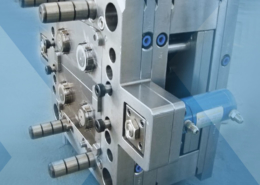
Precision Plastic Injection Moulding: Shaping the Future of Manufacturing
Author:gly Date: 2024-06-08
Introduction:
Precision plastic injection moulding stands as a cornerstone of modern manufacturing, offering unparalleled accuracy, efficiency, and versatility. From intricate medical devices to durable automotive components, this advanced technique has transformed the way plastic products are manufactured. In this article, we delve into the world of precision plastic injection moulding, exploring its origins, applications, and technological advancements.
Background:
Precision plastic injection moulding, also known as injection moulding, emerged in the mid-20th century and has since become a fundamental process in the produc
Title: Precision Plastic Injection Moulding: Shaping the Future of Manufacturing
Introduction:
Precision plastic injection moulding stands as a cornerstone of modern manufacturing, offering unparalleled accuracy, efficiency, and versatility. From intricate medical devices to durable automotive components, this advanced technique has transformed the way plastic products are manufactured. In this article, we delve into the world of precision plastic injection moulding, exploring its origins, applications, and technological advancements.
Background:
Precision plastic injection moulding, also known as injection moulding, emerged in the mid-20th century and has since become a fundamental process in the production of plastic components. It involves injecting molten plastic material into a mould cavity under high pressure, where it solidifies to form the desired shape. With advancements in machinery, materials, and software, precision plastic injection moulding has become synonymous with quality, efficiency, and innovation in manufacturing.
Precision and Accuracy
Precision plastic injection moulding excels in producing complex and intricate parts with exceptional precision and accuracy. The ability to control various parameters such as temperature, pressure, and injection speed ensures consistent quality and dimensional stability. This level of precision is crucial in industries such as healthcare, where tight tolerances are required for medical devices and implants.
Efficiency and Cost-Effectiveness
Beyond precision, plastic injection moulding offers unmatched efficiency and cost-effectiveness. By utilizing automated processes and high-speed machinery, manufacturers can produce large volumes of parts quickly and with minimal labor costs. Additionally, the repeatability of injection moulding reduces material waste, further enhancing cost efficiency and sustainability.
Material Versatility
One of the key advantages of precision plastic injection moulding is its ability to work with a wide range of thermoplastic materials, including engineering-grade plastics, elastomers, and biodegradable polymers. This versatility allows for the production of parts with varying properties, such as strength, flexibility, and heat resistance, to meet diverse application requirements. Moreover, advancements in material science continue to expand the possibilities of injection moulding, enabling the development of innovative products and solutions.
Design Freedom and Innovation
Precision plastic injection moulding offers unparalleled design freedom and innovation opportunities. With the ability to create complex geometries, thin walls, and intricate features, designers can push the boundaries of creativity and functionality. Furthermore, the integration of technologies such as 3D printing and computer-aided design (CAD) facilitates rapid prototyping and iteration, accelerating the product development cycle and fostering innovation in various industries.
Conclusion:
In conclusion, precision plastic injection moulding plays a pivotal role in shaping the future of manufacturing. Its combination of precision, efficiency, and material versatility makes it an indispensable process across industries, from healthcare and automotive to consumer electronics and beyond. As technology continues to evolve and new materials emerge, the potential for innovation and growth in precision plastic injection moulding remains boundless.
Recommendations for Future Research:
Looking ahead, further research and development in precision plastic injection moulding could focus on enhancing process efficiency, optimizing material properties, and exploring new applications in emerging fields such as biotechnology and sustainable packaging. Additionally, efforts to improve sustainability through the use of recycled materials and eco-friendly processes would contribute to a more environmentally conscious manufacturing industry.
GETTING A QUOTE WITH LK-MOULD IS FREE AND SIMPLE.
FIND MORE OF OUR SERVICES:
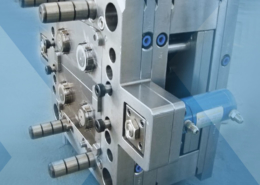
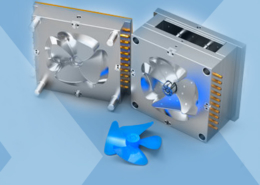
Plastic Molding

Rapid Prototyping
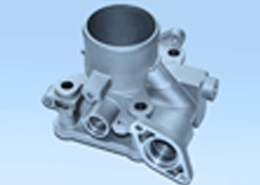
Pressure Die Casting
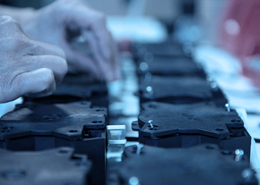
Parts Assembly
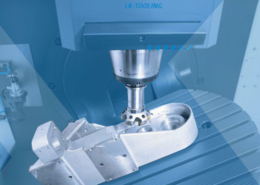