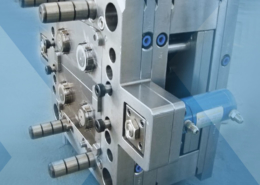
Resin casting - plastic casting
Author:gly Date: 2024-10-15
For certain medical device parts, metal isn’t necessary to create a mould for the injection moulding process, so 3D printing is commonly used to create moulds out of plastic instead.
Advanced Plastics is proud to support National Manufacturing Day 2024 by hosting children from schools in Goole, Vale Academy & Wyke. Pupils were shown a number of processes from hydraulic core systems in injection moulding tools, multi 6 axis robotic assemblies, laser scanning all located at our Hull site, hopefully inspiring them to a career in UK Manufacturing. #NMD24 @makeuk
The technique requires regular injection moulding equipment, but in order for walls to retain their structural integrity as they are created thinner, the base material used tends to be plastics like LCP, polypropylene and nylon – although silicone and metal can also be moulded this way.
While surface-borne infection is a general concern in hospitals, some medical devices have a greater need to remain hygienic than others, like tubes and respiratory masks.
The 3D printing method can also be used to print actual injection moulds, using plastic or metal, but currently available technology is not advanced enough to print with the narrow part tolerances required in an injection mould – although many expect this will change in the future.
Advanced Plastics is proud to support National Manufacturing Day 2024 by hosting children from schools in Goole, Vale Academy & Wyke. Pupils were shown a number of processes from hydraulic core systems in injection moulding tools, multi 6 axis robotic assemblies, laser scanning all located at our Hull site, hopefully inspiring them to a career in UK Manufacturing. #NMD24 @makeuk
Although traditional injection moulding and even gas injection moulding have numerous uses in medical device manufacturing – sometimes the small size coupled with both manoeuvrability and strong mechanical properties necessitates the use of metal over plastic.
In metal injection moulding, a powder made from the desired mix of metals is created using atomisation technology, and this powder is made into a pellet-like form called feedstock, which includes a plastic binding agent to make the substance easier to mould during the injection process.
When parts are created with regular injection moulding there’s a risk that sink marks can occur, making the final product look unsightly and potentially structurally weaker than it needs to be.
Liquid silicone injection moulding is used for devices like these because of the chemical resistance of the rubber-like substance produced using this method, as well as the use of a clean production room so that no ambient air makes contact with the mould and lets dust and moisture into the mixture as it sets.
Material selection will depend on the device being produced and will have undergone testing at different levels of physical pressures and temperatures to ensure they can do the job.
This method is used to create complex parts without any visual blemishes, but because the pressure exerted by the gas lessens if it doesn’t flow in a relatively straight line, it isn’t recommended for parts with sharp corners in their design.
The Advanced Plastics Group of companies provide technical injection moulding solutions to a diverse range of market sectors. Group Overview: Industry-leading with multiple customer satisfaction and industry recognition awards including the highly acclaimed PIA Processor Award in 2022. Annual sales revenue of £38M. 70 injection moulding machines ranging from 22t to 1600t. 300 employees. Three UK manufacturing sites strategically located in the North East, North West and South. 70 years combined heritage in injection moulding. ISO9001, ISO14001 and IATF16949 accreditation. Trading companies:- Advanced Plastics Ltd (Hull) Protool Plastic Components Ltd (Fareham) Protool Precision Plastics Ltd (Manchester)
Much like consumer products, medical device technology is becoming smaller as manufacturing processes become more advanced, and injection moulding has allowed the size of parts to keep pace with this demand for smaller devices.
The most recognisable technique on this list, 3D printing is not technically a form of injection moulding, but it does tend to be used to create prototypes to test a design before it goes into production using injection moulding.
Hull-based Advanced Plastics Group Limited provides a diverse range of technical #injectionmoulding products for blue chip clients across a wide range of market sectors. WITTMANN Group moulding technology currently accounts for over one third of the fleet of machines at Advanced’s disposal. Withing a few months both of the Advanced new acquisitions saw delivery of the tried and tested Wittmann #technology. Rob Anderson Chris Pearson Read more >> https://lnkd.in/exYAEhf5
The reason this happens is because thick areas of a mould cool more slowly than thin ones when the resin is injected, and without enough pressure to pack these areas tightly against the walls, the uneven distribution can cause a sunken appearance.
Once the mixture is injected, the binder is removed using solvent, thermal furnaces, a catalytic process, or a combination of methods, leaving only the metal and resulting in close to 100% density.
Gas-assisted injection moulding is used to solve this issue by running gas (usually nitrogen) through channels built into the mould.
According to a recent report from market insight firm 360 Research Reports, the global market for plastic injection moulding for medical devices is projected to reach over $42bn by 2026, up from $31.6bn in 2020.
Advanced Plastics is proud to support National Manufacturing Day 2024 by hosting children from schools in Goole, Vale Academy & Wyke. Pupils were shown a number of processes from hydraulic core systems in injection moulding tools, multi 6 axis robotic assemblies, laser scanning all located at our Hull site, hopefully inspiring them to a career in UK Manufacturing. #NMD24 @makeuk
Group Managing Director Mark Spence presented Mirella Duca with her award for contribution to Operational Process Improvements. Advanced Plastics Group Limited offers a monthly £50.00 voucher to employees that contribute to business improvements. Congratulations Mirella Duca! #ukmfg #injectionmoulding #continuousimprovement #CI #operations #operationalexcellence
The gas carves a hollow path through the middle of these thicker sections and creates the pressure needed to force the resin tightly against the walls of the mould, creating a smooth part that is structurally sound with no sink marks.
Bright and sunny start in Hull. With our strong balance sheet and multiple site group Advanced Plastics Group Limited is seen as a safe place for transfer business. The NPI team are seeing unprecedented levels of quoting, thanks for your efforts guys.
The term itself simply means creating the walls of a device in a way that makes them thin relative to the whole piece, but in practice this tends to mean walls thinner than 1mm.
Congratulations to Matthew May & Luiza Kotaba on 2 years of hard work to be awarded Cyber Essentials Certificate of Insurance from the National Cyber Security Centre. What is the accreditation and why is it important to us? It is the UK Government’s answer to a safer internet space for organisations of all sizes, across all sectors. Developed and operated by the National Cyber Security Centre (NCSC), gaining Cyber Essentials certification enables organisations to showcase their credentials as trustworthy and secure when it comes to cyber security. Cyber Essentials certification indicates that your organisation takes a proactive stance against malicious cyber attacks. In addition, it offers a mechanism to demonstrate to customers, investors, insurers and others that you have taken the minimum yet essential precautions to protect your organisation against cyber threats. The National Cyber Security Centre states that undertaking the Cyber Essentials certification process and implementing even one of the five controls required by Cyber Essentials can protect businesses from around 80% of attacks. Additional benefits of the certification include: Reassure customers that you are working to secure your IT against cyber attack. Attract new business with the promise you have cyber security measures in place. You have a clear picture of your organisation’s cyber security level. Some Government contracts require Cyber Essentials certification. Cyber hackers are becoming more intelligent and have adapted to many counter-hacking measures. The Cyber Security Breaches Survey 2020 reports that the nature of cyber attacks has changed over the years. Since 2017 the number of businesses experiencing phishing attacks has jumped from 72% to 86%. Our customers and suppliers can be assured that thanks to the IT Team Advanced Plastics Group Limited the systems in Hull, Fareham and Manchester are of the highest standard. #IT #NSCS #cyberessentials #cybersecurity
Rob Anderson comments on the 30 year work anniversary of Mark Desforges--uk at Advanced Plastics Group Limited Mark was our very first employee 30 years ago. From joining the company as a trainee operator, he has progressed through operator, technician, shift manager and process manager roles to his current position as NPI Process Manager. The 32-year development of the company from 4 to 300 employees and 2 to 70 moulding machines mirrors his remarkable journey and demonstrates the commitment to in house training and development, all while raising 3 boys (future employees perhaps). These days Mark will still be seen ostensibly on the shop floor breathing on processes old and new and making a difference. Mark has our unending appreciation for the hard work, skill and dedication he has delivered over the years and for being a pivotal member of the Advanced Plastics family. We salute your achievement, Mark.
From thin wall moulding with liquid crystal polymers (LCP) to the more commonly known 3D printing technique, we look at five types of injection moulding technology used to manufacture medical devices.
Rob Anderson hosted an Advanced Plastics Group Limited golf night. The companies ‘best golfers’ and 1 or 2 hangers on (you know who you are) met for a competition at Brough GC on Friday evening. A competitive and entertaining evening ensued resulting in a close finish with Charlie being pipped at the post by Rob. Suggestions of letting Rob win so he would buy the beers had no foundation, it was pure ability. Great to get out of the factory for some much-needed R&R after a busy week. A warm up for Gareth’s holiday to play in the USA at Sawgrass – hope the swing improved!!
Advanced Plastics Group with sites in Hull, Fareham & Manchester are ready to take immediate transfer business. All three sites have newly increased capacity for July 2024 with the addition of several new injection moulding machines. 70 injection moulding machines from 22 to 1,600 tonnes, IATF 16949, ISO14001 accreditation. Contact me on 07540 723587 to discuss your requirements if you need immediate support due to supplier issues.
But there are several techniques used by companies that produce these parts for medical devices, as well as specific materials better suited to some methods than others, like metals and composites.
Thin walls are often found in wearable devices and micro surgical tools, but can also be used in invasive equipment like catheter ablation tools and endoscopes.
Another benefit is that silicone is biologically inert, meaning it doesn’t react with biological tissue and can be implanted safely in the body.
The basic raw material for silicone rubber is sand, or silicon dioxide, which is processed into pure silicon and reacted with methyl chloride, after which a range of processing steps are used depending on the properties desired for the silicone.
GETTING A QUOTE WITH LK-MOULD IS FREE AND SIMPLE.
FIND MORE OF OUR SERVICES:
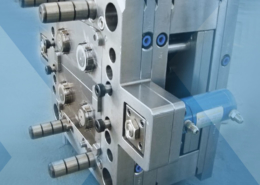
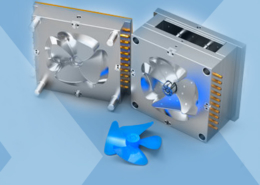
Plastic Molding

Rapid Prototyping
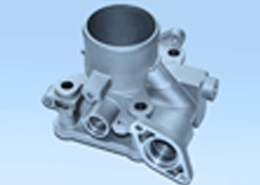
Pressure Die Casting
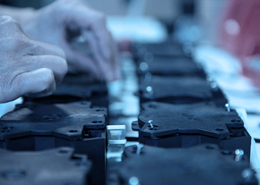
Parts Assembly
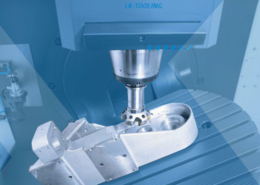