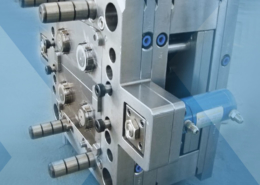
Servo-hydraulic injection molding machines have ... - KAIMING - ppe for injectio
Author:gly Date: 2024-10-15
For the past several decades, 3D printing has become synonymous with rapid prototyping and increased its notoriety as a viable manufacturing alternative. Improvements to printing processes, sintering, finishing, and materials have opened doors to new opportunities that were previously thought to be impossible. For example, the ability to 3D print injection mold tools for short-run prototyping and production projects. This relatively new application is beginning to gain momentum for product developers, tool makers, and contract manufacturers due to several unique advantages.
Using a 6 x 4 x 2 model, we can establish a cost analysis for prototype injection mold tooling that compares Fortify, rapid prototyping, and conventional aluminum processes. While it’s important to note that an aluminum mold will last for 1 – 10,000 parts, 3DP tools are much less expensive and provide more flexibility when it comes to design changes or part complexity. For example, injection molded parts with sharp corners, thin ribs, or undercut features will generally be more expensive because it requires a secondary process called EDM machining. Complexity comes free with Fortify, and is nowhere near as costly or problematic.
Historically, 3D-printed tools were considered a gimmick and unqualified due to a lack of material capabilities. They were brittle and unable to withstand the high temperatures of molding, leaving many engineers without a viable alternative. That is until Fortify presented a technology that is flexible, inexpensive, and strong enough to mold parts in end-use materials. Ceramic fiber-reinforced materials are revolutionary for the prototype injection mold market that enables a true bridge-to-production tool that will save engineers time and money, without sacrificing quality.
Prototype injection molding is a bridge-to-production method that minimizes risks and improves product validation well before mass manufacturing. The use of injection molding to prototype is beneficial for several reasons.
However, Fortify offers a unique path toward a much faster and more flexible solution. The Gantt chart below shows a traditional 3-phase injection molding process. Presuming that the product development (Phase one) takes approximately three weeks, we can determine the next steps in the process by comparing aluminum vs. Fortify molds.
We consistently manufacture precision injection molded products with the highest degree of quality, compliant with ISO 9000 standards and complete customer satisfaction.
Prototype injection mold tools can be created with a variety of different technologies. As previously presented, it’s possible to use hard tooling, aluminum, or 3D printing depending on resources and availability. To put it into perspective, a normal mold order for a complex part that requires threads, texturing, or undercuts could take approximately 5-8 weeks with an aluminum tool. That’s assuming that there are no alterations or changes within that time to further delay the process.
The bottom line is the bottom line. Cost and time savings have been referenced several times throughout this guide, and it’s important to address them directly. 3D-printed IM tools are perfect for the low-volume production of prototypes or end-use parts. For any application, it’s important to determine what exactly is low volume and how it pertains to your particular product. This is not easy, so we recommend speaking with an expert to determine what makes the most sense for your application and process.
Since 1996, Molding Solutions has consistently produced top quality injection molded products for our customers. Our customers come to us for aerosol caps & closures, beauty caps & closures, electronics, medical, safety, and a host of other industry needs.
Chart comparing Fortify’s tooling costs and turnaround time to 3D printing, steel tooling, and aluminum tooling prototyping methods.
Molding Solutions has a solid record of servicing customers with top quality injection molded products. Regardless of the issue, whether it be aesthetic, mechanical, or simply supply, we have provided solutions in the aerosol caps and closures markets, electronics, medical, sporting goods and a host of other industries.
If you have a new project requiring new tooling, or are interested in transferring your existing tooling for evaluation, please give us a call or e-mail and we’ll be happy to discuss several options.
For these services, we work with our customers to fully understand their products requirements in order to provide a fully functional product that meets or exceeds their quality standards. 100% validation can be provided with these services.
Inventors welcome! We have the ability to take your product idea from design, model making (3D print) and intoproduction.
At the core of our operation is the ability to provide the experience and expertise from initial design to complete production, assembly, and decorating of a vast array of injection molded products. Bring us your issue and we will engineer a cost-effective solution.
The table above compares several methods of producing multiple prototypes or low-volume production. As you can see, rapid prototyping of multiple parts starts to get relatively expensive as the quantity increases, but is still nowhere near the cost of an aluminum tool for less than 100 parts. However, the Fortify IM tool is significantly less expensive and just as capable to mold parts with the appropriate end-use materials. In fact, an engineering team can redesign a prototype injection mold tool with Fortify over 15 times for the same cost as a singular aluminum mold.
Learn more about how Fortify’s mold tooling significantly reduces tooling costs during the new product development process by downloading our free whitepaper
See how Fortify helped Cogmedix, a MedTech OEM, cut weeks off each design cycle using 3D printing and rapid injection molding technologies.
Let’s face it, no one designs or prototypes the perfect part right off the bat. What’s more problematic to your new product development (NPD) lifecycle—wasted time or wasted money? The real answer is both. Therefore, adopting a prototype injection molding process will provide real answers to production problems that typically occur late in the game. Thus eliminating costly redesigns or worse, production mishaps.
Product development relies on internal and external feedback to make improvements. Having access to a small batch of product parts with prototype IM tooling enables beta customers and remote engineering teams immediate access to the product. This is ideal to enhance customer relationships or international organizations with multiple facilities. No delays or hold-ups due to part scarcity.
Prototype IM tooling is a cost-efficient way for engineers to shoot end-use materials for true product testing and evaluation. For example, 3D printed mold tools that are reinforced with ceramic fiber and are strong enough to be injected with a variety of thermoplastics that include polycarbonate, nylon 66, ABS and POM, Ultem, GF Ultem, and more. Now, the engineering team can produce 20+ prototypes that are representative of the final product ready to be tested and processed.
Molding Solutions stands behind every mold we build and in turn run in our facility. Our philosophy is to design and build an injection mold that will not only deliver quality parts the first time but will continue to do so over millions of cycles.
Those familiar with conventional injection molding (IM) for production purposes are well aware of the inherent benefits associated. An aluminum tool can produce thousands of parts, and steel tools remain the most efficient mass-production method available today. However, the process doesn’t always yield the best results, and tooling mistakes can become economically problematic very quickly. Prototype injection molding with 3D printed tools has become a viable bridge-to-production tool and may be worth considering.
Notice that the first shots with Fortify IM tools are delivered early in Phase 2 while aluminum tooling takes much longer, resulting in parts being shipped at the beginning of Phase 3 (~two weeks later). Assuming you require a single iteration, Fortify can produce parts immediately and have them available in as little as three days. The design finishes on Monday, printing begins overnight then cleaning and curing on Tuesday. On Wednesday, the molds/inserts are coated and the parts are ready in a few hours. Second iteration? Third iteration? No problem, we repeat the process with an identical timeframe.
Prototype injection mold tooling with 3D printing is uniquely advantageous to designers and engineers because it is an inexpensive and fast way to make mistakes. Hard or aluminum tooling is costly and very difficult to alter once the mold has been delivered, making it a logistical and financial nightmare. The data below shows how significant the cost difference is when comparing multiple prototype methods. Not to mention, a dramatic decrease in the product development timeline.
Many of our customers have been Molding Solutions customers from the beginning as we continually provide superior support and products.
If you’d like to learn more about how you can maximize prototype injection molding with Fortify, get in touch with our experts.
Inject a variety of thermoplastics that include polycarbonate, nylon 66, ABS, and POM from a Fortify mold that is ~90% cheaper than aluminum. The conventional IM tooling process can take up to eight weeks to get parts delivered, imagine having those same parts within days. Fail fast and fail often by quickly redesigning prototype IM tools and testing parts immediately, getting to market faster than ever before.
GETTING A QUOTE WITH LK-MOULD IS FREE AND SIMPLE.
FIND MORE OF OUR SERVICES:
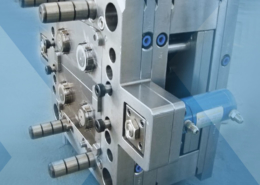
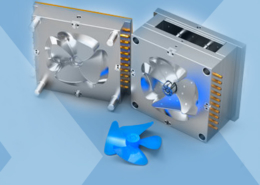
Plastic Molding

Rapid Prototyping
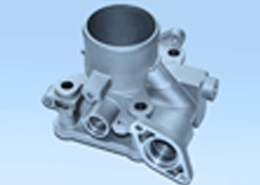
Pressure Die Casting
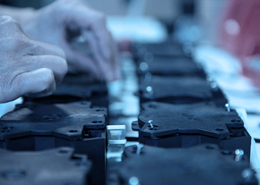
Parts Assembly
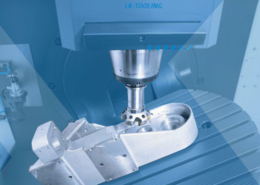