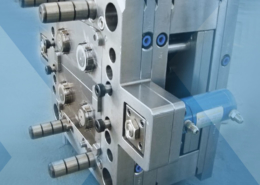
Top 3 Injection Molding Companies in Sri Lanka - plastic molds and moldings pvt
Author:gly Date: 2024-10-15
The foam injection molding machine then injected the material through the nozzle into the mold in a lower volume than the amount required to mold an object. Injection expansion and pressure of the polymer and gas then fills the mold. A porous surface is formed when the melt comes in contact with the cold surface of the mold. Then the foam injection molding expanding polymer mixture forms the cellular core.
Manufacture At Any Scale: Zeal 3D works with manufacturers to create tools and equipment in any quantity, from 1 to 10,000 pieces, enabling high or low-volume manufacturing at the most competitive pricing.
There is a wide range of rubber molding materials available in the market to accomplish different tasks. Some of the popular ones are:
Zeal 3D is an expert in injection molding and has the capacity to join fast prototyping procedures with ultimate ease. From high customization to complex design manufacturing, we do it all for you. We offer the best plastic mold manufacturing services for your every need. Search plastic injection molding companies near me and you will find Zeal to helping you about everything which you need to know about it.
One of the many industries that manufacture parts using the plastic injection moulding technique is defence. The injection moulding process is used in numerous applications in the defense sector for creating desired end-products.
Needs Less Post-Production: Since the parts typically have good aesthetic post-production, you will typically need very little post-production. You can create an injection moulding tool with a unique finish that will be immediately visible on the finished product.
The final step of this process includes sintering the remaining part at high temperatures (up to 1350°C) to reduce the space by around 1% to 5%, and it results in a high-density metal part. The furnace leverages inert gas to attaint's temperature of about 85% of the metal's melting point. This process helps remove pores and causes the part to shrink by 80% of its molded volume. The final part retains the original shape with higher tolerance levels.
Blow molding, another pivotal method in plastic manufacturing, is celebrated for its efficiency and speed. This process produces items ranging from plastic bags to bottles designed to hold makeup, chemicals, and soft drinks. By heating resin and inflating it with air, blow molding allows the material to conform to the mold's shape. The versatility and rapid production capabilities of blow molding have established it as a favored technique for manufacturing a wide array of plastic products.
Two-part injection moulding techniques called overmolding and insert moulding combine one material with a secondary substrate part or metallic insert to produce a single component. Our overmolding process shortens assembly time and increases the strength and flexibility of your parts by covering plastic, metal, and rubber over one another via chemical bonding.
By using this form you agree with the storage and handling of your data by this website. And agreed to get promotional emails.
Injection molding, a mainstay in plastic manufacturing, involves the meticulous process of heating resin pellets and injecting the molten material into a closed mold. This technique has revolutionized the production of an extensive array of products, including encapsulated electric coils, protective helmets, car bumpers, medical syringes, and various types of toys. Its precision and reliability have made injection molding indispensable in the creation of numerous everyday items.
Zeal 3D's engineering department uses state-of-the-art CAM programming equipment to send tool path instructions to our machines that will produce your desired part accurately. The quality is tested using automatic testers that ensure dimensional specifications are maintained right on target without any change.
Typically, the mould's surface preparation is finished throughout the manufacturing process. After the injection moulding is accomplished, we will give the end product-specific surface treatments in accordance with your specifications. Some of the high-end surface finishes are,
Even while using 3d printed injection mold for the MIM process, most of the rules are similar to the plastic injection molding. But, here are some additions that engineers need to follow:
The foam molding process is an ideal process for producing high-strength, lightweight parts. Many large-sized objects require thick walls than conventional injection molding, making the production more accessible. The structural foam brings a quick turnaround while working with thicker parts.
This streamlined approach enables the efficient production of durable, high-quality plastic goods, meeting a wide range of industrial needs.
Several industries including automotive, aerospace, and medical use robust metal parts manufactured using the metal injection molding process. Below are some of the commonly used metals used in MIM parts:
Next, the powder is molded utilising the same machine and tooling that engineers use in plastic injection molding. But in this method, the cavities are 20% larger to manage the part shrinkage during the sintering process. In the process, the machine first melts the feedstock and injects it into the mold cavity, where it cools and gets the desired shape.
In this process, the rubber is heated to a liquid stage before injecting it into the mold. The final product is obtained by opening the mod and then closing it to get the following injection process for producing molding rubber.
Zeal 3D is among the leading metal injection molding companies that cater to all your bespoke manufacturing requirements with ease.
Industries use several rubber molding solutions to accomplish respective structure and properties in the final product. There are majorly three types of rubber molding that are:
Injection molding is a prevalent and versatile plastic molding technique, known for its ability to produce three-dimensional, solid parts with mid to high strength. The cost of the process varies significantly based on the part‘s complexity and the materials used. What sets injection molding apart from other plastic molding methods is its capability to create relatively intricate shapes.
An injection moulded part's shiny and glossy surfaces are produced by A-grade finishes, which are created by involving a buffing process.
By using this form you agree with the storage and handling of your data by this website. And agreed to get promotional emails.
Using a platinum catalyst, a thermoset method called liquid silicone rubber moulding heat-cures a two-component compound in the mould to create the finished object.
Cost-Effective: Numerous copies of the same products can be produced. When you require parts with tight tolerances and high levels of dependability, injection moulding is the best option.
Injection molding is a robust manufacturing process used to make an enormous variety of products. It is a large-scale production method that is cost-effective for mid-volume production runs. In addition, it gives the manufacturer the ability to create complex items with fine detail accurately and efficiently. It is why injection molding has become so popular recently, as manufacturers are increasingly looking towards innovative processes to stay competitive in today's global market.
This is a sample text. You can click on it to edit it inline or open the element options to access additional options for this element.
High Detail: Under extremely high pressure, molten plastic is injected into the mould during the procedure. This forces the plastic firmly against the moulds, enabling the creation of detailed and complex shapes with lots of detail.
In the manufacturing process known as plastic injection moulding, plastic in a barrel is heated until it melts, at which point it is shot into a mould to create a finished thermoplastic item suitable for production. We are experts at designing and producing a variety of plastic injection moulds tailored to specific tolerance and budget with our expertise and cutting-edge equipment.
Blow molding is the versatile backbone of countless consumer products. From robust tanks to sleek CD cases, any hollow, three-dimensional item you can think of likely owes its existence to this innovative process. Blow molded products are designed to safely contain a wide range of substances, including herbicides, pesticides, cosmetics, and automotive oils. The secret behind this versatility lies in the thermoplastic resins used in blow molding, such as acetal, polysulfone, polyamide, polystyrene, butadiene styrene, Barex, polyvinyl chloride (PVC), and both high and low-density polycarbonate.
No MOQ Needed: Without needing a minimum order quantity, our staff will make the required effort to locate the supplies if you need manufacturing services utilizing materials that are not on the material list.
In this process, engineers keep a fixed amount of rubber compound into the mold cavity and then compress it into the shape of the cavity by closing both sides of the mold. In this process, the pressure remains the same while the heat is added to cure the product. Once the process is complete, engineers remove the final product from the mold.
Dip molding plastic stands as one of the most straightforward and cost-effective methods for producing a vast array of parts and products. This versatile process rivals blow molding in its ability to generate large quantities efficiently. Dip molding serves two primary functions in manufacturing: crafting complete flexible or rigid items, like rubber gloves, condoms, and plastic caps, and coating pre-manufactured items such as wire racks, cables, and plastic handles.
Extensive Material Support: Zeal 3D offers specialized 3D engineering services that cater to the client's needs and requirements using more than 45 different materials.
Plastic molding stands as a cornerstone in the world of manufacturing, integral to the creation of virtually every product available in today‘s market. The diverse methods employed in plastic molding contribute to the distinctiveness and innovation of its products. This versatility, allowing for the crafting of any shape, design, or configurationâno matter how intricateâis a testament to its widespread success and continued expansion.
The first step of metal injection molding is to form a powder mixture of metal and polymer, and the metal used in this process is much more refined (under 20 microns). The powdered metal is mixed with a heated thermoplastic binder, cooled, and then pulverised into a feedstock in pellets. The end feedstock consists of 60% of metal and 40% polymer.
Zeal 3d is a leading micro injection molding company that caters to all industrial requirements with higher accuracy and shorter turnaround time.
In this process, manufacturers utilize a standard injection molding machine, and the powder is melted before injecting into the mold. The powder cools down and solidifies into the desired shape during this process. After this, the heating process removes the unnecessary polymer to produce high-density metal objects.
Another benefit of leveraging this technology is that it's a very cost-effective molding process that produces robust products. With minimum warpage, the parts have superior durability.
In this step, the machine removes the polymer binder from the metal, and in many cases, engineers use solvent debinding to dissolve most of the binder. Once this step is complete, engineers perform the thermal debinding process. In this process, the molds are heated at a low temperature, and it helps in removing the polymer binder through evaporation.
Rotational plastic molding is a powerful process for producing plastic parts with exceptional strength and intricate structural details, surpassing the capabilities of other molding techniques. This method is distinctive in that it generates parts in relatively low volumes, making it ideal for specialized, short-run production. While it may not be suitable for mass production like blow molding, dip molding, or thermoforming, it is the go-to process for creating complex and high-performance components such as detailed plastic figurines and military-grade rackmount carrying cases.
This process is ideal for producing high-volume small metal parts with complex geometric designs. Metal injection molding can efficiently create objects with thin walls. Engineers can use a variety of ferrous and non-ferrous alloys and get the desired material properties. Our metal injection molding machine offers a tolerance level of up to ± 0.005 in and Max wall thickness of 0.04 to 0.25 in.
If you are launching a new automobile and need custom product designs, we have the best custom injection molding expertise and services. Our industrial plastic parts designs are also utilized by building and construction, food packaging, and medical industries. Whenever think about Injection Molding services, think of the largest plastic injection molding company in the world i.e Zeal 3D.
Being a leading provider of injection molding service, we offer a wide range of manufacturing services to OEMs. From gears to brackets, enclosures, knobs, pulleys, automobile parts, toy parts, robot parts, etc., we make thousands of molded plastic parts. We also offer an online injection molding service for which you just need to load your 2D or 3D CAD file on our website for an instant free quote. We provide free design assistance for our clients who needs alteration in the design of their product for Injection Molding.
Zeal is a leading company offering you on-demand plastic injection molding services. Regardless of your industry, Zeal offers you full-fledged plastic injection molding solutions to cater to all your manufacturing requirements.
Accuracy of final injection molded products depends upon the various factors like material, tooling, the geometry of the product, and surface finishes. The possible tolerance of most thermoplastic is ±0.2 to 0.5mm.in few specialized applications tolerances are low as ±5 µm on both diameters and linear features are achieved in mass production Surface finishes of 0.0500 to 0.1000 µm or better can be obtained. Rough or pebbled surfaces are also possible.
Australia Wide Fastest Delivery: In Australia, including Melbourne, Perth, Sydney, Brisbane, Canberra, Adelaide, Tasmania, and New Zealand, Zeal 3D offers the quickest delivery options for 3D metal printing.
Zeal Injection Molding Services and plastic molding manufacturing services additionally offer its clients an extensive variety of auxiliary administration alternatives that incorporate machining, powder covering, silk screening, painting, and ultrasonic welding. Zeal Injection Molding Services utilizes the most recent machines to deliver high-quality plastic products.
The wall thickness should be minimal, and it should be uniform throughout the part production. Minimising the wall thickness helps in reducing material volume and sintering times.
Twin sheet thermoforming is often employed for creating large, precision parts such as hot tubs and aerospace interior wall panels. Beyond these specialized applications, thermoforming offers a highly cost-effective method for producing three-dimensional plastic packaging. Vacuum forming can efficiently manufacture blister packs, clamshells, plastic covers, and trays, delivering low-cost solutions at high production volumes.
It is an ideal method for producing tiny components with higher design precision and accuracy. This mini injection molding begins with creating smaller cavities to form the desired shape. Resin or thermoplastics are rapidly injected into the cavity to form components at a higher speed.
In the realm of fiberglass-reinforced plastic manufacturing, fiberglass molding stands as the cornerstone process. Fiberglass is created when molten glass is meticulously drawn through minuscule apertures in specialized tools, resulting in fine, threadlike structures. These threads undergo further refinement through heat treatment or pressing and are then amalgamated with plastic resin to form the desired material.
Purchasing high-quality construction components, including injection moulded plastic building products and assemblies, is one of the keys to the success of architecture projects.
Blow molding can be broken down into three primary techniques: injection blow molding, extrusion blow molding, and stretch blow molding. Each method follows a two-step process, with variations primarily occurring in the initial stages. The final shape of the plastic product is determined by the mold cavity, allowing for an extensive range of standard shapes and sizes. Additionally, custom blow molding offers the flexibility to create unique products tailored for specialized applications, demonstrating the boundless possibilities of this dynamic manufacturing process.
Zeal 3D Services offers comprehensive services for prototyping and producing parts through a plastic injection molding process. We have advanced plastic moulding injection machines, skills, and experience to design and manufacture injection-molded plastic parts. Our plastic injection molding services are suitable for a variety of industries for designing and manufacturing high-quality plastic products for both high-volume and low-quantity parts production. We manufacture and supply durable, functional, and cost-effective plastic injection molded products defence, automotive, medical, aerospace, and consumer industries. We are among the best plastic injection molding companies that offer an amazing range of services for the Australian and overseas markets.
On the other hand, vacuum forming offers a distinct approach to plastic molding. Instead of heated resin pellets, this method uses plastic sheets, which are thermoformed by being forced into an open mold. This technique, free from the constraints of a two-part mold, is instrumental in manufacturing components like spacecraft walls and hot tubs.
Be it automotive, construction, computing, electrical, and electronics, Zeal offers clients a wide variety of molding processes to produce the best quality plastic products. We have a proven track record of supplying high-quality parts that meet each client's distinct requirements in terms of design, dimensions, and surface finish.
While performing sintering, the MIM parts need robust support, or the parts will get distorted as they shrink during the process. Engineering can use standard flat support trays or use custom supports if required.
Plastic extrusions are crafted in a manner akin to injection-molded plastics, but with a distinctive twist: they take shape through an open die. The process begins as plastic resins, including PVC, acrylic, polypropylene, or ABS, are funneled into a hopper and fed into the extruding barrel. Here, the resin is sheared and melted before being propelled through the open die to form a specific profile or shape. This newly formed profile is immediately submerged in cold water to set the plastic. The continuous extrusion process sees the profile passing through the die, cooling in water tanks, and arriving at a sawing table, where it is cut into pre-determined lengths.
What sets rotational molding apart is its unique process. Molten polymer, often polyethylene or polycarbonate, is poured into a closed, three-dimensional mold. This mold is then placed in a gyroscope-like machine that rotates slowly, allowing the polymer to coat the entire interior evenly, forming a hollow structure. This technique not only excels at crafting complex shapes but also ensures that the parts have uniform material consistency, resulting in very high strength and durability.
Polyurethane stands out as a versatile material prized for its dual flexibility and rigidity, making it indispensable in memory foam products. Its utility extends to solid plastic forms, polyurethane rods, urethane wheels, bushings, and sheets. Renowned for high performance, polyurethane moldings surpass plastic in durability and outshine rubber in impact resistance. They boast elastic memory, noise reduction, and resistance to heat and chemicals, embodying the best attributes of metal, rubber, and plastics. Moreover, polyurethane can form robust adhesive bonds with most plastics and metals.
We have a wide range of materials available for injection molding. The selection of material from the wide range of different grades of these materials can be a challenging task but our team of expert engineers will help you to select the most suitable material for your application.
C-grade finishes provide a rough, uneven surface using grit sanding stones. C-grade finished injection plastic components have a matte surface texture.
Grit and dry glass beads are used in D-grade finishes to provide a highly rough textured finish. Products might have a smooth or dull finish based on the type of material utilized.
One of the primary advantages of plastic molding is its adaptability to a broad spectrum of materials. These include fiberglass-reinforced plastics, polyurethane, polypropylene, polyvinyl, and various types of acrylics. Each material undergoes heating and shaping through specific processes tailored to the final product‘s form, required strength, and design complexity. This flexibility ensures that plastic molding can meet the demanding and varied needs of modern manufacturing.
The plastic molding industry continues to expand, playing a crucial role in the design and production of numerous household and industrial products.
Plastic injection molding is a faster and low-cost manufacturing process for quality and functional plastic products for a variety of uses across all industries. Our designers are experts in creating 3D CAD models with complex features and using laser-based rapid prototyping methods. We recommend all our clients to get injection molding to test fitting and functionality before going for production. Easy testing, assembling, and manufacturing are various advantages of rapid prototyping.
Low Waste: In comparison to several other manufacturing techniques, injection moulding generates a very little amount of waste. Even if there is any leftover or trash plastic, it can be recycled and used again.
By using this form you agree with the storage and handling of your data by this website. And agreed to get promotional emails.
The dip molding process follows a simple yet effective sequence. First, a large batch of glass or metal molds undergo surface preparation to ensure the final product easily releases once dry. For items being coated, meticulous buffing and prepping ensure the plastic adheres securely. These molds are then immersed in a vat of molten polymer or elastomer resin. Depending on the desired thickness and material consistency, molds may undergo multiple dips, sometimes alternating between the polymer bath and a cold water or solidifying reagent. Complex layered products, like kitchen gloves, might incorporate additional layers, such as fabric, between polymer coatings. Once the plastic sets, the product is ready for removal, trimming, cleaning, and finishing.
High-Quality Assurance: In order to reach the highest level of customer satisfaction, Zeal 3D makes a significant effort to ensure quality assurance and continuously delivers high-quality goods with strict tolerances.
With Zeal 3D services, we can support any of your injection molding needs and provide you with the best service and products at every step of your project. This ranges from design assistance to prototype verification or full-scale production, all by the highest quality standards.
Micro molding is an advanced and highly specialized manufacturing method that can produce tiny plastic components with extreme intricate geometries. This process can manufacture parts weighing from 0.1gm to 1gm and tolerance levels of 10 to 100 microns.
We are proud of being one of the top custom injection molding suppliers for manufacturers whose injection molding cost is lower than any market. Our team is skilled in producing high-precision and durable plastic injection molded parts. We work with advanced machines to handle our customers' needs for injection-molded parts from low to moderate, and large quantities in any 2D and 3D shapes. Whether you want to turn concepts into reality, enhance product design, or conduct injection molding and testing, we can provide a high degree of precision and aesthetic appearance to meet international standards.
The rubber molding machine creates molded rubber parts by hard pressing a rubber's block into a molding metal cavity. When the rubber is exposed to heat, it activates a chemical reaction, and there are several variations in this process to achieve the desired quality. The most popular variation methods are compression molding, transfer molding, and injection molding.
Rubber molding is a molding process that manufactures usable rubber items produced from uncured elastomers or rubber. Elastomer is any rubber molding materials that have good resilience for returning to the original shape when applied.
High-end Service Provider: Zeal 3D, a provider of 3D engineering and modern digital manufacturing services, is dedicated to constantly providing products and customized services that satisfy customers' expectations and adhere to regulatory requirements.
Efficient High Production: The cost per part for large volume production runs is quite cheap. By employing plastic moulds rather than metal ones, you may save costs even for medium volumes, or between 10,000 and 25,000 pieces.
This process offers several advantages to manufacturers. To begin with, it is a highly versatile process for manufacturing all kinds of plastic parts. It is ideal for producing items that range in size from fractions of millimetres up to several metres in length and creating them with amazing intricacy and detail.
To enhance the strength and durability of many products, they often require a protective coating. One effective method to achieve this is dip molding. This process involves immersing a completed product into a bath of resin. After being thoroughly coated, the product is removed and subjected to a drying process, which cures and hardens the plastic coating. Dip molding is a precise technique that significantly enhances the quality and resilience of various products.
Plastic tubing encompasses a wide range of tubes and pipes made from various plastics. Its versatility ensures its presence across numerous industries, from the stringent demands of aerospace and industrial applications to the sterile safety standards required in medicine and beverage tubing.
Most of the components used in the aircraft sector are manufactured using aerospace plastic injection moulding because of the number of advantages they provide.
Metal injection molding process consists of four significant production steps that turn powder from raw materials into a robust solid object. The process has the following steps:
Polyurethane molded parts typically require minimal to no finishing, streamlining the manufacturing process. This efficiency makes polyurethane the material of choice for producing a diverse range of products, including moldings, parts, bowling balls, urethane bumpers, belts, conveyor bushings, electrical potting compounds, press tool blocks, and pneumatic seals. Its applications span numerous industries such as athletic equipment, engineering, manufacturing, industrial, food processing, automotive, and construction. Discover the transformative potential of polyurethane molding.
Automobile plastic injection moulding is a crucial production technique in the automotive sector, where reliability, stability, and quality are of the highest importance. It is used to produce auto parts like,
Rotational molding, a specialized plastic processing technique, excels in creating individual and large-scale plastic products such as expansive bins, high-quality auto parts, boats, and sports equipment. This process utilizes a heated hollow mold filled with a precise amount of plastic material. As the mold rotates slowly, the plastic evenly coats the interior walls, resulting in products with exceptional strength and structural complexity.
Another highly popular and versatile molding technique is plastic extrusion. This process is renowned for its ability to create a vast array of flexible, sturdy, and durable products. Like other plastic molding methods, extrusion begins with heating resin. However, instead of placing the resin into a mold, extrusion involves forcing it through a die that shapes the resin into the desired profile. This efficient and rapid process is capable of producing products tailored to a wide range of applications, making it a cornerstone in the field of plastic manufacturing.
Zeal 3D Services excels in plastic injection moulding, offering high-quality, cost-effective parts for industries like defence, automotive, medical, and aerospace. With advanced machines and expert skills, we provide comprehensive services, including free design assistance and instant online quotes. Trust Zeal 3D for all your injection moulding needs.
Metal injection molding is an advanced variation of conventional plastic injection molding that allows engineers to perform fabrication of solid metal parts. In this metal molding process, the raw material called feedstock is the powder of metal and polymer.
In rubber transfer molding, the rubber compound is placed at a specific part of a mold called a pot before being pushed against a cavity to get the desired shape. Once the curing process is done, the mold is split while relating the product.
Fiberglass molding finds its application in a diverse array of products, ranging from machinery support components and electric circuit boards to the sleek shells of racing cars and durable panels. Its widespread use is attributed to the remarkable properties of fiberglass: it remains stable across temperature fluctuations, resists water absorption, withstands chemical exposure, boasts a high strength-to-weight ratio, is non-flammable, and is an excellent electrical insulator. These characteristics make fiberglass molding an indispensable technique in modern manufacturing.
Vacuum-formed plastics serve as faceplates and semi-flat components across various industries, particularly in electronic devices like fax machines, keyboards, phones, and home appliances. This process, also known as thermoforming or pressure forming, starts with plastic sheets instead of polymer resin pellets. These sheets are heated until pliable, then vacuumed into an open mold, where they conform precisely to the shape of the die beneath.
Several industries including, medical, automotive, and electronics manufacturing, require small injection molding processes to create minuscule parts. Following are some of the sectors using micro molding:
Extruded plastics are tailored to meet a wide array of specialized applications, such as building trim, window and door sealants, vinyl siding, PVC pipe, and surgical tubing. Additionally, plastic sheets and flexible plastic sheet rolls are produced through extrusion. In this variant, the melted plastic is stretched rather than cooled after exiting the die. Flexible sheets pass through a series of large calenders before being rolled onto a tube. Discover more about the fascinating world of plastic extrusions.
Advanced injection molding techniques include insert molding and reaction injection molding (RIM). Insert molding involves injecting molten plastic around a solid object, such as an electric coil, to create an encapsulated product. On the other hand, RIM combines a liquid resin thermoset polymer, typically polyurethane, with liquid polyisocyanate. The polyisocyanate acts as a reagent within the mold, causing the polymers to expand and form either open or closed cell foam, effectively filling the mold.
The foam injection molding process is a low-pressure injection molding process in which the machine introduces inter gases into the melted polymer to reduce the density of the product. The structural foam molding creates products that have cellular cores surrounded by integral and rigid skin. While making the homogenous mixture of polymer and gas, engineers use foaming agents, including NI, CO2, or CBA.
B-grade parts have a slightly rougher polish than A-grade parts due to the application of grit sandpaper. B-grade finished custom-moulded plastic components have quite a matte surface texture.
Zeal 3D is a leading rubber and silicone injection molding company that brings in the complete range of molding across industries.
Unlike the traditional plastic molding process, MPM parts don't require any draft. The polymer binder that is used in the powder material releases quickly from the mold.
GETTING A QUOTE WITH LK-MOULD IS FREE AND SIMPLE.
FIND MORE OF OUR SERVICES:
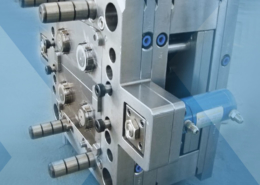
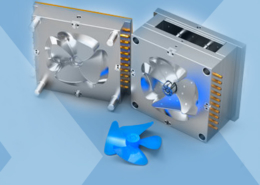
Plastic Molding

Rapid Prototyping
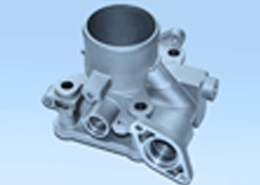
Pressure Die Casting
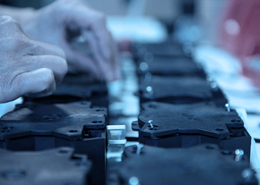
Parts Assembly
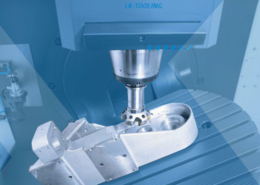