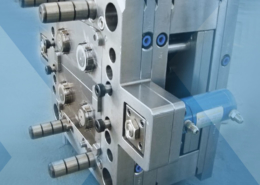
Exploring the World of Teflon Injection Molding
Author:gly Date: 2024-06-08
Teflon injection molding stands as a pinnacle of precision and performance in the realm of polymer processing. With its exceptional chemical resistance, low friction coefficient, and high temperature stability, Teflon (polytetrafluoroethylene or PTFE) has garnered immense interest across industries ranging from automotive to medical. In this comprehensive exploration, we delve into the intricacies of Teflon injection molding, uncovering its techniques, applications, advantages, and future prospects.
Understanding Teflon Injection Molding
Teflon injection molding is a specialized manufacturing process that involves injecting molten Teflon resin into a mold cavity under high pressure and temperature. This process allows for the production of complex parts with tight tolerances and exceptional surface finish. Unlike conventional thermoplastics, Teflon exhibits unique properties, such as non-stickiness, chemical inertness, and thermal stability, making it well-suited for demanding applications.
Properties of Teflon
Teflon, a fluoropolymer renowned for its remarkable properties, boasts a low coefficient of friction, excellent dielectric strength, and broad chemical resistance. These inherent characteristics make Teflon an ideal choice for applications requiring superior performance in harsh environments, such as chemical processing, food processing, and semiconductor manufacturing.
Low Friction Coefficient
One of the key attributes of Teflon is its exceptionally low coefficient of friction, which ranks among the lowest of any solid material. This property enables Teflon components to reduce frictional losses, enhance wear resistance, and improve operational efficiency in various mechanical systems.
Chemical Inertness
Teflon exhibits unparalleled resistance to chemicals, including acids, bases, solvents, and corrosive agents. This chemical inertness ensures the integrity and longevity of Teflon components in aggressive environments, where conventional materials would degrade or fail.
Thermal Stability
With a high melting point and exceptional thermal stability, Teflon retains its mechanical properties over a wide temperature range, from cryogenic temperatures to elevated temperatures exceeding 260°C (500°F). This thermal resilience makes Teflon suitable for applications exposed to extreme heat or rapid temperature fluctuations.
Techniques of Teflon Injection Molding
Teflon injection molding encompasses several techniques tailored to meet the diverse requirements of different industries and applications. From conventional compression molding to advanced multi-shot molding, each technique offers unique advantages in terms of cost-effectiveness, production efficiency, and part complexity.
Conventional Compression Molding
Compression molding is a traditional technique wherein Teflon powder or preforms are placed into a heated mold cavity and compressed under high pressure until cured. While this method is suitable for simple geometries and low-volume production, it may result in longer cycle times and limited design flexibility compared to injection molding.
Advanced Injection Molding
Injection molding of Teflon involves melting granular or powdered resin and injecting it into a cooled mold cavity under high pressure. This method enables the production of intricate parts with precise dimensions and excellent surface finish, making it ideal for high-volume manufacturing in automotive, aerospace, and electronics industries.
Multi-Shot Molding
Multi-shot molding, also known as overmolding, involves injecting multiple materials or colors into a single mold cavity to produce complex Teflon components with integrated features. This technique enhances product functionality, aesthetics, and assembly efficiency, opening up new possibilities for design innovation and customization.
Applications of Teflon Injection Molding
Teflon injection molding finds diverse applications across industries where exceptional performance, reliability, and longevity are paramount. From seals and gaskets in automotive engines to insulators and bearings in electronic devices, Teflon components play a critical role in enhancing product performance and durability.
Automotive Industry
In the automotive sector, Teflon injection molded parts are used in engine seals, gaskets, bearings, and wear components to withstand high temperatures, chemical exposure, and mechanical stress. These components contribute to the overall efficiency, reliability, and longevity of automotive systems, reducing maintenance costs and downtime.
Electronics and Semiconductor Manufacturing
Teflon injection molded parts serve as insulators, connectors, and seals in electronic and semiconductor applications, where reliability, precision, and purity are paramount. These components provide exceptional electrical insulation, thermal management, and chemical resistance, ensuring the integrity and performance of sensitive electronic devices.
Medical and Pharmaceutical Applications
In the medical and pharmaceutical industries, Teflon injection molded parts are utilized in surgical instruments, fluid handling systems, and drug delivery devices due to their biocompatibility, chemical inertness, and sterilizability. These components offer superior performance in demanding medical environments, where cleanliness, reliability, and patient safety are critical.
Advantages of Teflon Injection Molding
Teflon injection molding offers numerous advantages over conventional manufacturing processes, making it the preferred choice for many applications requiring high performance and reliability.
Exceptional Performance
Teflon injection molded parts exhibit exceptional performance in terms of wear resistance, chemical inertness, and thermal stability, surpassing traditional materials such as metals, ceramics, and other polymers. This superior performance ensures the longevity and reliability of Teflon components in demanding applications.
Design Flexibility
The versatility of Teflon injection molding allows for the production of complex shapes, intricate geometries, and integrated features that are difficult to achieve with other materials. This design flexibility enables engineers to optimize product performance, functionality, and aesthetics while reducing overall weight and assembly complexity.
Cost-effectiveness
Despite the initial tooling and setup costs, Teflon injection molding offers long-term cost savings due to its high production efficiency, minimal material waste, and low maintenance requirements. Moreover, the durability and longevity of Teflon components result in reduced replacement and downtime costs over their operational lifespan.
Challenges and Future Directions
While Teflon injection molding has revolutionized the manufacturing industry, it is not without its challenges and opportunities for improvement. Issues such as material handling, mold design, surface finish, and environmental impact continue to drive research and development efforts aimed at enhancing process efficiency, sustainability, and scalability.
In conclusion, Teflon injection molding stands as a cornerstone of modern manufacturing, offering unparalleled performance, reliability, and versatility across a myriad of applications. By understanding its techniques, properties, applications, and challenges, we can unlock the full potential of Teflon materials and pave the way for future advancements in polymer processing technology.
GETTING A QUOTE WITH LK-MOULD IS FREE AND SIMPLE.
FIND MORE OF OUR SERVICES:
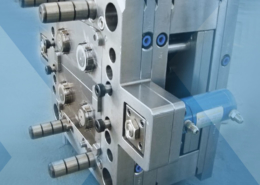
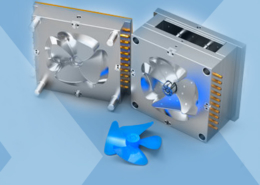
Plastic Molding

Rapid Prototyping
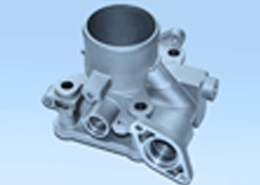
Pressure Die Casting
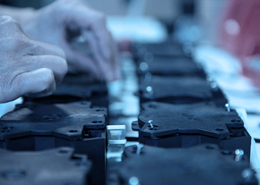
Parts Assembly
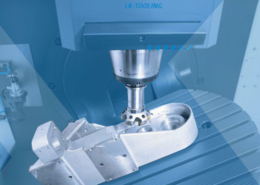