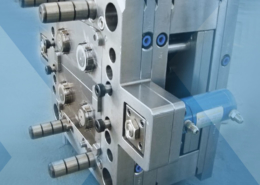
Polypropylene Injection Moulding - pp injection
Author:gly Date: 2024-10-15
If you have a sales inquiry, an RFQ / RFP or if you have any questions, please fill out the form below or email us directly at contactus@sussexim.com
Access a wide breadth of capabilities through our highly vetted network.
Accelerate development with instant quotes, expert DFM, and automated production updates.
By signing up, you agree to our Terms of Use and Privacy Policy. We may use the info you submit to contact you and use data from third parties to personalize your experience.
Overmolding is a form of injection molding that molds a polymer over a substrate. It eliminates the need for assembly after molding. Overmolding is used to produce handles on surgical instruments, but it can also be used in medical products without any metal parts — like silicones or thermoplastic elastomers (TPE) overmolded onto thermoplastic substrates.
By signing up, you agree to our Terms of Use and Privacy Policy. We may use the info you submit to contact you and use data from third parties to personalize your experience.
There are numerous benefits of multi-shot injection molding. Providing the simplest and most cost-effective way to produce parts with multiple materials, as the process only requires one machine cycle, multi-shot injection molding delivers reduced costs and needs for labor. The efficient process will also produce higher output levels compared to other manufacturing processes.
Two-shot, or multi-shot injection molding, is a highly efficient manufacturing process in which molded parts from two or more different materials are combined to build a single product.
By signing up, you agree to our Terms of Use and Privacy Policy. We may use the info you submit to contact you and use data from third parties to personalize your experience.
HCR’s higher viscosity makes this material more challenging to process, and HCR injection molding is generally more complex than LSR injection molding. Still, HCR can achieve better overall properties than LSR rubber. Depending on a part’s geometry, however, high shear conditions in the mold can cause shrink rates to vary — which underscores the importance of proper tool design and an experienced manufacturing partner. Applications for HCR silicone injection molding include gaskets and O-rings for medical devices.
Create your free Fictiv account and request an injection molding quote today — we mold complex parts at ridiculous speeds!
To enhance all of our injection molding expertise, Sussex IM has complete service offerings including, design for manufacture, dedicated 3PL capabilities and inventory management to round out our full-solutions service. From start to finish, we are the comprehensive partner to ensure success – that’s the Sussex Solution.
Metal injection molding (MIM) mixes powdered metal with a thermoplastic binder and heats this material so that the metal grains bond to the thermoplastic. The material is then heated again and injected into a mold to create the part. After the part is ejected, the thermoplastic binder is removed. The next step is sintering, a heat treatment process that subjects the part to high temperature and pressure. Sintering compacts any loose material, and this fusion results in a net-shape or near-net-shape part. Depending on the injection molded product, post-sintering operations may be required.
Material selection is always complicated, and given the recent shortages and price increases, finding your first choice can be nearly impossible, meaning material replacement is a growing need. At Sussex IM, our knowledgeable team is happy to help guide you through the material selection process.
MIM supports the high-volume production of medical parts with complex shapes in various sizes, and with superior strength and an excellent surface finish. This form of medical injection molding also provides a cost-effective alternative to CNC machining for parts made of difficult-to-machine metals such as stainless steels, cobalt-chromium alloys, and titanium alloys. Importantly, the dimensions and end-use properties of metal injection molded parts are comparable to those of wrought and cast materials. Applications include surgical instruments and implants, both of which use stainless steel.
If you have a sales inquiry, an RFQ / RFP or if you have any questions, please fill out the form below or email us directly at contactus@sussexim.com
The two halves of the mold remain clamped during curing, a process that averages 30 seconds with LSRs. By contrast, cure times for HCR, or high-consistency silicone rubber (see the next section) last five minutes or longer, especially if the rubber uses a peroxide curing agent. Injection-molded LSR can also be platinum-cured for greater optical clarity, tensile strength, and tear strength. Importantly, platinum-cured silicones have fewer extractables, aka compounds that can leach out of the material. With higher purity and faster cycle times, platinum-cured LSRs are used in high-volume medical applications like spacers for asthma inhalers.
When examining the end-use, it is vital to understand if the device will require higher durability, protecting against being exposed to fluctuating temperatures and the resilience required. For medical applications, considerations of FDA regulations the product will need to meet, especially if the device will be inserted into the human body or in contact with bodily fluids, will be critical.
In addition to conventional plastic injection molding, there are six main types of injection molding used in medical devices:
At Sussex IM, we recognize the nuances necessary for medical injection molding. To continuously serve the increased demand for medical manufacturing and new product development, we have strengthened our capabilities to support medical injection molding with our ISO Class 8 clean room.
By signing up, you agree to our Terms of Use and Privacy Policy. We may use the info you submit to contact you and use data from third parties to personalize your experience.
Overmolding isn’t just about layering one material on top of the other, however. Chemical bonds form at the molecular level and are a function of how well the overmold material wets the substrate. Mechanical bonds depend on the physical geometry at the interface of the substrate and the overmold. Two-shot molding, or double-shot molding, is a two-step continuous process that first molds a substrate, then over molds that substrate with a different material. Pick-and-place molding is used mainly for prototyping and for low-volume production.
For example, a medical device housing would require a material that is both durable and aesthetically pleasing. Two-shot injection molding can also offer an end-product that features a rigid plastic housing with a soft-touch grip.
The necessary double injection is carried out on one machine, built and programmed to perform two injections in one cycle. While the process can also occur with two or more molds in multiple injection molding machines, using one mold and one injection molding machine ensures reduced handling and guaranteed cleanliness. The single press method is also the lowest cost.
At Sussex IM, we strive to solve our customers’ problems in the most efficient way possible. Backed by our proven injection molding expertise, one of the ways that we deliver solutions is through two-shot or multi-shot injection molding. As your injection molding experts, Sussex IM is always looking for new ways to address our customers’ needs. To maintain this responsibility, we have continued to expand our medical injection molding capabilities with the addition of our new Class 8 clean room.
Do you need medical injection molding for prototyping, low-volume, or high-volume production? A good plan and skilled production partner are critical to avoid the added injection molding costs and risks that come with inadequate drying or improper processing methods.
Because thin wall injection molding can provide significant cost savings, it’s often used with high-volume production. Potential applications for thin wall injection molding include small enclosures for medical devices. And Fictiv offers cost-effective steel molds for medical device prototype development and low-volume manufacturing — an ideal solution for medical device designers looking for an alternative to 3D printing to ensure that the material used for functional samples can be used for high-volume production.
Create high quality custom mechanicals with precision and accuracy.
Like thin wall injection molding, gas-assisted injection molding reduces the amount of plastic required, decreases cycle times, and creates significant material cost savings. Gas-assist plastic injection molding also improves part appearance by reducing sink marks, blemishes, warpage, and distortion — the gas packs out the resin removing blemishes as the plastic solidifies. Also, because molding pressures are lower, there’s less residual stress on parts and less wear on molds.
Gas-assisted injection molding is a low-pressure plastic injection molding process that heats plastic, injects it into the mold, then injects pressurized nitrogen or carbon dioxide gas. In turn, the gas pushes the molten plastic into the mold’s extremities and produces thicker walls with hollow sections. When molding is complete, the gas is vented and the parts are removed. Typically, this process is used for plastic parts that have large surface areas, and require detailed textures and superior surface quality.
As the case with any manufacturing process, material selection is a critical part. In multi-shot injection molding, the selection process becomes even more vital as the resin not only has to be a fit for the end-use application, but the materials have to be a fit, chemically, with each other. Otherwise, bonding will not occur. Another way to overcome this challenge is through part design, mechanically bonding the two materials via internal channels and interlocking features. Typically, to aid in this decision-making process, a material compatibility chart is available to determine which resins may work together for this particular kind of injection molding.
By signing up, you agree to our Terms of Use and Privacy Policy. We may use the info you submit to contact you and use data from third parties to personalize your experience.
With the combination of different properties into one part, two-shot injection molding also provides value through improved aesthetics, functionality and quality. While any market will enjoy the benefits of combining materials to improve part integrity and greater visual appeal, as this process improves color and eliminates painting in secondary operations, the medical market has several applications where this manufacturing process is unmatched.
If you have a medical device application, multi-shot injection molding can benefit your needs and the advantages this manufacturing capability provides.
Thin wall injection molding produces thin, lightweight parts for reduced material costs and faster cycle times. As a medical molding process, it’s typically used for small, complex parts that require a high degree of precision. The thinness of the wall is important because the size of the part limits how thin the wall can be. Typically, injection molded parts with a wall thickness of less than 1mm are considered to be thin-walled.
Our trained employees ensure your parts will be delivered on time and to spec.
By signing up, you agree to our Terms of Use and Privacy Policy. We may use the info you submit to contact you and use data from third parties to personalize your experience.
LSR injection molding is used with liquid silicone rubber (LSR), a two-component elastomer that requires curing — a chemical process that crosslinks polymer chains — to achieve the material’s end-use properties. Typically, the components for LSR injection molding come in a 5-gallon pail or a 55-gallon drum. They are poured into a static mixer and fed into the injection unit, where additional mixing occurs. The injection screw then pushes forward the shot, or the amount of material, that’s needed to fill the mold.
This versatile manufacturing process produces complicated molded parts that may have different colors, components or materials. Usually, those factors are limited to two different types, but with customization of the molding machine and mold construction, a part could utilize up to three materials. Additionally, the use of multiple injection molding machines can create an even larger combination of materials.
By signing up, you agree to our Terms of Use and Privacy Policy. We may use the info you submit to contact you and use data from third parties to personalize your experience.
Beyond the ability to seamlessly create multi-color or multi-material parts, two-shot injection molding also is a flexible process that allows for added creativity and complexity in part design, opening up part complexity possibilities. The unique capabilities of two-shot injection molding are especially beneficial for the medical market as medical device designs continue to advance and have become increasingly intricate.
By signing up, you agree to our Terms of Use and Privacy Policy. We may use the info you submit to contact you and use data from third parties to personalize your experience.
With the recent increased demand for medical products, multi-shot injection molding is as popular as ever. The multi-shot injection molding manufacturing technique offers several favorable qualities that appeal to the medical market including, the opportunity for increased sterilization, molding precision and cycle time.
We exist to eliminate bottlenecks in new product development by integrating the people, processes, and platform you need to source custom parts.
By signing up, you agree to our Terms of Use and Privacy Policy. We may use the info you submit to contact you and use data from third parties to personalize your experience.
Fictiv has the global manufacturing network and production experts you need to get quality medical injection molded parts, no matter how complex your designs. And we have the skills and know-how to support you from part design through prototyping and production.
HCR injection molding is used with high-consistency silicone rubber (HCR), or heat-cured silicone rubber. Typically, this injection molding process involves heating a gum-like raw material and injecting it into a mold under high pressure. The injection screw preheats the gum rubber to reduce its viscosity, or resistance to flow. The silicone then fills the mold cavity completely, and the preheating at the beginning of the molding cycle helps to fill the cavity more rapidly.
This article describes each of these methods, and if you’re looking for information about the best way to design injection molded parts for medical devices, check out our design guide!
Sussex IM is a family owned, custom injection molder centrally located in Sussex, Wisconsin. Proud of our Midwestern roots we pride ourselves on providing solutions to meet our customers needs. We look forward to hearing from you.
We exist to eliminate bottlenecks in new product development by integrating the people, processes, and platform you need to source custom parts.
Injection molding for medical devices can use plastics, thermoplastic elastomers (TPE), silicones, metals, or composite materials. There are many types of injection moldable plastics, but medical device designers often choose polypropylene, polyethylene, polystyrene, or polyetheretherketone (PEEK), depending on the application. Silicone elastomers also offer a choice of materials and combine chemical stability with support for sterilization. Metals provide strength and can resist microbial growth while also supporting medical injection molding.
GETTING A QUOTE WITH LK-MOULD IS FREE AND SIMPLE.
FIND MORE OF OUR SERVICES:
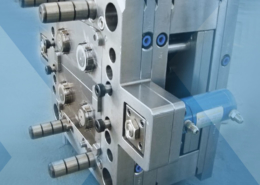
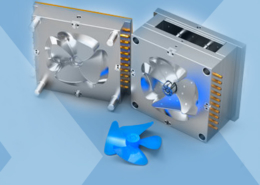
Plastic Molding

Rapid Prototyping
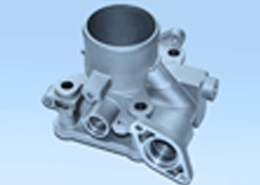
Pressure Die Casting
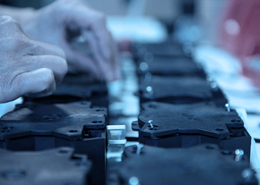
Parts Assembly
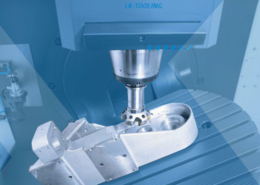