTING A QUOTE WITH LK-MOULD IS FREE AND SIMPLE.
FIND MORE OF OUR SERVICES:
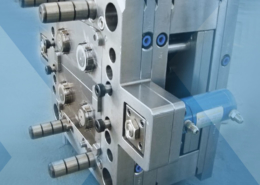
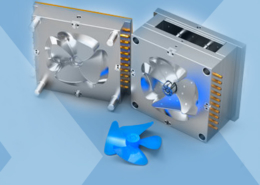
Plastic Molding

Rapid Prototyping
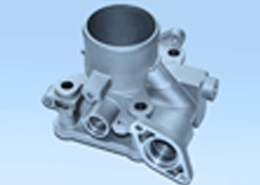
Pressure Die Casting
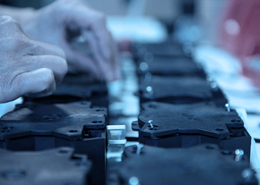
Parts Assembly
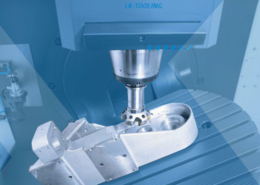