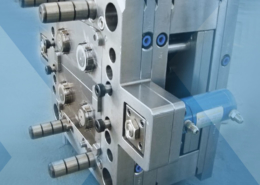
Rotomolding - Rotational Molding - NW Plastics, BC, Canada ... - plastics rotati
Author:gly Date: 2024-10-15
Injection molding is a very common way to form plastic parts and components. Depending on the material, the parts can be very strict with their tolerances as well as easy to process. Injection molding is one of the most common types of forming plastics. It is used in a variety of industries and not just for medical injection molding. In fact, you probably have a wide variety of injection molded parts all around you and simply don't know it. Your basic pens, your keyboard, and even your phone have injection molded components in them.
We provide assistance throughout each stage of your program, from design recommendation through mold tooling fabrication, prototyping, first article approval, process validation, full scale production medical molding, and transfer of turnkey system to customer facilities if requested.
The process is capable of making FDA approved medical devices that are both durable and reliable. This type of molding can also be used to make prototypes to send and get the much-needed FDA approval. Medical injection molding can be performed in a clean room and the components can be sterilized without harm as well. Let's take a look at injection molding.
FORESHOT is a renowned leader in the field of plastic injection molding and electronics manufacturing, specializing in producing a diverse range of high-quality finished goods, including advanced medical devices, sophisticated electronic components, durable automotive parts, and cutting-edge consumer electronics. Leveraging state-of-the-art manufacturing technologies such as RHCM, Double-Shot Injection Molding, and SMT, FORESHOT commits to delivering excellence and innovation in every product, from intricate medical appliances and robust vehicle accessories to the latest in communications and computing technologies.
Located in Taiwan since 1985, FORESHOT Industrial Corporation has over 30 years of industry experience, integrating OEM/ODM services and continuously developing new technologies. Their expertise covers a wide range of manufacturing techniques, including Double-Shot Injection Molding, micro injection molding, thin wall injection molding, and double shot injection molding. They serve various industries including computer, communications, consumer electronics, and medical devices.
RHCM (Rapid Heat Cycle Molding) is not only vanish the weld line of the surface, but also lighten up the rate of gloss and higher mold replication. RHCM technology application like plastic parts in Network Communication equipments and Computers / Communications / Consumer electronics.
Top ability of R&D team and mold design to efficiently complete any type of shape or surface. In addition, we can provide product development and complete solutions to mass production, which...
In order to provide high-quality products that satisfy customers, we have designed and developed a robotic intelligent production line dedicated to our customers' products.
Once these new devices are produced, we assist our customers in transitioning the project into the production phase. Quality and customer satisfaction are our primary goals, and Aberdeen can work with both high and low quantity requirements with over 700 square feet of cleanroom injection molding space.
Then the plastic injection molding machine rotates the first set of molds to the position of the second set of nozzles, and then closes the mold with the fixed side of the second set of molds, and the second set of molds rotates to the position of the first set of nozzles.
However, there are other types of plastics called thermosets that also can be used for injection molding, but the process is far different. These materials are most likely not going to be used for medical molding as they cannot be recycled as easily as the thermoplastic materials. Because of this, you don't see thermosets used as often as you do thermoplastics. A good example of a thermoset is your car tires. This is where they cannot be melted down and reshaped into something.
FORESHOT has been offering customers high-quality plastic injection molding and electronics manufacturing services since 1985, both with advanced technology and 33 years of experience, FORESHOT ensures each customer's demands are met.
FORESHOT is using precise molds and advanced V-Line injection machine to produce and control each item in micro level. Precision Injection Molding is applied in Vehicle Accessories, Medical Appliances and Accessories, cameras, gears inside of CD player or printer, earphone components and LED etc which are required highly precise standard.
Aberdeen’s primary goal is total customer satisfaction for even your most challenging projects. Our company culture is one of honor, respect and service with the highest degree of competence and professionalism that you will find anywhere.
Medical injection molding is a core technology of Aberdeen Technologies and represents a cutting edge solution to the manufacturing needs of healthcare companies who produce medical molded devices. As an insert molding manufacturer, we provide assistance to device manufacturers who approach us with new product concepts and ask us to mold parts for clinical trials and marketing evaluations.
Double-Shot Injection Molding uses plastic polymers to mold plastic parts with multiple colors, materials or components with complex designs in one mold and machine. Double-Shot injection molding allows versatility, is simpler and more cost effective in comparison to other processes.Double-Shot Injection Molding requires attention that strengthen of joint is one of critical issue to be considered.FORESHOT could use this technology to shorten the cycle time, assembly cost, human resource and turnover rate.Double-Shot Injection Molding apply in keyboard、Computer / Communication / Consumer Electronics、Electronic Components、Precision Components and Vehicle Accessories etc. FORESHOT UL safety standards Double-Shot Injection Molding, Dual-Injection Molding, Two-Shot Molding, 2K Injection Molding manufacturing technologies from Taiwan since 1985. FORESHOT covers a wide range of manufacturing techniques, including Micro Injection Molding, Thin-wall Parts Injection Molding, and Double-Shot Injection Molding. These services are tailored to meet the needs of diverse applications in sectors like Medical Appliances, Optical Components, and Vehicle Accessories. Their innovative approach and advanced technology in areas like RHCM and LSR/LSM Injection Molding position them as a leader in the field, capable of handling complex and precision-based requirements in plastic injection molding.
FORESHOT founded in 1985 has more than 30 years in plastic injection industry. In order to give customers more comprehensive service, FORESHOT integration of OEM / ODM and continue develop...
Over the past few years, the demands for plastic injection products have seen considerable increase in consumer electronics products, transportation applications, medical supplies, etc. With the advanced development of precision machine and fast progress of plastic injection technique, progressing from general injection mold to micro injection mold manufacturing, the standards of precision and quality for the completed products of small Precision Components、Electronic Components、Computer / Communication / Consumer Electronics and Vehicle Accessories etc..FORESHOT is dedicated to the development of precision plastic technique and processing, improvement of precision mold, and advancement of plastic object measurement technique, to provide its clients the products with high added value and competitiveness.FORESHOT using precise molds and advanced Sodick V-Line injection machine and JSW high-speed injection machine to produce and control each item in micro level.
Medical injection molding is a manufacturing process that produces plastic medical devices and components. It involves melting plastic resin pellets and injecting the molten material into a mold to create a specific shape. This process allows for precise control over the product's size and shape and is subject to strict quality and regulatory standards.
The Double-Shot Injection Molding process has two material tubes, which can respectively emit plastic materials of different materials. First, the mold is closed, and a material is injected into the first set mold by the first nozzle, and the obtained semi-finished product is cooled and opened.
In the medical field, we often see metal combined with the plastic part. This is called insert molding and is a very common practice for injection molders to do. You see this all over the medical arena from needles to EKG hook up leads and more.
Prime examples were molding non-communicating passageways through a plastic manifold, molding critical tolerance pacemaker components, and even molding around glass formations without breaking or cracking. Our advanced injection molding equipment makes even the most difficult projects possible.
And then closing the mold with the fixed side of the first set of molds, the first shot and the second shot simultaneously close the mold and open the mold, and then use a second set of nozzles to inject a colored material into the second set of molds, After the product is cooled and molded, the product is obtained by two-color molding, and then the product is taken out, as shown in the following picture.
With the development of science and technology, thin wall injection molding is becoming more and more important due mainly to the growth in telecommunications and portable electronic devices that require thinner and lighter plastic housings. Thin-wall molding offers the opportunity to reduce material part cost and to increase production output through faster cycle times.Thin wall injection molding requires new technology machines that have a multitude of control functions. FORESHOT has advanced V-Line injection machine to achieve the requirement of Thin wall parts and Micro Injection. The most thin thickness is 0.15mm.
Traditional plastic injection molding does often uneven surface gloss of products and floating or exposed fibers on the surface of the fiberglass reinforced plastic chassis、poor transferability、inject pressure excessive and inject pressure uneven that they make stress marks around the mold gate of the product.Therefore, it is necessary printing and painting process to cover these surface defects. For high gloss products, insufficient brightness and uneven brightness cannot be covered by painting.Therefore, FORESHOT develops and apply RHCM technology, not only solve the above problems but also solve traditional plastic injection molding in ultra-thin parts, thick parts and reduces the cycle time.RHCM (Rapid Heat Cycle Molding) is rapidly changing the temperature of mold in injection process.This process is not only vanish the welding lines of the surface, but also improve the rate of product gloss and higher mold transferability.High Gloss / Welding Line free Injection Molding with RHCM process is high-level technology, however, FORESHOT has been operated well in High Gloss / Welding Line free Injection Molding with RHCM process and invests many 250T ~ 1000T RHCM machines that they can do mass production and let customers satisfied.
FORESHOT has great experiences from mold design to assembly service including SMT, PCBA, EMS, plastic product injection, precision plastic parts manufacturing, metal stamping, glue dispense, Ultra Sonic Welding, Ultra Sonic Parts Cleaning, and Product Packaging, With its consistent manufacturing flow service, FORESHOT enables the perfect realization of producing products from scratch for clients.
Double-Shot Injection Molding uses plastic polymers to mold plastic parts with multiple colors, materials or components with complex designs in one mold and machine. Double-Shot injection molding allows versatility, is simpler and more cost effective in comparison to other processes. Double-Shot Injection Molding requires attention that strengthen of joint is one of critical issue to be considered. FORESHOT could use this technology to shorten the cycle time, assembly cost, human resource and turnover rate. Double-Shot Injection Molding apply in keyboard、Computer / Communication / Consumer Electronics、Electronic Components、Precision Components and Vehicle Accessories etc.
The most common types of materials used in medical insert molding are thermoplastics. These are materials that can be heated up into a molten state and pushed through a barrel into a mold. These molds can simply be open and shut type designs, which are what you would expect for, say a simple product such as a cake mold. Or they can be very complex with moving side parts called slides. Of course, the simpler the mold the better for maintenance and longevity. However, complex parts will need these complex designs in order to produce the desired part.
Sometimes the components need to be manufactured separately and then assembled. This is very common in many cases and this can be done by hand or robot.
GETTING A QUOTE WITH LK-MOULD IS FREE AND SIMPLE.
FIND MORE OF OUR SERVICES:
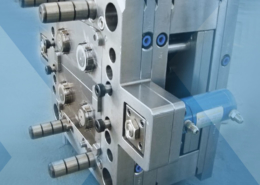
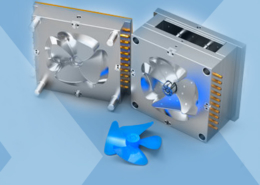
Plastic Molding

Rapid Prototyping
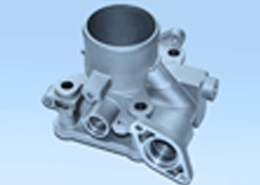
Pressure Die Casting
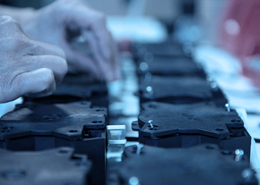
Parts Assembly
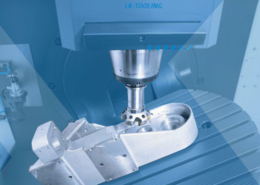