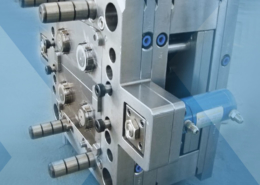
Two-Shot Injection Molding - Prototool - twin shot injection moulding
Author:gly Date: 2024-10-15
Winfit CPVC series Toggle Injection Moulding Machines are designed with CAD optimized high speed, five point twin toggle locking mechanism using graphite impregnated bushes & high tensile chrome plated tie bar for fast and precise mold closing and opening system.
At startup, barrel temperature is usually lower than the barrel heater gauge temperature. Ensure the barrel is heated to gauge temperature and then hold temperature for a while before starting.
A short shot refers to incomplete filling at the end of the material flow or incomplete filling in multi-cavity molds, especially in thin-walled areas or at the end of the flow path. It manifests as the melt solidifying before the cavity is fully filled, resulting in a shortage of material in the product.
Below is a table of common injection molding defects and their detailed channels, which interested friends are welcome to click on for in-depth understanding:
When impurities in the melt block the nozzle or cold material blocks the gate and runner, clean the nozzle or enlarge the mold cold well and runner cross-section.
Winfit CPVC series machines come with Servo technology as a standard feature. VDP system is also available as an additional option. Winfit CPVC series ranges from 75 to 350 ton clamping force capacity.
When raw material flowability is poor, the mold’s structural parameters affect short shots. Improve the gating system stagnation defect by reasonably positioning runners, enlarging gate, runner, and sprue sizes, and using a larger nozzle. Also, add appropriate additives to the raw material formula to improve resin flow performance.
Injection pressure is nearly proportional to the filling length. Low injection pressure shortens filling length and leaves the cavity unfilled. Address this by slowing injection speed, extending injection time, etc., to increase injection pressure.
The common method to control feeding is volumetric feeding. Check whether the plastic particle size is uniform and if “bridging” occurs at the feed port. If the feed port temperature is too high, it will also hinder feeding. To address this, clear and cool the feed port.
Additionally, in mold system process operations, improve poor ventilation by increasing mold temperature, reducing injection speed, reducing gating system flow resistance, decreasing clamping force, and increasing mold clearance.
If part thickness and length are disproportional, and the shape is complex with a large molding area, melt easily encounters flow resistance at the thin-wall entry, making cavity filling difficult. Design part shape considering the thickness and melt filling limit flow length.
Automatic mold height & tonnage setting through Sun gear mechanism with linear transducer eases mold setting, leading to advantages like positive drive, zero backlash, high rigidity, increased mold safety and longer life.
Injection molding defects are issues that every injection molding factory may encounter during the molding process. Short shot defects in Injection Molding are a common injection molding defect. However, unlike flash defects, most short-shot defects are resolved before mold testing.
Facing short shots in injection molding isn’t scary; what’s truly scary is when the factory doesn’t understand or can’t solve the issue. Familiarity with structural design, mold design, sample testing, problem analysis and resolution, appearance assurance, material characteristics, and more are essential skills for all injection molding practitioners.
If a large amount of gas remains in the mold due to poor ventilation and is compressed by the material flow to a pressure greater than the injection pressure, it will hinder the melt from filling the cavity, causing a short shot. To address this, check if there are cold wells or if they are correctly positioned. For deep cavities, add vent grooves or vent holes at the short shot location; on the parting surface, create vent slots with a depth of 0.020.04 mm and a width of 510 mm, and position vent holes at the last filling point of the cavity.
Injection speed directly affects filling speed. If injection speed is slow, melt fills slowly, and low-speed flowing melt easily cools, further reducing flow performance and causing a short shot.
A toggle machine line, the Winfit CPVC series is built for faster clamp movement, robust performance, higher energy efficiency and greater productivity.
During injection, the nozzle contacts the mold, and since mold temperature is generally lower than nozzle temperature, and the temperature difference is large, frequent contact cools the nozzle, freezing the melt at the nozzle.
For mold and injection molding factories, analyzing and perfectly resolving this short-shot problem is a fundamental skill. Every mold and injection molding practitioner has the responsibility and obligation to master all injection molding defects.
If nozzle temperature is low and can’t rise, check if the nozzle heater is damaged and increase nozzle temperature accordingly. Otherwise, excessive pressure loss in the flow will also cause a short shot.
In multi-cavity molds, appearance defects often arise from unbalanced gate and runner designs. When designing the gating system, ensure gate balance and the weight of parts in each cavity should be proportional to the gate size, so that each cavity can be filled simultaneously. The gate should be positioned at the thick wall, and a balanced runner design can also be adopted. If the gate or runner is small, thin, and long, the pressure of the melt during flow will result in excessive pressure loss, leading to filling issues. To address this, enlarge the runner cross-section and gate area, and use multiple feeding points if necessary.
Generally, within the appropriate molding range, the material temperature is nearly proportional to the filling length. Low-temperature melt flow performance decreases, shortening the filling length. If material temperature is below process requirements, check if the barrel heater is intact and raise the barrel temperature accordingly.
When selecting equipment, the maximum injection capacity of the injection machine must exceed 120% of the total weight of the part and the sprue, while the total injection weight should not exceed 85% of the machine’s plasticizing capacity.
If low-temperature injection is necessary to prevent melt decomposition, extend the injection cycle time to avoid short shots. For screw injection machines, increase the temperature in the front zone of the barrel.
Additionally, short holding time can also result in short shot. Control holding time within a suitable range, but note that excessive holding time can cause other faults. Adjust during molding based on the specific part.
The main cause of short shots is excessive flow resistance, preventing the melt from continuing to flow. Factors affecting the flow length of the melt include part wall thickness, mold temperature, injection pressure, melt temperature, and material composition. Mishandling these factors can result in short shots.
If the mold structure lacks a cold well, cold material entering the cavity solidifies immediately, preventing subsequent hot melt from filling the cavity. During mold opening, separate the nozzle from the mold, reducing mold temperature impact on the nozzle, and keep nozzle temperature within process requirements.
If injection pressure can’t increase further, remedy by increasing material temperature, lowering melt viscosity, and improving melt flow performance. Note that excessive material temperature can cause melt thermal decomposition, affecting part performance.
Using raw materials with excessive moisture or volatile content will also produce large amounts of gas, leading to poor mold ventilation. In this case, dry the raw materials and remove volatiles.
When melt enters a low-temperature mold cavity, it cools too quickly, failing to fill all corners of the cavity. Preheat the mold to the process-required temperature before starting, and control the mold cooling water flow at startup. If mold temperature can’t rise, check if the mold cooling system design is reasonable.
If the raw material formula has too much lubricant and the clearance between the injection screw check ring and the barrel is large, severe melt backflow in the barrel will result in insufficient feeding and a short shot. To address this, reduce lubricant usage and adjust the clearance between the barrel, injection screw, and check ring, as well as adjust the equipment.
GETTING A QUOTE WITH LK-MOULD IS FREE AND SIMPLE.
FIND MORE OF OUR SERVICES:
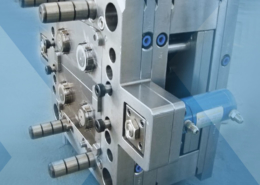
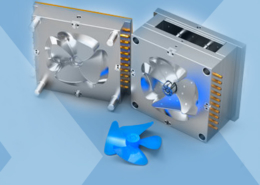
Plastic Molding

Rapid Prototyping
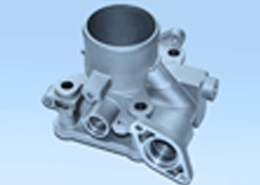
Pressure Die Casting
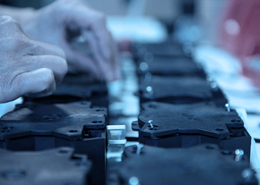
Parts Assembly
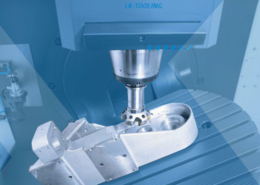