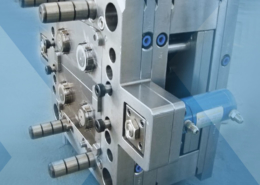
Routsis injection molding_reference | PDF - routsis injection molding
Author:gly Date: 2024-10-15
Mold Temperature: 120-200°F (49-93°C), highly filled grades require 180-200°F (82-93°C) to obtain the best overall surface appearance, higher temperatures will increase crystallinity.
High-density polyethylene injection molding results in products that are less flexible and stronger than products produced by injection molded lower-density polyethylene. With the fewest crystalline branches in its makeup, HDPE is defined with a density range of .941 to .960 g/cc. Although it has greater impact resistance, HDPE can sometimes be used in place of polypropylene, another commonly produced plastic found in commodity products.
While this material is a popular choice, under certain conditions, polyethylene can warp and suffer environmental stress fractures.
Within the broad industry of consumer goods, plastic injection molded polyethylene applications using grades from high density to low are found in many products, including:
The characteristics of plastic injection molded polyethylene differ by the grade selected with HDPE having the greatest strength and rigidity and LDPE showing the most softness and flexibility. Polyethylene is:
Use the search tools on our product listing page to find, view, and download technical data sheets for our plastic materials.
Regrind Level: typically no more than 25% is recommended, with higher levels possible for unfilled grades depending on the end use requirements. Make certain regrind is properly dried to virgin moisture levels.
Polyethylene plastic is the common choice for high-volume, low-cost injection molded applications. It can also be overmolded onto tubing for surface smoothness or roughness. Polyethylene is also used to produce sheeting for food wraps and plastic film. Interested in using this material for your project? Request a quote to get pricing.
At the other end of the polyethylene spectrum, LDPE has many crystalline branches in its composition for an end product that is softer, more flexible and less brittle than the polyethylene materials with higher density ranges. LDPE and LLDPE are often used for lower temperature injection molding applications and will not withstand the high temperatures tolerated by HDPE.
Nylene's high-performance nylon 6 fibers excel in various applications such as indoor/outdoor carpeting and synthetic turf.
Nylene offers extrusion grades with a wide viscosity range, suited for diverse applications like food packaging film, tubing, and profiles.
Melt Temperature: Nylene PA6 melts at 428°F, (220°C) actual melt temperatures of 440-560°F (227-293°C) are permissible, depending on residence time and shot size.
Nylene USA and Nylene Canada ULC are subsidiaries of the Polymeric Resources Corporation (PRC). Nylene companies develop and manufacture specialty nylons and engineering thermoplastics.
With over 40 years in the automotive market, Nylene provides lightweight, durable, and eco-friendly solutions for vehicle engineering.
Engineered resins for diverse molding processes, including injection molding, blow molding, extrusion, and rotational molding.
Nylene UL recognized materials offer superior performance in solar technology, automotive, domestic, and power cable insulation.
As a group, polyethylene plastic is the most widely-used plastic in consumer goods. The range of polyethylene plastic materials is defined by density produced by crystalline branching within the material composition. The material grades include high-density polyethylene (HDPE), medium-density polyethylene plastic (MDPE) and low-density polyethylene (LDPE). Within the low-density polyethylene family, linear low-density polyethylene (LLDPE) is stronger and less flexible than LDPE.
Drying Temperature: 150-180°F (66-82°C)for 2-4 hours, Nylene® PA6 should be dried to less then 0.20% moisture for optimum performance. Drying longer than 4 hours or at higher temperatures may cause discoloration of the polymer or adversely affect important physical properties.
Nylene offers products that are long-lasting and durable and resist damage from chemicals, weathering, and other physical forces.
GETTING A QUOTE WITH LK-MOULD IS FREE AND SIMPLE.
FIND MORE OF OUR SERVICES:
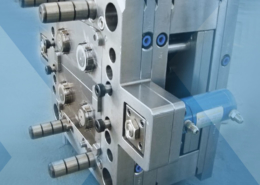
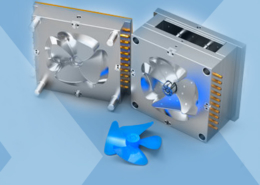
Plastic Molding

Rapid Prototyping
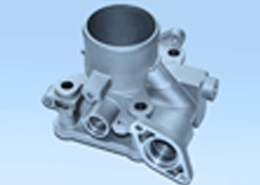
Pressure Die Casting
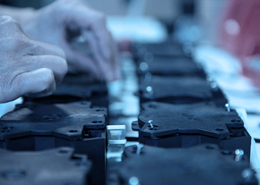
Parts Assembly
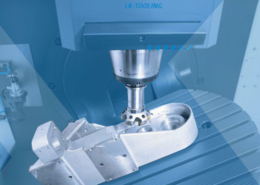