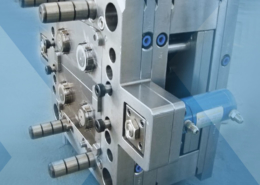
Top 10 Chinese Injection Molding Companies: Affordable ... - plastic injection m
Author:gly Date: 2024-10-15
Before proceeding with full-scale production, conduct thorough testing and prototyping. This phase helps identify design flaws, evaluate functionality, and make necessary adjustments without incurring excessive costs.
Wasting materials isn’t just detrimental to the environment; it’s also costly for your business. With low-volume injection molding, you produce only the quantity of parts you need, minimising excess inventory and material waste. This sustainability aspect not only aligns with environmentally conscious practises but also contributes to a more efficient and cost-effective production process.
Designing parts for low-volume injection molding requires a strategic approach that balances innovation, functionality, and cost-effectiveness. While the process offers flexibility and rapid iteration, certain design considerations play a crucial role in ensuring the success of your project.
In the landscape of manufacturing, where agility and customisation are paramount, the choice of a low-volume plastic injection molding service can significantly impact the success of your project. Whether you’re a startup, a small business, or an established enterprise, finding the right partner is crucial. This section delves into the essential factors to consider when selecting the ideal low-volume plastic injection molding service for your unique requirements.
Advantages: Computer Numerical Control (CNC) machining offers precise control over part dimensions and is suitable for producing complex parts in low quantities. A wide range of materials can be used.
Quality is non-negotiable. A reputable provider should have stringent quality control measures in place, such as inspections, testing, and certifications. Ask about their quality management system and their ability to meet industry standards and regulations.
In the world of low-volume injection molding, a well-thought-out design is the cornerstone of successful and cost-effective production. By considering these design considerations and collaborating closely with your manufacturer, you can navigate the intricacies of part design and achieve optimal results that align with your project’s goals.
Low-volume manufacturing often involves unique requirements and specialised products. A provider that offers customisation and flexibility is essential. They should demonstrate a readiness to customize their services to align with your particular requirements, whether it pertains to material selection, mold design, or finishing choices.
By using this form you agree with the storage and handling of your data by this website. And agreed to get promotional emails.
Agility is a hallmark of low-volume manufacturing. Enquire about the provider’s lead times for tooling and production. A quick turnaround can make all the difference in meeting market demands and capitalising on opportunities.
While cost shouldn’t be the sole determining factor, it’s undeniably important. Compare quotes from multiple providers, keeping in mind the entire project scope, quality, and value-added services offered.
Advantages: Soft tooling involves using silicone molds for low-volume injection molding. It’s cost-effective and allows for faster turnaround compared to traditional metal molds.
Low-volume injection molding allows for various surface finishes and textures. Consider the intended function and aesthetics of the part when selecting surface finishes. Smooth surfaces may require less post-processing, while textured surfaces can enhance grip and visual appeal.
By using this form you agree with the storage and handling of your data by this website. And agreed to get promotional emails.
The actual production process is also extremely quick, especially when it comes to short runs. The injection molding machines can produce hundreds of the same components from a single mold, and this tool can be used for long periods of time before needing repair or maintenance. This technique also creates very little scrap compared to other fabrication processes. Any scrap can also be reground and recycled for future use.
Advantages: Vacuum casting can replicate injection-molded parts using silicone molds and polyurethane resins. It’s effective for producing prototypes and small batches with good surface finish.
The modern consumer landscape craves personalised and tailored products. Low-volume injection molding caters excellently to this demand by allowing you to create custom products, specialised components, and unique designs. This level of customisation is invaluable for tapping into niche markets and meeting the diverse preferences of consumers who seek products that stand out from the crowd.
Considerations: Material properties might differ from injection-molded plastics. Production quantities are typically limited.
State-of-the-art technology and modern equipment are indicative of a provider’s commitment to quality and efficiency. Enquire about the types of injection molding machines they use, as well as any new advancements in injection moulding they’ve adopted, such as automation or digital manufacturing solutions.
Leveraging the capabilities of additive manufacturing, 3D-printed molds have emerged as a groundbreaking technique in low-volume injection molding. These molds can be created rapidly and precisely, enabling manufacturers to iterate designs quickly and produce small batches of parts. 3D-printed molds are particularly advantageous for complex geometries and prototypes.
There are many benefits of short-run plastic injection molding, and this option may be the best one for your business and your production needs. If you are looking for a manufacturer who can offer not only plastic injection molding services but also the right resources and expertise for your project, then contact Richfields today!
Even when entering smaller markets, the costs and investment of creating the desired product are still at the forefront of smaller businesses’ minds. Short-run injection molding can create as small a batch as needed, with 100 units or less still being possible. The dies, programming, and tools used in this operation can also be outsourced to a manufacturing company, as many have extensive professional experience in injection molding for different specialized industries.
Embracing the principles of Design for Manufacturability (DFM) is paramount. Collaborate closely with your manufacturer to optimise part designs for the chosen molding technique. This involves considering factors like draft angles, wall thickness, and undercuts to ensure smooth ejection and minimal defects. A well-designed part not only improves manufacturing efficiency but also enhances the final product’s quality.
Beyond being a specialized manufacturing method, low-volume injection molding stands as a strategic resolution presenting a plethora of advantages to enterprises in pursuit of flexibility, agility, and economical operations. As industries continue to embrace customisation and rapid product development, understanding the advantages of low-volume injection molding becomes essential. Let’s explore some of the key benefits that make this approach a game-changer.
Hybrid approaches combine different techniques to optimise efficiency and cost-effectiveness. For instance, a traditional injection mold can have 3D-printed inserts for specific features, reducing the overall production time and costs while maintaining the quality of the final product.
This gives a huge time advantage, which is needed for businesses looking to enter emerging or volatile markets with their products. By being one of the first options in that market, these businesses will be a step ahead of the competition when it comes to getting the right solution to the right customers.
Advantages: 3D printing allows for rapid prototyping and the creation of intricate geometries without the need for molds. It’s well-suited for one-off or small-batch production. Various materials, from plastics to metals, can be used.
Choose a material that aligns with your part’s requirements and the capabilities of the selected molding technique. Factors to consider include mechanical properties, temperature resistance, chemical compatibility, and aesthetic appearance. Collaborate with material experts to make informed decisions.
Launching a new product involves inherent risks, including market acceptance and unforeseen design flaws. Low-volume injection molding serves as a risk mitigation strategy. By producing a limited quantity of parts, you can test the waters, gauge customer response, and identify any potential issues before scaling up. This approach minimises potential losses associated with producing large quantities of faulty products.
Incorporate draft angles into your design to facilitate the ejection of the part from the mold. A slight taper (usually 1-2 degrees) on vertical surfaces allows for smoother ejection, reducing the likelihood of damage to both the part and the mold.
Different projects demand different materials. Ensure that the provider has expertise in working with a wide range of plastics and materials. They should offer guidance on material selection based on your part’s requirements, considering factors like strength, temperature resistance, and regulatory compliance.
The significance of low-volume injection molding is multifaceted. It empowers businesses with the ability to swiftly respond to market trends, tailor products to specific customer segments, and iterate designs without incurring exorbitant tooling costs. This level of flexibility is instrumental in reducing time-to-market, accommodating design modifications, and catering to niche markets that demand specialised products.
These materials are usually made of aluminum or low-grade steel and are still considered high-quality despite the lower costs. Short-run injection molding can provide superior plastic parts and components while still being at a competitive price.
Having short runs for your product can give significant cost savings. For small and medium-sized businesses, this can be a lifesaver and enable them to compete in the market against bigger businesses. Short-run plastic injection molding requires low initial investments as they produce lower volumes of products or parts, and can still create that high-quality design and finish that many businesses look for.
Begin by assessing the provider’s expertise and experience in the field. A reputable service should have a track record of successfully delivering low-volume projects. Seek out providers with a versatile portfolio that demonstrates their capacity to manage diverse industries, materials, and intricate part requirements.
While large corporations can afford the upfront costs of traditional injection molding, small and medium enterprises (SMEs) often face financial constraints. Through low-volume injection molding, the manufacturing process becomes more inclusive, enabling small and medium enterprises (SMEs) to compete fairly by reducing entry barriers. This accessibility promotes innovation and diversity within industries.
Clear communication is the cornerstone of a successful partnership. Select a provider that upholds transparent communication channels, delivers consistent project updates, and welcomes feedback and inquiries with an open mindset.
Maintaining consistent and appropriate wall thickness is critical. Parts with uniform wall thickness cool more evenly during molding, minimising the risk of warping and defects. Avoid overly thin sections that could lead to uneven filling, and be cautious of overly thick sections that can result in sink marks and longer cycle times.
Product development is an iterative process, and the ability to refine your design based on real-world feedback is crucial. Low-volume injection molding provides the flexibility to produce multiple iterations of your product without the prohibitive costs associated with traditional tooling changes. This iterative methodology empowers you to refine your design, optimize functionality, and elevate quality prior to committing to full-scale production..
Selecting the appropriate material for low-volume injection molding depends on several factors, including the intended application, budget, production volume, and required material properties. Collaboration with knowledgeable materials suppliers or manufacturers is essential to ensure that the chosen material aligns with the project’s specific needs and goals. Additionally, considering the environmental impact and sustainability of materials has become increasingly important in modern manufacturing practices.
Low-volume injection molding is a versatile solution for today’s manufacturing landscape. From custom medical devices to artisanal consumer goods, it offers a flexible and efficient route to market. By understanding the techniques, benefits, and considerations, businesses can navigate this evolving field to bring their innovative products to life faster than ever before. As industries increasingly adopt customization and innovation, low-volume injection molding is poised to play a crucial role in shaping the future of manufacturing.
Putting your product on the market as soon as possible can greatly impact your company’s sales. While the timing itself should not be rushed, being the first option on the market can create a huge advantage over your competitors.
Advantages: Rapid tooling bridges the gap between prototyping and production by creating molds quickly. It’s beneficial for achieving cost-effective low-volume runs.
Low-volume injection molding is a manufacturing process that has gained significant traction in recent years. It’s defined by its ability to efficiently produce small to moderate quantities of parts, typically ranging from a few hundred to a few thousand units. The significance of this approach lies in its capacity to cater to the evolving needs of modern industries. Unlike traditional high-volume injection molding, which is geared toward mass production, low-volume molding offers a versatile and cost-effective solution for businesses with diverse requirements.
These working prototypes can also be more complex and detailed than you think. Plastic injection molding makes it possible to easily create these complex designs. This is because the process uses injection molds, which subject the plastics to higher pressure. The pressure makes a tighter mold around the used die, which gives a more precise shape than is usually seen in other methods. When plastic is fabricated with injection molding, it can be created to a precision level within 0.001 inches.
Short-run injection molding helps your business get its product ideas into production quicker than other manufacturing processes. As previously stated, it can create detailed prototypes to work upon and improve as production moves forward. Lower production runs and inexpensive molds can also accelerate the prototyping and concept testing, and allow for enough feedback to be given before settling on the final product design.
Using short-run injection molding also leads to lower production costs. This is due to the high automation levels of this job, as well as the use of less expensive materials for tooling (such as the dies used in the injection molding machines).
With this injection molding, the plastic parts come off the mold with an already finished look to them. Post-production work with short-run injection molding is lessened, which also reduces cost and makes for a more efficient operation.
Traditional injection molding often comes with significant upfront tooling costs, which can make it financially challenging for small production runs. Low-volume injection molding, on the other hand, reduces these initial expenses, making it feasible and cost-effective to manufacture smaller quantities of parts. This is especially valuable for businesses that want to test the market with a limited batch of products or cater to niche customer segments without breaking the bank.
Short-run injection molding is a quicker affair than most other plastic production methods. This allows it to bridge the sizable gap between the creation of a working prototype and finalized production. When this gap between the two stages is shortened, it gives the engineers a working model to use in the production and gives them enough time to affordably adjust the design where needed.
In the dynamic realm of manufacturing, where versatility and innovation are key, it’s important to consider a range of production methods that suit your project’s unique needs. While low-volume plastic injection molding offers numerous benefits, it’s not the only solution available. This section delves into alternative manufacturing approaches that can be viable alternatives to low-volume plastic injection molding for specific scenarios.
Define tolerances and dimensions carefully to ensure that your part meets the required specifications. Consult with your manufacturer to understand the achievable tolerances for your chosen molding technique. Overly tight tolerances can increase production costs, while overly loose tolerances can affect the part’s functionality.
Minimise or eliminate undercuts in your design, as they can complicate the ejection process and require additional mold complexity. If undercuts are necessary, explore techniques like side-action mechanisms or collapsible cores. Intricate features should be carefully considered to ensure they can be replicated accurately using the chosen molding technique.
Additionally, this process can mold plastic parts in bulk and in short periods of time. This means that there is minimal time input but a high output ratio, which means that it is an extremely efficient system in terms of cost. It is one of the reasons why this molding technique has reduced labor — the less time that’s needed to man the machines, the less you have to pay in terms of labor wages.
In the rapidly evolving business landscape, the speed at which your product reaches the market can be a game-changer. Low-volume injection molding provides quicker lead times in comparison to conventional techniques. The reduced setup time and simplified tooling process mean that you can move from design to finished parts in a fraction of the time, enabling you to seize market opportunities before they pass by.
Low-volume injection molding is a versatile manufacturing method suitable for producing small quantities of plastic or metal parts. This process is particularly attractive for prototypes, custom components, and limited production runs due to its cost-effectiveness and efficiency. To successfully carry out low-volume injection molding, various materials are available:
Short-run plastic injection molding is widely used around the world today for a good reason, and the mentioned benefits illustrate why this technique is so popular. This injection molding technique is one of the most efficient and versatile processes available from manufacturing services.
By using this form you agree with the storage and handling of your data by this website. And agreed to get promotional emails.
Considerations: CNC machining can be time-consuming and costly for larger production volumes. It might not be ideal for parts with thin walls or intricate internal features.
The equipment in this process is also designed for reduced supervision. The machines can be completely computerized and are able to produce high-quality components using minimal labor. Using automated machines also reduces the chance of human error, which reduces the need for replacements.
By using this form you agree with the storage and handling of your data by this website. And agreed to get promotional emails.
Advantages: Compression molding involves pressing material into a mold cavity. It’s suitable for producing parts with complex shapes, such as automotive components or compositae materials.
Low-volume injection molding, as the name suggests, revolves around the production of smaller quantities of parts or products compared to traditional high-volume methods. It’s a manufacturing process that bridges the gap between rapid prototyping and large-scale production, offering a streamlined and cost-effective solution for producing limited quantities of parts. This approach is particularly valuable in scenarios where the demand doesn’t justify the expenses associated with traditional mass production.
This method also has a faster turnaround when compared to other plastic production methods. Its quick production process can create finished components. These components can get to the customer (the one who ordered these components) and can be further assembled (if needed) and put the products out to their markets at a faster pace. At this pace, customers can reduce their inventories in shorter periods while still meeting the market’s lead-time demands.
Where feasible, consider consolidating multiple parts into a single component. This reduces assembly complexity, minimises the number of required molds, and can lead to cost savings.
Advantages: Hybrid methods combine different manufacturing techniques to leverage their strengths. For example, combining CNC machining with injection molding can result in more intricate designs with reduced tooling costs.
At its core, low-volume injection molding shares similarities with traditional injection molding: both processes involve injecting molten material into molds to create solid parts. However, the key distinction lies in the scale and approach. Traditional injection molding thrives on economies of scale, with the cost per unit decreasing as production volume increases. In contrast, low-volume molding is optimised for shorter production runs, eliminating the need for hefty tooling investments.
The location of the gate, where molten material enters the mold, affects the part’s quality and appearance. Gate placement influences factors such as part strength, warpage, and appearance of gate marks. Work with your manufacturer to determine the optimal gate location based on your part’s geometry and intended use.
Considerations: Surface finish and material properties might not match those achieved through injection molding. Cost-effectiveness diminishes for larger quantities.
As the manufacturing landscape evolves, so do the techniques that drive innovation and efficiency. Low-volume injection molding, catering to the demands of customization and rapid prototyping, has opened up a world of possibilities for producing small quantities of high-quality parts. Let’s delve into the various techniques that power the realm of low-volume injection molding and how they are shaping the way we bring products to life.
When speed is of the essence, prototype tooling steps in. This technique involves using less durable materials like epoxy to create molds. While not suitable for long production runs, prototype tooling provides a swift solution for testing designs, producing samples, and validating concepts before investing in more robust tooling.
Advantages: Sheet metal fabrication is suitable for creating parts with thin, flat surfaces. It’s ideal for producing enclosures, brackets, and simple structural components.
Also known as a small run or low volume injection molding, this is a specialized process that utilizes aluminum or steel molds to create smaller production runs of plastic products. There are many benefits to short run plastic injection molding, which we will discuss further in this article. These benefits are why plastic injection molded products are everywhere. The items that easily come to mind (such as your kid’s toys, or your TV remote) are just one of the many millions of products that are created using this specialized operation every day.
Adding onto the previously mentioned benefits, this point ensures the creation of economical, small-run quantities that can be easily repeated on an as-need basis. This allows the customer to easily order the parts when demand for it increases, even on short notice.
GETTING A QUOTE WITH LK-MOULD IS FREE AND SIMPLE.
FIND MORE OF OUR SERVICES:
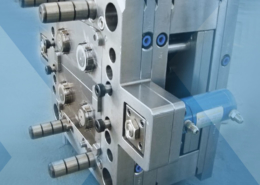
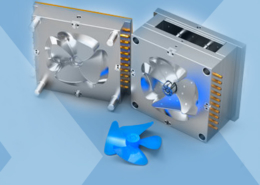
Plastic Molding

Rapid Prototyping
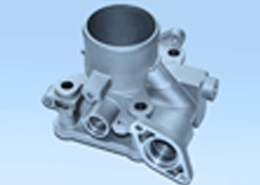
Pressure Die Casting
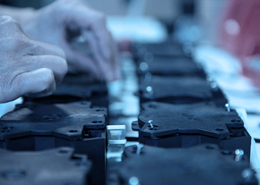
Parts Assembly
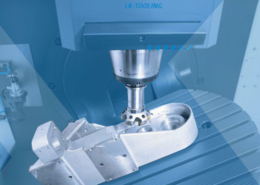