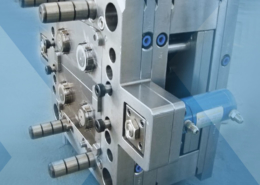
Setting instructions for plasticizing metering - plasticizing injection molding
Author:gly Date: 2024-10-15
Polypropylene (PP) injection molding parts offer good impact resistance, making them suitable for use in applications where mechanical strength and toughness are required. This property allows PP parts to withstand harsh conditions and heavy usage.
Polypropylene is susceptible to degradation when exposed to ultraviolet (UV) light over extended periods. Continuous exposure to sunlight or outdoor conditions can lead to the breakdown of the polymer chains, resulting in a reduction in mechanical properties and overall performance. To counter this disadvantage, UV stabilizers can be added to the polypropylene during the manufacturing process, but this can increase production costs.
For flat or nearly flat and very transparent parts, such as windows or lenses, resin coating is the best option. Because any release agent will display on a part surface, make sure to never use a release agent.
Get machined parts anodized and chromate plated with our quick-turn finishing option. Eligible materials include aluminum 6061/6082 and 7075.
Ultimately, the thermoplastic properties of your parts and the expectations end-users have about your part survivability, will influence your choice of optimal material for transparent plastic. Make sure to validate your choice of materials before proceeding with your project. Proper validation will save you time and money from design through manufacturing.
Acrylic can be injection-molded into crisply clear and colored plastic products, plus it's non-toxic, scratch-proof, and UV-resistant, making it a popular choice for use in outdoor equipment. Acrylic's accommodation and its variety of colorants make it a good choice for lenses, light fixtures, and objects requiring them. On the downside, acrylic can be inflexible and breakable, so it can't be used in products that must withstand a lot of pressure, and it must be dried after it absorbs moisture, possibly slowing the manufacturing process and causing issues for end-users.
Sungplastic is a plastic product manufacturer with rich experience in injection molding. According to the different product development requirements, we flexibly adjust the manufacturing process to achieve high quality, high efficiency and more economical.
We offer a variety of manufacturing services: Rapid Prototyping, Tool Making, Injection Molding, Product Design and Development, CNC Machining and Metal Stamping. You can choose from a variety of plastics, silicone rubber, or metal for your product. Regardless of mass production or small batch customization, Sungplastic has always been committed to providing assured, efficient and more economical one-stop processing services for your projects.
The pressure holding phase allows the molten plastic to fill any remaining voids within the mold cavity, ensuring a complete and well-defined product. By maintaining sufficient pressure during this stage, the risk of voids or incomplete parts is minimized, and the final product’s structural integrity is enhanced.
In plastic design, thick and thin parts are not easily achieved without sacrifice. That doesn't necessarily ring true with OLSR design. You can achieve thick and thin geometries that often can be as thin as 0.010 in. (0.25mm) and as thick as 2 in. (50mm), all within the same part geometry because you don't have issues with material flow, sink, or voids. OLSR is extremely resilient against the transparent molding issue that frequently creates thermoplastic problems, including the ability to create micro details. You also can design in negative draft angles without the need for expensive tooling that would normally require lifters, collapsible cores, and side-actions.
Commonly used in textiles, packaging, and containers, the high flexibility of polypropylene (PP) makes it an ideal choice for waterproof fabric for bags and clothing. It also has high electrical resistance, so it is used in electronics, and its nonreactivity with acids and bases makes it a good container for solvents and other corrosive materials. It even works well as a sort of dynamic hinge on non-loadbearing parts.
Like acrylic, high-density polyethylene (HDPE) is UV-resistant, but it is more easily translucent injection molded. HDPE is less brittle than acrylic, and it's cheaper to produce, but it still breaks under high pressure. These qualities dictate its common use in containers, especially bottles, and pipes. HDPE is formed by applying high heat and pressure to petroleum. These transparent injection molding features, along with being inexpensive, are why it's used in mass production.
Pure Polypropylene, also known as a commodity plastic, is the most common and widely used grade. It exhibits the lowest density among PP grades, making it lightweight and cost-effective. This type of PP is suitable for a wide range of general-purpose applications where mechanical strength and extreme performance requirements are not essential. Its affordability and ease of processing make it popular in various industries, including packaging, consumer goods, household products, and automotive components.
Manual sanding and polishing are best used for simple designs that lack details. Producing a clear product with this finishing method is expensive and time-consuming. The highest finish is SPI-A2, which is often appropriate for prototypes or optical projects with low runs, but if finish isn’t vital when evaluating a prototype, waiting to add it until the production process might save you some money.
So, what are the most popular materials we use to produce clear plastic injection molded parts? Well, first we should say that popularity shouldn’t be the determining factor for your part. One of our application engineers at Protolabs can discuss the best approach, if you’re not sure. Every project is unique, and just because a material is ordered the most often, it doesn’t mean you should use it, too.
One of the challenges with polypropylene injection molding is its resistance to bonding with adhesives and paint. This makes it difficult to apply coatings or adhesives to polypropylene surfaces, reducing the range of finishing options available for products made from this material.
In addition to UV resistance, polyetherimide (PEI) is impervious to intense heat, repeated pressure, and acids, making it appropriate for medical and automotive products. It is also often used as a translucent material in aerospace engine components, temperature sensors, and heat shields. PEI is more expensive because a steel mold must be used in manufacturing.
These two grades of PP offer a wide spectrum of possibilities for manufacturers and designers. While pure polypropylene is favored for its economic viability and versatility in common applications, high crystalline polypropylene is chosen when enhanced mechanical performance and structural integrity are paramount. The availability of various PP grades ensures that polypropylene injection molding industries can select the most suitable material to meet their specific requirements, striking a balance between performance, cost, and design.
PP is a relatively low-cost material, which makes it an attractive option for polypropylene (PP) injection molding manufacturers looking to produce high volumes of parts or products.
Polypropylene (PP) is a widely used thermoplastic polymer that is known for its versatility, durability, and cost-effectiveness.PP is a type of plastic that is derived from propylene, a gas that is produced during the refining of petroleum. It was first developed in the 1950s and quickly became popular due to its excellent properties and relatively low cost. Today, polypropylene injection molding material is one of the most commonly used plastics in the world and is used in a wide range of applications.
Polypropylene (PP) injection molding is a manufacturing process that involves injecting molten polypropylene into a polypropylene mold to create a wide range of plastic parts and products.
The key factors that affect the success of the polypropylene injection molding process include the temperature and pressure used during injection, the design of the mold, and the properties of the PP material being used. By carefully controlling these factors, manufacturers can produce high-quality parts that meet the specific needs and requirements of their customers.
While polypropylene has a high melting point compared to many other plastics, it is not suitable for applications requiring exposure to very high temperatures. Above its melting point, which is typically around 160-170°C (320-338°F), polypropylene will start to soften and lose its structural integrity.
The polypropylene injection molding process is a highly precise and efficient method of manufacturing plastic parts and products.Here are the steps involved in the polypropylene injection molding process:
High Crystalline Polypropylene, commonly referred to as HcPP, is a specialized variant that incorporates glass fibers into the PP matrix. This reinforcement significantly enhances its mechanical properties, making it ideal for applications demanding higher rigidity, strength, and dimensional stability. The addition of glass fibers results in improved tensile strength, flexural strength, and resistance to deformation under load. HcPP is often preferred in engineering applications that require durable and robust components, such as automotive parts, industrial machinery, and structural components.
Proto Labs, Inc. 5540 Pioneer Creek Dr. Maple Plain, MN 55359 United States P: 877-479-3680 F: 763-479-2679 E: [email protected]
The polypropylene injection molding process involves heating the thermoplastic material until it becomes molten and then injecting it into a mold cavity under high pressure. The polypropylene molds are typically made of steel and designed to create the desired shape and structure of the finished product. Once the polymer has cooled and solidified, the mold is opened, and the finished part is ejected.
Although polypropylene performs well at moderate temperatures, it becomes brittle and more susceptible to impact damage in extremely cold conditions. This limitation may affect its suitability for applications in freezing environments or industries that require materials with excellent low-temperature properties.
Polypropylene has a low friction coefficient, making it suitable for applications that require reduced friction between moving parts. This property is advantageous in mechanical and engineering components, reducing wear and energy consumption.
While polypropylene exhibits good chemical resistance to many common substances, it is vulnerable to certain aggressive chemicals, such as strong acids and bases. In environments where exposure to harsh chemicals is a concern, alternative materials may be more suitable.
Tough Black (Loctite Henkel 3843) and Ceramic-Filled (BASF 3280) are two new advanced photopolymer materials now available for 3D printing.
The versatility and range of properties of PP make it a popular choice for a wide range of applications across many industries.Here are some of the applications of polypropylene injection molding:
Remember that uneven cooling can cause problems, including surface defects and deterioration. Check out the website for many great design tips that will help you with transparent injection molding or clear plastic injection molding.
PP exhibits resistance to fatigue, meaning it can endure repeated load cycles without failure. This property is valuable in applications where parts undergo frequent or continuous stress, such as in mechanical components.
Polypropylene maintains its shape and dimensional stability even after prolonged use, temperature fluctuations, or exposure to environmental factors. This ensures the accuracy and consistency of parts over time.
Polypropylene injection molding is a highly efficient and precise process that allows for the production of complex parts with high accuracy and consistency. It is used in a wide range of industries, including automotive, packaging, consumer goods, and medical devices.
There are plenty of design tips on the Protolabs website for clear or translucent parts. Here are a few design reminders to wet your whistle.
Our digital factories create prototypes and low-volume parts fast, while our manufacturing network, offers advanced capabilities and volume pricing.
Polypropylene is relatively easy to machine, which simplifies the manufacturing process and reduces production costs. It allows for efficient and precise machining of complex shapes and designs.
In daily life, raw material of we commonly used food environmental protection bag and shell of the electronic products is polypropylene injection molding material. However, not many people know all about polypropylene injection molding material and polypropylene injection molding process. Polypropylene(PP) ranks as the second most commonly used plastic in the globe, known for its widespread applicability and advantageous properties. As an polypropylene molding material, PP offers good chemical resistance, shape retention after torsion or bending, a high melting point, and remarkable resistance to moisture and water exposure. Additionally, being recyclable further enhances its appeal in sustainable practices. At Sungplastic, a polypropylene(PP) injection molding manufacturer, you can know more about PP and achieve your polypropylene(PP) injection molding projects.
PP exhibits excellent weldability, allowing for easy joining of different components through various welding methods like ultrasonic welding, hot plate welding, and solvent bonding. This facilitates the assembly process and ensures strong and reliable connections.
To regulate the mold temperature and prevent any irregularities during the cooling process, a mold temperature controller is utilized. This controller injects water or oil into the cooling system, helping to maintain the mold’s temperature within the specified range. By carefully controlling the cooling process, the risk of warping, distortion, or defects in the finished product is reduced, leading to consistent and high-quality parts.
Polypropylene is highly flammable and can ignite easily. When subjected to high temperatures, such as above 100°C (212°F), it can dissolve into harmful aromatic hydrocarbons like benzene and toluene. This flammability limits its suitability for certain applications, especially those involving high-temperature environments or near potential ignition sources.
When searching for the best choice of polypropylene (PP) injection molding manufacturer, several critical factors should be considered to ensure a successful and satisfactory partnership. PP injection molding is a widely used manufacturing process, and Sungplatic can make a significant difference in the quality, cost-effectiveness, and overall success of your product development.
Different materials have different advantages in clear plastic injection molding. Here’s a rundown of the qualities of our clear plastics.
Polypropylene, a versatile thermoplastic material, is available in various grades to cater to specific application needs. There are two significant types of PP grades.
More expensive than acrylic or HDPE, polycarbonate is an alternative to clear plastic injection molding. It’s as transparent and UV-resistant as acrylic but less prone to damage from extreme temperatures. Polycarbonate's high impact resistance makes it a good choice for products that maintain safety, such as windows, containers, helmets, and safety goggles. However, like acrylic, it must be dried after it absorbs moisture before injection molding can occur.
Also, because clear plastics don’t hide impurities created during the molding process, material storage must ensure the material stays clean.
PP is a lightweight material, which makes it ideal for use in products where weight is a concern, such as automotive parts and packaging.
Our helpful design aid demonstrates part features that are too thin or too thick, bad bosses, right and wrong ribs, and other considerations to be mindful of while designing parts for injection molding.
Plastic Mold Manufacturing Plastic Injection MoldingRapid PrototypingCNC MachiningSheet Metal StampingPressure Die CastingSilicone & Rubber PartsSurface Finishing
Manufacturing clear molded parts adds all sorts of considerations to your designs and how we make your parts. The ideal materials for a project are determined by a material’s qualities and its behavior during both manufacturing and the end-user experience. Because transparent injection molding hides nothing, more finesse in design and manufacturing is required than when molding materials that can obscure a less-than-flawless design. The planning and preparation of raw materials, equipment, tooling, and molding processes must be precise.
Still another advantage is the non-yellowing factor. Thermoplastics without additives are not UV-resistant, meaning the parts could yellow and degrade due to prolonged exposure to light and sunlight. OLSR is non-yellowing, so it's excellent for outdoor fixtures exposed to harsh environments.
OLSR is an advanced material that has many properties that make it a preferred material choice over polycarbonate (PC) or acrylic (PMMA) for lighting and clear optical parts. All materials reduce the amount of light flowing through them. When your product requires a clear PC or PMMA part, you can improve light transmission using OLSR, which allows up to 94% light transmission.
It is essential to carefully evaluate these disadvantages of polypropylene injection molding when choosing the right material for specific applications. While polypropylene offers many advantages, such as good chemical resistance, lightweight properties, and affordability, its limitations may make it unsuitable for certain demanding or specialized applications.
Polypropylene (PP) injection molding is a versatile process that can be used to create a wide variety of complex shapes and structures. It can be used in a range of industries, from automotive to medical devices.
Polypropylene has a high flexural strength, meaning it can endure bending or torsional stresses without fracturing or deforming. This makes it ideal for applications where components need to maintain their shape under load.
GETTING A QUOTE WITH LK-MOULD IS FREE AND SIMPLE.
FIND MORE OF OUR SERVICES:
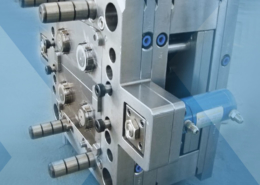
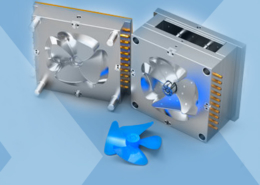
Plastic Molding

Rapid Prototyping
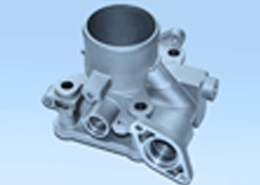
Pressure Die Casting
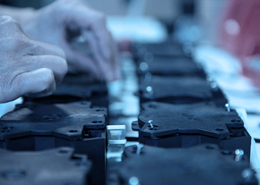
Parts Assembly
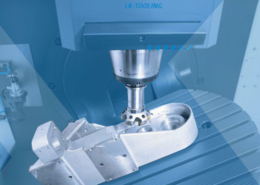