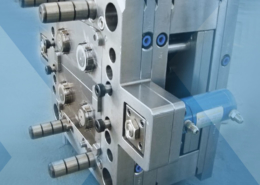
The role of injection moulding in medical device ... - injection molding medical
Author:gly Date: 2024-10-15
The simple answer is that plastic injection molds range in price from $100 for a 3D printed injection mold to $100,000 plus for a sophisticated multi-cavity steel mold for greater manufacturing loads, which is typically the most important fixed start-up cost in injection molding. However, because these expenses are spread across hundreds or thousands of components, injection molding is a suitable method for mass-producing plastic parts at a low cost.
What Thermoset Molding Provides – Lowers component or product assembly weight over metallic applications without compromising product performance.
Customer Pain Point – Components or product assemblies may degrade or disfigure while exposed to high heat and high operating temperatures during application use.
Whether a product assembly is completely new to the market, or an existing project exploring a material conversion from a metal or thermoplastic to thermoset; Woodland offers thermoset molding capabilities to alleviate product pain points, reduce manufacturing costs, consolidate the number of parts in an assembly, and improve overall product performance. Implementing molded thermosets into a product assembly protects internal components and product assemblies from degradation or failure, providing an assurance of safe handling and user operability.
Depending on the needs of the finished products, a broad range of polymers can be utilized for injection molding. The cost involved when you buy plastic injection mold materials varies depending on the material selected. Thermoplastic pellets range in price from $1 to $5 per kilogram.
With small desktop injection molding equipment and 3D printed molds, creating modest volumes of components with injection molding is the most cost-effective. Small-scale automated injection molding machines are viable options for medium-series manufacturing of small components.Large industrial injection molding machines can range in price from $50,000 to more than $200,000. These machines also have more strict facility requirements and the need for specialized staff for operations, upkeep, and monitoring. As a result, although injection molding is a core competency, most businesses outsource mass manufacturing to service providers and contract manufacturers, with equipment expenses included in the service prices.
What Thermoset Molding Provides – Heat resistance, temperature deflection, & dimensional stability up to 500° Fahrenheit and above.
For questions on Woodland Plastics’ thermoset molding capabilities, please contact us via email at sales@woodlandplastics.com or reach us via phone at (630)-543-1144.
Ph: 630.543.1144 | Fax: 630.543.1525 info@woodlandplastics.com
What Thermoset Molding Provides – Consolidation of multiple parts of an assembly. Elimination of costly secondary machining or painting operations.
Creating more sophisticated molds necessitates technical knowledge. As a result, companies typically outsource specific aspects of injection molding, for instance, mold design and production.
To a certain degree, asking for the costs of plastic injection molds cost is similar to questioning how much a car costs. Is your mold going to be a Pinto or a Porsche? Also, keep in mind that the cost of a mold is only the beginning. To calculate complete plastic injection molding costs for any projects, you must also include raw material, operating, and maintenance expenses in the future. These costs are a result of the aforementioned contributing factors.
Injection molding, the major cost driver is generally mold or tooling expenses. Molds for injection molding are typically created in one of three ways:
Mold manufacturer location: This was also mentioned while researching how mold size may affect your total injection molding expenses. To have your mold wherever it needs to go, an off-site plastic injection mold maker will charge you extra for shipping and handling.
3D printers can manufacture basic low volume 3D printed molds for as cheap as $100. A metal mold for a mid-volume service life of 1,000-5,000 units costs between $2,000 and $5,000. Mold costs can range from $5,000 to $100,000 for molds with more complicated shapes and prepared for higher production runs of 10,000+ pieces.
Why Partner with Woodland Plastics – With extensive thermoset molding experience, Woodland Plastics manufactures heat-stable components that remain dimensionally stable even within high operating temperatures.
When it comes to injection molding prices, basic plastic injection molds might range from $3,000 to $6,000. A big, more sophisticated high-production, cross-cavity mold can cost between $25,000 and $50,000 or more. Although it may seem obvious, several factors contribute to the cost of injection molding.
Why Partner with Woodland Plastics – Woodland Plastics offers integrated manufacturing solutions with support in engineering, tooling, and material selection to efficiently convert customers’ existing metal components or product assemblies to thermoset to drive product performance and lower manufacturing costs.
With decades of thermoset molding experience, Woodland Plastics specializes in injection molding of thermoset materials or composites including Phenolic, Bulk Molding Compound (BMC), Epoxy, and DAP with injection press tonnage from 80-500T for both large and small components. Our customers rely on Woodland Plastics as a preferred thermoset molder within a variety of industries and end products. Woodland Plastics molds parts for the Appliance, Automotive, Electrical, Energy, and Industrial markets that require components and assemblies to withstand aggressive and challenging environments. The environments suitable for thermosets include applications experiencing high and intermittent operating temperatures, electrical current, corrosive environments, outdoor and UV exposure, and applications exposed or submerged in chemicals, oils, and/or automotive fluids. Woodland Plastics has offers thermoset molding processes of injection, injection-compression hybrid, and insert molding.
Why Partner with Woodland Plastics – Woodland Plastics has decades of experience molding for a variety of customer and product end-markets including for product applications exposed to oils, fluids, salts, and moisture.
For injection molding, special-purpose equipment ranging from tiny personal molding machines that enterprises may use in-house to big industrial injection molding equipment primarily handled by providers, contractors, and major manufacturers is utilized.
Material cost is determined by the design of a product, the material utilized, and the quantity of material needed to complete the injection molding process.
Why Partner with Woodland Plastics – Woodland assists with customer light-weighting efforts and leverages approved suppliers for tooling and material selection, keeping overall manufacturing costs competitive against metallic or thermoplastic components.
What Thermoset Molding Provides – With excellent chemical resistance and stability, thermoset product assemblies and internal components will not corrode, nor be affected physically when exposed to harsh chemicals, fluids, or other challenging environments.
If a plastic injection mold factory has the tools and materials, creating molds in-house may be the most cost-effective option if the technical expertise is also accessible. If the tools required for injection molding are not easily accessible, outsourcing lowers the cost of developing a mold.
Typically, the cost of the mold, also referred to as the tooling cost, is the major cost driver in injection molding. Let’s take a look at some of the elements that influence the price of an injection mold.
Customer Pain Point – Product application may be exposed to oils, automotive fluids, or even rainwater run-off including salts or other chemicals.
GETTING A QUOTE WITH LK-MOULD IS FREE AND SIMPLE.
FIND MORE OF OUR SERVICES:
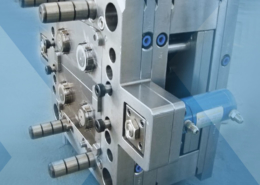
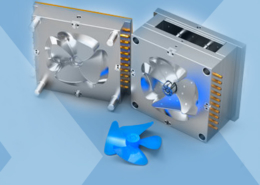
Plastic Molding

Rapid Prototyping
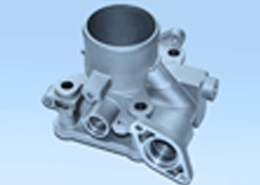
Pressure Die Casting
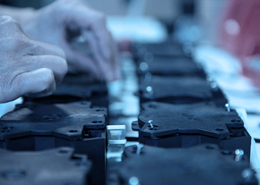
Parts Assembly
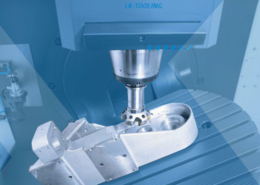