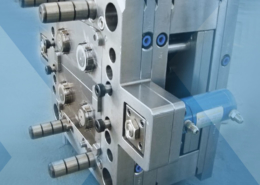
Recycled Resin: the Question and the Caution - recycled plastic injection moldin
Author:gly Date: 2024-10-15
The unique combination of raw materials: responsibly sourced biodegradable biopolymers and naturally occurring clay minerals, gives Sulapac Solid its beautiful ceramic look and feel, even sound, that makes it stand out. Sulapac Solid meets the EU and FDA requirements for food contact materials5 and it contains zero PFAS6.
1 Sulapac Universal Flex 30 meets the EU and US FDA requirements for food contact materials. Restrictions and specifications of use apply, please ask for Declaration of Compliance for further information.
Sulapac materials for injection molding are sustainable alternatives for PS, ABS, PC and PP. They can be used for various applications including cosmetic packaging, kitchenware, and cutlery.
Replace conventional plastic with the beautiful, functional and sustainable Sulapac material. We will help you to make the switch smoothly.
7 The heat resistance of the end product is dependent on the geometry and the manufacturing process of the product. It is the responsibility of the manufacturer of the end product to test and validate the maximum usage temperature and optimize the manufacturing process.
Sulapac Barrier contains 98% USDA certified biobased content2 and biodegrades without leaving persistent microplastics3 or toxic load behind. The material is food contact compliant4 and certified industrially compostable by BPI5.
5 As the compostability of an end product is also dependent on the geometry of product, it is the responsibility of the manufacturer of the end product to ensure compliance with the regulations.
1Biodegradation of 48%–59% in 280 days in the marine environment (30ºC/86ºF) (ASTM D6691). Tested also according to ASTM 5511 (accelerated biodegradation in the landfill, 37ºC/99ºF): 68% relative biodegradation in 160 days. Not considered degradable in California.
This bio-based (87%) material is safe for people and the planet: it is industrially compostable and biodegrades without leaving persistent microplastics behind1.
1Material is suitable for repeated use as per European Commission regulation (EU) No 10/2011. Dishwashability tested according to EN 12875 standard with 125 washing cycles.
4Relative biodegradation of 77,3% in 420 days in simulated marine environment test (ASTM D6691 86 °F/30 °C) using natural sea water. Not considered biodegradable in California
3Restrictions and specifications of use apply, please refer to relevant Declaration of Compliance for further information.
The material is processable with existing injection molding machinery. Our experts assist with the tests and production settings from mold selection to nozzle size.
Supplements that meet people’s unique needs In developed countries people have better living standards than ever before. A high...
Sulapac Premium is made of wood chips from industrial side streams combined with biodegradable biopolymers. This 100% bio-based material biodegrades without leaving persistent microplastics behind1.
Please note that if the end product needs to be resistant to high temperatures (HDT-B 130 °C)6, the minimum mold temperature is 100°C7.
Sulapac® materials are the sustainable, beautiful, and functional alternative to conventional plastic. Start using Sulapac with your existing injection molding equipment and gain competitive advantage through sustainability and innovation.
In the realm of injection molding, ejector marks can present challenges, affecting the surface quality and integrity of molded components. These marks, often undesirable, result from the ejection process and can detract from the aesthetics and functionality of the final product.
1 Material version with USDA Certified Biobased Product label (certification mark of the U.S. Department of Agriculture) available.
Sulapac Luxe contains 73-87% USDA certified biobased content1, sustainably sourced biodegradable biopolymers and non-visible wood flour from industrial side streams being the main components. The material is safe for people and the planet: it leaves no persistent microplastic2 or toxic load3 behind. Sulapac Luxe is recyclable by design4 and can also be made with recycled content.
2 Biodegradation of 56,7% in 280 days in the marine environment ASTM D6691(86°F / 30°C). Not considered biodegradable in California.
Insufficient Cooling Time: Premature ejection of the molded part before it has adequately cooled can lead to deformation and surface imperfections. High Ejection Force: Excessive ejection force applied to the mold can cause indentations or depressions on the surface of the part. Improper Mold Venting: Inadequate venting of the mold cavity can trap air or gases, resulting in localized pressure buildup and ejector marks. Inaccurate Ejector Pin Positioning: Misalignment or improper placement of ejector pins can cause uneven ejection forces, leading to visible marks on the part surface. Material Properties: Certain materials with high shrinkage rates or poor flow properties may be more prone to ejector marks if not properly managed during the molding process.
Sulapac Luxe Flex contains 73-86 % USDA certified biobased content1, sustainably sourced biodegradable biopolymers being the main raw material. Sulapac Luxe Flex is safe for people and planet2. It has been certified industrially compostable by TÜV Austria.3 The material is recyclable by design and can also be made with recycled content.4 Available as non-GMO; ask more from your account executive!
1 Sulapac materials within the same family of recipes show biodegradation of 26-60% at 140 days in the marine environment (30ºC / 86ºF) (ASTM D6691).
Sulapac Luxe Flex is a sustainable material for injection molding ideal for replacing hard plastics like ABS. Luxe Flex can be used to manufacture fragrance caps, cosmetic jars, lids, compact powder boxes, and pencils, for example. The material is resistant to temperature fluctuations, has a high density and a premium look and feel, even sound. With Sulapac Luxe both shiny and matt surface can be achieved depending on your mold selection. The material has excellent processability and it is easy to color with Sulapac masterbatches. Luxe Flex is now also available as black granules!
1The compostability has been tested up to the thickness of 1,48 mm. As the compostability of an end product is also dependent on the geometry of product, it is the responsibility of the manufacturer of the end product to ensure compliance with the regulations.
3The compostability has been tested up to the thickness of 150μm according to BPI (ASTM D6400). As the compostability of an end product is also dependent on the geometry of product, it is the responsibility of the manufacturer of the end product to ensure compliance with the regulations.
3 Raw materials fulfil the requirements for heavy metal tresholds and ecotoxicity according to EN13432 and ASTM D6400.The material complies with the EU and US FDA food contact requirements (restrictions and specifications of use apply, further information in Declaration of Compliance).
4 Can be recycled through hydrolysis back to monomers, suitable as feedstock for recycled biopolymers. Mechanical and chemical recyclability tested and proven technically feasible by third parties. Field tests have also verified that Sulapac materials can be collected and sorted out of a mixed waste stream. When collected together, Sulapac materials do not interfere with the current mechanical recycling of conventional fossil-based or bio-based non-biodegradable plastics. The technology for chemical recycling of bio-based and biodegradable materials exists, but the infrastructure is still under development.
Replace your traditional plastic material and start mass-producing truly sustainable products with minimal investment. Universal material is designed to fit to existing production lines and molds. It is suitable for rigid products such as jars and hangers. Technical specification and easy processing instructions are available in the technical datasheet.
Sulapac’s patent pending innovation is a perfect fit for cosmetic brands seeking for a sustainable packaging for water-based formulas. Used as the inner layer of a jar, it provides an excellent barrier against water evaporation and enables you to pack your emulsions in beautiful, bio-based and biodegradable Sulapac packaging. The weight loss of Sulapac Barrier in one year (demonstrated shelf life) is well below 3%1, which is the typically accepted maximum weight loss for cosmetic packaging.
After a few years of working abroad in Paris and Tokyo, Rebecca Dufour Partanen embarked on a journey that would see her pivot for a fashion and beauty startup in New York and return home to Stockholm with a fresh idea for her own slow...
The material is processable with existing injection molding machinery. Our experts assist with the tests and production settings from mold selection to nozzle size.
The material contains 100% USDA certified biobased content. Sulapac Solid has low carbon footprint2, and it is certified as industrially compostable by BPI3. It doesn’t leave persistent microplastics or toxic load behind4. Furthermore, the material is certified chemically recyclable by LOOPLA technology.
2 Relative biodegradation of 49,7 % in 308 days in simulated marine environment test (ASTM D6691 86 °F / 30 °C) using natural sea water. Not considered biodegradable in California.
To maximise the functionality of your end product, there’s a range of material grades you can choose from with different flexural and tensile properties, heat resistance and density. In terms of look & feel, you can opt for a natural appearance with large wood chips or a smooth polished surface, or something in between!
4 Restrictions and specifications of use apply, please refer to the relevant Declaration of Compliance for further information.
3 Fully biodegradable in simulated marine environment tests according to ISO 22403 and ASTM D6691. Relative biodegradation of 100% (ISO 22403, 27°C / 80°F) and 92% (ASTM D6691, 30°C / 86°F) in 56 days using natural sea water. Not considered biodegradable in California.
Sustainable innovation approach It all began with a desire. In 2018, LES EAUX DE CHANEL introduced a new olfactory world to the...
After a few years of working abroad in Paris and Tokyo, Rebecca Dufour Partanen embarked on a journey that would see her pivot for a...
Supplements that meet people’s unique needs In developed countries people have better living standards than ever before. A high standard of living has enabled people to focus on their health by using health apps and smart rings....
My factory is in Zhejiang, China, if you are interested, you can contact me and we will have a more meaningful negotiation and complete a co-operation project. I have been involved in aluminium casting since 2004 and I have provided countless solutions for my customers.
GETTING A QUOTE WITH LK-MOULD IS FREE AND SIMPLE.
FIND MORE OF OUR SERVICES:
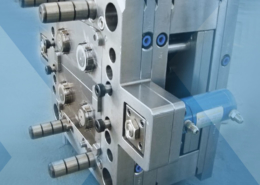
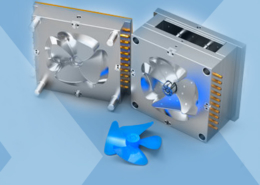
Plastic Molding

Rapid Prototyping
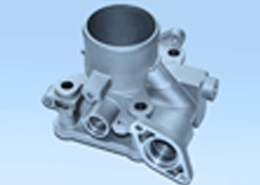
Pressure Die Casting
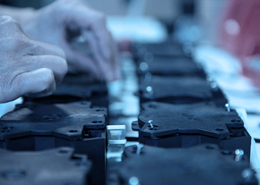
Parts Assembly
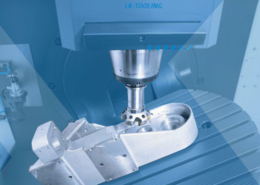