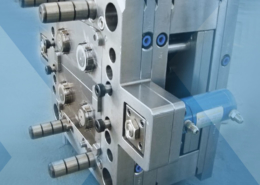
Top 10 Tips for Designing an Effective Injection Molding Die - injection molding
Author:gly Date: 2024-10-15
As technology continues to evolve, rapid injection molding is expected to become even more efficient and versatile. Several advancements in materials, processes, and machinery are on the horizon, promising to further revolutionize the industry.
Rapid injection molding offers a range of advantages that make it an attractive option for both prototyping and short-run production.
Its ability to quickly produce high-quality parts, especially for prototypes and small production runs, makes it an invaluable tool for industries like automotive, healthcare, and consumer goods.
Many industries have adopted rapid injection molding due to its speed, precision, and flexibility. These sectors require quick turnarounds and high-quality products to remain competitive in the market.
This innovative approach not only accelerates production timelines but also significantly reduces costs, offering a competitive edge in today’s fast-paced market.
Despite its many advantages, rapid injection molding comes with its own set of challenges. Being aware of these issues can help manufacturers avoid pitfalls and streamline the process.
This speed advantage is especially beneficial for industries that demand fast turnaround times, such as consumer goods and electronics, where product lifecycles are shorter, and time-to-market is crucial.
Several advanced technologies support the rapid nature of this injection molding process, enabling manufacturers to create highly accurate parts in a fraction of the time required by traditional methods.
One of the standout reasons to choose rapid injection molding is its flexibility. This process enables companies to experiment with different materials, design iterations, and product variations quickly, allowing for faster adjustments and improvements without the lengthy setup times of traditional methods.
Unlike conventional methods, this process focuses on reducing tooling time while maintaining the precision of the final product.
Optimization is key to ensuring both efficiency and quality in the rapid injection molding process. By fine-tuning various aspects of the procedure, manufacturers can maximize their return on investment while producing high-quality parts.
Precision is a hallmark of rapid injection molding. With advanced technologies like high-speed machining and 3D printing, manufacturers can achieve tight tolerances and complex geometries that would be difficult or time-consuming with other methods.
ACIS®, Autodesk Inventor®, CATIA® V5,Creo™ Parametric, IGES, Parasolid®, Pro/ENGINEER®,Siemens PLM Software’s NX™, SolidEdge®, SolidWorks®, STEP
This precision also leads to better product performance, especially in applications where detailed features or intricate designs are essential.
This innovative method blends the speed of prototyping with the scalability of mass production, offering manufacturers a competitive edge.
As industries push for faster turnarounds without compromising on quality, rapid injection molding becomes a go-to solution. Its relevance spans across multiple sectors, helping businesses meet tight deadlines while maintaining the high standards required for complex products.
The rapid injection molding process follows a structured series of steps, ensuring speed and accuracy from design to production.
Depending on the complexity of the part and the process used, molds can be designed and produced in as little as a few days.
As advancements continue to push the boundaries of this technology, manufacturers can expect even greater efficiencies, better materials, and more sustainable processes in the future.
The decision to choose rapid injection molding over other manufacturing methods depends largely on the specific needs of the project.
By using exact mold designs and accurate material injection, rapid injection molding minimizes defects, ensuring that each piece meets the required specifications.
In a recent exploration by 3ERP, the numerous advantages of rapid injection molding are meticulously examined, highlighting its transformative impact on manufacturing processes.
Rapid injection molding is an accelerated version of traditional injection molding, designed for quick production of plastic parts using pre-engineered molds.
Additionally, high-speed CNC machining plays a pivotal role in creating mold inserts with precise tolerances, ensuring that every part meets strict quality standards.
In today’s fast-paced manufacturing world, efficiency and precision are paramount. One technology that has revolutionized production is rapid injection molding.
This method stands out as a pivotal solution for industries aiming to optimize their production cycles and respond swiftly to market demands.
By understanding when and how to implement rapid injection molding, businesses can stay competitive and meet the ever-evolving demands of their industries.
By integrating rapid injection molding, companies can achieve enhanced precision and scalability, ensuring high-quality outputs with shorter lead times.
Before adopting rapid injection molding, manufacturers should consider several factors that can impact the success of the process.
Speed is one of the key differentiators of rapid injection molding, and it directly impacts production cycles. Compared to traditional injection molding, which can take weeks or even months to create a mold, rapid injection molding significantly reduces lead time.
Rapid injection molding is not the only manufacturing method available, and it is essential to understand how it compares with other popular techniques, such as CNC machining and traditional injection molding.
Design is a critical aspect of the rapid injection molding process, as optimizing the design can improve efficiency and product quality.
Rapid injection molding offers a variety of benefits, making it an appealing choice for manufacturers. The core advantages revolve around speed, precision, and the ability to produce high-quality parts in shorter lead times compared to traditional injection molding.
Choosing the right material is essential for achieving the best results in rapid injection molding. Different materials offer unique properties, making them more suitable for specific applications.
GETTING A QUOTE WITH LK-MOULD IS FREE AND SIMPLE.
FIND MORE OF OUR SERVICES:
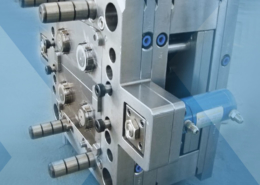
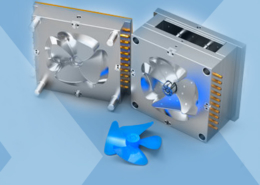
Plastic Molding

Rapid Prototyping
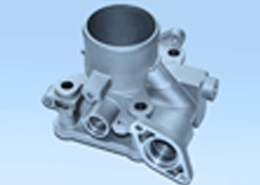
Pressure Die Casting
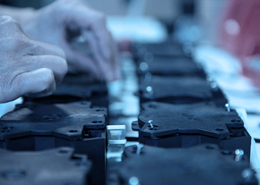
Parts Assembly
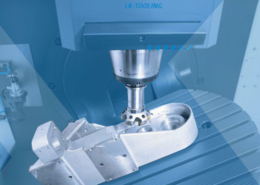