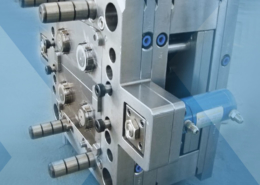
SUSSEX INJECTION MOLDING- Import Customs Data ... - sussex injection molding
Author:gly Date: 2024-10-15
Charles Daniels CFO of Wepco Plastics shares insights on the role of social media in manufacturing, how to improve the “business” side of a small mold shop and continually developing culture.
Steel supplier discusses high thermal conductivity metal powders that also address the skills gaps via user-friendly materials and promote sustainability via durability and higher cycle counts.
Intralox's integration of the Alpha Laser ALFlak has significantly improved their tool room efficiency when it comes to difficult welds and urgent repairs.
Join MoldMaking Technology Editorial Director Christina Fuges as she gets the latest news on this mold builder's use of VR for mold design education.
Smart sensors and sophisticated process and measurement data management are driving intelligent moldmaking to new heights.
Steps to improve data-driven decision-making and key features of a cloud-based system for mold monitoring and asset management.
In addition to manufacturing locations in Canada and Mexico, Integrity operates two other facilities within the United States. One location in Troy, Michigan, which houses a sales and engineering team and has recently added the capability of manufacturing fixtures and gages in addition to 3D printing. The other facility is located in Pulaski, Tennessee, which manufactures and repairs plastic injection molds, offers tooling support to Integrity Injection Molding.
After attending IMTS, it's clear that the integration of advanced technologies is ready to enhance precision, efficiency and automation in mold manufacturing processes. It’s a massive event, so here’s a glimpse of what the MMT team experienced firsthand.
Identify pain points, tackle each one strategically and maintain flexibility to keep your moldmaking business on a path to growth.
The need for data to track information and the history of the mold-building process is ever-increasing, and mold component solutions can help.
Overall, the shift to all-electric injection molding machines represents a significant leap in manufacturing efficiency and precision, aligning with modern demands for high-quality, cost-effective, and environmentally friendly production.
It’s easy to imagine the advantages automation offers the moldmaking process, but it's challenging to change one’s mindset, develop a plan and invest.
When used for conformal cooling in plastic injection, 3D printing opens a wide range of design freedom. This design freedom enables designers to develop highly-efficient thermal regulation networks. However, this blessing also comes at the expense of not only higher manufacturing cost but also higher design cost as the designer could spend weeks to develop optimal cooling channels. This webinar will explore strategies and tools — including SimForm, a front-end thermal simulation app — to help tool designers and tooling managers maximize the benefits of 3D printing while minimizing manufacturing and design costs. Agenda: 3D printing applied to the plastic injection industry 3D printing pros and cons Tools and methods to facilitate the integration of 3D printing
Integrity Mold & Tool, a world class mold manufacturer, has opened its first plastic injection molding facility in the United States, Integrity Injection Molding, Inc. The new molding facility is located at 512 Tarpley Shop Road in Pulaski, Tennessee. The new 35,000 square foot building will begin with 5 presses from Krauss-Maffei and Yizumi, ranging from 500 tons to 1800 tons, with capacity for future growth. Integrity Injection Molding will offer quality systems, tooling support, mold flow analysis, in house tryouts, R&D support, design visibility and logistics services for both automotive and non-automotive customers.
However, it’s essential to weigh these benefits against their higher costs, technical requirements, and certain operational limitations. Understanding the offerings of leading brands, both domestic and international, can further guide decision-makers in choosing the right equipment for their specific production needs.
In all-electric machines, servo motors replace these hydraulic systems. This change brings about notable benefits, including enhanced precision and speed in each action. Additionally, the integration of pressure and temperature sensors facilitates closed-loop control, significantly elevating manufacturing accuracy.
Below is a comparison chart that outlines the main differences between traditional hydraulic injection molding machines and all-electric injection molding machines, focusing on their essential characteristics.
This webinar will provide an overview of new developments in hot runners, controllers, mold components, predesigned molds, process monitoring and mold maintenance equipment. These advancements are designed with the goals of lowering scrap rates, optimizing process temperatures and managing energy consumption. The solutions also aim to support productivity and may contribute to extending the operational lifespan of tooling equipment. Agenda: Innovative undercut and thread-forming components Predesign mold bases and plate control Melt delivery and control solutions Process monitoring and maintenance
Discover how to enhance your mold design process with the right CAD/CAM tool for parting and cavity design. This webinar will explore CAD/CAM capabilities including how hybrid solid/surface modeling can streamline workflow and improve accuracy. Learn how to confidently tackle parting, runoff, and shutoff, ensuring precision and efficiency in your designs. Agenda: Part analysis QuickSplit techniques Parting and runoff strategies Shutoff solutions
Join this webinar where Hexagon will explore how state-of-the-art CAD/CAM technology can drive your business forward. Learn how to optimize tool paths, enhance design accuracy and reduce lead times with advanced simulation. Discover the power of automation and real-time data for continuous improvement. Tailored for mold and die manufacturers, this session offers actionable insights to boost productivity and quality. Don’t miss this opportunity to gain a competitive edge in progressive die manufacturing. Agenda: Key challenges in progressive die manufacturing Optimizing tool paths Enhancing mold and die design accuracy Reducing lead times with simulation Automating processes for greater efficiency Leveraging real-time data for continuous improvement
Steel supplier discusses high thermal conductivity metal powders that also address the skills gaps via user-friendly materials and promote sustainability via durability and higher cycle counts.
Diamond compounds, with their varied grades, colors and base options, provide a comprehensive solution for mold builders in need of precise and superior polishing across diverse materials and applications.
Formnext Chicago is an industrial additive manufacturing expo taking place April 8-10, 2025 at McCormick Place in Chicago, Illinois. Formnext Chicago is the second in a series of Formnext events in the U.S. being produced by Mesago Messe Frankfurt, AMT – The Association For Manufacturing Technology, and Gardner Business Media (our publisher).
In ISO 9001 quality management systems, the Management Representative (MR) plays a crucial role. While the 2015 version of ISO 9001 no longer mandates this position, having a trusted management member serve as an MR remains vital for streamlining operations and maintaining quality standards.
Servo motors make these machines more energy-efficient compared to traditional hydraulic counterparts. They consume energy only when necessary, leading to electricity savings of 40-60%.
Released earlier, this video remains a valuable recruitment tool and is being re-promoted in celebration of Manufacturing Day 2024.
Precise Tooling Solutions, X-Cell Tool and Mold, M&M Tool and Mold, Ameritech Die & Mold, and Cavalier Tool & Manufacturing, sit down for a fast-paced Q&A focused on strategies for improving efficiencies across their operations.
The realm of all-electric injection molding machines is marked by the presence of both prominent domestic and global manufacturers, each bringing their own expertise and innovations to the field.
Understanding these drawbacks is crucial for manufacturers considering an investment in all-electric injection molding machines, ensuring a balanced assessment of their potential in various production environments.
All-electric injection molding machines represent a significant innovation in the field of injection molding, distinguished by their use of electric servo motors to control all operational movements. This is a departure from traditional hydraulic injection molding machines, which rely on hydraulic systems to perform key functions such as mold opening and closing, plastic injection, and product ejection.
MoldMaking Technology addresses the complete lifecycle of the manufacture and maintenance of a mold—from design to first shot—by providing solutions and strategies to moldmaking professionals charged with designing, building and repairing molds. About Us
After attending IMTS, it's clear that the integration of advanced technologies is ready to enhance precision, efficiency and automation in mold manufacturing processes. It’s a massive event, so here’s a glimpse of what the MMT team experienced firsthand.
After attending IMTS, it's clear that the integration of advanced technologies is ready to enhance precision, efficiency and automation in mold manufacturing processes. It’s a massive event, so here’s a glimpse of what the MMT team experienced firsthand.
MoldMaking Technology Editorial Director Christina Fuges sits down with Murphy Forsyth, GM – Injection Molding and Director Of Marketing for Zero Tolerance LLC in Clinton Township, MI.
A connected software solution streamlines the moldmaking process by providing a unified source of design data, enhancing efficiency and reducing errors, with five key steps benefiting from this integration.
Integrity Mold & Tool, a world class mold manufacturer, has opened its first plastic injection molding facility in the United States, Integrity Injection Molding, Inc.
In conclusion, the journey into the world of all-electric injection molding machines reveals a landscape rich in innovation and efficiency. These machines offer a multitude of advantages, including precision, energy efficiency, and environmental friendliness, making them an increasingly popular choice in various manufacturing sectors.
These brands, with their diverse range of all-electric injection molding machines, cater to various industrial needs, emphasizing innovation, efficiency, and precision. Their contributions significantly shape the landscape of modern manufacturing technology.
Integrity Tool & Mold was established in 2000 in Oldcastle, Ontario, Canada. Integrity began as a humble tool shop and has grown to be the global leader in mold manufacturing with over 750 employees from Canada, the United States and Mexico.
Discover how to enhance your mold design process with CAD/CAM software specifically tailored for the moldmaking industry. In part two of this webinar series, Cimatron will demonstrate how to intelligently design mold components, such as slides and lifters, using powerful CAD/CAM tools to accelerate the design process. Additionally, it will cover how to avoid errors and ensure design accuracy for ejector pins by checking clearance distances, calculating cutoff heights correctly, and thoroughly documenting all ejector components. Agenda: Slides Lifters Inserts Ejection pins and charts
Understanding and facing the moldmaking industry’s obstacles to growth requires a strategy focused on increased profitability.
For many individuals, the term “all-electric injection molding machine” might be relatively unknown or perceived as a complex, high-end technology. However, this technology, which originated in the 1980s, experienced significant advancements in the 1990s.
Discover how CAD/CAM functionality tailored for the mold industry can significantly enhance the mold design process. In part three of the webinar series, Cimatron will focus on designing waterlines and cooling components. It will demonstrate how CAD/CAM tools can verify drill line depths for water lines and baffles, ensure that minimum steel requirements are met while placing water lines, and provide a complete list of all baffle cutoff lengths. Additionally, it will explore how to confidently design runners and gates using CAD functionality specifically developed for these aspects of mold design. Agenda: Waterlines and verification Conformal cooling Baffles and charts Runners and gates
Despite their numerous benefits, all-electric injection molding machines also present certain challenges and limitations, including:
These machines are especially beneficial in sectors where high precision and consistent replication are critical, such as in the production of medical devices and precision electronics. Overall, all-electric injection molding machines signify a progressive step in injection molding technology, embodying efficiency, precision, and environmental sustainability.
A water-based, eco-friendly plastic mold cleaning system helps Rankine-Hinman Manufacturing restore flow rates and avoid big-ticket failures on complex and costly molds.
Join MoldMaking Technology Editorial Director Christina Fuges as she gets the latest news on this mold builder's use of VR for mold design education.
As technology continues to evolve, all-electric injection molding machines stand as a testament to the industry’s commitment to progress, precision, and sustainability.
After attending IMTS, it's clear that the integration of advanced technologies is ready to enhance precision, efficiency and automation in mold manufacturing processes. It’s a massive event, so here’s a glimpse of what the MMT team experienced firsthand.
A focus on electrode design and automation helps toolroom improve efficiency, reduce tooling costs and deliver higher quality products.
Engineers use properly preloaded bolts, blocks, springs and side-action cores to enhance functionality and reliability in various mechanical systems.
In ISO 9001 quality management systems, the Management Representative (MR) plays a crucial role. While the 2015 version of ISO 9001 no longer mandates this position, having a trusted management member serve as an MR remains vital for streamlining operations and maintaining quality standards.
Gerardo (Jerry) Miranda III, former global tooling manager for Oakley sunglasses, reshares his complete mold design checklist, an essential part of the product time and cost-to-market process.
It’s essential for users to grasp what these machines are and the appropriate scenarios for their use. This article aims to explain these aspects in an uncomplicated and precise manner.
Explore the standout articles of September, featuring innovations, expert insights, and strategies to boost efficiency and quality for your moldmaking needs.
GETTING A QUOTE WITH LK-MOULD IS FREE AND SIMPLE.
FIND MORE OF OUR SERVICES:
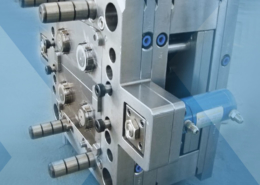
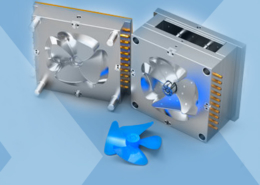
Plastic Molding

Rapid Prototyping
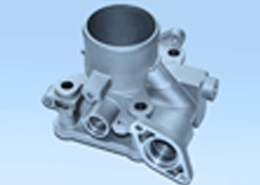
Pressure Die Casting
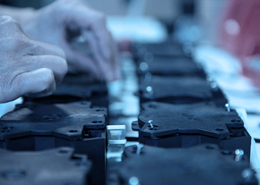
Parts Assembly
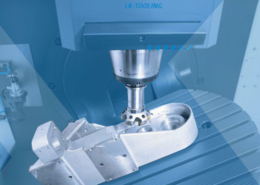