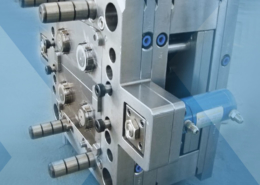
Sustainable materials for injection molding - plastic injection products
Author:gly Date: 2024-10-15
One of the greatest barriers to injection molding is the high price of the mold itself. We provide several options to lower you capital expenses including free molds for high volume projects and low cost prototype molds.
When you need high quality, injection molded parts for a reasonable price, we are the partner you can count on. This is why our customers keep coming back, over and over again.
Creating plastic molds at home is an exciting and useful skill that can be applied in various scenarios, from crafting to product development. This article will explore the process of making plastic molds at home, delving into the necessary steps, materials required, and the benefits of DIY molding. We will also consider the views of experts and provide tips for successful outcomes.
No, due to the limitations in accuracy associated with this file format it is not a viable option for building injection molds.
The team at Rapid Molding is amazing! They helped me improve my design to produce better results with injection molding versus machining and 3D printing. We are already working on our next project with them!
As pioneers in the rapid injection molding industry, we’ve used our research to develop faster, lower cost methods for manufacturing injection molds. Our relentless pursuit of process optimizations reduces human labor, resulting in industry-leading delivery, cost efficiency, accuracy, and tool life. Experience the Rapid Molding advantage — your shortcut to faster, more cost efficient injection molding.
I send all my plastic parts to Rapid Molding for prototype molding and/or bridge tooling. I get accurate parts for testing and the price is right. Plus their bridge tools often satisfy our production molding requirements.
Today we offer a full range of injection molding services that utilizes these three decades of experience to deliver everything from prototype injection molded parts to high volume custom injection molding, all with greatly reduced lead-times and competitive pricing.
We've run several projects through Rapid Molding since 2016. I've yet to find a mold maker/molder that can meet our early R&D needs, then roll straight into production, all within budget.
Plastic molding is a manufacturing process that involves creating a replica of a desired shape or design using plastic material. At-home molding generally involves using a mold-making material, such as silicone or plastic putty, to create a mold that can be used for casting plastic parts or components. Understanding the fundamentals of plastic materials, their properties, and how they behave during the molding process is crucial for successful outcomes.
Yes, in 2023 we changed our branding to better reflect the full-service nature of our business, which is building rapid molds and providing rapid injection molding services.
No more missed production deadlines. No sacrificing quality to fit your schedule. No long term expenses that pile up. Just on time, every time high quality parts.
The first step in making plastic molds at home is to gather the necessary materials and tools. Key items include plastic putty, silicone, molding sand, carving tools, and a heat source for shaping the mold. It is also important to have basic knowledge of how to use these tools effectively. The selection of materials will depend on the specific project and the desired outcome. For instance, silicone is often preferred for its ability to produce detailed and smooth molds.
Rapid Molding prides itself on swift turnarounds. Typically prototype injection molding lead-times are are 1-4 weeks. Whereas bridge tooling and production tooling lead-times can run 3 to 8 weeks depending on the size and complexity of the parts. In general, we deliver production molds 50% to 70% faster than industry standards, ensuring your projects hit the market without unnecessary delays.
Nothing, the term "tool" is a broad term that could refer to many different tools or dies, but in our process it is interchangeable with the term "mold".
In our process, there is no tangible difference in the parts. Some prototype molders may take shortcuts, like rounding off corners or eliminating water lines in the mold in an effort to reduce costs. We do not make these compromises.
Yes, we have provided plastic product design services for over 30 years and have engineers on staff that are very knowledgeable about injection molded part design.If you need assistance with 3D CAD creation or modifying your part design for better results with injection molding, inquire with your CSE (Customer Service Engineer).
Ready to revolutionize your product development and production processes? Experience 100% on-time delivery, backed by over 30 years of industry experience. Join thousands who trust us for high-quality injection molded Parts at the best prices. Don’t let mold costs hold you back – let’s bring your projects to life with precision and efficiency. Request a Quote now to get started.
Experts in the field of plastic molding often emphasize the importance of following safety guidelines and using high-quality materials for successful outcomes. They also recommend starting with simple designs and gradually progressing to more complex projects. Additionally, taking care during the mold-making process, particularly when handling hot materials, is crucial to avoid accidents. Experts also suggest seeking guidance from experienced hobbyists or professionals to enhance skills and knowledge.
We've used Rapid Molding on several projects in the past few years. They're our secret weapon for projects on tight timelines. They make us look good!
Rapid Molding, formerly Rapid Molds (RapidMolds.com), began with an idea, to cut mold build lead-times in half. In 1993, that simply meant high-speed machining, better EDM technology and optimized manufacturing routing (no part of the mold sits idle, until it’s complete). Additionally, we considered all options for every project, like proprietary mold systems and 3D printed cores and cavities. Over time the pursuit of lower costs and shorter lead-times drove us to employ improved high-speed machining techniques and faster, more precise machining equipment. Additionally, we developed no-polish EDM techniques and worked with our support network for specialty components and custom mold bases to improve their lead-times.
We continues to enhance our visibility and reputation, including exhibitions all over the world and we also actively taking corporate social responsibility.
In summary, making plastic molds at home is a rewarding endeavor that allows for creativity, customization, and cost-effective production. By understanding the basics, gathering the necessary materials and tools, following the steps carefully, and seeking expert advice, individuals can successfully create plastic molds at home.
We started using Rapid Molding because they could make our parts quickly without compromising our designs and at a fair price. We've come back because they are dependable and the quality is excellent.
There are numerous benefits to making plastic molds at home. Firstly, it allows for creativity and customization, enabling individuals to create unique designs and shapes that are not available commercially. Additionally, it is a cost-effective way to produce small quantities of parts or components, eliminating the need for expensive manufacturing processes. Furthermore, it provides a hands-on learning experience that enhances understanding of plastic materials and molding techniques.
• Moderate volume production • Parts in 3-6 weeks • Capable of 300k+ cycles • Family and multi-cavity molds • Automatic undercut details • Automatic unscrewing molds • Fully automatic production
At first I wasn't happy to have a new vendor pushed on me by our engineering department, but after 2 years of on time deliveries with zero quality issues, I have added Rapid Molding to my preferred vendors list. Thank you John!
We've been working with Rapid Molding for nearly 10 years. They're so dependable that this has become our standard process for getting to market quickly.
• Low volume production • Parts in 2-4 weeks • Capable of 10k+ cycles • Undercuts & unscrewing details • Square corners • 55 to 1200 tons
As an engineer, precision is everything. Rapid Molding not only delivered the desired accuracy, they did not require making changes to my parts. That was a huge advantage over the previous prototype molder.
Bridge molding utilizes a bridge tool to accomplish low to moderate volumes of molded parts quickly and cost efficiently. There are small sacrifices in tool longevity with a bridge mold versus a production mold, but often times a bridge tool has more life than many projects need (300k+ cycles). Whereas rapid production molding spares no expense when it comes to tooling and is therefore the king of low cost, high-volume production injection molding.
The process of making plastic molds at home involves several steps. Initially, a design or shape is created using either a 3D model or a template. Then, the mold-making material is applied to this design, following the contours and details of the shape. The material is then allowed to set and harden, creating a mold. This mold can be further refined and adjusted for precision. Finally, the mold is ready for casting plastic parts or components.
Our preferred 3D CAD format is STEP, as it imports into all of our CAD/CAM/CAE software smoothly. We can also accept IGES, IGS, STP, X_B and X_T, but we must have actual 3D CAD to provide accurate proposals or provide a molded product.
Rapid Molding has been providing rapid injection molding services for over 30 years! With tens of thousands of successful projects in our portfolio, we are the first and last partner you'll ever need.
Absolutely! We have decades of experience with complex molding projects. We are well equipped to handle even the most intricate molds. We've successfully tackled diverse projects, providing precision and efficiency for both simple and highly complex parts.
• High volume production • Parts in 4-8 weeks • Capable of millions of cycles • Unlimited part complexity • Optimized automatic production • Highly competitive pricing
GETTING A QUOTE WITH LK-MOULD IS FREE AND SIMPLE.
FIND MORE OF OUR SERVICES:
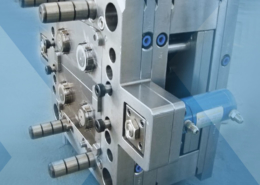
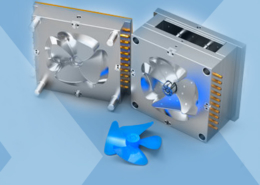
Plastic Molding

Rapid Prototyping
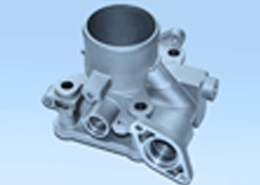
Pressure Die Casting
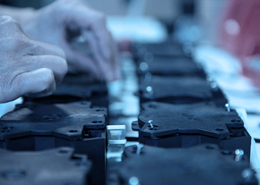
Parts Assembly
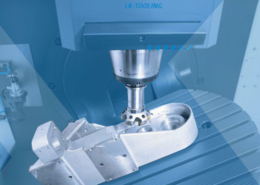