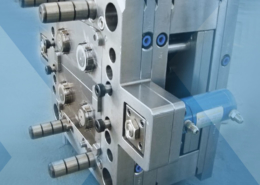
Two-shot Injection Molding Manufacturers - 2 shot injection molding companies
Author:gly Date: 2024-10-15
This section highlights the various steps manufacturers must follow during the ABS plastic molding process. They include:
“I have confidence that MME will provide top notch support for everything – from prototyping to production, and that they have the resources and staff to make that happen”.
We execute product design, design control and mechanical engineering for individual parts to full assembly. We apply FEA, DFMA, and industrial and manufacturing design and implementation.
When trying to start an ABS injection molding batch, a few factors must be in place. These factors are vital to having successfully molded parts. They include:
It is advisable to keep the backpressure of the ABS injection molding process as low as possible to prevent wear. The acceptable pressure is usually around 5 bar.
The recyclability of ABS makes it a perfect material for use in reusable applications. Recycling plants can easily shred the plastic parts and mix them up with fresh ABS to use for new parts production.
ABS stands for Acrylonitrile Butadiene Styrene. This plastic material comprises three monomers that make up its name. Each of these monomers contributes its properties to the polymer plastic to give it a wide range of properties.
ABS is harmless and non-toxic. This is one of many reasons it is a popular plastic material in manufacturing. However, it is not encouraged to use in medical implants.
If you’re trying to produce some parts using injection molding, it is only right you find out about the cost of the whole process before going ahead. To estimate the costs involved, you need to factor in different costs. Examples of the various costs involved include:
Our quality systems are managed through design control, full qualification, validation, process control and traceability. We are ISO 13485:2016 certified; ITAR, FDA and FMR registered; have certifications for UL, CE and TUV. Learn More
One of ABS plastic’s major shortcomings is its poor sunlight performance. The material tends to degrade upon constant exposure to sunlight. However, part manufacturers enhance its performance in sunlight by adding additives to the ABS plastic during molding.
Other activities carried out during ABS molding processes include decorated moldings using laser marking or hot stamping, ultrasonic welding, etc.
After treating the material, the next step is to prepare the ABS molding machine for work. This will involve setting the parameters such as the compression ratio, clamping force, and injection molding pressure. The typical values for these parameters include a compression ratio greater than 2, a clamping force ranging from 4700 to 62000 tonnes per square meter (t/m²), and an injection molding pressure greater than 1500 bar.
This is the cost of buying the material (in this case, ABS). You’ll be able to find the material for a cost ranging from $1 to $5 per kg.
This is also known as the tooling costs. This drives up the cost of the ABS injection molding process. There are three different methods used in making injection molds. They include CNC machining, 3D printing, and electrical discharge machining (EDM). These methods can range as low as $100 for low-volume simple 3D-printed molds. The price could also go as high as $100,000 for huge production runs or molds with complex designs.
Our diverse selection of machine and materials delivery consists of thermoplastics and silicone. We are experts in overmolding, two-shot, thin wall, and insert molding utilizing vertical and horizontal presses ranging from 10 – 750 tons.
ABS injection molding is a process that seems pretty easy to achieve. However, its technicalities that only experts understand. This is why it is important to outsource your ABS molding to companies that actually understand the practical principles of the manufacturing process.
The mold is quite vital in determining how the finished ABS product will turn out. Hence, the design of the mold and its gate is quite important in the process. The thickness of the ABS mold ranges between 0.025 – 0.05mm, while the gate length is set at less than 1mm. Also, the diameter of the channel through which the molten ABS flows is set at 3mm, while the vent hole width ranges from 4 – 6mm. Finally, the mold temperature used is always around a range of 60 – 65°C.
Despite its acclaimed strength and toughness, this strong plastic isn’t so impervious to UV light. Hence it has limited outdoor use. However, part manufacturers have found ways to manipulate the properties of this plastic to withstand UV light by using various additives and fillers such as acrylic, glass, and stainless steel fibers. These additives alter the properties of the plastic and further enhance its uses for various applications.
To prevent the out-gassing that comes from the flame-retardant ABS plastic absorbing moisture, you need to ensure the material is fully dried. Also, you need to ensure good temperature and residence time control during the injection molding process to prevent thermal degradation of the ABS plastic.
Injection molding is a common manufacturing process with different variants depending on the raw material used. One of such variants of the process is the ABS injection molding process. Just as the name implies, the raw material for this injection molding variant is ABS plastic.
MME Group is the newest member of your team, providing industry leading solutions for your designs from engineering through assembly.
The residence time is the time it takes for a plastic pellet to move from the injection molding barrel to the injection mold. For ABS plastics, the residence time is usually between 5 – 6 minutes at a temperature lower than 265°C. However, for flame-retardants grade ABS plastic, the residence time is shorter, and the temperature is way lower.
The costs here are responsible for the remuneration of the personnel carrying out the tasks and for the setup and maintenance of the machines. Examples of parameters factored in here include:
Designing the parts before the injection molding process makes it possible to determine if producing the part is actually possible. Here are some general principles that work with ABS parts design:
Working with an injection molding machine with good temperature control is essential as this process still requires a lot of heat. For example, when the ABS parts in production contain a high level of gloss, the temperature used in production is higher than normal. However, it is important to note that the higher the temperature used for the injection process, the shorter the exposure time should be.
ABS plastic has some hygroscopic properties (it can absorb moisture from the air) and also absorb water around it. However, the presence of water in any molded ABS plastic could cause structural defects in the plastic. Hence, ensuring the ABS plastic used is properly dried is essential. There are two parameter types for drying the plastic: either dry at 80 – 95°C for 3 – 4 hours or use a dry hopper at 80°C for 1 – 2 hours.
We provide value-added assembly services for high-precision, complex product configurations. We ensure the assembly conforms to quality standards and product performance expectations.
Due to the processability of ABS, it is the most suitable material to use in making complex parts. Its processability makes it easy to reproduce complex and functional parts using the plastic. Apart from the parts being accurately produced, they still maintain functional integrity even when used in extreme conditions, thanks to the hardness of the plastic.
ABS plastic has uses in different industries due to various reasons. Due to its ease of molding, the low cost of production, and resistance to physical and chemical changes, this polymer has become a manufacturer’s favorite. Here are some examples of industries where ABS plastic parts have found use:
You’ll most likely outsource your production to companies with the necessary equipment. These companies will charge you a separate fee for the equipment used. However, if you plan to get the equipment, you’ll have to dole a sum within the $50,000 – $200,000 range. Apart from buying the equipment, you’ll also have to maintain the equipment, which could cost you a fortune. The cost-effective option will be to outsource the production.
Controlling the temperature is crucial during ABS injection molding as overheating the plastic could lead to thermal degradation. This thermal degradation is due to the chemical bonds in the plastic breaking, which could cause brown granules on the finished part.
The injection molding temperature used for a particular ABS injection molding process depends on the quality/grade of ABS used. Listed below are examples of some grades of ABS plastic commonly used in ABS plastic molding and the optimum injection molding temperature used:
Our services include in-house tooling design and build for molds, assembly fixtures, testing and measuring fixtures. Tooling aligns with the program stage from prototyping, bridge and production.
The injection molding speed depends on the grade of the ABS plastic and the finished product requirements. For example, flame-resistant ABS plastics can only use slow injection molding speeds. Also, products that require precision surface finishing could require multi-stage, high injection molding speeds.
Some ABS grades tend to stick to the mold screw after removing the part. So the best way to clean this up is to wait a little bit for the residue to wear off, then clean the compartments of the injection molding machine thoroughly using polystyrene.
ABS molded parts are suitable for use in applications that require supporting heavy loads because of their high tensile strength. Their ability to withstand heavy mechanical impacts makes this plastic a good budget option for high tension applications.
At WayKen, with advanced manufacturing technologies and resources, we can provide our customers with professional rapid prototyping services ., including CNC machining, rapid injection molding, vacuum casting, etc. So, get a quote today, and you can be sure to get high-quality injection molded parts at a competitive price.
There are many reasons why ABS injection molding is one of the most popular forms of plastic molding. Some of the advantages include:
While ABS parts usually have high tensile strength, they can’t withstand heavy loads for long periods because of their poor fatigue resistance. The ABS plastic part might degrade easily if constantly exposed to high-stress environments.
Before using a piece of ABS plastic for manufacturing, it needs proper drying. The drying temperature used is within the range of 80 – 85°C done for 2 – 4 hours. Another drying method involves using a drying hopper with a temperature of 80°C. However, the latter process only lasts for 1 – 2 hours.
These properties and potential for manipulation make ABS the most widely used polymer in the injection molding process. Want to find out how this plastic is used for manufacturing various finished products? Then, the next section is a must-read.
The properties the plastic possesses include chemical resistance, hardness, and heat resistance contributed by acrylonitrile. Other properties include impact resistance and toughness (bestowed by butadiene) and strength and gloss contributed by styrene. Despite its wide range of features, it is relatively one of the cheapest plastics to purchase. Also, it is one of the easiest plastics to use in injection molding due to its ease of processability.
“We would like to thank the MME team for the excellent support and execution of the molded components that recently received FDA clearance…the clear communication and program management from MME made the process smooth and productive”.
MME Group is a full-service injection molder and contract manufacturer. Our vertical integration advantage is your advantage. We offer on-site tooling design and builds, custom plastic and silicone injection molding, secondary operations, high-level assembly, packaging, inventory, supply chain management and distribution all from our two locations in St. Paul, MN.
GETTING A QUOTE WITH LK-MOULD IS FREE AND SIMPLE.
FIND MORE OF OUR SERVICES:
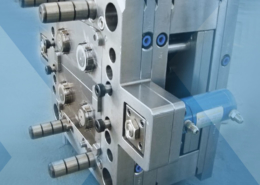
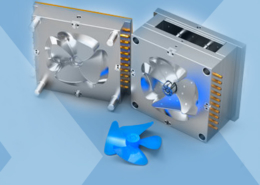
Plastic Molding

Rapid Prototyping
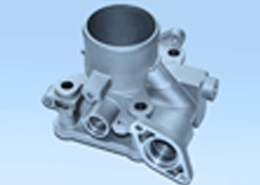
Pressure Die Casting
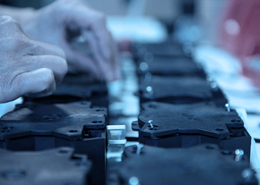
Parts Assembly
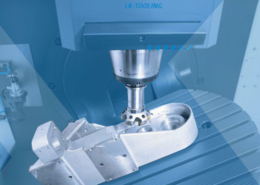