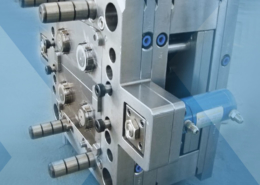
Exploring Prototype Injection Molding: Revolutionizing Product Development
Author:gly Date: 2024-06-08
In today's fast-paced world of product development, time-to-market is often a critical factor in a product's success. This urgency has led to the widespread adoption of rapid prototyping techniques, among which prototype injection molding stands out as a versatile and efficient method. This article delves into the realm of prototype injection molding, uncovering its significance, applications, benefits, and future prospects.
Introduction to Prototype Injection Molding
Prototype injection molding is a manufacturing process that involves the creation of prototype parts or components using injection molding technology. Unlike traditional injection molding, which is geared towards mass production, prototype injection molding focuses on producing small quantities of parts for testing, validation, and iteration during the product development phase.
Advantages of Prototype Injection Molding
Speed and Efficiency
Prototype injection molding offers unparalleled speed and efficiency in producing functional prototypes. With rapid turnaround times, designers and engineers can quickly iterate designs, test functionality, and validate concepts, accelerating the product development cycle.
Cost-Effectiveness
Compared to traditional methods of prototyping, such as CNC machining or 3D printing, prototype injection molding can be more cost-effective, especially for producing small to medium-sized batches of parts. The amortized cost per part decreases as the quantity increases, making it an attractive option for low-volume production runs.
Material Selection
One of the key advantages of prototype injection molding is the ability to use a wide range of materials, including engineering-grade thermoplastics. This allows for more accurate functional testing, as prototypes can closely mimic the properties of final production parts.
Applications of Prototype Injection Molding
Prototype injection molding finds applications across various industries, including automotive, aerospace, medical devices, consumer electronics, and more. From concept validation to pre-production testing, prototype injection molding plays a crucial role in bringing innovative products to market.
Challenges and Considerations
While prototype injection molding offers numerous benefits, it is not without its challenges. Factors such as tooling costs, design complexity, and part geometry can impact the feasibility and cost-effectiveness of the process. Additionally, material selection and compatibility with production-grade resins require careful consideration to ensure accurate prototype validation.
Future Trends and Innovations
The future of prototype injection molding is ripe with possibilities. Advances in additive manufacturing technologies, such as multi-material printing and in-situ reinforcement, promise to further enhance the capabilities of prototype injection molding. Additionally, the integration of digital twin technology and machine learning algorithms could revolutionize the design optimization and prototyping process.
Conclusion
In conclusion, prototype injection molding stands as a cornerstone of modern product development, offering unparalleled speed, efficiency, and flexibility. By enabling rapid iteration and validation of design concepts, prototype injection molding accelerates the journey from ideation to market-ready products. As technology continues to evolve, the potential for innovation in prototype injection molding remains limitless, paving the way for a future of faster, more cost-effective product development processes.
GETTING A QUOTE WITH LK-MOULD IS FREE AND SIMPLE.
FIND MORE OF OUR SERVICES:
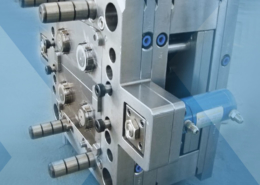
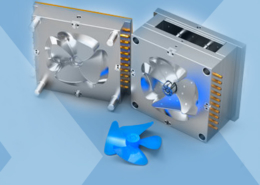
Plastic Molding

Rapid Prototyping
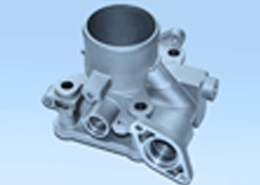
Pressure Die Casting
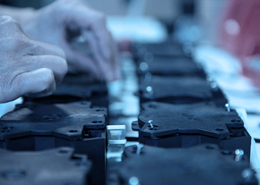
Parts Assembly
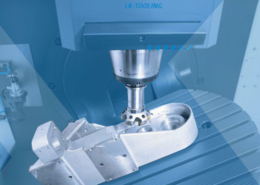