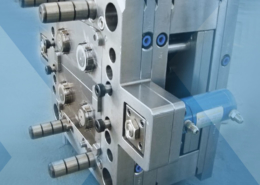
Three Reasons For Choosing Small-batch Injection Molding - small batch injection
Author:gly Date: 2024-10-15
3.1.2 If the surface of the cavity has oil and water stains, or the mold release agent makes too much, it will make the surface of the plastic part dark and lusterless. In this regard, we should remove the oil and water stains in time, and use the mold release agent in a limited amount for custom ABS plastic injection molding . .
In the picture below, the area of 1.5mm is the area where the nameplate is placed. Increase the wall thickness here by 0.3mm to improve the stagnation in this area, thus eliminating the welding line and the air trapping here.
The kind of plastic you choose for your prototype influences its price and use. Selecting the plastic that best meets your demands is crucial since different plastics have different prices and features.
Understanding the prototype’s function is the first step in plastic rapid prototyping. Consider the issue you’re attempting to address by asking yourself possible questions.
ABS is a general-purpose thermoplastic engineering plastic developed in the 1940s for plastic injection molding process. It is a plastic with excellent overall mechanical properties, good rigidity, hardness and processability, and high toughness, and it can be injection molded, extruded or thermoformed.
4.1.9 The ejecting force of custom ABS injection molding ejector mechanism should not be too large, otherwise the surface of the plastic part will easily have whitening.
The success of your plastic prototype depends critically on the material you choose. Think about the traits and qualities you want to duplicate or test. The material selected will impact strength, adaptability, aesthetics, and temperature resistance.
“PTS always can quickly find a solution for any complex Manufacturing situation. With their capacity, quality, and knowledge, PTS can help any company achieve its goals.”
In the original design, the deformation is 3.8mm, and after optimization, the deformation is 1.8mm, and the improvement of deformation is about 55%.
4.1.1 The moisture absorption of ABS is relatively strong, and the high moisture content of the raw material will lead to the poor gloss of the plastic parts and the poor quality of the internal molecular structure, so the ABS injection molding factory should dry the raw material to make sure the moisture content is not more than 0.3% before custom ABS plastic injection molding .
Generally, you start with a 3D or computer-aided design (CAD) model to make a plastic prototype. The actual prototype’s physical design is based on this digital illustration.
Plastic prototyping provides a variety of applications and benefits that may significantly speed up your product development process. Rapid prototyping techniques for plastic may help you save time and money while retaining the accuracy and viability of your ideas.
3.1.3 If the product draft angle is too small, it is difficult to demolded, or the demolded force is too large when eject the parts out, so that the surface of the plastic parts is not shiny, in this regard, we should increase product draft angle during DFM stage.
3.1.5 If the gate or runner cross-sectional area is too small or suddenly changed during melting flow , the melt flowing in which the shear force is too large, is turbulent dynamic flow, resulting in poor luster, in this regard, should be appropriate to increase the gate and runner cross-sectional area for custom ABS plastic injection molding ..
CNC machining (“computer numerical control”) is a subtractive manufacturing method employing CNC machines to form plastic prototypes accurately.
For limited production runs or complicated geometries, 3D printing and CNC machining may be more cost-effective than injection molding owing to lower tooling costs.
This article will examine four common methods for manufacturing plastic prototypes: vacuum casting, 3D printing, CNC machining, and injection molding. You will explore their advantages and uses to decide which method suits your prototyping requirements.
ABS combines a graft copolymer containing butadiene and an acrylonitrile-styrene copolymer. Acrylonitrile accounts for 15%-35%, butadiene for 5%-30%, and styrene for 40%-60%, with a most common ratio of A: B: S = 20: 30: 50.
Selecting the most efficient way to implement your concept is ensured by evaluating the intended shape of your prototype.
ABS injection molding services is used to make interior and exterior assemblies parts, radiator grilles, lamp covers, instrument panels and control panels, etc.
Kemal Plastic Injection Molding Services can help you with anything from idea development to creating high-quality plastic prototypes owing to their experience in prototyping technology.
For example, 3D printing could be effective if your design asks for a straightforward geometric form. However, methods like CNC machining or injection molding may be more suitable if you are working on detailed and complicated designs.
Kemal Plastic Injection Molding Services can be a trustworthy collaborator in all phases of the plastic prototype process.
Even if you have a fantastic concept in your head, it might take much work to convey it to others appropriately. You can fill the gap by giving a practical example of your idea in a plastic prototype.
It’s essential to remember that plastic prototyping is more than simply making a physical version of your product; it’s also a tactical tool that enables you to iterate, improve, and verify your ideas before going into mass production.
3.2.1 If the injection speed is too small, the surface of the plastic part will not be dense and show poor appearance during custom ABS plastic injection molding .
PTS is custom injection molding company On-demand from prototype to production, leader in injection molding, rapid prototyping,helping you bring your concepts to market faster, Our company export injection molding parts to more than 60 countries, including but not limited to The United States, Australian and Canada and so on.
Plastic prototypes may be made using the flexible and economical vacuum casting technique. It includes creating a silicone cast using a master pattern, often created via CNC machining or 3D printing.
There are many varieties of ABS resins, and the barrel temperature varies from one variety to another, 180-230°C for general ABS, 190-240°C for heat resistant ABS, 170-220°C for flame retardant ABS.
The following picture shows the deformation caused by different reasons, and the deformation trend shows that the uneven shrinkage is the main cause of product deformation.
What level of detail should you include in your proof-of-concept model? Do you want to make a precise replica of the finished product? Choosing the best prototype approaches and procedures would be easier if you knew the complexity level.
Most injection molding suppliers do not pay attention to this point, we have professional mold flow analysis engineers to analysis the gate and runner dimensional for you plastic injection molding project.
ABS Injection Molding has become a larger plastic variety at present and wide range applications, such as:Electronic appliances, household appliances,home appliances, office equipment,instruments,machinery, automobiles and other industrial equipment accessories.
3.2.4 If the melt temperature is too low, which makes the liquidity poor and leads to bad appearance, the melt temperature should be increased appropriately during custom ABS plastic injection molding .
The plastic injection molding manufacturer should not add overmuch recycled materials or sprue materials into the raw plastic materials, Remember, the plastic injection molding factory should put quality in the first place.
Set the analysis sequence as “Cooling+Filling+Pressure+Warpage”, select the analysis material as “Polylac PA-757 ABS”, the cooling inlet temperature as 25˚C.
4.1.10 Although the molding shrinkage of ABS is small, but it is easy to have internal stress after injection molding, so the plastic parts generally need to be heat treatment, Usually we put the products in a 70 degree room for 2-4 hours.
Using prototypes, you may evaluate several design options, streamline production, and eliminate waste. Purchasing a plastic prototype in advance might save costs and improve product quality.
Several procedures are available for producing plastic prototypes, each with a unique set of benefits and factors to consider. This article will examine four standard processes.
You may choose the best material by identifying the qualities of the material that match the needs of your project. This guarantees that your prototype resembles the finished product, allowing you to perform reliable and accurate evaluations.
4.1.6 The viscosity of ABS material is medium, better than PC, PVC, but worse than PS, it is better to use straight-through nozzle for mass production.
There are a few essential factors to consider while working on a plastic quick prototyping project to guarantee an excellent outcome. By carefully weighing these aspects, you may decide how to optimize the prototype process best to match your unique demands.
The intended smoothness or texture of your prototype’s surface finish might impact the price. The cost of total post-processing operations such as polishing, painting, or coating will also increase.
From the above, it can be found that at the early stage of product design, it is difficult to predict the possible problems in product production through experience. With the assistance of Moldflow software, it can help designers to predict risks and find problems in a timely manner, so that problems can be avoided in advance by optimizing the product in order to prevent problems from appearing in the production stage and then come back to solve them. The resulting development cycle is shortened and efficiency is improved.
It allows you to demonstrate your product’s size, shape, and general look, making it easier for stakeholders and prospective buyers to understand your idea. Observing your concept come to life can enable you to get user input and make the required adjustments.
ABS is an amorphous plastic with no clear melting point, and the melt flow temperature is not too high, above 160°C, which is sufficient fluidity, but the high temperature does not increase the fluidity.
To improve the deformation, it is necessary to know what causes the deformation of the injection molded product. For injection molded products, there are several main reasons of deformation as follows:
Injection molding is often used to manufacture plastic components. High production efficiency and consistent quality are offered, but only after a significant investment in tooling.
4.1.4 ABS has good molding performance, and there is no special requirement for injection molding machine, and general screw type and plunger type injection molding machine can be used.
As a professional ABS injection molding manufacturer, we make the following details on this topic. Please correct us if we are wrong; we will learn together!
The injection molding temperature of ABS plastic is 180-250°C, but ABS injection molding factory need to pay special attention to the fact that it is better not to exceed 240°C, otherwise the resin will be decomposed.
After the design change, the welding line was also improved, and although there are still two short welding lines, they are within the acceptable range for the customer.
Problem points such as the above were identified through Moldflow software prediction, and the problems could be eliminated by modifying the product design before actual production, thus ensuring the quality of the design.
Because of its high strength, corrosion resistance, and temperature resistance, it is often used to manufacture plastic housings for instruments.
3D printing is perfect for making a few prototypes at a minimal cost. If you require more prototypes, injection molding or vacuum casting may be cheaper. Prototyping is efficient and cost-effective when volume and budget are balanced.
4.1.2 ABS melt has obvious non-Newtonian, increasing the injection pressure can make the melting viscosity decrease significantly
3.1.1 If the mold cavity manufactuirng is poor, such as scars, microporous, wear, roughness and other deficiencies, will inevitably react to the plastic parts, so that the plastic parts appearance is not good, for this, to carefully build the mold, make sure the surface of the cavity has a small roughness, if necessary, polishing chrome plating for custom ABS plastic injection molding .
4.1.5 When using screw type injection molding machine, in order to improve the quality, dimensional stability, surface gloss and eliminate residual internal stress, The injection volume should be limited to 50% of the maximum volume of injection molding machine, all injection molders needs to confirm the density of the raw material and the weight of sprue & product when calculating the volume.
3.3.4 The dispersion of additives is too slow to lead to poor appearance on plastic parts, in this regard, should be replaced the additives with better flowability before custom ABS injection molding.
Before mass production, creating a plastic prototype can save you time, effort, and money. Early detection and correction of design flaws may result in cost savings and decreased product failure.
After the design change, the difference of wall thickness between the nameplate area and the surrounding area became smaller, and the problem of trapped air was improved.
What exactly is it that you need to verify or test? Your prototype’s quality and complexity needs will be determined by the objectives that you set for it.
The number of prototypes you want and the resulting cost implications are other crucial factor in plastic prototyping. Consider your prototype needs for testing, confirmation, and market evaluation. This helps you determine the most cost-effective production processes for your volume.
3.3.2 Too much recycled material or sprue material is added to the raw material, which affects the uniform melting and makes the appearance bad, so the ratio of adding recycled material or sprue material should be reduced before custom ABS injection molding .
If the flow resistance is high when filling the mold,a higher injection pressure shoule be used; conversely,a lower injection pressure should be used,Usually wholesale doesn’t know it, Our company is very familiar with ABS plastic injection molding.
You may give your ideas life and evaluate their functioning, design, and compatibility with the help of plastic prototyping. It lets you test your plastic product concept and assess its viability, usefulness, and innovation.
3.3.3 The content of moisture or volatile matter in raw plastic materials is too high, and evaporates into gas when heated, and condenses in the mold cavity, resulting in poor appearance on plastic parts, so the raw plastic materials should be pre-drying treatment a few hours before ABS injection molding.
Checking the filling time results, in the area where the product is labeled with the nameplate, the air trapping is generated because the wall thickness is thinner than the surrounding thickness.
By looking at the “volume shrinkage at ejection” graph below, we can see that the uneven shrinkage is mainly caused by the shrinkage of the main product and the shrinkage of the ribs on the core side of the mold.
Typical choices include nylon, polypropylene, ABS, and polycarbonate. Due to causes like performance, performance criteria, or availability, certain materials may be more costly than others.
You can transform the digital design into a physical plastic product using several prototype methods, including CNC machining, 3D printing, or injection molding.
As shown below, the maximum wall thick of the product is 2.5mm(fair wall thick), the rib thickness is jsut 1.0mm, and the rib height reaches 40mm.
3.3.5 There are foreign materials, miscellaneous materials or insoluble materials mixed in the raw material, they can’t be mixed with the raw material evenly and lead to bad appearance, in this regard, these miscellaneous materials should be strictly excluded beforehand.
3.3.6 If the amount of lubricant is too little, the fluidity of the melt is poor, and the surface of the plastic part is not dense, which makes the luster bad, for this, the amount of lubricant should be increased appropriately before custom ABS injection molding .
4.1.3 ABS has a small molding shrinkage, with a range of 0.3% to 0.8%, so it can be designed for high accuracy of the injection molded part.
Utilize Kemal Plastic Injection Molding’s experience and the versatility of plastic prototyping to quickly and effectively bring your ideas to life.
Your prototype’s design complexity significantly influences the cost. More time and resources are needed to create sophisticated designs with intricate elements, which might raise the final price.
ABS injection molding services is used to make instrument panels, instrument cases, cameras, clocks, musical instruments, bracket,pellet,cabinet etc.
The injection mold temperature should be controlled within the allowable range during the molding process, generally at 50-70°C, The injection mold temperature has a great impact on the quality of the parts.
● Product Name: Printer Enclosure ● Product Color: White ● Product Size: 520mm*200mm*10mm ● Wall Thickness: 1.5-2.0mm ● Product Material: Polylac PA-757 Grade ABS ● Product appearance Requirements: No welding line, No any appearance defects
While computer simulations and schematics are helpful, they only explain how your product will work in actual situations.
Our cutting-edge manufacturing skills and knowledgeable staff guarantee that your prototypes are manufactured precisely and quickly, saving you time and money.
ABS injection molding services is used to make drainage and exhaust ducts, pipe fittings, window and door frames, shutters and safety caps, etc.
For the problem points identified in the preliminary analysis, there are different improvement countermeasures for different problem points.
“In manufacturing, reliability is everything. That’s what we get from PTS industrial Ltd and they have also reduced our rejects by up to 90%. If all our equipment worked as well…our jobs would be easier, and our customers would be very happy”
Although short turnaround times may be achieved using rapid prototyping methods, the intricacy of your design and the chosen manufacturing process might affect the lead time.
Worry about our quality? See what our happy customers said about our products/services. You will LIKE us once you started with us!
●Housing and other parts for TVs ●Recorders ●Washing machines ●Refrigerators ●Telephones ●Computers ●Vacuum cleaners ●Electric fans and ●Air conditioners, ●And many more
8.2 days for TESLA prototype injection molding at 11/2021,other factories need 13 days. 14.6 days for FORD medium volume injeciton molding production at 05/2022, other factories need 25days.
Contact Kemal Plastic Injection Molding Services for a detailed pricing estimate on your plastic prototype. Based on your precise needs, required quantities, and preferred materials, we will provide comprehensive cost estimation for your plastic prototypes.
PTS Manufactures And Supplies OEM ODM Plastic Injection Molding From An Industry Leader With The Expertise Experience And Resources To Handle Large-Scale,Complex Projects From Concept Through Manufacturing Via Our Digital Injection Molding.
Our ABS injection molding services cover all of these industries, We have made ABS injection molding products for the following finished products:
The injection pressure depends on the product structure and wall thickness. Generally, the injection pressure is 50-70MPa for general ABS, 60-85MPa for heat resistant ABS, 60-100MPa for flame retardant ABS.
3.2.3 If the holding pressure is not enough and the holding time is short, the density of the plastic part is not enough and the luster is not good, for this, the holding pressure and holding time should be increased during custom ABS plastic injection molding .
The cost of your prototype may increase if it has many parts or has to be put together. Prices may rise due to intricate assembly procedures.
See how we process your orders, from quotation to plastic injection molding, as our machines and efficient team ensure you receive your parts within the scheduled lead time and meet your requirements perfectly.
But The product quality will be better with screw type injection molding machine, our injection molding factory 100% use screw type injection molding machine for ABS injection molding.
While increasing the rib thickness, it is important to note that too much flesh thickness can cause shrinkage, and usually 0.6 times the thickness of the base surface at the root of the rib will not cause shrinkage.
The price may vary depending on your needed prototypes. Spreading out fixed expenses by producing many prototypes helps lower per-unit prices.
We follow international tolerance standards to ensure our parts meet your requirements, and We have the ability to deliver products anywhere in the world that you specify.
PTS Industrial Ltd is Specializing in precision manufacturing and injection molding parts since 2002. We supply CNC machining (milling&turning) parts and injection molding parts for various industries to customers worldwide.
Plastic prototyping is a technique that enables you to use plastic materials to build a prototype or actual model of your intended product. Before going on with mass manufacturing, it’s a valuable strategy for testing and verifying your idea.
As a professional Custom ABS plastic injection molding supplier, we will make the details DFM report to Analyze the customer’s design.
3.2.5 If the injection speed is too large and the gate cross-sectional area is too small, the vicinity of the pouring product will be dark and bad luster, in this regard, the injection speed can be properly reduced and the gate cross-sectional area increased during custom ABS plastic injection molding .
3.1.4 If the mold venting system is bad, too much gas stays in the model, which also leads to bad appearance, for this, check and correct the mold venting system system for custom ABS plastic injection molding ..
4.1.8 The sub-runner must be large enough to allow the melting to fill the mold cavity before the sub-runner solidified and is compacted in the mold cavity. The sub-runner diameter should generally be larger than 5mm, but not more than 10mm.
Knowing precisely what you want the prototype to do can help you concentrate your efforts and allocate your resources efficiently.
3. Deformation status Since the main concern of the product is the overall flatness, we mainly look at the deformation in the Z-direction. below picture shows the overall deformation in Z-direction, and the overall deformation value is about 3.8mm, which is larger.
That’s why it is so important to work with a professional injection molding factory, which can help you to develop and evaluate new products quickly, economically and with less risk.
After the trial ABS molding phase, we start ABS batch molding, which uses powerful machining to manufacture parts at fast rates to save on time and costs.
Our sales are transferred from project manager who speak good english and will never make you feel difficult to communicate with our injection molding factory, Professional in injection molding.
PTS is your China partner, your China researching and developing team, your easteel and south of China ABS Plastic Injection Molding manufacturer / Services.
Plastic prototypes are ideal for iterative and rapid prototyping. A physical prototype lets you swiftly apply feedback and testing findings. Iterative development cycles reduce time to market and setbacks.
“We started using engineering parts around 10 years ago from PTS. We have always received excellent parts from every batch, timely replies to all our queries, and very competitive quotes and make us more competitive in the market.”
Due to its quick manufacturing capabilities, 3D printing is often preferred when time is essential. However, the setup and tooling times for processes like CNC machining or injection molding might be longer.
There are two similar ribs at the core side of the mold. Although the other one is at the end of the flow and does not show stagnation in the analysis, the flesh thickness is also changed to 1.5 mm to avoid the risk in actual production.
At the early stage of product development, MoldFlow can be applied to analyze the manufacturing feasibility of the product. Through MoldFlow, the filling pressure, the location of the welding line and air trapping, short shot defects, the deformation, and many more points can be predicted before plastic injection molding.
How your plastic prototype is made might affect the price. Typical processes include CNC machining, 3D printing, and injection molding.
We have our own mold making factory,This will ensure the mold quality of all manufacturing processes. The mold property is yours.
This article allows you to assess and enhance your product’s design, usability, and aesthetics, giving you the trust you need to proceed with the mass production process.
A plastic prototype enables you to engage with your design physically while testing its functionality and assessing its usability. You can spot design issues by handling, using, and experimenting with the prototype.
The expense of your project may also be affected by its urgency. Due to the need for speedier manufacturing processes or prioritized resources, rush orders or expedited production may be subject to additional fees.
Every prototype project, including plastic rapid prototyping, depends on time. Consider the project’s timeline restrictions when evaluating the lead time needed to produce the prototypes.
The shrinkage of the base surface was about 2%, while the shrinkage of the rib was about 0.5%, so the difference between the shrinkage of the top and bottom was too large. Since the shrinkage of the base surface was large, so the product warped upward.
After thickness analysis, the air trapping of the ribs is mainly due to the hysteresis of the front melting. The melting will preferentially flow towards the place with less filling resistance during the filling process. And the melting with stagnant flow is rapidly cooled by the mold, thus risking to cause a short shot.
The main reasons for the bad appearance of plastic molded parts are mold, the injection molding process, and raw materials.
Removing the ribs to eliminates the difference in volume shrinkage, but the strength of the product also decreases, so the method of reducing the height of the ribs (as shown below) is used to reduce the unbalance of shrinkage to improve warpage.
3.2.2 For thick-walled plastic parts, if the cooling is not sufficient, the surface will be hairy and the luster will be dark, in this regard, the cooling system should be improved during custom ABS plastic injection molding .
In Moldflow software, when analyzing warpage, the deformation results caused by different reasons can be analyzed separately, so that the main cause of deformation can be easily judged.
Plastic prototyping is essential to developing new products since it helps bring imaginative concepts to life. Before proceeding with mass manufacturing, you can visualize and test your ideas.
You benefit from seeing and touching your product in actual form when you use plastic prototyping. This gives you a more precise understanding of its size, characteristics, and general shape. The prototype’s ergonomics, user experience, and room for development may all be better understood by touching the part in your hands.
Since the cause of the short shot has been identified, increasing the thickness of the product rib can reduce the flow resistance and thus eliminate the stagnation problem. The thickness of the product rib is thickened from 1.0 mm to 1.5 mm (as shown below).
3.3.1 The plastic granule size of raw materials varies greatly, which makes it difficult to melt evenly and makes the appearance bad; the raw materials should be sieved before starting ABS injection molding.
GETTING A QUOTE WITH LK-MOULD IS FREE AND SIMPLE.
FIND MORE OF OUR SERVICES:
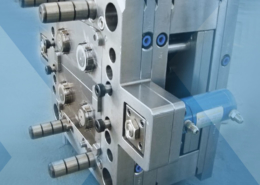
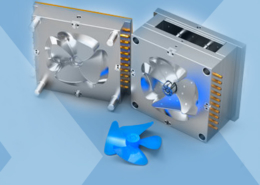
Plastic Molding

Rapid Prototyping
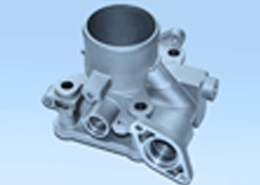
Pressure Die Casting
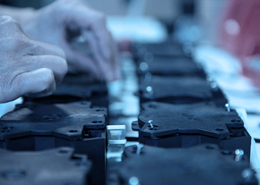
Parts Assembly
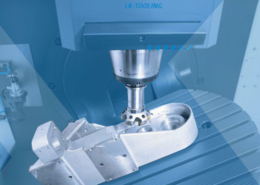