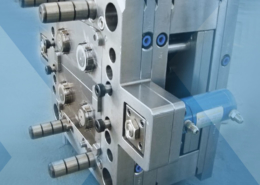
POLYSULFONE Injection Molding Solution - ppsu injection molding
Author:gly Date: 2024-10-15
What are the challenges and opportunities for the injection moulding industry in the future? How will Rosti respond to them?
As environmental concerns grow, the development and use of biodegradable plastics and bio-based materials will become increasingly important. Injection moulding technologies that can effectively process these materials will be crucial for the industry's sustainability efforts. Also, within the spectrum of Industry 4.0, the integration of sensors, connectivity, and data analytics into injection moulding machines can lead to smarter, more efficient production processes. Real-time monitoring and control can optimise cycle times, reduce waste, and improve part quality. Another process, liquid silicone rubber (LSR) moulding is gaining popularity due to the material's versatility, durability, and ability to withstand extreme temperatures. Advancements in LSR injection moulding technology can expand its applications, particularly in the medical and automotive industries.
These challenges, however, present many opportunities. Growth in emerging markets presents opportunities for expansion, as these regions may have increasing demand for consumer goods, medical devices, and automotive components. Another opportunity is the growing market for sustainable products and practices. Companies that can successfully integrate eco-friendly materials and processes have the opportunity to differentiate themselves and capture new business. In terms of advanced technologies, innovations in injection moulding technologies, such as smart factories and advanced robotics, offer opportunities to improve efficiency, reduce labour costs, and enhance product quality.
In all these, Rosti has been responding. For one, Rosti can continue to invest in sustainable practices, such as using green materials, optimising energy usage, and reducing waste. The company can also develop expertise in processing bioplastics and other eco-friendly materials. Rosti continues to invest in state-of-the-art machinery and adopt new technologies like 3D printing, automation, and Industry 4.0 solutions to improve efficiency and product quality. In the area of skilled workforce development, the company can focus on training and developing a skilled workforce to operate advanced equipment and adapt to new manufacturing processes. Rosti has also been investing in R&D to stay ahead of material innovations and develop new moulding techniques to meet the demands of various industries.
Asia has fast-growing downstream applications for injection moulding technologies. In automotive production, the demand for lightweight and durable components for fuel efficiency and emissions reduction is driving demand. In electronics, the ever growing consumer electronics market in Asia, with its need for small, high-precision parts, is a significant driver for the injection moulding industry. In the medical industry, there’s growing demand for high-quality, medical-grade plastic components due to the expanding healthcare sector in Asia. In the packaging industry, particularly for food and beverage products, there remains heavy reliance on injection moulded parts for containers, caps, and closures. Lastly, in the area of consumer goods, the production of a wide array of household items and personal gadgets also contributes to the demand for injection moulded parts.
Which injection moulding process and technology will have a significant impact on the production of plastic parts and products in the future?
What do you think of Rosti's position in the development of the Asian injection moulding industry? What are your core competencies?
Asian injection moulding sector also covers a diverse manufacturing base as the sector serves a wide range of industries, from electronics and automotive to medical and consumer goods. Technological advancement is also one characteristics as Asian injection moulders are increasingly adopting advanced technologies including automation, high-precision machinery, and smart manufacturing practices to enhance efficiency and quality. The region has a large and skilled workforce that is proficient in various injection moulding techniques and materials. Also, Asian countries are progressively implementing stricter environmental regulations, which are influencing the industry to adopt more sustainable practices and materials.
Technological adaption which means keeping pace with rapid advancements in technology, such as automation, Industry 4.0, and additive manufacturing, requires significant investment and a skilled workforce capable of operating and maintaining new machinery.
What are the characteristics of the injection moulding industry in Asia? Which downstream applications are positive? What new requirements are being asked by your customers in the region?
Each of these technologies addresses different needs and challenges within the plastics industry. Their adoption and advancement will depend on factors such as cost, material advancements, industry demand, and environmental regulations. Overall, the future development of the plastics industry will likely be shaped by a combination of these innovative injection moulding technologies, driving efficiency, sustainability, and the creation of more complex and high-value products.
Currently, Rosti has become the first injection moulding manufacturer in Asia to use Carbon's latest cutting-edge manufacturing capabilities. Thanks to better heat management, the Carbon M3 series printers have a higher yield rate per square foot under limited heat conditions and produce smoother parts than previous generations. In addition, the next generation DLS (Digital Photosynthesis) printing can reduce the difference in parts up to 50% - which means that the overall accuracy difference of engineering resins is smaller and production repeatability is higher. Whether it is small-scale production of complex parts that cannot be produced by injection moulding, or helping customers complete sample development within 72 hours, M3 will become an important cutting-edge technology for Rosti.
Mr. Williams: We have noticed some marked characteristics of the injection moulding sector in Asia. For one, there is rapid growth being experienced in Asia, particularly countries like China, India, and Southeast Asian nations. The rapid expansion of the injection moulding industry is fueled by growing domestic demand and the region's role as a manufacturing hub for global markets.
Another aspect is Rosti's commitment to sustainability aligns with the growing environmental regulations in Asia and the increasing demand for eco-friendly manufacturing practices. This commitment can serve as a differentiator and attract clients looking for green manufacturing partners. Also, Rosti's ability to offer customized solutions and adapt to client needs is a core competency that is particularly important as customers seek more personalised and flexible services. The company’s experience across various industries, such as automotive, electronics, consumer goods, and medical devices, allows it to bring a wealth of knowledge and best practices to the Asian injection moulding industry. With complex global supply chains, Rosti's expertise in supply chain management is critical, especially in Asia, where supply chain efficiency can significantly impact production timelines and costs.
Specific industry requirements present multiple opportunities. For one, the medical industry's need for high-precision, sterile, and complex components provides a growing market for specialised injection moulding services. In industries such as automotive and aerospace, there is a push for lightweight materials to improve fuel efficiency, and injection moulding can play a role in producing lightweight plastic parts that replace heavier metal components.
Mr. Williams: In order to ensure the successful development of new projects, advanced and efficient plastic processing technology is essential. Rosti has strong capabilities in R&D and production and is known for our many cutting-edge injection production technologies, such as IMD (in-mould film technology), IML (in-mould label injection technology), RHCM (high-speed high-temperature moulding technology), LSR injection technology, in mould holographic anti-counterfeiting technology, Microfluidics technology, Dye Penetration (thermal sublimation technology) and so on.
Other challenges pertain to the highly competitive environment as manufacturers from around the world aim to take a slice of the market share. Companies must continuously improve efficiency, reduce costs, and offer high-quality products to remain competitive. Customization demands must also be met as customers are increasingly demanding customized and complex parts. Meeting these demands requires flexible manufacturing processes and the ability to rapidly change production setups.
Mr. Williams: Rosti Integrated Manufacturing Solutions Co., Ltd., with its global presence and expertise in precision moulding, is well-positioned to play a significant role in the development of the Asian injection moulding industry. Rosti's investment in state-of-the-art machinery and technology positions it as a leader in producing high-quality, precision-moulded parts. This is crucial in an industry where the demand for precision and reliability is constantly increasing. Rosti's focus on innovation and research and development ensures that it stays ahead of industry trends and can meet the evolving demands of its customers, especially in a region where technological advancement is rapid.
Multi-component moulding (overmoulding) technology, which involves injecting multiple materials (including different types of plastics or a combination of plastic and metal) into a single mould, can produce more complex and functional parts and allows for material combinations that provide enhanced product properties, such as improved grip or aesthetics. In in-mould labeling and in-mould decoration, the techniques of placing labels or graphics inside the mould before the plastic is injected yields fully decorated part that comes directly out of the mould, eliminating the need for post-moulding labeling or painting. This can lead to cost savings and increased durability of the graphics.
As a global strategy, Rosti can leverage its global presence to tap into emerging markets while maintaining strong local market knowledge and relationships. It has been forming partnerships with material suppliers, technology providers, and customers to stay informed about industry trends and customer needs, leading to collaborative innovation. By addressing these challenges and capitalizing on opportunities, Rosti can position it for future success in a rapidly changing industry.
So given all these, new customer requirements emerge in terms of high precision and quality, faster turnaround times, customization, the use of eco-friendly materials, compliance with international standards and certification and cost-effective solutions to maintain competitiveness.
Mr. Williams: The injection moulding industry faces several challenges and opportunities as it adapts to evolving market demands, technological advancements, and environmental concerns. For instance, increasingly stringent environmental regulations regarding plastic use and waste management pose challenges for the industry. Companies must find ways to reduce their environmental footprint, such as by optimising energy consumption, minimising waste, and incorporating sustainable materials. Another is material innovations where the development of new materials, including bioplastics and composites, requires adjustments in processing techniques and equipment. Manufacturers must be willing to invest in R&D to adapt to these new materials.
Mr. Williams: Several emerging and evolving injection moulding technologies have the potential to significantly promote the development of the plastics industry in the future. The integration of 3D printing with traditional injection moulding can lead to rapid prototyping, reduced time-to-market, and the ability to produce complex geometries that are not possible with conventional methods. This technology can also be used to create moulds more quickly and cost-effectively.
In the injection moulding sector, Rosti has taken a special position due to its many innovations that have been benefiting plastics manufacturers. International Plastics News for Asia has been able to talk to Pat Williams, Senior Vice President of Rosti Asia, on the company’s recent achievements and moves to meet market demands.
GETTING A QUOTE WITH LK-MOULD IS FREE AND SIMPLE.
FIND MORE OF OUR SERVICES:
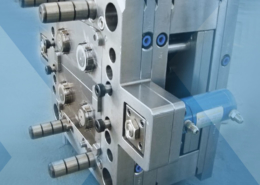
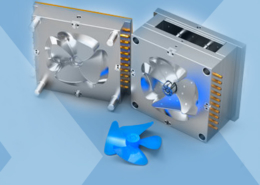
Plastic Molding

Rapid Prototyping
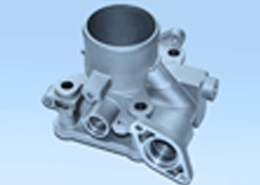
Pressure Die Casting
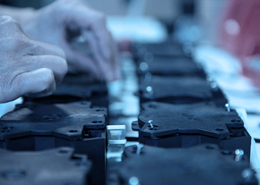
Parts Assembly
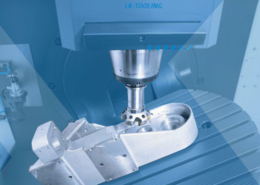