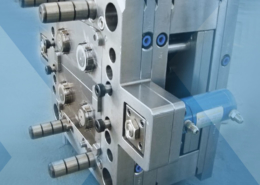
Recycled Resin: the Question and the Caution - recycled plastic injection moldin
Author:gly Date: 2024-10-15
BMP Medical, a manufacturer of diagnostic products, has a full line of urinalysis disposables. We offer the components separately, or in various kit sizes and configurations. The line is built around our 10-chambered Decislide which is made out of optically clear acrylic. It can take 10 individual samples on the same slide eliminating the need for a new slide for each sample.
1. Real clamping force of machine is insufficient. When selecting an injection molding machine, rated clamping force of machine must be higher than tension formed by longitudinal projection area of injection molded product during injection, otherwise it will cause mold expansion and flash. 2. Mold clamping device is not well adjusted, toggle mechanism is not straight, resulting in uneven clamping of left and right or top and bottom molds, phenomenon that parallelism of mold cannot be achieved, causing one side of mold to be tightly closed while the other side is not closely attached, flash will appear during injection. 3. Mold itself is not parallel well, or installation is not parallel, or mold plate is not parallel, or tension rod is unevenly distributed and deformed. These will cause mold to be not tightly closed and flash. 3. Check ring is severely worn, spring nozzle spring fails, barrel or screw is worn too much, inlet cooling system fails to cause "bridging" phenomenon, barrel set injection volume is insufficient, cushion is too small, etc., which may cause flashes to appear repeatedly, and must be repaired or replaced in time .
1. Poor precision of mold parting surface. Movable mold plate (such as middle plate) is deformed and warped; foreign objects are stained on parting surface or there are protruding skid print burrs on the periphery of mold frame; old mold is fatigued and collapsed due to previous flash extrusion. 2. Mold design is unreasonable. Opening position of mold cavity is too off, which will cause tension on one side of mold during injection, causing flash. Fluidity of plastics is too good, such as polyethylene, polypropylene, nylon, etc., in molten state, viscosity is very low, and it is easy to enter movable or fixed gaps, which requires high mold manufacturing accuracy. On the premise of not affecting integrity of product, it should be placed on the center of mass symmetry as much as possible, material should be fed into thick part of product to prevent situation of flashing while lacking material. When there is a molding hole in or near center of product, it is customary to open a side gate on the hole. Because under high injection pressure, if clamping force is insufficient, supporting force of mold in this part will be insufficient and slight warping will occur, resulting in flash. For example, when there are movable components on the side of mold, projected area of side is also affected by molding pressure. If supporting force is not enough, it will cause flash. Sliding core has poor matching accuracy, offset of fixed core and cavity installation position will also cause flash. Poor venting of cavity, no venting groove on parting surface of mold, or venting groove is too shallow, too deep or too large, or blocked by foreign objects will cause flash. For multi-cavity molds, attention should be paid to reasonable design of each runner and gate, otherwise it will cause uneven filling force and flash.
In order to shorten injection molding cycle, the shorter injection port, the better, cross-section should be circular, minimum diameter of nozzle opening is 6 mm, it is a circular cone, and inner angle is 5 degrees. It is best to add a cold slug well, which can prevent poorly melted semi-solid materials from entering mold cavity, and these materials will affect surface modification and product strength. Draft angle should be between 0.50 and 10 to ensure that there is enough venting equipment in cavity. Commonly used vent size is 0.03-0.05mm deep and 6mm wide, or clearance around each thimble is 0.03-0.05 mm. Mold should be made of stainless steel or plated with hard chrome.
1. Injection pressure is too high or injection speed is too fast. Due to high pressure and high speed, opening force to mold increases and causes flash. Injection speed and injection time should be adjusted according to thickness of product. Thin products should be filled quickly at high speed, no injection after full; thick products should be filled at low speed, skin should be generally fixed before reaching final pressure. 2. Excessive feeding volume causes flash. It is worth noting that do not inject too much melt in order to prevent depression, so that depression may not be "filled", but flash will appear. This situation should be resolved by extending injection time or holding time. 3. Too high temperature of barrel and nozzle or too high mold temperature will reduce viscosity of plastic and increase fluidity, which will cause flashing under condition of smooth injection.
These high-quality non-graduated lab containers are designed for the collection, transport, and storage of specimens and samples. Tight fitting lids prevent leaks and odors. Ideal for storing biologically hazardous samples for terminal autoclaving before disposal. Molded from various materials. The stackable containers are resistant to freezing and boiling.
BMP Medical is a leading plastic manufacturing of medium- to high-volume medical devices and components. Our global state-of-the-art facility located in Sterling, Massachusetts, offers product design and development, R&D tooling, custom cleanroom assembly and packaging, Class 7 assembly, and Class 8 cleanroom manufacturing. Whether you have a new device concept, an approved design, or a design transfer, we’ll work with you to provide the best injection molding solution.
We are a privately held company that has been in business for over 45 years. We use state-of-the-art molding techniques and machinery to produce varying-sized components with very tight specifications. We also offer design consultation, engineering, drawing, R&D, tooling, mold development, process automation, and statistical process control. Our facility is equipped with a Class 8 cleanroom for manufacturing, assembly, and packaging needs.
We offer two lines of tissue grinders for the clinical lab and research lab. The standard product is all plastic and is designed to grind softer tissues such as liver and spleen. The Ultra tissue grinder line has a vitrified tip and is designed for tougher material such as muscle or bone. Both lines are delivered sterile sealed Tyvek® (Tyvek® is a registered trademark of DuPont) package.
Our 80,000 sq. ft. plastics manufacturing facility is based in North America and headquartered in Sterling, Massachusetts.
At BMP Medical, a leader in contract manufacturing for medical devices, we prioritize fostering a work environment that promotes growth, safety, and inclusivity for all employees. Our recent initiatives reflect our dedication to continuous improvement and workforce...
Failure to use the correct rotor cushion or adapter will shorten the life of the bottle and may prevent achievement of the maximum rated RCF and/or bottle failure.
PVC is a heat-sensitive plastic. Overheating or excessive shearing will cause decomposition and spread rapidly, because one of decomposition products (such as acid or HCI) will have a catalytic effect, causing process to further decompose. Acid will erode metal and turn it into dents. It will also peel off protective layer of metal and cause rust, which is more harmful to human body. 1. Screw gasket: Screw gasket is between 2mm and 3mm. larger machines will be larger. 2. Injection volume: Actual retention time of cylinder should not exceed 3 minutes. 3. Barrel temperature setting: Temperature provided can only be used as a reference. Make appropriate adjustments according to actual conditions of machine and raw materials, or it may exceed recommended range. 4. Residence time of barrel: under temperature control of 2000C (compound), residence time of barrel can exceed 5 minutes at most. 5. Injection speed: Injection speed should be slow, otherwise excessive shearing will degrade material. When using UPVC to produce extremely smooth thick-walled products, multi-stage injection speeds should be used. If there are light brown stripes radiating from gate, it means that injection speed is too fast. 6. Back pressure: Commonly used surface value is 5bar. Increasing back pressure is beneficial to color mixing and exhaust, but back pressure should be as low as possible. 7. Shutdown: Due to low overheating stability of PVC, shutdown part is very important. Clean barrel without leaving any PVC. Other thermoplastics with high overheating stability and non-resistance to PVC can be used, such as PMMA, PP, LDPE, or GPPS), do not mix POMT UPVC in same barrel, otherwise it will cause excessive chemical reaction and cause serious damage to machine. 8. Mixing ratio: Maximum mixing ratio of nozzle material is 20%, otherwise it will affect product quality. 9. Typical products: Main purpose of UPVC is to make drainage pipes, shells of computers and televisions, water filter tanks, photocopier shells, electric meters and gas shells, transparent covers of printing machines, communication styles and various electronic parts.
Our workforce boasts a high degree of experience and training in the manufacturing of plastic medical devices and components for OEM partners. We will work together with you on developing a personalized and effective quality plan and assurance program with routine audits that meets all of your quality, traceability and consistency requirements. We’ll be your trusted long-term partner. BMP Medical employees are trained with an emphasis on the “pursuit of perfection” in all we do.
When collaborating with BMP Medical, you will experience very robust quality assurance standards. BMP Medical is ISO 13485:2016 certified, fully FDA compliant, and cGMP. Our continuous improvement approach provides OEMs superior quality and better management oversight of their suppliers. Ask us why BMP Medical became the first MedAccred certified injection molding company within the MedTech industry.
Flash, also known as flashing, burrs, piercing, etc., mostly occurs at opening and closing positions of mold. Such as: parting surface of mold, sliding part of slider, gap of insert, hole of ejector, etc. If flash is not resolved in time, it will be further enlarged, resulting in a partial collapse of imprinting mold, causing permanent damage. Flash of insert gap and ejector pin pores will also cause product to be stuck on mold and affect demolding.
The Hemodrop is designed to reduce the risk of exposure to bloodborne pathogens in the Hematology laboratory. To prepare a manual differential smear, a drop of blood needs to be dispensed onto a glass slide from the specimen tube. Simply puncture the rubber stopper with the Hemodrop, and then invert and press gently onto the slide. A single drop of blood will be dispensed and the slide is ready. No more removing the stopper and manually putting a drop on the slide to test blood.
Efficiency and precision are paramount in the medical device manufacturing industry. As technology advances and regulatory requirements become more stringent, the need for streamlining the assembly process has never been more
We are ISO 13485: 2016 certified. Our Quality Management System (QMS) is designed to meet all of our customers’ expectations and documentation requirements and we will work with you to address any additional requirements.
Thermal stability of PVC is poor, molding temperature is close to decomposition temperature, fluidity is not good, and appearance is easy to form defects. PVC material has poor heat resistance and is most likely to scorch, generate acid gas and corrode mold. Plasticizer can be added to increase its fluidity during processing. Generally, additives must be used. Its strength, electrical insulation and chemical resistance are good.
Polypropylene Beakers are resistant to most commonly used laboratory reagents, including a variety of strong acids, bases, and organic solvents, these high quality polypropylene beakers are the premier choice for scientific laboratory applications. All beakers are transparent for clear content visibility and graduated for easily estimating volumes. Molded-in pouring spouts, and a rolled lip, for a dripless working environment. Autoclavable to 121ºC ( 248ºF).
Because of its low price, PVC material has inherent anti-inflammatory properties, is strong and strong, has good chemical resistance, and has a shrinkage rate of 0.2-0.6%. Products are increasingly used in electrical appliances, machinery, construction, daily necessities, toys, and packaging. According to characteristics of PVC material, injection molding process of products is analyzed as follows:
1. If plastic viscosity is too high or too low, flash may appear. Plastics with low viscosity, such as nylon, polyethylene, polypropylene, etc., should increase clamping force; plastics with strong water absorption or water-sensitive plastics will greatly reduce flow viscosity at high temperatures and increase possibility of flashing. These plastics must be thoroughly dried; viscosity of plastics mixed with too much recycled materials will also decrease, and if necessary, replenish retained components. If viscosity of plastic is too high, flow resistance will increase, and a large back pressure will increase pressure of cavity, resulting in insufficient clamping force and flash. 2. When size of plastic raw materials is not uniform, feeding amount will vary, parts may not be full or flash.
In today's healthcare landscape, precision, reliability, efficiency and quality are paramount. Medical injection molding companies play a crucial role in meeting these demands, especially in the development of life-enhancing medical devices, diagnostic tools, and...
Step one is to establish the correct Intellectual Properties register rights for your product. Once that is complete, you are ready to engage with BMP Medical as your trusted manufacturing partner. We understand your concerns when it comes to protecting your IP. We will work closely with you on developing a signed nondisclosure agreement that states your organization owns the IP.
These precision molded centrifuge bottles are available in polycarbonate or polypropylene. For low speed applications the bottles provide excellent value for large volume/large batch centrifugation procedures. For high-speed work, the easy-to-use Noryl® (Noryl® is a registered trademark of General Electric Company) sealing caps with silicone O-rings enable leak-free processing at high centrifugal forces over long durations. Bottles must be filled to 80% of capacity.
Centrifuge bottles may be autoclaved at 121ºC at 15 psi for 20 minutes. Caps should be placed on the bottles without engaging the threads. Bottles are qualified to the rated g-forces using Sorvall® (Sorvall® is a registered trademark of Kendro Laboratory Products) and Fiberlite® (Fiberlite® is a registered trademark of Piramoon Technologies Inc.) high-speed rotors, tested at 20ºC, with bottles filled to 80% of capacity.
For specimen collection and transport, this system provides disposable products for the convenient collection, delivery, and testing of urine specimens. A plastic cup is provided for specimen collection and the pressure sensitive patient identification labels have ample writing space. The lightweight transport rack is small and easy to carry yet provides space for up to 20 tubes with labels and caps. The tubes are made of sturdy polystyrene and are safe for centrifuging. The flared top permits the use of a midget urinometer ensuring a tight cap fit.
BMP Medical Cytology Funnels for the Shandon CytoSpin® Centrifuge BMP Medical Cytology Funnels are the functional equivalent of the Thermo Shandon CytoFunnel®. Fully compatible with the Shandon CytoSpin Centrifuge, BMP Medical Cytology Funnels can be used to deposit a thin layer of cells in a clearly defined area of a microscope slide. The filter card absorbs any excess fluid. Operation is identical to those supplied by Shandon and easy-to-follow instructions are included in each pack. All products sold in case quantities only.
We continuously work to ensure that we meet all quality and regulatory requirements throughout your entire product life-cycle.
BMP Medical is a quality manufacturer of plastic consumables and plastic products for research and medical diagnostic laboratories. Our products are manufactured to the highest quality standards. We offer a wide selection of products sold through the world’s premier laboratory distributors.
BMP Medical is a family-owned business with nearly one hundred employees. We foster strong, long-term relationships to develop tailored plastic manufactured solutions for your medical device and component needs. You will always experience a one-on-one personal touch with a complete team approach when interacting with BMP Medical. Whether you are reviewing a quotation with our sales representatives or discussing a prototype with our engineers, you will always experience a friendly, knowledgeable, and extremely dedicated individual. We work endlessly to provide optimal value to our customers, and take pride in our ability to be agile to your evolving needs. Get to know BMP Medical!
GETTING A QUOTE WITH LK-MOULD IS FREE AND SIMPLE.
FIND MORE OF OUR SERVICES:
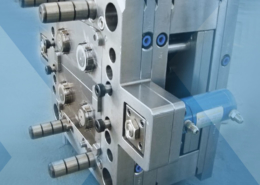
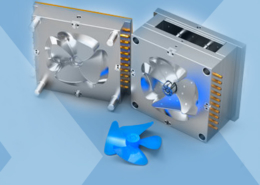
Plastic Molding

Rapid Prototyping
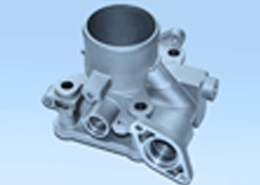
Pressure Die Casting
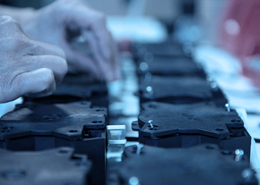
Parts Assembly
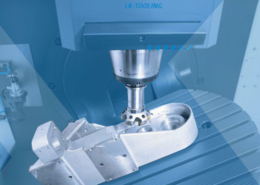