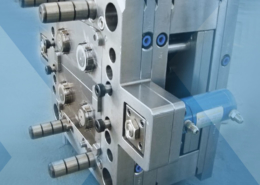
Top 30 Plastic Injection Molding Companies in The USA - 2024 - best injection mo
Author:gly Date: 2024-10-15
Some complicated parts require the intricate molds and this is done through the use of advanced tools such as 3D printing, CNC or EDM machining. These complex molds get more material, and as a result, the costs are increased.
These approaches ensure that there is no wastage and increase the efficiency of the processes of production processes, thus enable the manufacturers achieve quality with a lower cost.
The durability needed for high-volume production makes steel molds a cost-effective option, although their initial cost is higher. The costs also relate to the mold accuracy and finishing needs, where narrower tolerances contribute to increased costs.
Components such as an ejector system are installed into the mold before being loaded on an injection molding machine. The engineer then configures the machine temperature, pressure, and injection speed and conducts a test run to check the production run quality.
Undercut-like characteristics can make the process of molding complex. The best is to remove them if it’s feasible. If not, other methods are the use of slide shut-offs or modification of the parting line to ease mold construction.
Knowledge of these variables leads to effective analysis in the area of cost in plastic injection molding projects brought about by optimized design and production practices.
This involves using 3D printing to create a prototype of injection molds also known as 3D printed molds. Engineers can make use of the mold normally after checking for flaws in design and functionality and correcting the errors. The mold is then improved using manufacturing processes such as 3D printing or CNC machining.
Inclusion of non-essential features like textures or high polish raises costs. These often need more cavities in the mold demand, thus pushing costs higher. Focus on the essentials to manage the costs well.
This technique involves low temperatures and pressures leading to the use of inexpensive materials. Furthermore, surface finish is important because the product may pick up some details of the mold. Generally, manufacturers limit thermoforming to manufacturing relatively simple components like packaging trays, vehicle door panels, etc.
The tooling cost in injection molding depends most on part complexity. Parts that have sharp corners, thin ribs, or undercuts require more expensive tooling.
There are various other low volume plastic manufacturing methods aside from injection molding. Below are some of the alternatives you can choose for cost-effectiveness and faster time to market.
A quality plastic injection molding process provides immediate feedback to help improve manufacturability. It enables the testing of new concepts in various industries before the mass production of parts.
Low volume plastic injection molding offers several advantages that make it the manufacturing choice for several plastic parts over the traditional injection molding process. Here are some of its advantages.
After you inject molten material into the plastic injection mold, the molten plastic cools and solidifies. The cooling/solidification time depends on the type of mold taking longer to cool due to a slower thermal transfer occurring in plastic than metal. In such a case, cooling is improved by using compressed air or interchangeable stacks.
On-demand low volume manufacturing is a relatively new concept in the manufacturing world. It brings about several dramatic changes to how engineers interact with suppliers and manufacturers. This is even more so when it comes to custom plastic fabrication.
3D printing is a quality-focused manufacturing process considered an alternative to quick turn molding by many product designers and manufacturers. It does not require upfront investment into mold creation and has a short lead time.
This level usually goes for injection mold and molding process outsourcing. Below is an estimated cost breakdown for a production volume of 5,000 to 10,000 units using thermoplastic materials like polypropylene:
In the process of molding, post-operations can substantially increase the general cost of the project. These are assembly, finishing, and packaging, which are adapted to improve the product’s functionality and appearance.
Despite using a softer tooling material, low volume plastic injection molding produces highly durable and functional parts
It is the perfect method for prototyping plastic parts. It offers benefits such as quick and cost-effective production, easier testing, and validation of designs before mass production tooling, and easier refinement.
Urethane casting is an excellent alternative characterized by no upfront cost and reduced lead time. The manufacturing process involves creating a master pattern of the product with high-resolution 3D printing or CNC machining.
Furthermore, aluminum tooling allows for easier heat treatment because there is no need for the extra annealing step. This is unlike steel which needs annealing to reduce any internal stress and to toughen the metal sufficiently. Moreover, aluminum molds support most surface treatments that you would normally use for steel.
Packaging is customized to the product, ranging from simple bulk boxes to elaborate structures that provide protection against damage during transportation. Packaging requirements vary depending on the fragility and size of the parts.
Low-volume injection molding is a cost-effective manufacturing solution for small and medium-scale businesses. Key applications of the manufacturing solution include:
When it comes to plastic injection molding, the choice of material is a crucial factor that directly impacts the overall cost. The type of plastic you select will not only affect the upfront material expenses but also influence the durability, performance, and production efficiency of your final product.
These thermoplastic resins come in different additive fillers, color options, and properties such as strength, thermal and chemical resistance, durability, etc.
All these three factors including set-up, repair, and operator costs are important in the total cost of producing injection molded parts. The effective management and qualified labor help to reduce these costs that come with keeping the high production standards.
The total cost depends on factors like mold complexity, production volume, and material choice. Whether you’re producing 100 parts or 100,000, understanding these costs upfront can help you budget effectively and make informed decisions.
This discussion on plastic injection molding cost aims to examine the key factors that determine the price and efficiency of the production. Key points include the material, size, and complexity that affect mold manufacturing costs and the equivalent costs of equipment types by machine type.
Low volume injection molding is an efficient process for high-quality manufacturing. However, finding the best plastic injection molding services provider could be challenging. Here are a few factors to consider before choosing a plastic molding company:
Wall thickness is crucial in rapid injection molding. Walls should not be thicker than the recommended range for plastic families. When not considered, such walls may sink, warp, or experience other molding defects. The general rule of thumb is to use a wall thickness between 0.04 to 0.14 inches consistently across the whole part.
Manufacturers need to understand this type of injection molding to gain an advantage in the evolving markets. As a result, this extensive guide takes you through everything you need to know about low volume injection molding.
This level of production uses advanced machines, which cost extra at first but drop the cost per Part significantly due to economies of scale.
Plastic injection molding costs can vary widely, typically ranging from $100 for simple 3D-printed molds to over $100,000 for complex steel molds used in high-volume production.
Low volume plastic molding allows manufacturers to make parts without demanding minimum orders. Therefore, if you are looking to get small batch plastic manufacturing, this can be helpful. You will also avoid getting products from an outdated inventory. All of these translate to effective cost-saving.
For simple molds, costs can range from $1,000 to $5,000. More complex molds, especially those with multiple cavities or intricate designs, can cost between $25,000 and $75,000 or more.
Traditional manufacturing involved the mass production of large-scale similar products. However, on-demand manufacturing enables low-volume, customized products such as small-scale plastic injection molding. It takes advantage of cloud-based technologies and self-service models. This allows customers to get quotes in real-time and keep tabs on their orders throughout manufacture.
Despite being one of the oldest manufacturing methods, CNC machining remains a reliable small quantity plastic manufacturing method. It is versatile and can work with other types of materials including metals. Furthermore, it helps to create accurate molds, patterns or dies for various manufacturing processes such as molding, casting, and others.
Low-volume injection molding usually entails making 100-1,000 parts. This kind of a production level is for the less complicated types of molds and for simpler machinery.
Injection molding requires multiple types of mechanical parts, which can either wear out or break, requiring frequent maintenance and some repairs once in a while. The costs are critical in making sure the operation is ongoing.
HITOP is committed to assisting customers by offering a comprehensive one-stop solution, encompassing product design enhancement, initial sample creation, mold fabrication, injection molding, and product assembly.
This, therefore, makes high-volume production more economical for large numbers of units of a product, providing significant savings per Part. Here’s a breakdown of estimated costs for producing 100,000 to 300,000 units using ABS plastic:
For mid-volume runs (5,000-10,000 parts), the cost per part can be around $3. For high-volume production (100,000-300,000 parts), the cost per part can decrease to around $1.75.
The cost of mold manufacturing is dependent upon the material (steel or aluminum), size, and complexity. Complicated designs usually demand high skills, such as:
It will be best to go for a company that can offer low-volume but high-quality injection molded products without compromising the specification. This means that the low volume injection molding company must fully comply with the design specification. Recommendations are allowed based on experience, knowledge, and expertise. You must approve every adjustment to the design.
General up-keep of worn parts and routine maintenance is essential for avoiding down-time and efficient operation. Therefore, such preventive maintenance addresses the issue of bigger and more expensive repairs later.
Small batches do not require the hardened steel mold tooling typical of the traditional molding method. Rather, it uses the softer aluminum material for making the molds. Aluminum is a considerably softer material than steel. Thus, aluminum molds are easier and faster to work with.
High-performance plastics, though initially more expensive, can reduce maintenance and replacement costs over time, providing better value in applications where durability is essential.
This depends on the type of machine but involves the transfer of the molten plastic to the injection barrel and subsequent injection to the mold.
If a company plans to have a mass-produced product, low volume injection plastic molding is the way to start. It helps to bridge the production gap between prototyping and production. This method brings a feasible prototype to production in a quick turn without requiring too much commitment. It also helps to fine-tune the product and the process.
For instance, minimizing power consumption such as using energy-efficient equipment or operational optimization will help minimize these costs.
Machining of aluminum molds occurs using end mills. Therefore, sharp internal corners may be a concern. Sharp corners on injection molded parts often create stress and compromise a part’s integrity. As such, it will be best to use vertexes or rounded edges (radii) for plastic part design. This will ensure a more substantial product and improved moldability.
RapidDirect, for example, now combines the latest Big Data analytics, software, and hardware to enable Industry 4.0 integration. This way, there is a guarantee for innovative approaches and best practices. It, in turn, results in smarter production and ensures the cost-efficiency of low-volume plastic parts production.
The proper choice of an injection molding machine type is important to ensure the balance between cost and performance. Each kind has its own specific benefits and costs, which affect the general effectiveness of production.
One of the most common mistakes you can make with plastic injection molding is choosing a better surface finish than necessary. This may badly impact the product’s functions. For example, very smooth surface finishes require hand-polishing of mold cavity surfaces. The polishing may be done with diamond buff up to 2 Ra.
The first step in narrowing down your choice is to use the company’s volume capacity and specialization. Companies capable of low to moderate production (pars under 10,000) are advised. This is because they can offer prototypes quickly enough for testing.
Your choice of material depends on the intended application of the low volume plastic parts and their operating environment.
Thermoforming is another alternative that involves creating molds over which there is the heating of a thin sheet of plastic formed using mechanical force, pressure, or vacuum which takes the mold’s shape with extra material being trimmed off.
From its name, on demand allows businesses to make parts based on demand. As a result, there is less need for large inventories leading to lower storage costs. Furthermore, it becomes easier to adapt to fluctuations in demand which makes low volume plastic injection molding suitable for businesses that operate in unpredictable industries.
We boast of a fast turnaround on our low-volume plastic injection molding services without compromising on quality. Choosing RapidDirect would mean that you get quality prototypes with short lead times and budget-friendly prices. Upload your design file, and let us offer you our best services.
The whole low volume injection molding process translates to a shorter lead time. In mold design, the use of aluminum known for its soft nature makes the mold manufacturing process easier and quicker.
The cost of plastic injection molding depends on several factors, including the complexity of the part, the number of cavities in the mold, the type of material used, and the production volume.
Undercuts make the matter complicated which requires more time for design and machining. Most of the times, such features are not possible to be incorporated due to the complex side actions, larger molds are needed. All of these factors substantially increase the tooling cost at the beginning.
Ejection of low volume plastic parts can be manual or via the use of ejector pins. In the latter, the clamping plate moves backward and the mold halves open. Afterward, the ejector pins push out the final part.
Sharp edges can inhibit the use of circular cutters to necessitate further EDM. This secondary operation is important for small features. Thin ribs more than 0.5″ (or thinner than .0625″) also require EDM.
These additional costs are crucial for guaranteeing that the parts meet the required standards and have been prepared for the market or for further assembly. It is much more beneficial to use simple post-molding operations in some cases as it will help to control these costs efficiently.
The rise of various advanced technologies continues to evolve the manufacturing space. In so doing, there is an increased potential to eliminate quoting delays and improve prototype manufacturing techniques. The visibility of orders within the supply chain becomes a lot more straightforward. Also, customers can manage their orders from anywhere via a convenient platform.
Aluminum has a better heat transfer rate than steel which reduces the complexity in positioning the cooling lines. Furthermore, it makes more room for more mold components. As a result, the low volume plastic manufacturing process ensures better design flexibility, closing the gap between prototyping and high-volume production.
Material costs and the level of production have a critical effect on the overall costs as well. Such elements are critical in effective cost management.
Incorporating draft angles leads to the production of low volume plastic parts with tapered edges. As a result, there is less friction during demolding, which prevents mold/part damage, and easier part removal. A good rule of thumb in injection molding is adding a draft angle of 1 to 2 degrees.
This pattern helps in creating a urethane mold and pouring suitable resin into the mold will allow the manufacture of several copies of the product. A urethane mold can last for up to 20 runs and is a cost-effective option that allows product designers to test design requirements and gather feedback early.
If you want to produce high-quality machined parts with a sleek appearance, it’s essential to consider some critical factors related to CNC machining.
The high volume of the process of injection molding is characterized by the production of hundreds of thousands to millions of parts, and it is accomplished in durable steel molds due to their long life.
These are home costs, and unlike overhead, these are costs associated with an operating facility. These overhead costs need to be managed and optimized in an effective way for profitability to be sustained.
Most engineers and designers prefer 3D printing for quick iterations during plastic product production. 3D-printed parts often come with layered surfaces. However, the surfaces can be easily sanded and painted for the desired surface finish.
The cost of injection molding per kg of material depends on the type of plastic being used. Common plastics like polypropylene or polyethylene can cost between $1.50 and $3 per kg.
Quality control involves inspecting low-volume plastic parts for any defect and ensuring they meet quality standards. Afterward, trim the molded parts and use secondary surface finishing operations.
The rapid manufacturing industry is in a massive transition state and with low volume injection molding, plastic part manufacturers can easily cater to the market needs as the process allows you to create a small quantity of plastic parts with consistent characteristics and qualities.
To reduce injection molding costs effectively, consider these streamlined strategies:Increase Production Volume: Distributing overhead set-up and mold costs over a larger number of units leads to reduced cost per piece, thus maximizing economies of scale for better performance.
RapidDirect is your number-one low-volume injection molding partner. We effectively combine our experience, expertise, and powerful facilities to get your plastic parts from production to market within a short time. Our rapid quotation system uses the latest technologies to give you quotes within seconds.
This involves using a clamping system that can generate a clamping force that holds the mold in place, closing the gap between the mold halves. The clamping force should be equal to the injection force to prevent disruptive movement and should be lower in 3D printed injection molds that are protected by a metal frame.
Polyethylene (PE) and polypropylene (PP) are among the cheapest plastics used for injection molding. They are widely available, cost-effective, and suitable for a variety of applications.
Up to 90% of costs at injection molding facilities are due to energy usage, which represents a substantial part of the total operational expenses. This will result in significant cost savings.
You must opt for an injection molding partner that offers a wide range of prototyping services. These include mold flow analysis, responsive manufacturing, and part design. Offering other manufacturing services such as CNC machining and injection molding will be a quality addition. Such companies will understand your requirements better and tackle production problems early.
With on-demand manufacturing, customers can order precise small series injection molding parts. The quantity on order will satisfy immediate production requirements. This will address several pain points regarding lead time, communication, design for manufacturability (DFM), and cost. With digital technology becoming central to the industry, on-demand manufacturing is leading a decent revolution.
Low volume production involves manufacturing smaller quantities in the small run. Therefore, there will not be any major impact if a company decides to modify or alter the design. That way, the product can be perfect before it gets to the consumer.
The larger the Part, the more materials are consumed, hence, the higher costs. Using correct size of injection molding machine and mold for these large parts is very essential.
Even with the fact that injection molding machines are automated, operators are still needed. They control the production process to make sure that everything goes fine, adding to labor costs.
The first step is the identification of the final plastic parts specifications and choosing the right materials. This will aid in the design of the mold. Metals are suitable for making injection molds with aluminum being the most popular.
If you wish to form multiple identical parts in a single shot, then a multi-cavity mold will be useful. It helps to produce two or more designs with tiny iterations at the same time. This enables the quick testing of different product designs simultaneously. Whenever there is a need for quantities beyond initial samples, they also serve as good options. At the same time, they can also help to reduce costs per unit.
The extremely high level of precision needed within the aerospace industry makes CNC machining a suitable manufacturing process for the sector.
The completion of the entire production cycle for such quantities takes approximately three days and therefore, this method is rather effective in prototype and small batch requirements.
Hydraulic machines work with a help of a hydraulic pump. They are characterized by strength and reliable functioning. These systems are cheaper in the first instance while having a higher power consumption and a less accurate performance.
Hybrid machines are a combination of electric and hydraulic technologies. They utilize servo motors and hydraulic pumps, thus, providing high accuracy and power savings.
By getting these factors, you will get the knowledge of how to reduce the costs strategically and get the efficiency and profitability of the projects of injection molding.
Techniques such as laser marking and pad printing are employed for adding intricate designs or instructions to the parts and are important for functionality and compliance in industries such as medical and aerospace.
This practice significantly increases mold manufacturing costs and lead times. A more cost-effective finish is an as-milled surface that probably shows some tool marks. The two other options available involve the use of 600 gritstone or bead blasting textured finish. The chosen finish must be compatible with the part’s function.
An important step in low volume injection molding is the right selection of material among the several commercial-grade plastic materials available for manufacturing.
Processes like ultrasonic welding, heat staking, and painting or texturing are used. These processes enhance not only the aesthetic but also the functional properties of the parts.
Electric machines use electro-servo motors to achieve accurate control. They are energy-saving with less operational costs. They are user-friendly. Nevertheless, they will need more upfront costs and also routine care.
A good on-demand injection molding company for producing a small batch of plastic parts must adhere to the best standards of efficiency and quality. The machines should work with the latest technologies with high-quality project management software for better communication.
In this guide, we’ll explore the key elements that influence plastic injection molding costs, helping you find the best balance between quality and cost-efficiency for your project.
In low-volume production, 3D-printed polymer resins or rapid tooling is often used by manufacturers, which is more cost-effective for shorter runs.
Installation of the injection molding machines needs accurate configurations by each production run. Preparing molds is precise work that requires time and a lot of skill.
Injection molding is a cost-effective solution for mass-production technique but with low volume plastic molding, small and medium-scale businesses can produce small quantities of plastic parts. This leads to faster market entry, better product quality control, shorter lead time, etc. This article talks about everything you need to know about small run injection molding so you can make a better-informed decision.
This volume is suitable for the products that need a balance of cost efficiency and volume, and is the best for the larger batches of standardized products.
In the UK, the cost of injection molding is influenced by factors similar to those in other regions. The price per part can range from £1 to £5 for small to medium production volumes.
Mid-volume injection molding is used to produce 5000-10000 parts. This scale typically demands pre-hardened steel or aluminum molds.
We are committed to helping you elevate quality standards, fostering enterprise growth, and actualizing your internationalization strategy.
CNC machining is a costlier alternative but is suitable for quick production runs. In some cases, a CNC machining technique such as CNC milling is combined with other processes like 3D printing for effective production or achieving tighter tolerances.
It is also applicable to make a small batch of a part providing an economical solution, especially for businesses without enough capital for large-scale production. It incurs lesser costs unlike traditional injection molding and supports small run production allowing businesses can respond quickly to changing market demands.
Hi, I am Sparrow Xiang, COO of the HiTop company, me and my team would be happy to meet you and learn all about your business, requirements and expectations.
Since the injection mold gets to the manufacturing facility a lot quicker, and it involves low production volume, production is fast. In many cases, this significantly accelerates time to market, making this technique beneficial for both small and large product teams.
Outsourcing injection molding is cheaper than buying equipment. This strategy eliminates the costs that are incurred in buying and maintaining machines.
By choosing the most suitable material for your needs, you can enhance production efficiency and product performance, ensuring that your investment delivers long-term benefits.
HiTop Industrial leads as a manufacturer of molds and supplier of injection molding services. Their skill guarantees customized, high-quality production. For any questions or more details, please feel free to contact HiTop Industrial.
GETTING A QUOTE WITH LK-MOULD IS FREE AND SIMPLE.
FIND MORE OF OUR SERVICES:
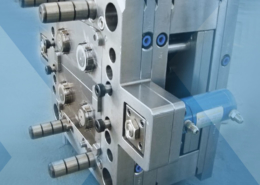
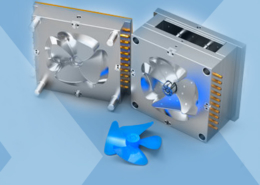
Plastic Molding

Rapid Prototyping
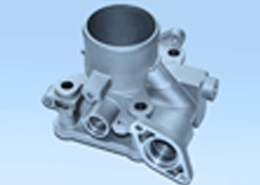
Pressure Die Casting
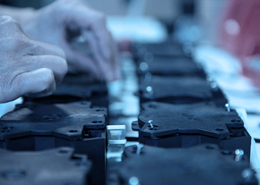
Parts Assembly
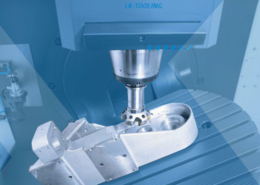