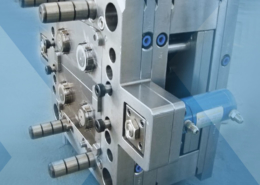
Top 10 Tips for Designing an Effective Injection Molding Die - injection molding
Author:gly Date: 2024-10-15
The prototyping phase allows for short runs using a prototype mold (often tooled in aluminum) in order to ensure the product specifications are optimal before investing in the tooling of a steel production mold. Along the way we will have also determined which of our fleet of 70+ injection molding machines are best suited for full production runs of the plastic item. As a manufacturing process, custom injection molding is often the most cost-effective solution for many medical devices and parts.
The above is just an overview of a small sample of plastic resins available for use in the injection molding process for medical and dental devices. Rest assured the experts at Global Plastics will know which plastic material is the best option for your specific project.
With decades of experience in managing a diverse range of injection molding projects from beginning to end, Global Plastics invites you to learn more about our services. We work tirelessly to achieve cost effectiveness while maintaining the highest quality possible for every medical device, part, or component we produce. Our ability to efficiently deliver a solution that achieves the desired result is how we’ve built our reputation in this highly competitive industry with each customer client. We’d be honored to do it for your company as well. Use the contact us form on our website to learn more about our plastic medical device injection molding services.
The driving force behind our molding process is our process engine which carefully analyzes and guides our technicians to ensure optimal conditions to help create your consistent custom molded plastic parts. We provides quick-turn thermoplastic injection molding often used for prototyping, bridge tooling and short-run manufacturing up to 10,000+ parts. We use advanced aluminum alloy molds that allow us to eliminate the costly and time-consuming custom engineering that normally goes into the development of tooling. We offer hundreds of engineering-grade resins that produce molded parts that are strong and can have excellent finishes. For more production efficiency, we utilize all electric presses to provide you with the highest quality injection molding services. Electric Machines use 80% less energy than standard hydraulic machines and provide for a more controllable plastic injection process. Our machines range from 50 to 450 tons, combined with Proprietary Process Engine enables us to manufacture your custom parts more consistently and at the best possible price. Whether your product requires a single cavity, open and shut mold, or a complex, multi-cavity, multiple-gate, multiple-action tool, we can handle your job. Start a quote today and see how we can deliver your parts in 1-15 days.
While the number of different plastic devices and components used in the medical industry and dental industry seem nearly infinite, there are a variety of “usual suspects” in constant high demand among injection molding manufacturers, including the following:
Applicable regulatory frameworks must be consulted, whether those of the FDA (U.S. Food and Drug Administration) or ISO 13485 standards related to medical devices, and whether clean room or white room manufacturing environments are needed.
Global Plastics has Safe Quality Food (SQF) certification for manufacturing food packaging materials and plastic molded food closures.
The process that results in finished, high-quality plastic medical devices and related components requires a number of key pieces to be in place. In the product design phase, the device or part must be conceptualized with design engineers to determine essential specifications and parameters, including intended use. Early on in this process, choosing the right plastic material for the project is critical—and there are thousands from which to choose.
As injection moulding company, we always serve the best for our customer. We utilize all electric presses to provide you with the highest quality injection molding services.
The number of different plastic resins available today is staggering. Choosing the right plastic material is an essential step for any plastic medical device or component based on its intended application. Available plastic materials include the following:
GETTING A QUOTE WITH LK-MOULD IS FREE AND SIMPLE.
FIND MORE OF OUR SERVICES:
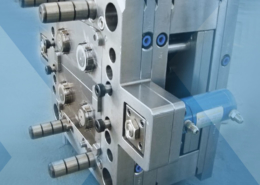
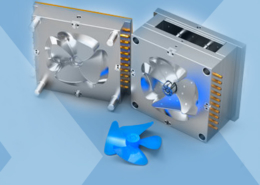
Plastic Molding

Rapid Prototyping
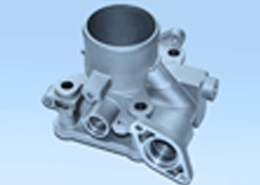
Pressure Die Casting
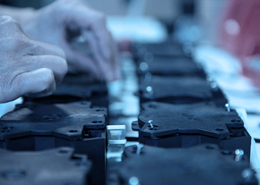
Parts Assembly
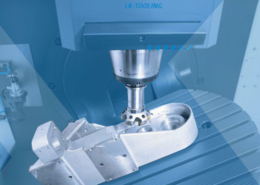