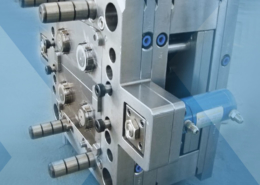
Top 10 Chinese Injection Molding Companies: Affordable ... - top 10 injection mo
Author:gly Date: 2024-10-15
Unmatched Lead TimesReduce your product development cycle by weeks—sometimes months—and bridge to production with injection-molded parts within days. Some injection molding orders can ship in as fast as 1 day.
Overmolding and insert molding are two-part injection molding processes where one material is overlaid onto a second substrate part or metal insert to create a single component.
In most cases, we can maintain a machining tolerance of +/- 0.003 in. (0.08mm) with an included resin tolerance that can be greater than but no less than +/- 0.002 in./in. (0.002mm/mm).
Proto Labs, Inc. 5540 Pioneer Creek Dr. Maple Plain, MN 55359 United States P: 877-479-3680 F: 763-479-2679 E: [email protected]
No one ever said that designing and manufacturing molded parts was easy. Our goal is to get you through it quickly and with quality parts. A good starting point is our Design for Moldability Toolkit.
Aluminum moldsStandard lead times as fast as 7 daysTolerances of +/-0.003 in. plus resin tolerance (in./in.)Set-up fees apply to each run Consultative Design Services (CDS)Finishing OptionsNo minimum order quantities (MOQ)Quick-turn shipping in as fast as 1 day
Injection molding is plastic manufacturing process that can produce high quality parts at scale. It's typically used for low- to high-volume production but our aluminum tooling can also make prototyping runs economical.
Liquid silicone rubber molding is a thermoset process that mixes a two-component compound together, which is then heat cured in the mold with a platinum catalyst to produce a final part.
Get machined parts anodized and chromate plated with our quick-turn finishing option. Eligible materials include aluminum 6061/6082 and 7075.
We have two unique offers to meet your needs wherever you are in the product lifecycle. Our prototype injection molding process helps you cut product development cycles by weeks—sometimes months—and bridge to production with injection-molded parts within days. Our On-demand Manufacturing process is designed to meet your production needs, and helps you qualify parts quickly to seamlessly transition into production with scientific molding, in-process CMM inspections with GD&T, and a full suite of secondary operations to make sure that your parts show up and perform as expected.
Make the move from prototyping to on-demand manufacturing for affordable, high-quality molded parts within days. Better yet, your prototyping tool is free once you shift to an on-demand manufacturing tool. Working with a single supplier that provides free design consultation services also massively speeds up the manufacturing process, allowing for greater supply chain flexibility, more consistent parts, and making qualification a breeze.
Creating more sophisticated molds necessitates technical knowledge. As a result, companies typically outsource specific aspects of injection molding, for instance, mold design and production.
Yes, we offer a production tooling option called on-demand manufacturing. This tooling option provides several benefits: lower piece part price, multi-cavity capabilities, guaranteed tooling for the life of the project (we will cut a new tool if it wears out), and first article inspections.
No Minimum Order Quantities (MOQs)Procuring parts on demand, without MOQs, helps you manage market or demand volatility and provides a cost-effective source for bridge production, line-down emergencies, end-of-life production, or product customization.
Injection molding, the major cost driver is generally mold or tooling expenses. Molds for injection molding are typically created in one of three ways:
Typically, the cost of the mold, also referred to as the tooling cost, is the major cost driver in injection molding. Let’s take a look at some of the elements that influence the price of an injection mold.
Because of the initial capital investment in tooling, injection molding makes sense for higher volumes of parts. Our mold cost starts at $1,495 and will vary depending on part geometry and complexity. Other factors that will impact injection molding cost are lead times and material.
The simple answer is that plastic injection molds range in price from $100 for a 3D printed injection mold to $100,000 plus for a sophisticated multi-cavity steel mold for greater manufacturing loads, which is typically the most important fixed start-up cost in injection molding. However, because these expenses are spread across hundreds or thousands of components, injection molding is a suitable method for mass-producing plastic parts at a low cost.
We have wide selection of more than 100 thermoplastic and thermoset materials. And if you're looking for alternative material options, check out our guide to resin substitutes for ABS, PC, PP, and other commonly molded plastics.
3D printers can manufacture basic low volume 3D printed molds for as cheap as $100. A metal mold for a mid-volume service life of 1,000-5,000 units costs between $2,000 and $5,000. Mold costs can range from $5,000 to $100,000 for molds with more complicated shapes and prepared for higher production runs of 10,000+ pieces.
For injection molding, special-purpose equipment ranging from tiny personal molding machines that enterprises may use in-house to big industrial injection molding equipment primarily handled by providers, contractors, and major manufacturers is utilized.
We do quoting a little differently. When you request an injection molding quote, you'll not only receive accurate pricing, but also a manufacturing analysis—within just a few hours. Our online quoting platform also provides you with gate and ejector pin layouts and a price curve tool to help select the best tooling option for your project.
If a plastic injection mold factory has the tools and materials, creating molds in-house may be the most cost-effective option if the technical expertise is also accessible. If the tools required for injection molding are not easily accessible, outsourcing lowers the cost of developing a mold.
We combine scientific (or decoupled) molding techniques, which optimize and lock in processing parameters to ensure part consistency—with extra attention paid to critical-to-quality dimensions using our proprietary automated CMM process. Plus, with every order you'll get:
Mold manufacturer location: This was also mentioned while researching how mold size may affect your total injection molding expenses. To have your mold wherever it needs to go, an off-site plastic injection mold maker will charge you extra for shipping and handling.
Injection molding is widely used for plastic part production in medical, consumer, and automotive industries. Typical parts include:
Our helpful design aid demonstrates part features that are too thin or too thick, bad bosses, right and wrong ribs, and other considerations to be mindful of while designing parts for injection molding.
Depending on the needs of the finished products, a broad range of polymers can be utilized for injection molding. The cost involved when you buy plastic injection mold materials varies depending on the material selected. Thermoplastic pellets range in price from $1 to $5 per kilogram.
Material cost is determined by the design of a product, the material utilized, and the quantity of material needed to complete the injection molding process.
To a certain degree, asking for the costs of plastic injection molds cost is similar to questioning how much a car costs. Is your mold going to be a Pinto or a Porsche? Also, keep in mind that the cost of a mold is only the beginning. To calculate complete plastic injection molding costs for any projects, you must also include raw material, operating, and maintenance expenses in the future. These costs are a result of the aforementioned contributing factors.
Tough Black (Loctite Henkel 3843) and Ceramic-Filled (BASF 3280) are two new advanced photopolymer materials now available for 3D printing.
When it comes to injection molding prices, basic plastic injection molds might range from $3,000 to $6,000. A big, more sophisticated high-production, cross-cavity mold can cost between $25,000 and $50,000 or more. Although it may seem obvious, several factors contribute to the cost of injection molding.
With small desktop injection molding equipment and 3D printed molds, creating modest volumes of components with injection molding is the most cost-effective. Small-scale automated injection molding machines are viable options for medium-series manufacturing of small components.Large industrial injection molding machines can range in price from $50,000 to more than $200,000. These machines also have more strict facility requirements and the need for specialized staff for operations, upkeep, and monitoring. As a result, although injection molding is a core competency, most businesses outsource mass manufacturing to service providers and contract manufacturers, with equipment expenses included in the service prices.
Design for Manufacturing FeedbackEvery quote includes real-time pricing and design analysis. We evaluate your 3D CAD and help identify any features that may pose challenges during the molding process such as difficult to machine undercuts and insufficient draft.
Plastic injection molding is a manufacturing process where resin in a barrel is heated to a molten state, then shot into a mold to form a final production-grade thermoplastic part.
Our digital factories create prototypes and low-volume parts fast, while our manufacturing network, offers advanced capabilities and volume pricing.
This complete reference guide walks you through everything from quoting, design analysis, and shipment to best practices that ensure your model is optimized for molding.
Injection Molding ExpertiseWe'll work with you throughout the course of your project to help you quickly move from prototyping to production, including finishing options and inspection reporting.
GETTING A QUOTE WITH LK-MOULD IS FREE AND SIMPLE.
FIND MORE OF OUR SERVICES:
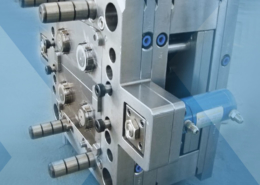
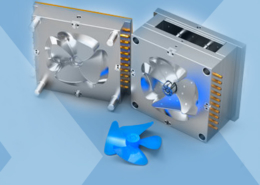
Plastic Molding

Rapid Prototyping
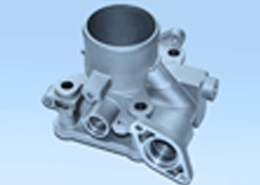
Pressure Die Casting
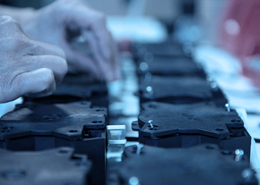
Parts Assembly
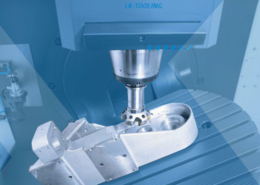