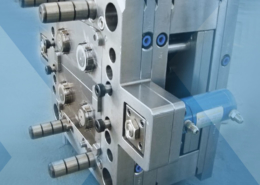
SUSSEX INJECTION MOLDING- Import Customs Data ... - sussex injection molding
Author:gly Date: 2024-10-15
Safety is paramount. HDPE’s vulnerability to high temperatures can be a concern, especially when exposed to flames. But, as with many materials, science offers a remedy. By incorporating flame retardants into the HDPE mold, we can significantly reduce its flammability, ensuring both the safety of the manufacturing process and the end product.
Transitioning from the challenges, let’s delve into the myriad applications of HDPE, showcasing its versatility. But before that, here’s a table juxtaposing the advantages and challenges of HDPE:
While HDPE’s advantages in the manufacturing process are undeniable, it’s essential to address the challenges that come with it.
With a clear understanding of HDPE’s strengths and areas for improvement, we can better appreciate its role in various industries and applications.
The high strength and impact resistance of HDPE are tales of legend in our industry. From rugged playground equipment to durable storage containers, HDPE molding shapes these items with the promise of enduring wear and tear. The words “high strength” and “low cost” often don’t share the same sentence, yet HDPE melds these together harmoniously.
In my years of experience, I’ve found HDPE’s chemical resistance to be quite impressive. The material, with its high density, resists corrosion and withstands many chemicals, making it a favorite for industrial applications. Imagine a knight in shining armor, unperturbed by the surroundings—that’s HDPE for you.
And yet, amidst all its strength, HDPE moulding doesn’t turn a blind eye to our planet. Its recyclability is commendable. From milk jugs to detergent bottles, HDPE parts, once they’ve served their purpose, are reborn in the crucible of recycling. A commitment to the environment, one could say.
Diving into the economic canvas, HDPE injection molding stands out as an excellent choice due to its cost-effectiveness. Manufacturing products in large quantities using HDPE injection molding machines taps into economies of scale. It’s like watching a symphony of efficiency: HDPE plastic molding reduces labor costs while ensuring production efficiency.
The automotive sector, ever-evolving and always on the move, has embraced HDPE molding. Car components, molded with precision, take advantage of HDPE’s impact resistance and low thermal conductivity. This has paved the way for lighter vehicles, translating into improved fuel efficiency. A simple injection molded HDPE part can play a pivotal role in this vast machinery of movement.
In the sprawling landscape of thermoplastic polymers, High Density Polyethylene, or HDPE moulding, stands as a titan. Its molecular architecture—a long chain of carbon atoms bonded to hydrogen—imbues it with properties that have ushered in a revolution across various industries. While discussing chemical compositions might seem like traversing a mundane path, HDPE surprises us with its simplicity and strength. It’s akin to the minimalism in an art masterpiece: unassuming yet profound.
As a seasoned technician, I’ve seen how HDPE molding holds its own against other plastic resins. It emanates high tensile strength and low cost, giving it an edge over its cousins. In the world of injection molding, HDPE resin is like a reliable workhorse—consistent and trustworthy. It molds into an assortment of consumer products, displaying versatility that other plastics could only aspire for.
One of the primary concerns with HDPE parts is their high coefficient of thermal expansion. As the injection molding process inherently generates heat, HDPE tends to expand. This expansion, when followed by cooling, can lead to warping or distortion, compromising the aesthetic integrity of the final product. It’s a dance of heat and shape, where the rhythm can sometimes go awry.
HDPE, though a marvel, isn’t devoid of quirks. Shrinkage and warping are perennial challenges. But with intuition and experience, it’s possible to predict these behaviors. Design modifications and process adjustments can counteract these potential pitfalls, ensuring the end product remains true to its intended form.
Comparing it to its sibling, LDPE, HDPE is denser and possesses higher temperature resistance. From food storage containers to medical applications, HDPE parts have become the backbone of countless products. It’s remarkable how this versatile material effortlessly adapts to the shape of the mold, catering to a wide range of applications.
Designing with foresight, incorporating generous radii and draft angles, can make the ejection process smoother. An elegant curve not only enhances aesthetics but also adds to the structural strength, while draft angles prevent part sticking, ensuring the HDPE parts release effortlessly from the mold cavity.
Looking to kick off your injection mold work? Pick ACO Mold! We’re all about using a bunch of different plastics for injection molding. Think HDPE, ABS, PP, PE—you name it. Got questions? Just hit us up. Our pros at ACO Mold are here to hook you up with everything you need, all in one place!
Designing for HDPE injection molding is an art. The right wall thickness ensures structural integrity without wastage. There’s an old adage among us technicians: “Design is not just what it looks like. Design is how it works.” This rings true, especially when considering how uniform wall thickness can prevent sink marks and voids.
Mastery over the injection molding machine parameters is paramount. Balancing the melt temperature, injection speed, and pressure can make all the difference between an average and an outstanding product. As they say, “The devil is in the details.”
As I ponder the vast expanse of the injection molding world, HDPE emerges as a beacon of promise. Its versatility, coupled with its economic advantages, places it at the forefront of consumer and industrial applications. While challenges persist, the path forward for HDPE moulding is bright, fueled by innovation and an ever-growing demand. The tapestry of the past interwoven with the threads of the future makes HDPE molding an attractive option for generations to come.
HDPE, in its pellet form, can be a magnet for moisture. Before molding, it’s imperative to ensure the resin is dry. Moisture can lead to weak spots, compromising the product’s integrity. I’ve witnessed this firsthand and can’t stress enough the importance of thorough pre-drying.
Too fast, and you risk trapping air; too slow, and you might not fill the mold completely. The dance with the injection molding machine is one of nuance and subtlety, with the right rhythm resulting in impeccable HDPE parts.
The industrial landscape is painted with HDPE’s footprints. From pipe thread protectors to industrial products that demand high strength and chemical resistance, HDPE moulding has found its niche. Reflecting upon the numerous projects I’ve worked on, HDPE’s adaptability to complex geometries and its compatibility with large-scale production never cease to amaze.
HDPE’s low surface energy makes it a bit of a lone wolf, resisting bonding with other materials. This characteristic can pose challenges in processes requiring adhesion, such as overmolding. However, every challenge has its solution. In this case, specialized adhesives designed explicitly for HDPE can bridge the bonding gap, ensuring a firm union between HDPE and other components.
Step into any American household, and you’ll witness HDPE’s ubiquity. From milk crates to food storage containers, this versatile thermoplastic polymer seamlessly blends into our lives. HDPE plastic bottles, often overlooked, are silent testimonies to the material’s wide range of industries and applications.
GETTING A QUOTE WITH LK-MOULD IS FREE AND SIMPLE.
FIND MORE OF OUR SERVICES:
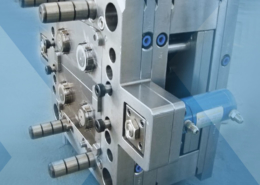
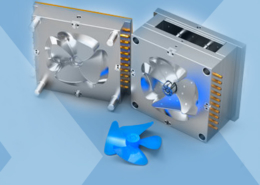
Plastic Molding

Rapid Prototyping
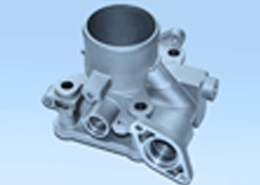
Pressure Die Casting
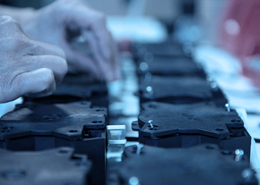
Parts Assembly
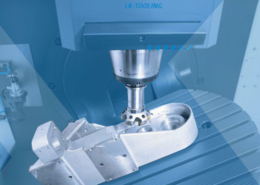