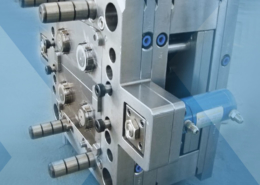
Understanding Injection Mold Cost for Parts and Tooling - plastic molding cost
Author:gly Date: 2024-10-15
Bawana, New Delhi Plot No.5, Pocket- I, Sector-3 BAWANA, Bawana, New Delhi - 110039, Dist. New Delhi, Delhi
Sector 10, Noida, Dist. Gautam Buddha Nagar Ground Floor, G - 20, Noida, Sector - 6, Ganesh Nagar, Sector 10, Noida - 201301, Dist. Gautam Buddha Nagar, Uttar Pradesh
Sinkage marks are depressions in the surface of the plastic injection moulded part caused in the last phase or stage of the plastic injection moulding process, during the cooling process. The thicker sections of the plastic cool at a slower rate than the others, resulting in a higher percentage of shrinkage in that local area. After the material on the outside has cooled and solidified, the material on the inside begins to cool and its shrinkage pulls the surface inwards, causing a surface depression.
Loni Industrial Area, Ghaziabad Plot No-4, Ground Floor, Anand Industrial Area, Mohan Nagar, Loni Industrial Area, Ghaziabad - 201007, Dist. Ghaziabad, Uttar Pradesh
Malad West, Mumbai 1st Floor, Unit No 33, Sumatinath Industrial Estate, Chincholi Bunder Road, Malad West, Malad West, Mumbai - 400064, Dist. Mumbai, Maharashtra
Incomplete filling occurs when a one injection moulded part is missing material to correctly generate its geometry. This occurs when the molten polymer cannot fill the entire cavity (or cavities) in the Injection mould, usually the thinner sections where the polymer melt cools before completely filling the mould. Any factor that increases the flow front resistance of the polymer melt can result in incomplete filling. Some of these factors are:
– Reduce the injection speed. High plastic injection speeds can cause jetting, which causes trapped air to appear right at the inlet gate. Reducing the injection speed will give the displaced air at the gate enough time to escape through the aeration zones.
Basai Road, Gurugram Khewat No– 55, 108 Basai, Near Basai Dhankot flyover Gurgaon-122001 Haryana-India, Basai Road, Gurugram - 122001, Dist. Gurugram, Haryana
Nalasopara East, Vasai, Dist. Palghar Unit No. 7, Survey No. 57, Near Parshwa Industrial Complex Goraipada, Nalasopara East, Vasai - 401208, Dist. Palghar, Maharashtra
A weld line (also called a weld mark) is formed when two melt flow fronts travelling in opposite directions meet. In contrast, a bond line occurs if these two fronts flow parallel to each other creating a bond line.
The formation of wrinkles or waves is due to the fact that a part of the flow front cools rapidly on the mould walls producing a fold on the flow front itself. Themain factors influencing the formation of these wrinkles are the flow velocity, the temperature of the mould walls, and the temperature of the molten polymer, among others.
Dhamatvan, Ahmedabad Survey No 337, Dhamatvan Village, Dhamatvan, Dhamatvan, Ahmedabad - 382435, Dist. Ahmedabad, Gujarat
Ambattur Tass Industrial Estate, Chennai 5, Kannan Koil Street, Pattravakam Ambattur Industrial Estate, Ambattur Tass Industrial Estate, Chennai - 600098, Dist. Chennai, Tamil Nadu
Vavdi, Rajkot Sr No. 32, Shri Rama Chowk, Shed No. 2, Plot No. 9/1, Opposite Poonam Dumper Behind Tata Perfect, Rajkot Gonadal NH 8B, Vavdi, Rajkot - 360004, Dist. Rajkot, Gujarat
Valiv, Vasai, Dist. Palghar Shop No 23, Ground Floor, Lusi Industrial Estate, Sativali Road, Vasai West, District Palghar, Valiv, Vasai - 401208, Dist. Palghar, Maharashtra
The following recommendations can be used to reduce the impact of weld lines and parting lines on injection moulded parts.
Sector 9, Noida, Dist. Gautam Buddha Nagar 1st Floor H-29 Sector 9, Sector 9, Noida - 201301, Dist. Gautam Buddha Nagar, Uttar Pradesh
Some of the actions to be taken to improve the surface finish are related to actions to increase the flow rate and temperature of the molten polymer and the mould walls. Therefore, the improvement of the surface quality is achieved by measures such as:
A poor finish can be caused by the formation of wrinkles or waves at the edges of the part or in the last filling areas during injection moulding.
Moshi, Pune Flat No D 204, Mantra Movements, Gat No 167 168, Moshi,, Moshi, Pune - 412105, Dist. Pune, Maharashtra
A rule of thumb to avoid excessive distortions in the part due to temperature differences after injection, is that the average temperature differences in any part of the part after injection should not be greater than 15-20ºC.
Andheri west, Mumbai 3, 1st Floor, Monisha Bldg, S.v.road Opp Fire Brigade, Andheri West, Andheri west, Mumbai - 400058, Dist. Mumbai, Maharashtra
Odhav, Ahmedabad 19, Girivar Glove Industrial Park, Behind Dhaval Industrial Estate, SP Ring Road, Odhav, Ahmedabad - 382415, Dist. Ahmedabad, Gujarat
Some of the practices we develop in the Moldblade Engineering Department to correct the problem of incomplete filling are:
Vatva, Ahmedabad C-22, Devashray Estate, Near Express Way Beside Haridarshan Esate, Oppoiste NKR Engineering, Vatva, Ahmedabad - 382445, Dist. Ahmedabad, Gujarat
Traditionally, the joint angle between the two faces is used to differentiate weld lines from joint lines. A joint angle of less than 135º produces a weld line, while a joint angle of more than 135º is defined as a joint line. In general, a weld line mark disappears when the joint angle reaches between 120º and 150º. The weld lines are considered more critical than joint lines in terms of both aesthetics and mechanical properties of the joint. Translated with www.DeepL.com/Translator (free version)
S.P Ring Road, Ahmedabad 32,Abhishri IND Park,Near Grand Vishala Estate,B/h Tirupati Hotel,S.P Ring Road,Odhav, Ahmedabad, S.P Ring Road, Ahmedabad - 382350, Dist. Ahmedabad, Gujarat
Trapped air will result in voids and bubbles within the moulded plastic part, incomplete filling or surface defects such as stains or burn marks.
The burr is a defect that occurs when part of the molten polymer flows through the existing gaps in the injection mould such as parting plane, aeration zones, ejectors, etc. Burring occurs for the following reasons:
Weld lines and joint lines can be caused by holes or insertions in the part, the existence of multiple injection gates, or due to areas of varying wall thickness where hesitation or race-tracking occurs.
Mayur Vihar Phase 1, New Delhi B 15, DSIDC Complex Kalyanpuri, East Delhi, Mayur Vihar Phase 1, New Delhi - 110091, Dist. New Delhi, Delhi
North West Delhi, New Delhi Khasra No 368, Gali No 7/8, Main Kushak Road No 2, Near Govt Ration Bansal Shop, Saroop Nagar, North West Delhi, New Delhi - 110042, Dist. New Delhi, Delhi
Nalasopara East, Vasai, Dist. Palghar Ground Floor, Gala No-4, Agarwal Udyog Nagar, Waliv Golani Naka Vasai East, Vasai Virar, Nalasopara East, Vasai - 401208, Dist. Palghar, Maharashtra
Okhla Industrial Estate, New Delhi Ground Floor, B-79, Rear Portion, Okhla Ind Area Phase -2, South Delhi, Okhla Industrial Estate, New Delhi - 110020, Dist. New Delhi, Delhi
Ambattur, Chennai No.27, Karpagam Nagar, Thirumudivakkam, Kancheepuram, Ambattur, Chennai - 600044, Dist. Chennai, Tamil Nadu
However, achieving uniform shrinkage is complicated by the presence and interaction of many factors such as the orientations of the polymer molecules, temperature variations in the mould walls, compaction variations in the plastic parts (over-compacted areas and under-compacted areas, due to unbalanced flow paths), etc. Note that areas of higher compaction, such as injection gates, have a lower shrinkage since part of the compaction of the molten polymer compensates for it. In contrast, areas further away from the gate are subject to less compaction and therefore tend to have a higher shrinkage.
The jetting defect occurs when molten polymer is pushed at speed through a small area, such as the injection nozzle or gate, to access a much larger area. The jetting defect results in mechanical weakness in the part, surface imperfections and multiple internal defects.
Makarba, Ahmedabad Neeka Tube Compound, Plot No-226, Pushpak and Pushpam Industrial Estate, Phase I, GIDC Estate,, Makarba, Ahmedabad - 382445, Dist. Ahmedabad, Gujarat
If welding or joining lines cannot be avoided, a good practice is to ensure that they are generated in low visibility or mechanically non-critical areas. This is often done by modifying the plastic injection gate, modifying the flow fronts and the areas where the weld/joint lines occur. Another practice is to try to achieve a good joint between the two fluxes so that the mechanical weakness that occurs is not excessive. To do this, the aim is for the junction of the two flux fronts to take place at the highest possible temperature and pressure, so that they are not far from the inlet port. Translated with www.DeepL.com/Translator (free version)
Sakinaka, Mumbai GALA NO. 4,GILBERT COMPOUND,KHERANI ROAD,SAKINAKA,OPP CHURCH, Sakinaka, Mumbai - 400072, Dist. Mumbai, Maharashtra
The trapped air defect appears when a certain amount of air cannot escape out of the mould during injection, a small area without material appeared in the injected part. In a correct Injection mould design, at each injection, air is exhausted through mould vents, mould inserts or even ejectors, which also act as vents.
The dimensional shrinkage of parts is inherent to the injection moulding process. Shrinkage occurs because the density of the polymer varies from processing temperature to ambient temperature (see, for example, the specific volume of a semi-crystalline polymer in Figure 5.46 – PVT curve). During the stages of the injection moulding process, cooling shrinkage produces a series of internal stresses in the part. These residual stresses act on the part with similar effects as possible externally applied stresses. If the residual stresses induced during moulding are high enough, the part after ejection from the mould may warp / twist or warp, resulting in defective parts.
The locations of the air leakage areas in the moulds are located in the areas that are filled at the end of the injection cycle or phase. A common cause of the trapped air defect is an insufficient size of the mould vents. Another common cause is when racetracking occurs (tendency of the polymer melt to flow preferentially in thicker sections leaving thinner areas with trapped air). Translated with www.DeepL.com/Translator (free version)
The warping or twisting of an injection-moulded plastic part is therefore due to the existence of a series of residual internal stresses in the part which are in turn generated by the differential shrinkage of the material during cooling. If the shrinkage throughout the part is uniform, the resulting part does not warp or twist, it simply shrinks uniformly and becomes smaller. Thecrystalline polymers, e.g. acetal, nylon, high density polyethylene, polyethylene terephthalate and polypropylenecause the most serious problems with shrinkage from 1 to 4%. Amorphous polymers, e.g. polystyrene, acrylic and polycarbonate are more treatable, with shrinkages of only 0.3 to 0.7%.
Occasionally, the use of high compaction pressures causes acceptable sink marks by reducing volumetric shrinkage although these cannot be completely eliminated. This is because the volumetric change of plastic from melt to solid is about 25% and the compressibility of plastics at typical injection moulding pressure is only 15%, which means that it is impossible to compact the molten plastic sufficiently to compensate for cooling shrinkage.
Ambernath, Ambarnath, Dist. Thane Flat No 104 K2 PH-11 Opp Ayappa Temple Khoj Khuntawali Mohan Suburbia Oxford Ambernath W, Ambernath, Ambarnath - 421501, Dist. Thane, Maharashtra
Landge Vasti, Pune S. No. 8/7, Shanti Nagar, Landewadi, Bhosari, Landge Vasti, Pune - 411039, Dist. Pune, Maharashtra
Noida, Dist. Gautam Buddha Nagar E -10, Sector -7, Noida - 201301, Dist. Gautam Buddha Nagar, Uttar Pradesh
GETTING A QUOTE WITH LK-MOULD IS FREE AND SIMPLE.
FIND MORE OF OUR SERVICES:
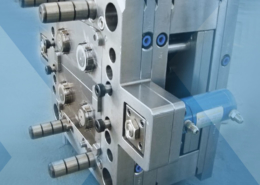
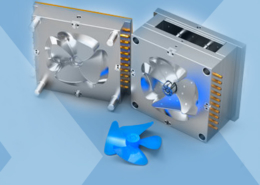
Plastic Molding

Rapid Prototyping
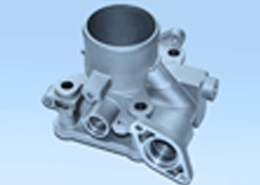
Pressure Die Casting
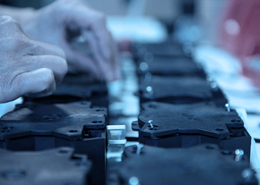
Parts Assembly
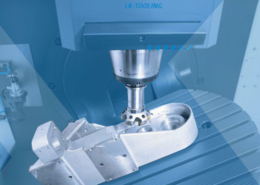