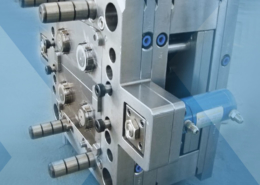
6. Challenges and Considerations
Author:gly Date: 2024-06-08
Despite its numerous benefits, prototype plastic injection molding also presents challenges and considerations that must be addressed to optimize its effectiveness and efficiency in product development.
Cost Constraints
One of the primary challenges of prototype plastic injection molding is cost. Traditional injection molding requires the fabrication of custom molds, which can be expensive and time-consuming. While prototype molds are typically less costly than production molds, they still represent a significant investment. Manufacturers must carefully weigh the benefits of prototype molding against the associated costs and determine the most cost-effective approach for their specific project needs.
Time-to-Market Pressures
In today's fast-paced business environment, time-to-market is a critical factor in product success. Prototype plastic injection molding offers a rapid development cycle compared to traditional manufacturing methods. However, even with accelerated timelines, there may still be pressure to bring products to market quickly. Manufacturers must balance the need for speed with the importance of thorough testing and validation to ensure product quality and reliability.
Design Limitations
While prototype plastic injection molding enables the production of complex geometries and functional prototypes, there are limitations to consider. Certain design features, such as undercuts, thin walls, and intricate details, may be challenging to replicate using injection molding. Designers must work closely with molders to optimize designs for manufacturability and identify any potential issues early in the development process.
7. Future Outlook and Emerging Trends
The future of prototype plastic injection molding is bright, with emerging trends and technological advancements poised to reshape the landscape of product development and manufacturing.
Digital Twin Technology
Digital twin technology holds promise for revolutionizing prototype plastic injection molding. By creating virtual replicas of physical molds and production processes, manufacturers can simulate and optimize every aspect of the molding process, from material flow and cooling kinetics to part quality and performance. Digital twins enable real-time monitoring and predictive analytics, allowing for proactive maintenance, process optimization, and continuous improvement.
Additive Manufacturing Integration
The integration of additive manufacturing with prototype plastic injection molding offers exciting possibilities for design innovation and customization. Hybrid manufacturing processes, such as mold inserts produced through 3D printing, enable the rapid iteration of mold designs and the production of complex geometries that would be difficult or impossible to achieve with traditional methods. Additive manufacturing also facilitates on-demand production, reducing lead times and inventory costs.
Sustainable Solutions
Sustainability will continue to be a driving force in prototype plastic injection molding. Manufacturers are exploring sustainable materials, such as bio-based polymers and recycled resins, to reduce environmental impact and meet consumer demand for eco-friendly products. Additionally, advancements in energy-efficient processes, waste reduction strategies, and closed-loop recycling systems will further enhance the sustainability of prototype molding operations.
8. Conclusion: Embracing Innovation in Prototype Molding
In conclusion, prototype plastic injection molding represents a cornerstone of innovation and agility in product development and manufacturing. From its ability to rapidly iterate designs to its applications across industries and its potential for future advancements, prototype molding plays a vital role in bringing ideas to life and driving progress in the global marketplace.
As we look to the future, it is essential for manufacturers to embrace innovation, sustainability, and collaboration in prototype plastic injection molding. By leveraging emerging technologies, optimizing processes, and prioritizing customer needs, we can unlock new opportunities, overcome challenges, and create a brighter, more sustainable future for generations to come. Through collective effort and shared vision, prototype molding will continue to empower designers, engineers, and innovators to shape the world around us.
GETTING A QUOTE WITH LK-MOULD IS FREE AND SIMPLE.
FIND MORE OF OUR SERVICES:
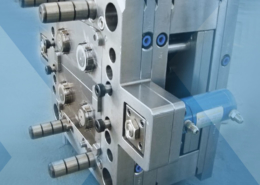
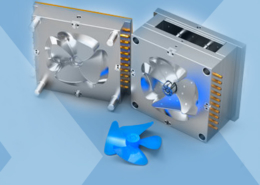
Plastic Molding

Rapid Prototyping
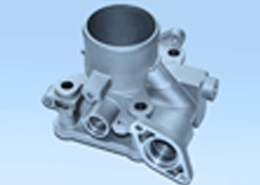
Pressure Die Casting
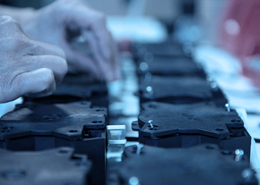
Parts Assembly
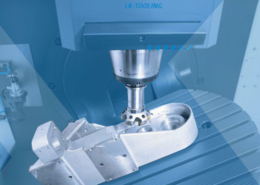