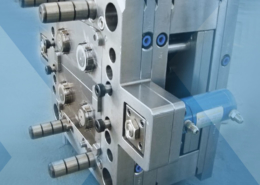
Exploring Custom Soft Plastic Molds: Revolutionizing Manufacturing
Author:gly Date: 2024-06-08
Custom soft plastic molds have emerged as indispensable tools in modern manufacturing processes, revolutionizing the production of various plastic components. As technology continues to advance, the demand for precision, efficiency, and customization in manufacturing has never been greater. In this article, we delve into the world of custom soft plastic molds, exploring their significance, applications, design considerations, and future prospects.
Understanding Custom Soft Plastic Molds
Custom soft plastic molds are specialized tools used in the injection molding process to produce flexible plastic components tailored to specific requirements. Unlike traditional molds, which are typically made of steel or aluminum, soft plastic molds are constructed from materials such as silicone or urethane. This flexibility in material allows for the creation of intricate designs and complex geometries that would be challenging or impossible to achieve with conventional molds.
Applications in Various Industries
The versatility of custom soft plastic molds enables their widespread use across a diverse range of industries. From automotive and aerospace to consumer electronics and medical devices, these molds play a crucial role in the production of components such as gaskets, seals, covers, and prototypes. Their ability to accommodate varying degrees of hardness, texture, and color makes them ideal for applications where flexibility and customization are paramount.
Design Considerations
Designing custom soft plastic molds requires careful consideration of several factors to ensure optimal performance and longevity. Parameters such as material selection, mold geometry, cooling systems, and injection parameters must be meticulously optimized to achieve desired outcomes. Additionally, factors like shrinkage, warping, and part ejection mechanisms must be addressed to mitigate potential defects and ensure consistent quality.
Material Selection
Choosing the appropriate material for custom soft plastic molds is critical to their performance and durability. Silicone and urethane offer excellent flexibility and moldability, allowing for intricate designs and complex part geometries. Factors such as temperature resistance, chemical compatibility, and wear resistance must be taken into account when selecting the most suitable material for specific applications.
Mold Geometry and Cooling Systems
Optimizing mold geometry and implementing efficient cooling systems are essential for achieving uniform part quality and minimizing cycle times. Complex part geometries may require intricate mold designs and advanced cooling channels to ensure proper material flow and uniform cooling throughout the mold cavity. Computational fluid dynamics (CFD) simulations can aid in the design process by predicting flow patterns and optimizing cooling strategies.
Injection Parameters and Process Control
Fine-tuning injection parameters such as temperature, pressure, and injection speed is crucial for achieving precise molding outcomes. Process control technologies, such as closed-loop feedback systems and real-time monitoring, enable manufacturers to maintain tight tolerances and detect deviations from optimal conditions promptly. By continuously monitoring and adjusting process parameters, manufacturers can ensure consistent part quality and minimize production variability.
Future Perspectives and Challenges
Looking ahead, the field of custom soft plastic molds is poised for continued growth and innovation. Advancements in materials science, additive manufacturing, and automation are expected to drive further improvements in mold design, performance, and efficiency. However, challenges such as material compatibility, surface finish, and scalability remain areas of ongoing research and development. Addressing these challenges will be crucial for unlocking the full potential of custom soft plastic molds in the years to come.
In conclusion, custom soft plastic molds represent a paradigm shift in modern manufacturing, offering unparalleled flexibility, customization, and efficiency. By understanding their applications, design considerations, and future prospects, manufacturers can harness the full capabilities of these innovative tools to stay competitive in today's dynamic market landscape.
GETTING A QUOTE WITH LK-MOULD IS FREE AND SIMPLE.
FIND MORE OF OUR SERVICES:
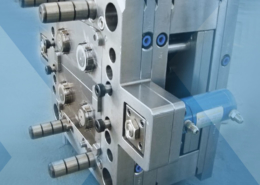
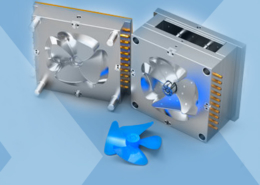
Plastic Molding

Rapid Prototyping
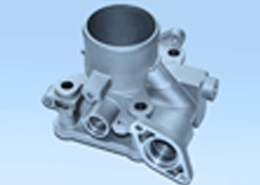
Pressure Die Casting
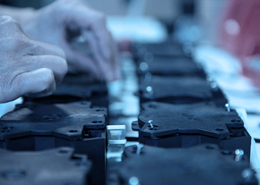
Parts Assembly
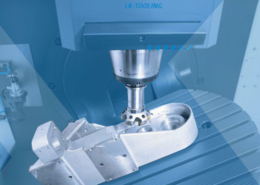