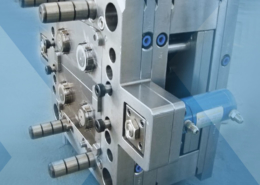
Thermoplastic Injection Molding: Revolutionizing Manufacturing
Author:gly Date: 2024-06-08
Thermoplastic injection molding stands as a pinnacle of modern manufacturing techniques, revolutionizing the way products are designed, produced, and distributed. This process involves injecting molten thermoplastic material into a mold cavity, where it solidifies to form the desired shape. Its versatility, precision, and efficiency make it indispensable across various industries, from automotive to electronics. Understanding its intricacies and potential is crucial for grasping its impact on contemporary manufacturing landscapes.
Introduction: Unveiling the Essence
The Genesis
The roots of thermoplastic injection molding can be traced back to the mid-19th century, marked by the invention of the first injection molding machine by John Wesley Hyatt in 1872. Initially utilized for manufacturing simple products like buttons and combs, the process gradually evolved, driven by advancements in materials science, machinery, and automation.
The Mechanics
At its core, thermoplastic injection molding entails a meticulously orchestrated dance between temperature, pressure, and precision. A thermoplastic resin is heated to its melting point and injected into a mold under high pressure, where it cools and solidifies. The mold then opens, revealing the finished product, ready for assembly or distribution.
The Advantages
The allure of thermoplastic injection molding lies in its myriad advantages. Firstly, it enables the production of complex geometries with high precision, facilitating intricate designs and functional components. Secondly, it boasts rapid production cycles, significantly reducing time-to-market for new products. Additionally, its scalability and repeatability ensure consistent quality across large production runs.
Exploring the Depths
Material Selection
The choice of thermoplastic material plays a pivotal role in the success of injection molding projects. Factors such as strength, flexibility, durability, and chemical resistance must be carefully considered to ensure optimal performance and longevity of the final product. Common thermoplastics used include polyethylene, polypropylene, polycarbonate, and ABS.
Design Considerations
Designing for thermoplastic injection molding demands a holistic approach that balances aesthetics, functionality, and manufacturability. Features like draft angles, uniform wall thickness, and ribbing are essential for facilitating ejection, reducing warpage, and enhancing structural integrity. Employing advanced CAD software and leveraging prototyping techniques streamline the design iteration process, minimizing costly errors.
Process Optimization
Achieving maximum efficiency and quality in thermoplastic injection molding hinges on meticulous process optimization. Fine-tuning parameters such as temperature, pressure, injection speed, and cooling time is paramount for minimizing defects like sink marks, voids, and flash. Moreover, implementing advanced technologies like computer-aided engineering (CAE) and real-time monitoring systems enhances process control and traceability.
Conclusions: Embracing the Future
In conclusion, thermoplastic injection molding stands as a cornerstone of modern manufacturing, driving innovation and efficiency across industries. Its ability to translate intricate designs into tangible products with unparalleled precision and speed has reshaped the global marketplace. As technology continues to advance, embracing emerging trends like additive manufacturing and industry 4.0 integration will further propel the evolution of thermoplastic injection molding, ushering in a new era of possibilities.
In light of this, continued research and development efforts are imperative to unlock the full potential of thermoplastic injection molding, paving the way for sustainable practices, enhanced product performance, and novel applications. By fostering collaboration between industry stakeholders, academia, and policymakers, we can harness the transformative power of this transformative manufacturing process, shaping a brighter, more resilient future for generations to come.
GETTING A QUOTE WITH LK-MOULD IS FREE AND SIMPLE.
FIND MORE OF OUR SERVICES:
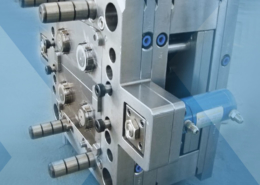
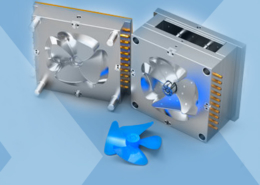
Plastic Molding

Rapid Prototyping
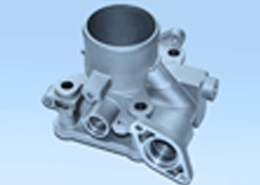
Pressure Die Casting
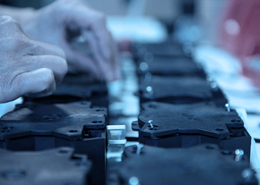
Parts Assembly
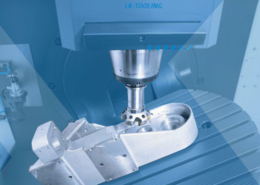