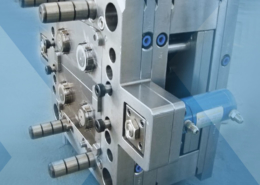
The Cost Dynamics of Custom Plastic Molding: An In-Depth Analysis
Author:gly Date: 2024-06-08
Plastic molding is a cornerstone of modern manufacturing, offering unparalleled versatility and cost-effectiveness in producing a wide array of products. However, understanding the intricacies of custom plastic molding costs is crucial for businesses aiming to optimize their manufacturing processes and budgets. In this comprehensive analysis, we delve into the multifaceted aspects of custom plastic molding costs, shedding light on its significance, factors influencing it, and strategies for cost optimization.
Understanding Custom Plastic Molding Costs
Custom plastic molding involves the creation of unique plastic components tailored to specific requirements, ranging from intricate shapes to precise dimensions. The cost of such processes encompasses various elements, including material expenses, labor costs, tooling expenditures, and overhead expenses. Moreover, factors such as design complexity, production volume, and quality standards significantly influence the overall cost dynamics.
Material Costs
The choice of raw materials plays a pivotal role in determining the cost of custom plastic molding. Different polymers exhibit varying properties, each suited to specific applications. Factors such as material availability, market demand, and desired characteristics impact material costs. Additionally, considerations such as material waste, recycling capabilities, and sustainability initiatives contribute to the overall material expenditure.
Labor Expenses
Labor constitutes a significant portion of custom plastic molding costs, encompassing wages, benefits, and training expenses. Skilled labor is essential for operating molding machines, conducting quality checks, and troubleshooting production issues. Moreover, labor efficiency, productivity improvements, and workforce management strategies influence labor expenditures and overall operational costs.
Tooling Expenditures
Tooling costs are critical in custom plastic molding, as molds and dies are essential for shaping plastic components. The complexity of the desired design, precision requirements, and tooling materials impact tooling expenses. Furthermore, factors such as tool maintenance, lifespan, and amortization affect long-term cost considerations.
Overhead Costs
Overhead expenses encompass various indirect costs associated with custom plastic molding operations, including facility rent, utilities, insurance, and administrative overheads. These costs are essential for sustaining manufacturing operations but can significantly impact overall cost structures. Strategies such as lean manufacturing, energy efficiency initiatives, and overhead cost optimization can mitigate the impact of overhead expenses on overall costs.
Factors Influencing Custom Plastic Molding Costs
Several factors influence custom plastic molding costs, shaping the cost dynamics and profitability of manufacturing operations. Understanding these factors is essential for businesses to make informed decisions and optimize their cost structures effectively.
Design Complexity
The complexity of the desired product design significantly impacts custom plastic molding costs. Intricate shapes, undercuts, and tight tolerances require specialized tooling and increased production time, leading to higher costs. Collaborative design efforts, design optimization techniques, and prototyping can mitigate cost escalations associated with design complexity.
Production Volume
Production volume plays a crucial role in determining custom plastic molding costs, as economies of scale influence per-unit costs. High-volume production often leads to cost reductions due to optimized manufacturing processes, while low-volume production may incur higher costs per unit. Forecasting demand, capacity planning, and production scheduling are essential for balancing cost considerations with production volumes effectively.
Quality Standards
Maintaining stringent quality standards is vital in custom plastic molding, as product defects and deviations can escalate costs through rework, scrap, and customer dissatisfaction. Investing in quality assurance measures, process controls, and continuous improvement initiatives is essential for achieving optimal quality while managing costs effectively.
Market Dynamics
Market dynamics, including competition, customer preferences, and industry trends, influence custom plastic molding costs. Price fluctuations in raw materials, labor market conditions, and technological advancements can impact cost structures unpredictably. Businesses must stay vigilant to market changes and adopt agile strategies to adapt to evolving cost dynamics effectively.
Strategies for Cost Optimization
Optimizing custom plastic molding costs requires a holistic approach that addresses various cost drivers and leverages strategic initiatives to enhance efficiency and competitiveness.
Design Optimization
Collaborative design efforts focusing on simplifying designs, reducing material usage, and minimizing production complexities can yield significant cost savings in custom plastic molding. Employing design for manufacturability (DFM) principles, conducting design reviews, and leveraging advanced simulation tools enable proactive cost optimization at the design stage.
Process Efficiency
Streamlining manufacturing processes, optimizing machine utilization, and implementing lean manufacturing principles are instrumental in reducing custom plastic molding costs. Continuous process improvement, waste reduction initiatives, and automation technologies enhance operational efficiency and mitigate cost escalations.
Supply Chain Management
Efficient supply chain management practices, including vendor collaboration, inventory optimization, and strategic sourcing, contribute to cost reduction in custom plastic molding. Building resilient supply chains, mitigating supply chain risks, and exploring alternative sourcing options enhance cost competitiveness and ensure continuity of operations.
Technology Adoption
Embracing technological advancements such as 3D printing, digital simulation, and IoT-enabled monitoring systems can revolutionize custom plastic molding processes and drive cost efficiencies. Investing in innovative technologies, upgrading equipment, and adopting Industry 4.0 practices enable businesses to stay ahead of the curve and optimize cost structures effectively.
Conclusion
In conclusion, custom plastic molding costs are influenced by various factors ranging from material expenses and labor costs to tooling expenditures and overhead expenses. Understanding the cost dynamics and implementing strategic initiatives for cost optimization are essential for businesses to enhance competitiveness and achieve sustainable growth in today's dynamic manufacturing landscape. By leveraging design optimization, process efficiency, supply chain management, and technology adoption, businesses can effectively navigate cost challenges and capitalize on opportunities for innovation and growth in custom plastic molding operations.
GETTING A QUOTE WITH LK-MOULD IS FREE AND SIMPLE.
FIND MORE OF OUR SERVICES:
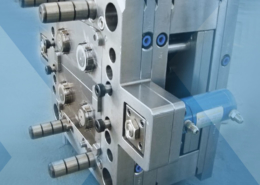
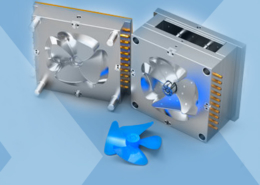
Plastic Molding

Rapid Prototyping
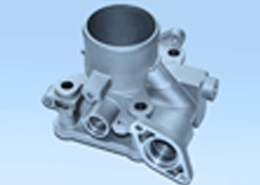
Pressure Die Casting
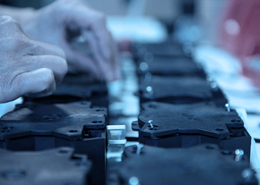
Parts Assembly
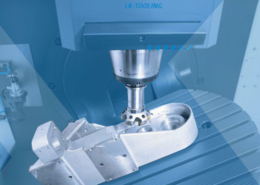