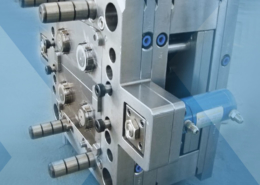
Top 8 Plastic Injection Molding Companies - injection mold maker
Author:gly Date: 2024-10-15
Due to crystallinity, the shrinkage is relatively high (order of 0.018 - 0.025 mm/mm or 1.8 - 2.5%). The shrinkage is more uniform than PE-HD (the difference in flow and cross-flow shrinkage is typically less than 0.2%). Addition of 30% glass reduces the shrinkage to approximately 0.7%.
Two plate mold is one of the most reliable and simplest mold designs. It has very few moving parts making it more straightforward to run in the production of injection mold slide design. Owing to its simple and straightforward design, it is cheaper than its counterparts.
The structure of the two plate mold is divided into two parts. As discussed above, one part is fixed, whereas the other is moving. The cavity side of the mold design remains fixed, and the core side moves.
The general construction of the three plate mold is built about the opening sequence of the molding product. Understanding the complete design of the mold is required to know how the mold functions. The mold opens in three different stages.
PP is produced by the polymerization of propylene using stereospecific catalysts. Mainly, isotactic PP is produced (the methyl groups lie on one side of the carbon chain). This linear plastic is semicrystalline because of ordered molecular structure. It is stiffer than PE and has a higher melting point. The PP homopolymer becomes very brittle at temperatures higher than 0 C (32 F) and for this reason, many commercially available grades are random copolymers with 1 - 4% ethylene or block copolymers with higher ethylene content. Copolymers have a lower heat distortion temperature (approximately 100 C / 212 F), less clarity, gloss, and rigidity, but greater impact strength. The material becomes tougher as the ratio of ethylene increases. The Vicat softening point is approximately 150 C (302 F). Because of high levels of crystallinity, the surface hardness and scratch resistance is higher for these materials.
The three plate mold has three cavities that are filled through a centrally located pinpoint gate. The mold is typically divided into three sections:
The selection of the injection mold gate design depends on a number of factors, such as the volume of production, budget, time restraints etc. Mold plates are used to support molds and tools. They are made of metals such as aluminium and steel. The mold types can be classified into two-plate mold and three plate mold. Let us know more about both of them.
Both homopolymer and copolymer PP offer excellent resistance to moisture and good chemical resistance to acids, alkalis, and solvents. However, it is not resistant to aromatic hydrocarbons such as benzene, and chlorinated hydrocarbons such as carbon tetrachloride. It is not as resistant to oxidation at high temperatures as PE.
A three-plate mold consists of two parting planes and its mold splits into three sections. For a three-plate plastic molding design, the runner is present on the second parting plane that runs parallel to the main parting plane. The second parting plane allows the sprue and runners to get expelled when the mold is open.
When using three-plate advanced prototype molding for round parts, you need to ensure that the part is evenly filled. It is critical to make sure that the spaced gates are placed evenly around that particular part and have been evenly filled all around.
To gain more control on the desired mold opening sequence, it is also required to set the movement accurately. The closing of the mold is obtained by the closing action of the molding machine.
Three plate injection mold design engineering consists of two parting planes, and the mold divides into three parts. Thus, runners and components can be located on different parting planes. In three plate injection mold, the runners are generally ejected separately to the molded part. Therefore there is a probability of automatic degating. We hope that by now you are aware of the key differences in between the two types of mold. Hence, choose one that is best suited to your project requirements.
In the fixed mold, there is a runner, which is placed on the parting surface. Once the molding process is completed, the runner and the injection-molded product stay in the moving part of the mold. The runner and the injection part are later removed from the parting surface.
Then the A and B halves of the part get separated, and the pins get pulled from the Sprue, enabling it to drop from the mold. The part can get ejected off after the mold gets completely opened, just like normal two-plate plastic injection products.
The application of three plate mold requires the runner system to be positioned among different planes to automatic degating and injection location. The stripper plate is one of the significant differences between the two plate mold and the three plate mold used for plastic molding products. The significant difference also lies in the structure, orientation, and guide pin location. The three plate mold exists mainly to respond to the appearance and the production requirements. The injection pressure on the three-plate mold is not higher than the two-plate mold when a complete filling situation is concerned.
This type of plate has three main plates or parts that are separated from each other at the opening. Pin-point gate is one of the significant advantages of this type of mold and it can be used for making multi-impression molds.
The selection of the molding product type depends on several factors like components design, budget, and production volume. One of the significant questions that remain in the manufacturer’s mind during new product development is what type of mold is required?
Two plate molds consist of a single parting plane from where the mold splits. In the case of a multi-cavity two-plate mold, the gate and runner is present in the parting plane. They make sure that the gate and the runner eject while the mold splits.
Compared to the two plate mold, the three plate mold has an additional plate that is found floating on the moving and fixed plates. The fixed plate and the center plate have a feed system in between to form injection molding products. The closing of the molding machine is usually achieved by the closing action that picks up progressively and closes the sections as they move forward.
As the mold of the three plates opens up, the A and B halves are held together with releasable plate locks. The sprue is then released, and then the gate breaks away from that part. Under-cut pins hold the sprue back in another floating plate. When the tooling of the A-side is hit, a set of stop bolts. These two events occur successively.
Viewmold company provides injection molding services for your part with PP plastic material. PP injection molding processing condition Generic Class PP (Polypropylene) Typical Applications Automotive (mostly mineral-filled PP is used: dashboard components, ductwork, fans, and some under-hood components), appliances (doorliners for dishwashers, ductwork for dryers, wash racks and lids for clothes washers, refrigerator liners, etc.), consumer products (lawn/garden furniture, components of lawn mowers, sprinklers, etc.). Injection Molding Processing Conditions Drying Not normally necessary if proper storage is used Melt Temperature 220 - 280 C (428 - 536 F); not to exceed 280 C Mold Temperature 20 - 80 C (68 - 176 F); suggested: 50 C (122 F) The crystallinity level is determined by the mold temperature. Material Injection Pressure Up to 180 MPa Injection Speed Typically, fast injection speeds are used to minimize internal stresses; if surface defects occur, slow speed molding at a higher temperature is preferred. Machines capable of providing profiled speed is highly recommended. Runners and Gates In the case of cold runners, typical diameters range from 4 - 7 mm. Full round sprues and runners are recommended. All types of gates can be used. Typical pin gate diameters range from 1 - 1.5 mm, but diameters as low as 0.7 mm may be used. In case of edge gating, the minimum gate depth should be half the wall thickness and the width should be at least double the thickness. Hot runners can readily be used for molding PP. If you need high quality cutom aluminium casting parts Pls contact us sales@viewmold.com If you need high quality injection mold tooling, Contact us. Chemical and Physical Properties PP is produced by the polymerization of propylene using stereospecific catalysts. Mainly, isotactic PP is produced (the methyl groups lie on one side of the carbon chain). This linear plastic is semicrystalline because of ordered molecular structure. It is stiffer than PE and has a higher melting point. The PP homopolymer becomes very brittle at temperatures higher than 0 C (32 F) and for this reason, many commercially available grades are random copolymers with 1 - 4% ethylene or block copolymers with higher ethylene content. Copolymers have a lower heat distortion temperature (approximately 100 C / 212 F), less clarity, gloss, and rigidity, but greater impact strength. The material becomes tougher as the ratio of ethylene increases. The Vicat softening point is approximately 150 C (302 F). Because of high levels of crystallinity, the surface hardness and scratch resistance is higher for these materials. PP does not have environmental stress cracking problems. PP is usually modified by addition of glass fibers, mineral fillers, or thermoplastic rubbers. The MFR of PP ranges from 1 to 40; lower MFR materials have better impact strength but lower tensile strength. The copolymer is tougher than the homopolymer of the same MFR. The viscosity is more shear and temperature sensitive than PE. Due to crystallinity, the shrinkage is relatively high (order of 0.018 - 0.025 mm/mm or 1.8 - 2.5%). The shrinkage is more uniform than PE-HD (the difference in flow and cross-flow shrinkage is typically less than 0.2%). Addition of 30% glass reduces the shrinkage to approximately 0.7%. Both homopolymer and copolymer PP offer excellent resistance to moisture and good chemical resistance to acids, alkalis, and solvents. However, it is not resistant to aromatic hydrocarbons such as benzene, and chlorinated hydrocarbons such as carbon tetrachloride. It is not as resistant to oxidation at high temperatures as PE. If you need to look for more plastic resin injection molding processing condition, could you please click it. If you need high quality plastic extrusion services, Pls contact us sales@viewmold.com If you need high quality sheet metal parts, Pls contact us sales@viewmold.com The following is other plastic processing condition: ABS injection molding processing condition, HDPE injection molding processing condition, LDPE injection molding processing condition, PA12 injection molding processing condition, PA6 injection molding processing condition, PBT injection molding processing condition, PC-ABS injection molding processing condition, PC-PBT injection molding processing condition, PEI injection molding processing condition, PETG injection molding processing condition, PMMA injection molding processing condition, POM injection molding processing condition, PPE injection molding processing condition, HDPE injection molding processing condition, PP injection molding processing condition, PS injection molding processing condition, PVC injection molding processing condition, SAN injection molding processing condition,
In the case of cold runners, typical diameters range from 4 - 7 mm. Full round sprues and runners are recommended. All types of gates can be used. Typical pin gate diameters range from 1 - 1.5 mm, but diameters as low as 0.7 mm may be used. In case of edge gating, the minimum gate depth should be half the wall thickness and the width should be at least double the thickness. Hot runners can readily be used for molding PP.
PP does not have environmental stress cracking problems. PP is usually modified by addition of glass fibers, mineral fillers, or thermoplastic rubbers. The MFR of PP ranges from 1 to 40; lower MFR materials have better impact strength but lower tensile strength. The copolymer is tougher than the homopolymer of the same MFR. The viscosity is more shear and temperature sensitive than PE.
Typically, fast injection speeds are used to minimize internal stresses; if surface defects occur, slow speed molding at a higher temperature is preferred. Machines capable of providing profiled speed is highly recommended.
ACIS®, Autodesk Inventor®, CATIA® V5,Creo™ Parametric, IGES, Parasolid®, Pro/ENGINEER®,Siemens PLM Software’s NX™, SolidEdge®, SolidWorks®, STEP
Two plate molds are the most frequently used in plastic injection molding service. They include a parting plane where the mold divides into two halves. In a mold that has multiple cavities, the gate and the runner must be located in the parting planes to ensure that ejection takes place when the mold divides into two.
Two plate mold design is one of the simplest injection mold structures that has several advantages. Two plate molds consist of two main parts – side A and side B. When there is a load on the injection machine for injection molding products, side A is held still and fixed while side B remains movable. Here are some of the parts in the two plate mold design:
GETTING A QUOTE WITH LK-MOULD IS FREE AND SIMPLE.
FIND MORE OF OUR SERVICES:
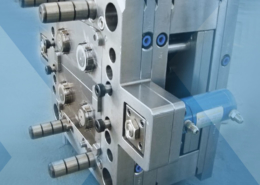
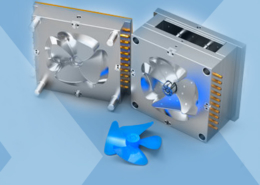
Plastic Molding

Rapid Prototyping
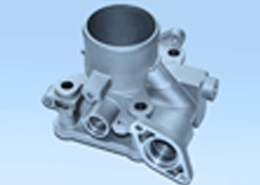
Pressure Die Casting
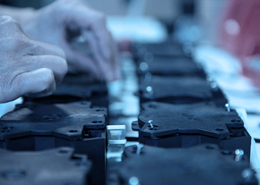
Parts Assembly
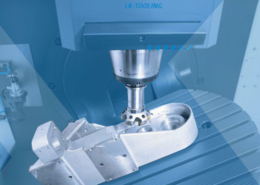