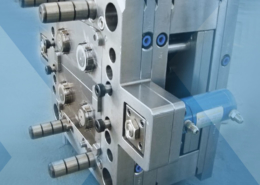
The Difference Between Double Shot Molding and ... - twin shot injection mouldin
Author:gly Date: 2024-10-15
One of the advantages that foam molding has is that the process is fast. Combined with properties that support the use of this type of component in vehicles, it is a very cost-effective choice for companies in the automotive industry.
Foam molding also provides more possibilities in terms of product design. Using the foam molding process, it is possible to create custom-shaped parts and efficiently combine smaller parts into a complete component.
In addition to EPP foam, Knauf also offers EPS foam molding. This type of material is widely used in the industry. In the automotive industry, it is used to create technical interior components and packaging, among other things. Expanded foam molding, which produces EPS, is a process used by many companies.
Knauf Industries offers numerous products made using structural foam molding technology. Using advanced foam molding machines combined with the extensive experience and knowledge of the specialists, Knauf factories can consistently deliver high-quality EPP foam and EPS polystyrene components. These are materials that are widely used in the automotive sector. Internal EPP and EPS automotive components are just one example – Knauf manufactures dashboard parts, door panels, flooring components, trunk elements and cockpit parts, and much more.
Plastics processing is the core business of Knauf Industries. The company specializes in the innovative technology of foam molding, among other things. Knauf has many years of experience in plastics processing – including the molding of EPP foam parts. Companies involved in foam molding, such as Knauf Industries, are becoming increasingly important in the automotive market due to the growing popularity of EPP and EPS components. With years of experience and proven technology, Knauf Industries is the brand that many automotive manufacturers trust.
When collaborating with customers, we focus on tooling design and manufacturing strategy to provide an optimal solution for each product. Trelleborg will take your plastic product and see its completion from concept to manufacturing.
Plastic injection molded parts are also often used as inserts for products such as overmolded diaphragms and gaskets, where increased rigidity is needed to ease product assembly or to obtain improved permeation resistance.
Trelleborg Medical Solutions provides a wide range of comprehensive services for your molded part requirements. As a specialist in custom plastic injection molding for medical devices, we partner with you to produce impactful products to improve patient quality of life.
Another category is high-quality EPP car seats – this is the best material for making these types of components. EPP seats are very durable and comfortable, and they are also much lighter than parts made of other plastics, which allows you to reduce your vehicle's operating costs.
Ask your question in a 1 on 1 enquiry and we will give you a detailed answer, whatever the country/region you need our support.
The foam molding process is a technology that plays a vital role in automotive manufacturing. Learn more about what Knauf Industries offers and the opportunities associated with this process
Knauf Industries experts have the know-how to mold foam materials like EPS, EPP the right way and produce the highest quality automotive components. Contact us and take advantage of the latest technological processes in automotive manufacturing.
Foam molding is a technological process that creates components by injecting foam under low pressure into a mold. Injected material (beads) contains blowing agent. Thus, when injected into the mold and heated, the gas activates expansion which fills periphery of the mold. Thus, when injected into the mold, the gas or selected substance pushes the foam to the periphery of the mold. As the manufactured component cools down, the foam element takes on its desired properties – it becomes strong while remaining lightweight.
The foam molding process is one of the many parts of the Knauf Industries product range. In addition to manufacturing automotive parts, the structural foam process makes it possible to produce various types of packaging, which can be an important part of a modern company's logistical processes. The high durability of products made from this material encourages reuse, which can reduce a company's carbon footprint, among other things.
Foam molding offers numerous advantages for companies involved in vehicle manufacturing and outfitting, as well as for companies in other industries. Today, foam parts are increasingly replacing parts traditionally made of metal or other plastics. One of the benefits is the lower weight of the material itself, which translates to a reduction in the total weight of the vehicle and thus greater energy savings.
Custom plastic injection molded parts from Trelleborg Healthcare & Medical are used in many medical applications. Typical areas include:
We manufacture injection molded plastics into custom shapes such as gears, impellers, valve balls and ball seats. We can combine our molded parts with other machined parts and seals to make Durobal® bearing assemblies and sub-assemblies which improve performance and simplify the product assembly process for our customers.
This manufacturing process also helps save raw materials compared to other methods of creating automotive components. It is also worth noting that this type of technology works perfectly due to the high durability of the parts made. Thanks to the foam molding method of manufacturing automotive equipment, it is also possible to increase the safety of drivers and passengers.
Knauf Industries offers comprehensive services related to the foam molding method. Foam molding projects for a specific customer are approached on an individual basis. Experienced specialists at Knauf assess the needs of the customer and determine the technical requirements that the foam process and the parts produced must meet. This way, customers can be assured that orders are prepared in the best possible way. Knauf Industries also has a dedicated management system that provides engineering support to original equipment manufacturers and direct suppliers throughout the product development and life cycle.
GETTING A QUOTE WITH LK-MOULD IS FREE AND SIMPLE.
FIND MORE OF OUR SERVICES:
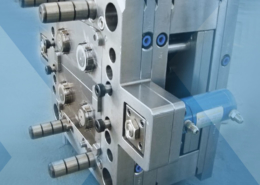
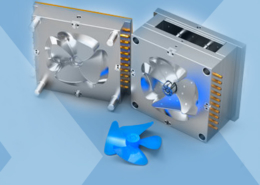
Plastic Molding

Rapid Prototyping
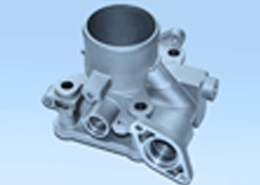
Pressure Die Casting
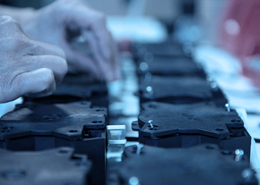
Parts Assembly
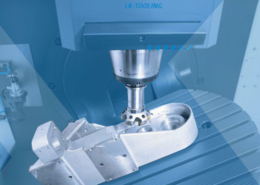