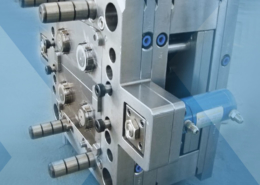
Precision Plastic Mold: Revolutionizing Manufacturing
Author:gly Date: 2024-06-08
Precision plastic molds stand at the forefront of modern manufacturing, revolutionizing industries with their intricate designs and impeccable quality. In this comprehensive exploration, we delve into the essence of precision plastic molds, uncovering their significance, applications, and the technological innovations driving their evolution.
The Genesis of Precision Plastic Molds
Precision plastic molds trace their origins to the dawn of the plastics industry. With the increasing demand for complex plastic components across diverse sectors, the need for precise and efficient molding techniques became paramount. The advent of precision plastic molds marked a paradigm shift, enabling manufacturers to achieve unparalleled accuracy and consistency in their production processes.
Pioneering Innovations
Pioneering innovators in the field, such as Robert A. Schad and Herbert Rees, played instrumental roles in refining and advancing precision plastic molding technology. Their groundbreaking contributions laid the foundation for the sophisticated molding techniques employed in contemporary manufacturing.
Evolution of Materials
The evolution of materials used in precision plastic molds has been pivotal in enhancing their performance and versatility. From traditional thermoplastics to advanced engineering polymers, the repertoire of materials compatible with precision molding continues to expand, offering manufacturers a broader spectrum of possibilities.
Integration of Automation
The integration of automation and digitalization has revolutionized the landscape of precision plastic molding. Computer-aided design (CAD) and computer-aided manufacturing (CAM) systems have streamlined the design-to-production workflow, optimizing efficiency and minimizing errors.
Applications Across Industries
The versatility of precision plastic molds transcends industry boundaries, finding application in a myriad of sectors, including automotive, electronics, medical devices, and consumer goods. Let's explore some prominent domains where precision plastic molding makes a significant impact:
Automotive Sector
In the automotive sector, precision plastic molds are indispensable for the fabrication of intricate components ranging from dashboard panels to engine parts. Their ability to withstand high temperatures and corrosive environments makes them ideal for demanding automotive applications.
Electronics Industry
The electronics industry relies heavily on precision plastic molds for the production of miniature yet intricately designed components such as connectors, housings, and circuit encapsulations. The precise dimensional control offered by these molds ensures optimal performance and reliability of electronic devices.
Medical Device Manufacturing
In the realm of medical device manufacturing, precision is paramount, and precision plastic molds rise to the occasion. From surgical instruments to implantable devices, these molds facilitate the production of sterile, biocompatible components that meet stringent regulatory standards.
Technological Advancements
Continual advancements in technology drive the evolution of precision plastic molds, pushing the boundaries of what is achievable in terms of design complexity, cycle times, and material compatibility.
Additive Manufacturing Integration
The integration of additive manufacturing techniques, such as 3D printing, complements traditional molding processes, enabling rapid prototyping and the fabrication of intricate mold inserts with unprecedented geometries.
Multi-Material Molding
Multi-material molding techniques enable the incorporation of diverse materials within a single component, enhancing functionality and performance. This versatility opens new avenues for product innovation across various industries.
Micro-Molding Capabilities
Micro-molding capabilities have expanded the horizons of precision plastic molding, allowing for the production of ultra-small components with micron-level precision. This breakthrough has catalyzed advancements in fields such as microfluidics, MEMS (Micro-Electro-Mechanical Systems), and biomedical engineering.
Challenges and Future Prospects
While precision plastic molding has undoubtedly revolutionized manufacturing, it is not without its challenges. Issues such as tooling costs, cycle time optimization, and material selection continue to pose challenges for manufacturers. However, with ongoing research and development efforts, these hurdles are gradually being overcome.
Sustainable Practices
The adoption of sustainable practices in precision plastic molding is imperative to mitigate environmental impact. Innovations in recyclable materials, energy-efficient processes, and waste reduction strategies are pivotal in fostering a greener and more sustainable manufacturing ecosystem.
Industry 4.0 Integration
The integration of precision plastic molding with Industry 4.0 principles, such as IoT (Internet of Things) connectivity and data analytics, holds immense potential for optimizing production processes, predicting maintenance needs, and achieving unprecedented levels of efficiency and quality control.
In conclusion, precision plastic molds epitomize the synergy between technological innovation and manufacturing excellence. As we continue to push the boundaries of what is achievable, these molds will remain at the forefront of industrial progress, shaping the future of manufacturing with their precision, versatility, and transformative capabilities.
GETTING A QUOTE WITH LK-MOULD IS FREE AND SIMPLE.
FIND MORE OF OUR SERVICES:
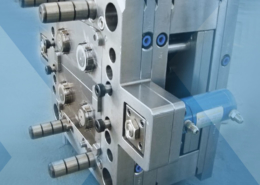
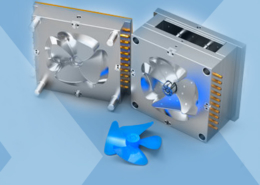
Plastic Molding

Rapid Prototyping
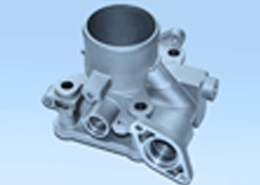
Pressure Die Casting
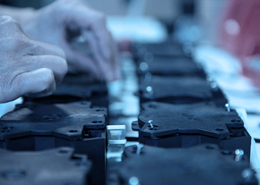
Parts Assembly
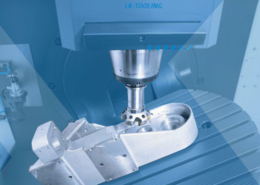