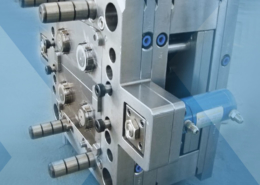
Tailoring Our Medical Injection Molding Services to Meet ... - all american inje
Author:gly Date: 2024-10-15
Molding materials that are thermoset include Bulk Molding Compound (BMC), Phenolic, Epoxy, and Diallyl Phthalate (DAP). Bulk Molding Compounds are unsaturated polyesters and vinyl esters. Thermosets can be injection, compression, injection-compression, or transfer molded. The main molding or processing difference between thermosets and thermoplastics is that thermosets are molded into a preheated or hot mold at around 350F. The thermoset resin meeting the hot mold causes a chemical reaction, and gives the molded part its strong end properties. A thermoplastic on the other hand is molded into a cooled mold to form the molded parts, and does not offer the same stability thermosets offer in its molded properties.
Thermosets are synthetic composites or plastics that strengthen when heated but cannot successfully be remolded or reheated after being molded. Parts and components molded from thermosets offer excellent dimensional stability in high temperature and electrical environments. Thermosets offer material properties that provide resistance to corrosion, UV exposure, and aggressive chemicals such as oils and automotive fluids, making thermosets an ideal material choice for part assemblies exposed to outdoor elements and automotive applications. In electrical applications, thermoset molded components exude exceptionally strong electrical properties, electrical insulation, dielectric strength, and resistance to electrical arc and track. Thermoset materials protect the integrity of a molded part and internal electrical components and wiring throughout a product life cycle as parts will not degrade or disfigure under electrical exposure that thermoplastic molded part may experience.
There are a variety of manufacturing methods used to create plastic molded products. Two methods mentioned in this article, double shot molding and overmolding, are viable manufacturing processes that offer several advantages for many plastic manufacturers. Both processes can be difficult to master since they require adherence to the very tightest of tolerances. Below, we discuss the differences and advantages between double shot molding and overmolding.
Double shot molding is an ideal process for complex, multi-material, and multi-colored plastic products; specifically in high-volume production scenarios. Other advantages include:
Overmolding can be added to change the surface of a piece or product by adding texture, color, and incorporating necessary functionality components. Other advantages include:
In layman terms, molding or curing a thermoset is like cooking an egg or baking a cake. Once an egg is dropped into boiling water and cooked, it cannot revert to its original physical state as a yoke. Similarly, after thermosets are molded, it cannot be ground up and reprocessed or remolded.
As mentioned above, these processes are relatively simple to understand. However, it is highly difficult to master. It requires high levels of technical expertise and attention to detail. When dealing with high-volume production scenarios, the smallest mistake can be costly. This is why it is critical to find a highly capable molding manufacturer. Once you find one, you need to involve them early on in the design phase of your part, as they can engineer value and quality into any problem areas. If you have questions or concerns regarding your part or the double shot or overmold processes, contact our experts at Midstate Mold today!
Ph: 630.543.1144 | Fax: 630.543.1525 info@woodlandplastics.com
With an array of material property benefits, molded thermoset parts are used in a variety of customer end-markets and applications that require a strong, durable material capable of withstanding aggressive elements. Thermosets will not degrade with exposure to certain chemicals, oils, and automotive fluids. In electrical applications and assemblies, thermoset parts protect internal components with superior dielectric strength and electrical insulation. In outdoor applications, thermoset components remain durable even in wide-ranging weather conditions including exposure to heavy sunlight and UV, rain, sleet or snow. Whether a product application functions in Alaska or Arizona, thermosets remain a preferred material choice of engineers and designers for challenging applications requiring heat-stable components. Cost-wise, thermosets are advantageously priced per pound against similarly-performing engineered thermoplastics.
If you are overmolding a metal part with plastic, you can really use any type of plastic. If you are overmolding a plastic part with another plastic, then there can be some compatibility issues. Your experienced molder will be able to recommend the best materials suitable for your project
Double shot molding, sometimes referred to as two-shot molding, is a manufacturing process used to produce complicated molded parts from two different materials by molding plastic around a preformed metal or plastic insert. The process is relatively simple; one material is injected into a mold in order to make the initial piece of the product, followed by a second injection of another material that is compatible with the initial injection molded piece. The two plastic resins then form a molecular bond and the multi-resin molded part is cooled and ejected.
In scientific terms, a thermoset monomer must have three or more reactive ends, with its molecular chains crosslinking in three dimensions. Post-molding, thermosets have virtually all molecules interconnected with strong, permanent, physical bonds which are not heat reversible. Thermoplastic monomers on the other hand, only have two reactive ends for linear chain growth.
Overmolding is a process of adding an additional layer of material over an already existing piece or part. This process is regularly used to manufacture parts, sub-sections of parts, and for prototype development. Typically, the substrate material (the first piece in what will be bonded and mechanically interlocked with other materials) is placed into an injection molding tool, at which point the overmold material is shot into or around the substrate. When the overmold materials solidify, the two materials become joined together as a single part.
Filed Under: Our blog Tagged With: double shot molding, double shot molding and overmolding, injection molding manufacturer, overmolding injection molding, plastic injection molding, two-shot molding
GETTING A QUOTE WITH LK-MOULD IS FREE AND SIMPLE.
FIND MORE OF OUR SERVICES:
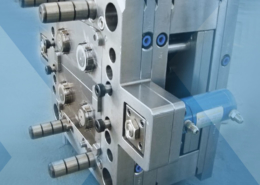
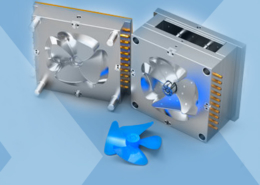
Plastic Molding

Rapid Prototyping
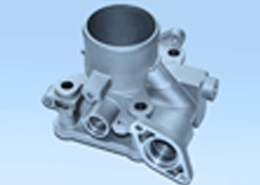
Pressure Die Casting
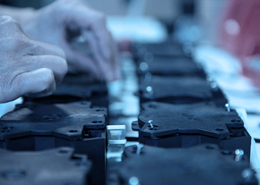
Parts Assembly
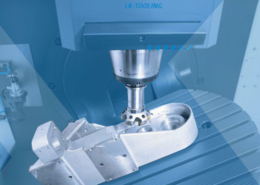