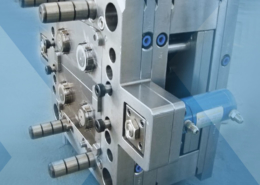
Sustainable materials for injection molding - plastic injection products
Author:gly Date: 2024-10-15
Plastic molding stands as a cornerstone in the world of manufacturing, integral to the creation of virtually every product available in today‘s market. The diverse methods employed in plastic molding contribute to the distinctiveness and innovation of its products. This versatility, allowing for the crafting of any shape, design, or configurationâno matter how intricateâis a testament to its widespread success and continued expansion.
Another highly popular and versatile molding technique is plastic extrusion. This process is renowned for its ability to create a vast array of flexible, sturdy, and durable products. Like other plastic molding methods, extrusion begins with heating resin. However, instead of placing the resin into a mold, extrusion involves forcing it through a die that shapes the resin into the desired profile. This efficient and rapid process is capable of producing products tailored to a wide range of applications, making it a cornerstone in the field of plastic manufacturing.
You can create a new account at the end of the order process or on the following page. You can view all of your orders and subscriptions in your customer account. You can also change your addresses and your password.
Rapid prototype injection molding is a preferred method that not only helps engineers and designers confirm part quality, but also delivers real-world parts that can be market-tested before designs are considered finalized. In addition to design verification and structural validation, you can use rapid prototype injection molding to help finalize tooling designs for your long term production runs. Rapid injection molding greatly benefits buyers of products with strict appearance requirements and functionality early in product launch phases. Before you spend extra on production tooling, contact MSI Mold for a quote rapid prototype injection molding. Other benefits of making prototype plastic parts before full scale manufacturing begins include:
In the realm of fiberglass-reinforced plastic manufacturing, fiberglass molding stands as the cornerstone process. Fiberglass is created when molten glass is meticulously drawn through minuscule apertures in specialized tools, resulting in fine, threadlike structures. These threads undergo further refinement through heat treatment or pressing and are then amalgamated with plastic resin to form the desired material.
From time to time you will find us at design fairs and popup markets in Switzerland. Subscribe to our newsletter and you’ll receive the latest news.
One of the primary advantages of plastic molding is its adaptability to a broad spectrum of materials. These include fiberglass-reinforced plastics, polyurethane, polypropylene, polyvinyl, and various types of acrylics. Each material undergoes heating and shaping through specific processes tailored to the final product‘s form, required strength, and design complexity. This flexibility ensures that plastic molding can meet the demanding and varied needs of modern manufacturing.
Blow molding can be broken down into three primary techniques: injection blow molding, extrusion blow molding, and stretch blow molding. Each method follows a two-step process, with variations primarily occurring in the initial stages. The final shape of the plastic product is determined by the mold cavity, allowing for an extensive range of standard shapes and sizes. Additionally, custom blow molding offers the flexibility to create unique products tailored for specialized applications, demonstrating the boundless possibilities of this dynamic manufacturing process.
In a supporting role, 3D printing is sometimes useful to correct early design flaws and help visualize a finished product. But one clear benefit of using prototype injection molding is gaining manufacturing experience and knowledge that can be applied when starting to prepare for production . Testing the chosen production material along with the injection mold design offers the manufacturer a preview of any potential problems that may arise in future production.
Polyurethane stands out as a versatile material prized for its dual flexibility and rigidity, making it indispensable in memory foam products. Its utility extends to solid plastic forms, polyurethane rods, urethane wheels, bushings, and sheets. Renowned for high performance, polyurethane moldings surpass plastic in durability and outshine rubber in impact resistance. They boast elastic memory, noise reduction, and resistance to heat and chemicals, embodying the best attributes of metal, rubber, and plastics. Moreover, polyurethane can form robust adhesive bonds with most plastics and metals.
Fiberglass molding finds its application in a diverse array of products, ranging from machinery support components and electric circuit boards to the sleek shells of racing cars and durable panels. Its widespread use is attributed to the remarkable properties of fiberglass: it remains stable across temperature fluctuations, resists water absorption, withstands chemical exposure, boasts a high strength-to-weight ratio, is non-flammable, and is an excellent electrical insulator. These characteristics make fiberglass molding an indispensable technique in modern manufacturing.
The design features of a prototype injection mold should try to represent the basic design intent of a future production mold within a budget. Using the intended gate location and type, ejection locations and other important tooling features can help designers and engineers discover any manufacturing challenges. Be cautious of prototype injection molds that are constructed using 3D printer technologies. 3D printed prototype molds are not representative of true production injection molding conditions.
Advanced injection molding techniques include insert molding and reaction injection molding (RIM). Insert molding involves injecting molten plastic around a solid object, such as an electric coil, to create an encapsulated product. On the other hand, RIM combines a liquid resin thermoset polymer, typically polyurethane, with liquid polyisocyanate. The polyisocyanate acts as a reagent within the mold, causing the polymers to expand and form either open or closed cell foam, effectively filling the mold.
Plastic tubing encompasses a wide range of tubes and pipes made from various plastics. Its versatility ensures its presence across numerous industries, from the stringent demands of aerospace and industrial applications to the sterile safety standards required in medicine and beverage tubing.
Rotational plastic molding is a powerful process for producing plastic parts with exceptional strength and intricate structural details, surpassing the capabilities of other molding techniques. This method is distinctive in that it generates parts in relatively low volumes, making it ideal for specialized, short-run production. While it may not be suitable for mass production like blow molding, dip molding, or thermoforming, it is the go-to process for creating complex and high-performance components such as detailed plastic figurines and military-grade rackmount carrying cases.
What sets rotational molding apart is its unique process. Molten polymer, often polyethylene or polycarbonate, is poured into a closed, three-dimensional mold. This mold is then placed in a gyroscope-like machine that rotates slowly, allowing the polymer to coat the entire interior evenly, forming a hollow structure. This technique not only excels at crafting complex shapes but also ensures that the parts have uniform material consistency, resulting in very high strength and durability.
No, we don’t have a physical store location at the moment. We accept only orders through our online shop and we’re shipping all orders with the Swiss Post Service. Please visit our shipping section for more details.
Injection molding is a prevalent and versatile plastic molding technique, known for its ability to produce three-dimensional, solid parts with mid to high strength. The cost of the process varies significantly based on the part‘s complexity and the materials used. What sets injection molding apart from other plastic molding methods is its capability to create relatively intricate shapes.
Beware of “production injection molds”. Engineers and buyers within the injection molding industry blindly specify that production injection molds should be made from steel. The first assumption of most any injection molding company is that production injection molds are made from steel. As mentioned above, the proper reference between a prototype injection mold and a production injection mold should not be the metal that it is made from. A production injection mold should be designed and constructed to accomplish the fastest cycle times, the highest quality parts, and the longest tooling life possible no matter the metal that it is made with!
The plastic molding industry continues to expand, playing a crucial role in the design and production of numerous household and industrial products.
Dip molding plastic stands as one of the most straightforward and cost-effective methods for producing a vast array of parts and products. This versatile process rivals blow molding in its ability to generate large quantities efficiently. Dip molding serves two primary functions in manufacturing: crafting complete flexible or rigid items, like rubber gloves, condoms, and plastic caps, and coating pre-manufactured items such as wire racks, cables, and plastic handles.
Any mold within this category is available at considerably less cost than traditional injection mold tooling. This cost assumption is considered true most of the time. But, any mold that is manufactured by “rapid prototyping” should be assumed as made by 3D printing and 3D printed molds have a very narrow set of advantages. With their relatively quick manufacturing time, they offer a cost-effective way to test a basic design but should only be used for extremely low quantity molding. In most cases, a prototype injection mold made from aluminum is a much better choice for near the same cost.
On the other hand, vacuum forming offers a distinct approach to plastic molding. Instead of heated resin pellets, this method uses plastic sheets, which are thermoformed by being forced into an open mold. This technique, free from the constraints of a two-part mold, is instrumental in manufacturing components like spacecraft walls and hot tubs.
Polyurethane molded parts typically require minimal to no finishing, streamlining the manufacturing process. This efficiency makes polyurethane the material of choice for producing a diverse range of products, including moldings, parts, bowling balls, urethane bumpers, belts, conveyor bushings, electrical potting compounds, press tool blocks, and pneumatic seals. Its applications span numerous industries such as athletic equipment, engineering, manufacturing, industrial, food processing, automotive, and construction. Discover the transformative potential of polyurethane molding.
Blow molding is the versatile backbone of countless consumer products. From robust tanks to sleek CD cases, any hollow, three-dimensional item you can think of likely owes its existence to this innovative process. Blow molded products are designed to safely contain a wide range of substances, including herbicides, pesticides, cosmetics, and automotive oils. The secret behind this versatility lies in the thermoplastic resins used in blow molding, such as acetal, polysulfone, polyamide, polystyrene, butadiene styrene, Barex, polyvinyl chloride (PVC), and both high and low-density polycarbonate.
Vacuum-formed plastics serve as faceplates and semi-flat components across various industries, particularly in electronic devices like fax machines, keyboards, phones, and home appliances. This process, also known as thermoforming or pressure forming, starts with plastic sheets instead of polymer resin pellets. These sheets are heated until pliable, then vacuumed into an open mold, where they conform precisely to the shape of the die beneath.
Blow molding, another pivotal method in plastic manufacturing, is celebrated for its efficiency and speed. This process produces items ranging from plastic bags to bottles designed to hold makeup, chemicals, and soft drinks. By heating resin and inflating it with air, blow molding allows the material to conform to the mold's shape. The versatility and rapid production capabilities of blow molding have established it as a favored technique for manufacturing a wide array of plastic products.
Injection molding, a mainstay in plastic manufacturing, involves the meticulous process of heating resin pellets and injecting the molten material into a closed mold. This technique has revolutionized the production of an extensive array of products, including encapsulated electric coils, protective helmets, car bumpers, medical syringes, and various types of toys. Its precision and reliability have made injection molding indispensable in the creation of numerous everyday items.
Through our plastic prototyping services we can offer you the same options that exist for long term production projects:
Extruded plastics are tailored to meet a wide array of specialized applications, such as building trim, window and door sealants, vinyl siding, PVC pipe, and surgical tubing. Additionally, plastic sheets and flexible plastic sheet rolls are produced through extrusion. In this variant, the melted plastic is stretched rather than cooled after exiting the die. Flexible sheets pass through a series of large calenders before being rolled onto a tube. Discover more about the fascinating world of plastic extrusions.
Rotational molding, a specialized plastic processing technique, excels in creating individual and large-scale plastic products such as expansive bins, high-quality auto parts, boats, and sports equipment. This process utilizes a heated hollow mold filled with a precise amount of plastic material. As the mold rotates slowly, the plastic evenly coats the interior walls, resulting in products with exceptional strength and structural complexity.
Unfortunately, we’re unable to offer free samples. As a retailer, we buy all magazines from their publishers at the regular trade price. However, you could contact the magazine’s publisher directly to ask if they can send you a free copy.
We often send out our newsletter with news and great offers. We will never disclose your data to third parties and you can unsubscribe from the newsletter at any time.
Twin sheet thermoforming is often employed for creating large, precision parts such as hot tubs and aerospace interior wall panels. Beyond these specialized applications, thermoforming offers a highly cost-effective method for producing three-dimensional plastic packaging. Vacuum forming can efficiently manufacture blister packs, clamshells, plastic covers, and trays, delivering low-cost solutions at high production volumes.
Plastic extrusions are crafted in a manner akin to injection-molded plastics, but with a distinctive twist: they take shape through an open die. The process begins as plastic resins, including PVC, acrylic, polypropylene, or ABS, are funneled into a hopper and fed into the extruding barrel. Here, the resin is sheared and melted before being propelled through the open die to form a specific profile or shape. This newly formed profile is immediately submerged in cold water to set the plastic. The continuous extrusion process sees the profile passing through the die, cooling in water tanks, and arriving at a sawing table, where it is cut into pre-determined lengths.
This streamlined approach enables the efficient production of durable, high-quality plastic goods, meeting a wide range of industrial needs.
Recent news heavily features the advent of 3D printing technology as a solution for many prototype injection molding applications. Real world plastic injection molding can still be the best alternative for most prototyping scenarios in many cases. You should be aware of each prototyping method’s strong points to understand which is best suited for your application.
MSI Mold’s team of experienced tooling engineers and injection molding technicians can guide you for your specific custom plastic part prototyping needs. We can:
The dip molding process follows a simple yet effective sequence. First, a large batch of glass or metal molds undergo surface preparation to ensure the final product easily releases once dry. For items being coated, meticulous buffing and prepping ensure the plastic adheres securely. These molds are then immersed in a vat of molten polymer or elastomer resin. Depending on the desired thickness and material consistency, molds may undergo multiple dips, sometimes alternating between the polymer bath and a cold water or solidifying reagent. Complex layered products, like kitchen gloves, might incorporate additional layers, such as fabric, between polymer coatings. Once the plastic sets, the product is ready for removal, trimming, cleaning, and finishing.
To enhance the strength and durability of many products, they often require a protective coating. One effective method to achieve this is dip molding. This process involves immersing a completed product into a bath of resin. After being thoroughly coated, the product is removed and subjected to a drying process, which cures and hardens the plastic coating. Dip molding is a precise technique that significantly enhances the quality and resilience of various products.
GETTING A QUOTE WITH LK-MOULD IS FREE AND SIMPLE.
FIND MORE OF OUR SERVICES:
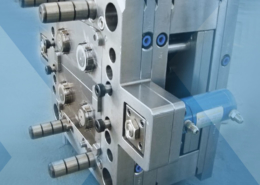
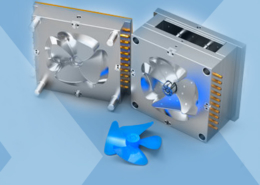
Plastic Molding

Rapid Prototyping
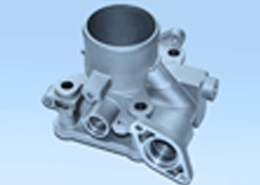
Pressure Die Casting
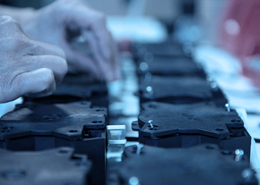
Parts Assembly
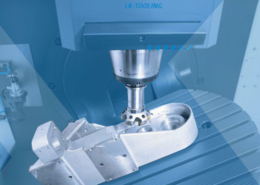