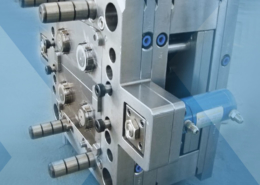
Precious Plastics V2 Injection Machine - precious plastic injection
Author:gly Date: 2024-10-15
Polyetheretherketone (PEEK) is a high-performance engineering thermoplastic known for its excellent mechanical properties, chemical resistance, and thermal stability. When it comes to injection molding PEEK, certain key elements and considerations are essential to ensure successful processing and high-quality parts.
Material Selection: Choose the appropriate PEEK material grade based on the specific application requirements, considering factors such as mechanical properties, temperature resistance, chemical resistance, wear resistance, and regulatory compliance.
Low volume injection molding is a production process that is particularly suitable for short runs, typically in the range of hundreds to thousands of parts. It’s a cost-effective solution for projects that don’t require the high quantities often associated with traditional injection molding, which is typically optimized for runs of tens of thousands to millions of units.
Ming-Li Precision offers advanced capabilities in molding PEEK (Polyether Ether Ketone), a high-performance engineering thermoplastic known for its exceptional mechanical properties, chemical resistance, and thermal stability. With over 100 tons of PEEK material molding production experience, Ming-Li is a valuable partner for industries requiring precision and durability in challenging environments.
3D printing has revolutionized many manufacturing processes, including injection molding. In this process, a mold is 3D printed using a high-temperature material such as thermoplastic polyurethane (TPU) or polyetherimide (PEI). The mold is then used to produce the part using conventional injection molding techniques. One of the advantages of this process is that it can produce parts with complex geometries in a relatively short amount of time, and at a lower cost than conventional injection molding. However, the mold material is not as durable as steel or aluminum, so the number of parts that can be produced is limited.
Quality Control and Inspection: Establish comprehensive quality control measures and inspection procedures to monitor part dimensions, surface finish, and physical properties. Conduct regular inspections and testing to verify part quality and consistency.
Our team of experienced engineers and technicians works closely with clients to ensure that their specific requirements are met. We provide customized solutions for small batch production, prototyping, and end-use parts, using the latest technology and materials. Our services are ideal for startups, small businesses, product designers, and medical device manufacturers who require small quantities of high-quality plastic parts.
Low volume injection molding is suitable for companies or individuals who need to produce small quantities of plastic parts. This could include:
Serving as a credible low-volume injection molding company, Sungplastic follows a process that involves injecting molten plastic material into a mold cavity, which is then cooled and solidified to form a part. Efficiently and affordably, making hundreds of functional prototypes and regions can accelerate product development, reduce costs and lead times, and bring better products to market, ultimately contributing to creating business value. You can invest in your projects and produce high-quality and repeatable parts by choosing to avail quality services from top injection molding manufacturers.
Our on-demand, low volume production approach offers numerous benefits, including cost-effectiveness, efficient supply chain management, and the ability to validate part design and manage inventory overhead.
Low volume injection molding is a manufacturing process used to produce small quantities of plastic parts. It is typically used for prototyping, bridge tooling, and low volume production runs. The low volume injection molding process involves injecting molten plastic material into a mold cavity, which is then cooled and solidified to form a part. There are several processes used for low volume injection molding, each with its own advantages and limitations. Next, we will discuss some of the most commonly used processes for low volume injection molding.
Desktop 3D printing presents an efficient and cost-effective solution for rapidly fabricating injection molds. With minimal equipment requirements, it saves CNC time and skilled labor for other valuable tasks. Manufacturers can harness the speed and flexibility of in-house 3D printing to create molds that, when coupled with injection molding, can deliver series of units from common thermoplastics within days. This approach enables the realization of intricate mold designs that might be challenging through traditional methods and can be utilized on both desktop and industrial molding machines, fostering greater innovation in development teams. Moreover, product development benefits from the ability to iterate on designs and test end-use materials before investing in costly hard tooling.
As a full-service low volume manufacturing provider, we can help you validate your part design and manage inventory overhead by producing parts only when demand dictates. This approach also allows you to optimize your supply chain, making it more agile in managing demand volatility.
Venting and Degassing: Ensure proper venting and degassing of the mold cavity to eliminate trapped air and gas bubbles during the injection process, preventing defects such as voids, bubbles, or surface imperfections in the molded parts.
Traditionally, molds are crafted from metal using CNC machining or electric discharge machining (EDM). These industrial methods are costly and require specialized equipment, advanced software, and skilled labor. As a result, producing a metal mold typically takes four to eight weeks and incurs costs ranging from $2,000 to $100,000+, depending on the part’s shape and complexity. For smaller part quantities, the expenses, time, specialized equipment, and skilled labor associated with fabricating metal molds through conventional means often make injection molding at this scale unfeasible.
Before moving on to high-scale production, high-quality prototypes can be produced using low-volume injection molding for testing and validation.
Throughout the entirety of the low-volume injection molding process, it is crucial to continually monitor and adjust parameters as needed to ensure the production of parts of the highest quality. Always adhere to safety protocols and industry best practices to ensure the well-being of personnel and the proper operation of equipment.
By addressing these key elements and optimizing the PEEK injection molding process, manufacturers can produce high-quality, precision-molded parts with consistent performance and reliability for a wide range of applications.
Are you looking for the right manufacturing process for your new plastic product? If you have questions about plastic manufacturing processes, material selection, or input costs, please contact us. We are more than happy to help you.
Low-volume injection molding is the most economical and practical choice for products that need specialized or custom parts in small quantities.
Conventional injection molding is the most common process used for high-volume production runs, which usually uses steel mold. However, it can also be used for low volume runs as well. In this process, the plastic material is melted and injected into steel mold cavities under high pressure. The steel injection mold is then cooled to solidify the plastic and the part is ejected. One of the advantages of this process is that it can produce complex geometries with tight tolerances. However, the high cost of tooling and long lead times make it less ideal for low volume runs. If plastic products require complex structure and high precision, choosing the steel mold to carry out injection molding processing, which can get a stable quality of the final product.
Moreover, our cost-effective aluminum tooling provides a bridge to mass production of plastic parts, allowing you to transition without committing to a significant investment in steel tooling. This way, you can streamline your production process and reduce costs while maintaining high-quality standards.
In the realm of low-volume injection molding, the type of injection press used has minimal impact on the process. These injection machines are costly, have stringent facility requirements, and demand skilled labor. Consequently, most enterprises choose to outsource mid- and high-volume production to service providers and contract manufacturers.
PEEK plastic exhibits superb mechanical properties and is highly resistant to chemicals and thermal degradation, making it a highly desirable material for plastic injection molded products. PEEK resin holds up well against high temperatures and long-term liquid submersion and is very durable in harsh environments. PEEK plastic makes an excellent reinforcement material, providing great tensile strength with low weight.
Initiate the injection molding process as per the operating instructions of the machine.The process typically involves the following stages:
Tool Fabrication: Fabricate the mold tooling using high-quality materials and precision machining techniques to achieve tight tolerances, smooth surface finishes, and durability. Verify the accuracy of the mold components through thorough inspection and validation.
Here is your chance to avail yourself of the most efficient low-volume injection molding, a renowned manufacturing process for producing small quantities of plastic parts. Sungplastic is a trusted injection molding manufacturer that vouches that these solutions are ideal for various purposes, such as prototyping, bridge tooling, and low-volume production runs. So, if you are looking for credible low-volume injection molding solutions, look no further.
We strive to provide high-quality, affordable components. Sungplastic provides a variety of low-volume injection molding services to meet customer needs. Our professional engineers and technicians use the latest technology and materials to create specific solutions for small-batch production, prototyping, and end-use parts to meet the client’s individual needs.
Injection Process Optimization: Optimize process parameters such as barrel temperature, injection pressure, injection speed, cooling time, and hold pressure to achieve consistent part quality, minimize cycle times, and prevent defects such as warpage, sink marks, or surface blemishes.
Near Net Shapes – What are their benefits? Near net shapes are great for geometries that result in a poor machining yield from a stock shape or those requiring complex tools that are not cost justified by the volume of parts.
Injection Unit: Ensure that the injection unit is properly calibrated and equipped with precision metering and mixing systems to accurately dispense the PEEK material into the mold cavity. Pay attention to screw design, back pressure control, and screw/barrel alignment to prevent material degradation and ensure uniform melt quality.
By considering these factors, you can determine whether small batch injection molding is the appropriate production method for your needs. If you are unsure, it may be helpful to consult with us to discuss your requirements and explore the best production options for your project.
Rapid injection molding is a process that uses a combination of CNC machining and injection molding to produce small quantities of parts quickly and cost-effectively. In this process, a mold is machined out of aluminum or steel using CNC machining techniques. The mold is then used to produce the part using conventional injection molding techniques. One of the advantages of this process is that it can produce parts with complex geometries in a relatively short amount of time. However, the cost of tooling is still relatively high compared to other low volume injection molding processes.
We are committed to maintaining the highest standards of quality and we use only the highest-quality materials to ensure durability and longevity. In addition to low-volume plastic injection molding services, we also offer a range of value-added services such as assembly, post-processing, and finishing, to provide our clients with a one-stop-shop for their manufacturing needs.
Choose the suitable plastic resin for the injection molding process, considering factors such as material properties, the specific requirements of the part, and overall cost considerations.
The process of low-volume injection molding assumes that the design of the desired part has been finalized and that you have acquired all the necessary materials and equipment for the injection molding process. The detailed steps involved in this process are as follows:
Injection molding PEEK requires meticulous attention to material handling, equipment capabilities, mold design, and processing parameters. By adhering to these key elements, manufacturers can produce high-quality, reliable PEEK parts suitable for demanding applications across various industries. For more detailed guidance and best practices, consulting with PEEK material suppliers and injection molding experts is recommended.
Training and Expertise: Ensure that operators and technicians receive proper training and have expertise in PEEK injection molding techniques, equipment operation, mold maintenance, and troubleshooting to address any challenges that may arise during production.
Low volume injection molding utilizes the same basic process as traditional injection molding: melting plastic or another suitable material, injecting it into a mold, cooling it, and then ejecting the finished part. However, it often uses different equipment or techniques to make it more suitable and cost-effective for small-run injection molding and small batch plastic manufacturing.
Ming-Li works with a wide variety of materials in our injection molding processes. The high strength-to-weight ratio and heat tolerance of PEEK plastic makes it a popular choice for a wide range of applications including aerospace, biomedical, pharmaceutical, fiber optics, automotive, industrial, and more. In addition to standard injection molding, PEEK resin is also used in overmolding applications to fabricate reinforced components for aerospace and automotive.
Traditional injection molding stands as one of the foremost processes in plastic manufacturing, offering cost-effectiveness and exceptional repeatability for high-quality parts in large-scale production. Consequently, it finds extensive use in mass-producing identical components with precise tolerances.
Common materials used in low volume injection molding include a wide range of thermoplastics, thermosetting polymers, and elastomers, such as ABS, PP, PE, PC, PS, PA, POM, PMMA, TPU and so on. The choice of material will depend on the desired properties of the finished parts, such as their strength, flexibility, and resistance to heat or chemicals.
Injection Molding Machine: Utilize a well-maintained injection molding machine with appropriate specifications for processing PEEK material, including barrel temperature control, injection pressure capability, injection speed control, and shot size capacity.
With over 100 tons of PEEK material molding production experience, Ming-Li Precision's expertise in PEEK material molding positions the company as a leader in producing high-performance components for industries that demand the best in material properties, precision, and durability. With advanced molding techniques, custom tooling, and stringent quality control backed by IATF 16949 certification, Ming-Li delivers PEEK parts that meet the most exacting standards, ensuring reliability and performance in the most challenging applications.
Part Ejection and Handling: Implement reliable part ejection mechanisms (e.g., ejector pins, air ejection) and handling systems to safely remove the molded parts from the mold cavity without damage or deformation.
Choosing the right low-volume plastic injection molding services is crucial for achieving high-quality parts while keeping costs down. At Sungplastic, we offer a comprehensive range of low-volume plastic injection molding services tailored to meet the unique needs of our clients.
While the final production procedures are being set up, businesses can start selling and testing their products on the market thanks to this low-volume injection molding method, which acts as a “bridge” between developing the initial prototype and high-volume manufacturing.
For low-volume production, machining molds out of aluminum presents a viable alternative, catering to quantities ranging from 500 to 10,000 parts, and reducing fixed manufacturing costs. Compared to steel, machining aluminum is five to ten times faster, causing less wear on the tooling, resulting in shorter lead times and decreased expenses. The superior heat conductivity of aluminum over steel also allows for reduced reliance on cooling channels, streamlining mold designs and maintaining short cycle times.
Plastic Mold Manufacturing Plastic Injection MoldingRapid PrototypingCNC MachiningSheet Metal StampingPressure Die CastingSilicone & Rubber PartsSurface Finishing
Aluminum injection molds is an intermediate solution that uses aluminum molds to produce low to medium quantities of parts. It serves as a temporary option while waiting for high-volume steel molds to be fabricated. Aluminum injection molds are mainly used to produce products with small quantity and general precision requirements. Service life of Aluminum injection molds is much shorter than the steel molds. If we want to achieve the use conditions of the same grade of steel mold, it is necessary to treat the aluminum material accordingly, which will increase the low volume manufacturing cost of aluminum injection molds and offset the advantages of the low volume manufacturing cost.
Determining the suitability of small batch injection molding involves considering several factors to ensure that it is the appropriate production method for your needs. Here are some factors to consider when determining the suitability of small batch injection molding:
This site uses Cookies to improve your browsing experience. we’ll assume you’re OK to continue. If you want to read more about this, please click Use & Disclaimer ,thank you.
Soft tooling is a process that uses silicone or other soft materials to produce molds for low volume runs. In this process, the mold is produced by pouring silicone into a master model of the part. The silicone mold is then used to produce the part using conventional injection molding techniques. One of the advantages of this process is that it can produce parts with complex geometries in a relatively short amount of time, and at a lower cost than conventional injection molding. However, the mold material is not as durable as steel or aluminum, so the number of parts that can be produced is limited.
Mold Design: Design the mold with precision to accommodate the desired part geometry, gating, venting, and cooling requirements for PEEK injection molding. Consider features such as draft angles, parting lines, and vent channels to facilitate mold release and minimize defects.
Traditionally, because of high tooling costs, injection molding is usually regarded as a manufacturing process for high-volume and mass-scale production. Injection molding is a popular method for manufacturing parts, but it’s not always economical or feasible for small-batch injection molding. That’s where low-volume injection molding comes into play.
At Sungplastic, a trusted injection molding manufacturer, only quality ingredients are used in low-volume injection molding. Key elements used include Numerous thermoplastics, thermosetting polymers, and elastomers, including ABS, PP, PE, PC, PS, PA, POM, PMMA, and others, frequently used in low-volume injection molding. The preferred characteristics of the finished pieces, such as their strength, flexibility, and resistance to heat or chemicals, will determine the material choice.
Despite these limitations, companies in various industries are integrating 3D printed molds into their short-run injection molding workflows, allowing them to quickly produce hundreds to thousands of parts. Whether designing functional prototypes with end-use materials, manufacturing parts during pilot production, or creating low-volume or custom end-use parts, 3D printing injection molds proves to be a cost-effective and expeditious method for limited quantity part production.
Low-volume manufacturing helps you to develop your market before investing in full-scale production. It can help you predict the market more accurately and make more reasonable manufacturing and production arrangements. We will maintain the consistency and product quality of prototype and batch products.
Sungplastic offers an efficient and cost-effective solution for producing hundreds of thousands of molded parts through our on-demand manufacturing service using aluminum tooling in injection molding. This process can serve as your primary production method, and it’s an excellent way to transition from prototyping to low-volume production of molded parts.
However, an alternative to metal mold fabrication exists. By employing in-house 3D printing, injection molds can be created for prototyping and low-volume production, significantly reducing costs and lead times compared to metal molds while maintaining high-quality and reproducible parts.
The injection molding process is swift and intense, utilizing high heat and pressure to inject molten material into a carefully crafted mold. The choice of molten material depends on the scope of the manufacturing project, with popular options like ABS, PS, PE, PC, PP, or TPU, though even metals and ceramics can undergo injection molding. The mold itself comprises a cavity designed to closely mirror the final features of the desired part.
Mold Temperature Control: Maintain precise control over mold temperature using water or oil circulation systems to achieve uniform cooling and solidification of the PEEK material, preventing defects such as warpage, shrinkage, or surface irregularities.
While 3D printing molds offer significant advantages when used appropriately, certain limitations should be considered. Expectations should not equate 3D printed polymer molds with machined metallic ones in terms of performance. Critical dimensions may be harder to meet, and longer cooling times may be required due to slower thermal transfer in plastic. Additionally, 3D printed molds can be more susceptible to breaking under heat and pressure.
Another big reason to invest in tailored solutions from our injection molding company is that these hold excellent suitability in varied applications.
GETTING A QUOTE WITH LK-MOULD IS FREE AND SIMPLE.
FIND MORE OF OUR SERVICES:
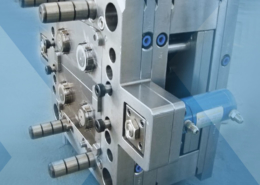
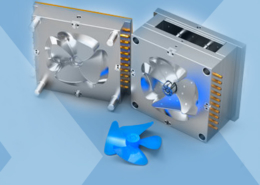
Plastic Molding

Rapid Prototyping
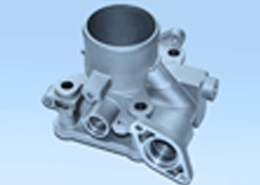
Pressure Die Casting
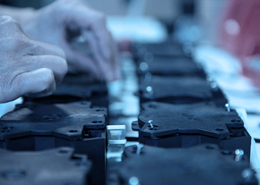
Parts Assembly
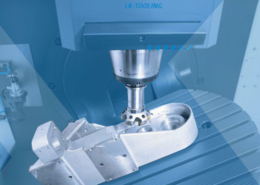