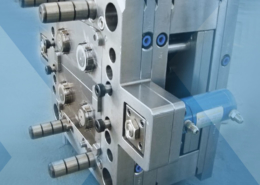
Polystyrene Trim Pros and Cons - The Tool Pit - molding polystyrene
Author:gly Date: 2024-10-15
Injection molding is highly cost-effective for large-scale production due to its rapid production cycle times and the ability to produce complex shapes without additional machining or finishing processes. The initial cost of creating a mold can be significant, but when spread over thousands or even millions of parts, the per-unit cost drops dramatically. This economy of scale makes injection molding ideal for producing POM parts for pumps and valves, where demand often extends into large quantities.
Chemical Resistance: POM is inherently resistant to many chemicals, making it an ideal choice for parts exposed to harsh substances.
Cost Savings: POM's ease of processing and material efficiency in injection molding can lower production costs, making high-performance pumps more affordable.
Homopolymer vs. Copolymer: POM is available in homopolymer and copolymer grades, each with distinct properties. Homopolymers offer higher mechanical strength and rigidity, while copolymers have better chemical resistance and lower melting points. The choice between them depends on the specific requirements of the pump or valve application.
Through precision injection molding processes, manufacturers can leverage POM's properties to produce parts that meet tight tolerances, withstand harsh operating environments, and deliver reliable performance over their lifespan. The case studies underscore the material's potential to solve specific operational challenges, improving outcomes such as extended equipment life, reduced maintenance requirements, and increased system efficiency.
POM vs. Nylon (PA): Although Nylon has good wear resistance and flexibility, POM offers better dimensional stability and lower moisture absorption, which is crucial for precision components.
Centrifugal pumps are widely used for water supply, wastewater management, and various industrial processes. POM injection molded parts, such as impellers and casings, offer several advantages in these applications. The material's high strength and rigidity improve the pump's efficiency by maintaining precise impeller dimensions and clearances, even in abrasive or corrosive fluids. Additionally, POM's excellent dimensional stability and resistance to creep ensure that pump components retain their shape and performance characteristics over time, leading to reliable and consistent operation.
Polyoxymethylene (POM), widely known as Acetal or by brand names such as Delrin, is a semi-crystalline engineering plastic characterized by its high mechanical strength, dimensional stability, and excellent wear resistance. These properties make POM ideal for precision parts in high-performance applications, particularly in manufacturing pump and valve components where reliability and durability are paramount.
Wall Thickness: Uniform wall thickness is crucial to prevent warping, sink marks, and voids. POM parts should maintain consistent wall thickness throughout the design to ensure uniform cooling and reduce stress concentrations.
Reduced Maintenance: POM's durability and resistance to wear and chemicals reduce the frequency and cost of pump maintenance.
Longer Lifespan: POM's inherent strength and stability extend the service life of pumps, ensuring they continue to operate efficiently for more extended periods.
Our design engineers are experienced in mold making and the injection molding process. Plastimold will save you time and money by optimizing your parts for manufacturing. All tools designed and built by Plastimold are backed by a lifetime mold guarantee. We build precision Aluminum and Steel tools to meet your production requirements.
Leak-proof Performance: The precision achievable with POM injection molding ensures that valve components fit perfectly, minimizing the risk of leaks and improving system efficiency.
Chemical Compatibility: Selecting a POM grade with appropriate chemical resistance for parts exposed to aggressive chemicals is crucial. It ensures that the pump or valve maintains its integrity and functionality over time.
Diaphragm pumps, which handle a wide range of fluids, including aggressive chemicals, benefit significantly from POM's chemical resistance. The material's toughness and flexibility make it an excellent choice for diaphragm pump membranes and valves, which must withstand cyclic stresses and exposure to harsh substances. POM's resilience contributes to the pump's reliability and maintenance-free operation, which is crucial in process industries such as chemical manufacturing and water treatment.
Superior Wear Resistance: With a low coefficient of friction, POM parts exhibit outstanding wear resistance, essential for moving components in pumps and valves.
Understanding the properties of POM and how it compares to other engineering plastics is crucial for selecting suitable materials for pump and valve applications. Its unique combination of strength, stability, and resistance makes POM a standout choice for components that require precision, durability, and reliability. In the following sections, we will explore the advantages of using injection molding to produce POM parts and delve into specific applications within pumps and valves, highlighting how POM contributes to the efficiency and reliability of these essential industrial tools.
Challenge: A leading manufacturer of hydraulic gear pumps faced issues with wear and tear in their metal-based pump gears, leading to frequent maintenance and downtime.
Outcome: The redesigned POM check valves achieved a 100% seal under all operational conditions, eliminating backflow issues and significantly improving the water treatment system's efficiency and safety.
Ribs and Gussets: To enhance the structural integrity of POM parts without increasing wall thickness, designers can incorporate ribs and gussets. These features should be carefully designed to prevent sink marks and ensure adequate material flow.
POM vs. Polycarbonate (PC): PC offers superior impact resistance and transparency, but POM wins in mechanical strength, fatigue resistance, and lower moisture absorption, which is essential for mechanical components.
100% Fulfillment of your product. Adhesive bonding, mechanical assembly, hot staking, and ultrasonic welding. Plastimold also offers custom package design and production. Bulk packed items are packaged with care so they arrive to you without any damage during transit.
Chemical and Wear Resistance: POM's inherent chemical resistance makes it suitable for valves in aggressive environments, while its wear resistance ensures long-term reliability.
Additives and Fillers: The performance of POM parts can be tailored with additives and fillers to enhance properties such as UV resistance, lubricity, and strength. For instance, adding glass fibers can increase the part's strength and stiffness, while PTFE additives can improve wear resistance.
Check valves rely on their ability to prevent backflow in systems, requiring components that combine precision, durability, and minimal wear. POM's injection molded parts, such as valve bodies and sealing elements, offer the necessary precision and wear resistance to ensure these valves function reliably over time. The material's excellent flow characteristics during molding allow for creation of complex shapes, such as those found in spring-loaded or swing-check valves, without compromising performance or quality.
POM distinguishes itself with a unique set of physical and mechanical properties that are highly valued in industrial applications:
Solution: The manufacturer optimized performance by redesigning the check valve components with POM, focusing on the valve's sealing mechanism and spring action for precise opening and closing. Injection molding allowed the production of complex part geometries that improved the valve's responsiveness to pressure changes.
POM vs. PET: While PET has excellent dimensional stability and strength, POM typically outperforms wear resistance and ease of machining.
When designing parts for injection molding with Polyoxymethylene (POM), several critical considerations must be addressed to optimize the final components' performance, durability, and manufacturability. This is particularly true for pump and valve parts, where precision and reliability are paramount. This section outlines critical design considerations for POM injection molded parts, ensuring successful integration into pump and valve applications.
Polyoxymethylene is renowned for its high mechanical strength, excellent dimensional stability, and outstanding wear resistance, essential for the smooth operation of pumps and valves in various industrial settings. These components are the lifelines of systems in sectors such as water treatment, chemical processing, and automotive manufacturing, where failure is not an option. Thus, selecting a material that can withstand harsh conditions and maintain performance over time is critical.
Mold Flow Analysis: This analysis predicts how the POM material will fill the mold cavities, calm, and solidify. Mold flow analysis is essential for identifying potential issues such as air traps, weld lines, or short shots, enabling adjustments to the mold design or processing parameters to ensure high-quality parts.
Looking for the best plastic injection molding companies in the USA? Plastimold Products is the one stop shop injection molding supplier and plastic part manufacturer you've been looking for. We specialize in the design and manufacturing of custom injection molded parts at the highest quality and lowest cost possible. As an ISO9001:2015 certified and registered company, our goal is to consistently provide quality parts, meet customer expectations, and adhere to regulatory requirements. All tools manufactured with Plastimold are guaranteed for life.
Plastics are pivotal in industrial manufacturing due to their versatility, durability, and efficiency. Among these materials, Polyoxymethylene (POM), also known as Acetal, is a preferred choice for fabricating crucial components in pumps and valves. POM's unique blend of mechanical properties and cost-effectiveness makes it an ideal candidate for applications demanding precision, longevity, and resilience.
Exploring real-world applications and success stories of POM injection molded parts in the pump and valve industry illustrates the material's versatility. It showcases its impact on enhancing product performance and operational efficiency. This section highlights a few case studies where POM has been instrumental in solving engineering challenges, leading to improved outcomes for manufacturers and end-users alike.
The automated nature of the injection molding process ensures a high level of consistency across all produced parts. Advanced quality control measures can be integrated into production, allowing real-time monitoring and adjustments. This consistency is critical for pump and valve components, where each part must meet stringent performance criteria to ensure the reliability and longevity of the final product.
Injection molding is a cornerstone technology in manufacturing POM parts, particularly for pump and valve components where precision, efficiency, and quality are non-negotiable. This process offers several advantages, making it an attractive choice for producing large-scale engineering plastic parts.
Solution: The valve manufacturer selected a copolymer POM grade with enhanced chemical resistance for the valve bodies and internal components. The parts were designed with attention to detail in stress distribution and chemical exposure, utilizing POM's capability to be injection molded into complex shapes while maintaining integrity.
Finite Element Analysis (FEA): Early in the design process, FEA can be utilized to predict how POM parts will behave under various load conditions. This simulation helps identify potential failure points and areas of high stress, allowing for design optimization before tooling begins.
Solution: The adoption of POM for manufacturing the ball valve seats and seals was chosen to leverage POM's excellent dimensional stability and resistance to thermal expansion. The material's low friction coefficient also minimized wear on moving parts.
Looking for the best plastic injection molding companies in the USA? Plastimold Products is the one stop shop injection molding supplier and plastic part manufacturer you've been looking for. We specialize in the design and manufacturing of custom injection molded parts at the highest quality and lowest cost possible
While many engineering plastics are available, POM often stands out for specific applications due to its balanced properties:
Operating Temperature Range: With a continuous-use temperature range of -40 °C to 120°C (- 40°F to 248°F), POM can perform in a wide range of environmental conditions without degradation.
Injection molding can produce complex shapes and designs in a single step, eliminating the need for multiple manufacturing processes. This capability, combined with the fast cycle times of the injection molding process, allows manufacturers to turn designs into finished products quickly. Moreover, the versatility of injection molding machines and the wide range of POM grades available mean that manufacturers can easily adjust to produce parts for different applications within the pump and valve sectors.
High Mechanical Strength: POM has a tensile strength of 63 MPa (9100 psi), enabling it to withstand significant mechanical stress.
Challenge: Solenoid valves used in chemical processing plants were failing prematurely due to corrosion from harsh chemicals, causing leaks and operational disruptions.
Outcome: The switch to POM resulted in a significant reduction in wear, extending the lifespan of the pumps by 30%. Additionally, the POM gears contributed to quieter operation due to their inherent damping properties, enhancing user experience.
Designing POM injection molded parts with these considerations ensures that the final components meet the stringent requirements of pumps and valves. By adhering to DFM principles, selecting the appropriate grade of POM, and utilizing stress analysis and simulation, manufacturers can achieve parts that offer superior performance, longevity, and reliability in demanding applications. This comprehensive approach to design enhances the functionality of pumps and valves and contributes to the overall efficiency and success of the systems they comprise.
Cost-effectiveness: The efficiency of the injection molding process, combined with POM's material properties, results in cost savings in manufacturing and maintenance, making high-quality valves more accessible.
The production of POM parts often utilizes injection molding, a manufacturing technique celebrated for its ability to produce complex shapes with high precision and repeatability. This process is particularly suited for creating high-volume batches of parts, making it a cost-effective solution for industries operating on a large scale. Injection molding's efficiency and versatility in handling POM material allow for the design and production of pump and valve components that meet strict industry standards and tolerances.
Outcome: Using POM in ball valves doubled the valves' service life and reduced maintenance intervals, offering substantial cost savings and operational improvements for the cooling systems.
Design Flexibility: POM's versatility in injection molding opens possibilities for innovative valve designs, accommodating complex geometries and integrated functions without sacrificing performance.
Our goal is to put you in the best position to succeed. If you're successful, we're successful. The Plastimold team has a strong reputation of doing whatever it takes to get the job done on time, and with zero defects. See why we are the top plastic injection molding companies in Florida.
After years of frustration with overseas manufacturing, the Plastimold team was able to help us out of a bad situation and successfully launch our new product line!
The injection molding process is designed to use material efficiently, minimizing waste. Excess material can often be recycled and reused in subsequent production runs, reducing the environmental impact and material costs. This efficiency and the ability to recycle material that is not biodegradable are particularly beneficial for POM, contributing to a more sustainable manufacturing process.
Enhanced Performance: The precision manufacturing achievable with POM injection molding leads to better fitting parts, minimizing leaks, and improving efficiency.
One of the most compelling benefits of injection molding is its ability to produce parts with incredibly tight tolerances, typically up to ±0.005 inches. This precision is crucial for pump and valve parts, where even minor deviations can lead to leaks, malfunctions, or complete system failures. The repeatability of the injection molding process ensures that each part is virtually identical to the last, maintaining consistent quality across high-volume production runs.
Solution: The company transitioned to using POM injection molded gears, capitalizing on POM's high wear resistance and mechanical strength. The redesign incorporated POM's precise molding capabilities to achieve tight tolerances and smooth surface finishes, essential for the pump's efficiency.
Good Chemical Resistance: POM is resistant to many solvents, hydrocarbons, and neutral chemicals, making it suitable for use in chemically aggressive environments.
Pumps are critical components in a wide array of industrial, commercial, and residential systems, facilitating the movement of fluids in various applications. In pump designs, Polyoxymethylene (POM) injection molded parts underscore the material's adaptability and performance under demanding conditions. This section delves into the specific applications of POM in different types of pumps, highlighting its contributions to enhancing efficiency, durability, and functionality.
Solenoid valves, which control the flow of fluids electronically, benefit from POM's electrical insulation properties, making it a preferred material for the valve body and internal components. POM's strength and precision manufacturing through injection molding contribute to the valve's responsive operation and longevity, even in applications requiring frequent cycling. Additionally, POM's chemical resistance is a significant advantage in solenoid valves used in corrosive environments, where material compatibility is crucial for maintaining system integrity.
Gear pumps, known for their efficiency in transferring viscous fluids, rely heavily on their components' precision and wear resistance. With its excellent dimensional stability and superior wear resistance, POM is ideally suited for manufacturing these pumps' intricate gears and housings. The material's low coefficient of friction and good lubricity ensure smooth operation, minimal wear, and extended service life, even under continuous use. It makes POM a preferred choice for gear pump components, particularly in applications like hydraulic systems, where reliability and performance are paramount.
Outcome: Using copolymer POM extended the valve's operational life by over 50% in aggressive chemical environments. The improved durability and reliability of the valves significantly reduced maintenance costs and downtime for the processing plants.
The exploration of Polyoxymethylene (POM) injection molded parts in pump and valve applications highlights the material's indispensable role in enhancing these critical components' performance, durability, and efficiency. With its exceptional mechanical strength, dimensional stability, and chemical resistance, POM provides a solution to many of the engineering challenges faced in the design and operation of pumps and valves across various industries.
Challenge: Ball valves in industrial cooling systems were degrading quickly due to thermal cycling and pressure fluctuations, necessitating frequent replacements.
Challenge: A water treatment facility was experiencing efficiency losses due to check valves not performing optimally under varying pressure conditions, leading to backflow and contamination risks.
In summary, the advantages of using injection molding to produce POM parts are clear. The process offers unparalleled precision, cost-efficiency for high-volume orders, sustainability through material efficiency, and the speed and versatility needed to meet the demanding requirements of the pump and valve industry. These benefits make injection molding an essential manufacturing process for creating high-quality, reliable POM components fundamental to industrial systems worldwide.
Temperature Considerations: POM components used in environments with extreme temperatures should be designed with the material's thermal expansion and resistance in mind. It ensures that dimensional stability is maintained across the part's operational temperature range.
Plastimold’s prototyping services include CNC and 3D printed mechanics, PCB samples, and assembly for testing and short run production. Build minimum viable product (MVP) prototypes to show off and test your product early in development.
Valves, essential for controlling the flow of fluids in systems across numerous industries, demand materials that offer precision, durability, and compatibility with various media. Polyoxymethylene (POM) stands out for its excellent mechanical properties and chemical resistance, making it an ideal choice for valve components. This section explores the specific roles of POM injection molded parts in various types of valves, emphasizing how POM enhances their performance and reliability.
Excellent Dimensional Stability: Its low moisture absorption rate ensures minimal dimensional changes, maintaining tight tolerances even in humid environments.
Ball valves are prized for their ability to provide secure, leak-proof operation with a simple quarter-turn motion. POM is particularly suited for the seats and seals of ball valves, where its low friction coefficient ensures smooth operation, and its excellent wear resistance prolongs the valve's lifespan. Furthermore, POM's dimensional stability and tight tolerance capabilities via injection molding mean these critical parts maintain their integrity and sealing capabilities even under fluctuating temperatures and pressures, ensuring reliable operation in water systems, chemical processing, and pneumatic applications.
In conclusion, POM injection molded parts play a crucial role in the design and function of various pumps. By leveraging POM's unique material properties, manufacturers can achieve superior pump performance, durability, and efficiency, fulfilling the needs of diverse applications from industrial processing to everyday water management. It underscores the importance of material selection in pump design and POM's significant advantages in this context.
Plastimold is an ISO 9001:2015 and ISO 13485 certified quality plastic injection molding company in Florida, but goes above and beyond ISO requirements. Our processes ensure that quality plastic products are delivered on time and meet your companies specific requirements. We are also AS9100 compliant, FDA registered, maintain an active CAGE Code, registered with the ATF as a FFL, and frequently test product to UL, CE, and FCC standards with third party partners. Learn More...
Draft Angles: Incorporating draft angles in the design of POM parts facilitates easier ejection from the mold, reducing the risk of damage to the part. A minimum draft angle of 1° for smooth surfaces and 3° for textured surfaces is recommended.
To sum up, applying POM injection molded parts in valves highlights the material's critical role in ensuring the efficiency, reliability, and durability of fluid control systems. Whether in ball, solenoid, or check valves, POM's exceptional properties support the stringent requirements of modern industrial, commercial, and residential applications. By choosing POM for valve components, manufacturers can achieve superior performance, meeting the demands of diverse operating environments and contributing to the overall effectiveness of fluid control systems.
Over the past 22 years, we've produced billions of plastic injection molded parts for a global customer base out of our injection molding Florida location. Our innovative approach to injection molding takes advantage of the latest technology to compete and beat overseas competition. All of our plastic parts are Made in America. If you already have molds built, Plastimold can retrofit molds into our machines and begin molding your product. If not, we can develop a new design or analyze your existing design , build your mold, and manufacture your injection molded parts at our Florida factory. Contact Us now for a FREE project analysis.
GETTING A QUOTE WITH LK-MOULD IS FREE AND SIMPLE.
FIND MORE OF OUR SERVICES:
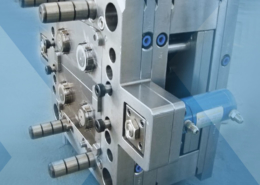
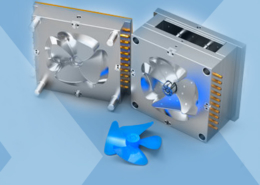
Plastic Molding

Rapid Prototyping
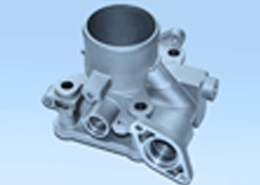
Pressure Die Casting
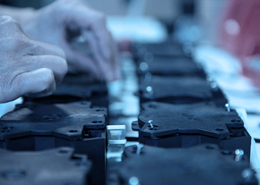
Parts Assembly
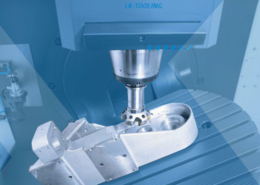