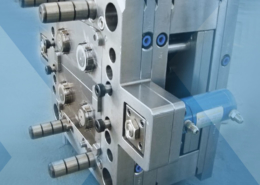
POLYPROPYLENE INJECTION MOULDING - injection polypropylene
Author:gly Date: 2024-10-15
After sufficient cooling time has passed, ejection takes place to release the finished part from the mold. Ejection mechanisms vary depending on part geometry and complexity but often involve pins or ejector plates that push against specific areas of the molded part to facilitate its removal from within intricate cavities.
The cost of a plastic injection mold is mainly driven by the part geometry, the material being molded, and the complexity of the mold.
When it comes to injection molding, there is no single “right” answer when it comes to finding the best value. However, there are a few tips and tricks that can help you save on injection molding costs. The first tip is to work with an experienced and reputable company. This will ensure that you get the best possible price for your project. The second tip is to be realistic about your project’s design and budget. Injection molding can be a complex and time-consuming process, so it’s important to have a clear understanding of your project’s requirements before getting started. By following these tips, you can be sure that you’re getting the best value for your injection molding project.
There are a few things to keep in mind when designing self-mating parts for injection molding. First, the part must be designed so that it can be easily removed from the mold. Second, the part must be designed so that it can be assembled and disassembled easily. Third, the part must be designed so that it can mate with other parts without any gaps or other problems.
When it comes to injection molding, the design of self-mating parts is an important consideration. This is because self-mating parts must be able to fit together perfectly in order to function properly. Injection molding is a process that can create very precise parts, so it is important to take advantage of this when designing self-mating parts.
In order to produce a high quality product, it is important to get rid of unnecessary features and simplify the design injection molding.
In short run plastic molding, efficiency is paramount. By utilizing transfer molds, manufacturers can optimize production cycles and reduce overall costs. The ability to produce smaller quantities with minimal setup time allows businesses to quickly respond to market demands and adapt their product offerings accordingly.
Mold costs can vary greatly, depending on a number of factors. A plastic mold can cost anywhere from $1,000 to $10,000. The exact cost depends on a number of factors, including the size and complexity of the mold, the material it is made from, and the company that makes it.
The duration of a small batch plastic molding project depends on several factors such as complexity, quantity required, and current workload at the manufacturing facility. However, on average, it can take anywhere from a few days to a few weeks to complete.
The steel,size and complexity of the mold will have the biggest impact on the price, but other factors like the material and the turnaround time can also affect the cost.
In contrast, Small Batch Plastic Molding significantly reduces tooling costs. Since smaller quantities are produced, businesses can opt for less expensive molds or even utilize rapid prototyping techniques such as 3D printing for initial iterations. This allows companies to test the market without committing significant financial resources upfront.
Cooling plays a vital role as it allows the plastic to take on its intended shape while maintaining structural integrity. Different cooling methods can be utilized depending on factors such as part complexity and material properties. Common cooling methods include air cooling, water cooling, or even specialized cooling channels incorporated within complex molds.
The cost of injection mold can vary based on a number of factors, but the median cost is around $3,000. The price range can be as low as $1,000 or as high as $10,000, so it’s important to get quotes from multiple companies before making a decision.
Absolutely! Small batch plastic molding is an excellent choice for prototyping. It allows you to quickly produce functional prototypes and iterate on designs before committing to mass production. This helps save time and money in the development process.
In the plastics industry,modifying and reusing molds is a common practice. It can be done with either new or existing molds and can save companies time and money.
The size and complexity of the mold are perhaps the most important factors in determining its cost. A simple mold for a small object may only cost a few hundred dollars, while a more complex mold for a larger object could cost several thousand.
Short run plastic molding is a manufacturing process that specializes in producing smaller quantities of plastic parts efficiently. Unlike large-scale production methods, such as mass production or high-volume injection molding, short run plastic molding is ideal for businesses that require smaller quantities or have limited budgets.
On-demand production can save businesses money in the long run by reducing inventory costs and eliminating the delivery time. In addition, on-demand production can help businesses respond quickly to changes in customer demand.
By utilizing low volume injection molding, businesses can meet the demands of these niche markets without compromising profitability.
One of the key benefits of Small Batch Plastic Molding china is its ability to reduce time-to-market by swiftly producing small quantities of plastic parts. Unlike traditional manufacturing methods that require lengthy setup times and large minimum order quantities, short run injection molding enables businesses to rapidly prototype and produce smaller batches.
It is also necessary to take into consideration how the plastic mold will be used. If it is for a one-time project, then a smaller size may be more cost effective. On the other hand, if the mold will be used multiple times, then a larger size may be necessary in order to avoid having to replace it frequently.
By embracing this flexibility, companies can ensure that their products meet the highest standards of quality and functionality while also satisfying customer preferences.
There are several reasons why a company might choose to modify a mold. In some cases, the original mold was not designed correctly and needs to be modified to fix the problem. Other times, a company may want to change the design of the part that is being produced.
Transfer molds play a crucial role in the short run plastic molding process by facilitating the transfer of molten plastic into the mold cavity. These molds are designed to ensure precise and accurate filling of the mold cavities, resulting in high-quality finished products.
As the world increasingly moves away from traditional manufacturing methods, on-demand production is becoming a more popular option for businesses. Plastic molding is one area where on-demand production can be a great option for businesses. There are many benefits to choosing on-demand production for your plastic molding needs, including a reasonable price.
Estimating injection molding costs requires understanding the diverse factors comprising the total expenditures. Simplifying part geometries, standardizing tooling, and optimizing processes offer significant savings over a program lifespan. Collaboration between product developers and molders, combined with emerging technologies, ensures cost-effective, quality plastic part production.
However, small batch injection molds may not be suitable for every project. The initial investment in tooling can be significant, making it more viable for higher volume production runs. Design modifications during production are more challenging and time-consuming compared to other plastic molding methods.
There are a few ways to eliminate undercuts, but the best way is to design the part so that it can be molded without them. This can be done by using symmetrical geometry, designing bigger draft angles into the part, or using core pins.
One advantage of small batch plastic molding is its versatility. It allows manufacturers to choose from different processes based on factors like part complexity, material selection, and desired surface finish. This approach offers greater flexibility in terms of design modifications during production runs.
Shorter lead times associated with Small Batch Plastic Molding enable businesses to respond faster to changing market demands. They can quickly adjust their product offerings or introduce new designs without significant delays, giving them a competitive edge in dynamic industries.
In conclusion, small batch plastic molding offers numerous benefits for businesses looking to produce low volumes of plastic parts. It provides flexibility, cost-effectiveness, and faster turnaround times compared to traditional injection molding methods. With short run injection molding, companies can quickly iterate and refine their designs without committing to large production runs.
Ultimately, the decision of what size plastic mold to use should be based on what is most likely to produce the desired results at a reasonable price. Taking into account all of these factors will help ensure that the final product is exactly what is needed.
Gone are the days of waiting for large-scale production runs. With small batch plastic molding, you can produce a series of high-quality products in no time. Say goodbye to lengthy lead times and hello to quick turnaround times. This innovative approach combines speed, precision, and affordability like never before.
If you’re looking for a way to save on production costs, you may want to consider using overmolding plastic mold. Overmolding is a process that allows you to mold two or more different materials together, which can help reduce waste and eliminate the need for separate assembly processes. Additionally, overmolding can improve the strength and durability of your products.
One of the key advantages of using transfer molds is their versatility. They are suitable for both short run and long run production. This means that manufacturers can seamlessly transition from producing small batches to larger volumes without having to invest in new molds or equipment.
Moreover, by minimizing tooling costs through short runs, businesses can allocate their budget towards other critical areas such as marketing, research and development, or expanding their product line.
When the machine is ready, it applies high pressure to inject molten plastic into the mold cavity. This pressure ensures that every detail of the mold design is accurately replicated in the final product. Once injected, cooling mechanisms are activated to rapidly cool down and solidify the molten plastic within seconds or minutes.
Injection molding is a process that was invented in the late 1800s, and it has come a long way since then. The first plastic injection molding machine was created in 1872 by John Wesley Hyatt, who was trying to find a way to make billiard balls without using ivory. Ivory was becoming increasingly expensive and difficult to obtain, so Hyatt came up with the idea of using a mold to create the balls from celluloid instead.
Finally, the company that makes the mold can also affect its cost. Typically, an experienced manufacturer that makes molds for many industries and types of products will have experience and be able to make the mold in less time, which can bring down your cost.
Small Batch Plastic Injection Molding China is particularly valuable for niche markets that require specialized products in smaller quantities. In such cases, traditional volume production methods may not be cost-effective due to high setup costs and minimum order requirements. Small batch plastic molding bridges this gap by enabling manufacturers to produce limited quantities economically.
So why wait? Experience the benefits of small batch plastic molding today and take your manufacturing game to the next level!
The price of a multi-cavity mold can vary depending on the size and complexity of the mold. However, in general,multi-cavity molds are more expensive than single-cavity molds.
Furthermore, transfer molds allow for efficient cooling during the solidification process. Proper cooling is essential for achieving optimal mechanical properties and minimizing defects like warping or shrinkage. With well-designed cooling systems incorporated into the transfer mold design, manufacturers can achieve faster cycle times and maintain consistent part quality.
Transfer molds offer flexibility. Manufacturers can choose from a wide range of plastics based on their specific requirements, including thermoplastics like polypropylene (PP), polyethylene (PE), polystyrene (PS), and more. This flexibility enables businesses to select materials that best suit their product’s functionality, durability, and aesthetic appeal.
The mold constitutes a significant upfront fixed cost, so minimizing its expense is crucial. Factors influencing mold costs include:
Even small optimizations add up significantly over production lifetimes. An experienced molder provides valuable guidance.
Simpler molds with standardized, interchangeable parts cost substantially less. Partnering with an experienced mold maker is vital for optimizing these tradeoffs.
Furthermore, exploring the applications for low volume injection molding reveals its versatility across various industries. From prototyping and product testing to limited edition manufacturing and spare part production, small batch plastic molding caters to a wide range of needs. Whether you’re in the automotive, electronics, or consumer goods sector, this manufacturing method can meet your specific requirements.
One of the significant advantages of small batch plastic molding in China is its flexibility. Design changes can be made relatively easily during the production process compared to traditional injection molds. However, it’s important to consult with your manufacturer regarding any modifications to ensure smooth execution.
Both methods cater to similar requirements but differ in terms of cost and lead time. Let’s delve deeper into the comparison between small batch plastic molding and small batch injection molds to better understand their nuances and determine which option suits specific project requirements.
This accelerated production process provides several advantages. First, it allows companies to test their products in the market sooner, gaining valuable customer feedback early on. This feedback can then be used to make necessary design improvements or modifications before committing to larger production runs.
Are you looking for a cost-effective manufacturing solution for low volume production? Look no further! Small batch plastic molding China is here to revolutionize your production process. By utilizing a specialized injection molding process, this method offers an efficient and affordable way to bring your new product designs to life. Whether you need prototypes or functional prototypes for testing purposes, small batch plastic molding has got you covered.
Understanding the process of plastic injection molding is crucial in grasping the intricacies of small batch production. From mold design and material selection to the actual manufacturing process, each step plays a vital role in achieving high-quality end products.
When it comes to the cost of a plastic injection mold, there is no definitive answer. The reason for this is because there are so many variables that can affect the price. Some of these variables include:
However, there are some limitations associated with small batch plastic molding. The initial setup costs can be relatively high due to the need for creating custom molds or tooling for each project. Furthermore, as the number of parts produced increases within a single run, unit costs tend to decrease.
Molten plastic is injected into a mold cavity under high pressure. This injection molding process is widely used in the manufacturing industry to create various plastic products. The process begins with the design of the mold, which determines the shape and features of the final product.
One significant advantage of small batch injection molding china is its ability to support customization and personalization of products. In today’s market, consumers seek products that cater to their specific needs and preferences. Low volume injection molding allows manufacturers to produce smaller quantities of highly customized products efficiently.
To make the most out of small batch plastic molding opportunities, it is essential to consider partnering with reliable manufacturers who possess expertise in this field. Ensuring that they adhere to industry standards and have a proven track record will help guarantee satisfactory results.
As the years went by, and more companies began to specialize in mold building, the prices began to come down. Today, the cost of a plastic injection mold is much lower than it was in the past.
Understanding how to accurately estimate and minimize injection molding costs is key for creating viable, cost-optimized plastic products. This comprehensive guide covers the factors comprising total molding costs and advice for effective budgeting.
If the mold is made of a more expensive material like titanium, then the price will increase as well. Also, if the mold is being produced in large quantities, then it will be less expensive per unit. The lead time should also be considered.
This will minimize the potential for defects and improve the overall efficiency of the production process. There are a few key things to keep in mind when simplifying a design for injection molding:1. Remove any features that are not absolutely essential to the function or aesthetics of the final product.
The steel material the mold is made from also plays a role in its cost. Molds can be made from various metals, plastics, or even composites. Molds are generally more expensive when made of more expensive steel, like S136, which costs three times as much as P20.
Small Batch Plastic Molding offers numerous benefits for businesses looking to quickly produce small quantities of plastic parts. This manufacturing process allows for flexibility in design modifications and iterations, while also offering lower tooling costs compared to high volume production. Let’s delve into the advantages of short run injection molding in more detail.
The use of transfer molds also contributes to enhanced precision and accuracy in the manufacturing process. The molten plastic is transferred directly into the mold cavity through channels or sprues, ensuring consistent filling throughout each part produced. This results in uniform dimensions and improved product quality.
In recent years, advancements such as 3D printing have influenced mold design and prototyping stages of plastic injection molding. This technology allows for quicker iterations and validation of mold designs before committing to expensive metal molds. It has revolutionized the industry by reducing lead times and costs associated with mold development.
In conclusion, if you’re looking for a cost-effective way to produce low volumes of plastic parts without compromising quality or speed-to-market, small batch plastic molding is an excellent solution. Embrace this innovative approach and unlock endless possibilities for your business today!
Another significant advantage of Small Batch Plastic Molding is the flexibility it offers in terms of design modifications and iterations. With traditional manufacturing methods, making changes to a product’s design after tooling has been completed can be costly and time-consuming.
However, with Small Batch Plastic Molding, businesses have the freedom to experiment with different designs and make adjustments as needed without incurring substantial expenses. This iterative approach allows for rapid prototyping and refinement until an optimal design is achieved.
Using a multi-cavity mold can be more expensive than using a single-cavity mold, but it can also be faster and more efficient. If you need a large number of parts, or if your part is complex and has many features, a multi-cavity mold may be the best option.
Generally, the cost of a plastic injection mold starts at around $3,000. This is for a simple mold that is relatively small and does not have any intricate designs. If the mold is larger or more complex, the price will increase.
Small Batch Plastic Molding offers a cost-effective alternative to high volume production. Traditional manufacturing methods typically require substantial upfront investments in molds and tooling, which can be prohibitive for businesses with limited budgets or uncertain market demand.
This level of customization not only enhances the overall customer experience but also sets businesses apart from their competitors in niche markets with limited demand.
The cost of a plastic injection mold has changed significantly over time. In the early days of injection molding, the price of a mold was very high. This was due to the fact that the process was new and there were not many companies that knew how to build molds.
Injection molding enables mass-producing plastic parts with consistency, detail, and efficiency. While a highly cost-effective process, developing an accurate budget requires evaluating numerous cost components. We’ll explore fixed and variable costs, quoting considerations, design strategies, tooling factors, and advice for minimizing overall expenditures without sacrificing part quality.
Small batch plastic molding and small batch injection molds are two terms often used interchangeably in the manufacturing industry. However, it is important to understand that while small batch plastic molding refers to the overall process, small batch injection molds specifically focus on the tooling aspect.
The molder then factors in their production capabilities, overhead, and desired margins when preparing a detailed quote. Leave buffer for potential changes in the design process.
There are several benefits to choosing an on-demand production option for your plastic mold needs. Perhaps the most obvious benefit is that it allows you to only produce what you need, when you need it. This can help save on costs associated with inventory and storage. Additionally, on-demand production can help reduce lead times and improve flexibility in your supply chain.
A core cavity approach to injection molding is a process whereby a mold is created with an inner core that forms the shape of the desired product. The molten plastic is then injected into the mold and allowed to cool, forming the product.
Yes, small batch plastic molding is capable of producing complex parts with intricate features. With advanced mold design and manufacturing techniques, manufacturers can achieve high levels of precision and detail in the final products.
This approach has several benefits over traditional injection molding methods, including increased accuracy and precision, as well as decreased production time and costs.
A wide range of materials can be utilized in small batch plastic molding, including various types of thermoplastics such as ABS, polypropylene, polycarbonate, and nylon. The choice of material depends on the specific requirements of your project.
Injection molding undercuts can be a difficult and costly problem to fix. They are caused by the mold not being able to release the part from the mold cavity. Undercuts can also lead to the material not flowing properly into the mold cavity.
Small batch plastic molding, also known as low volume injection molding, has a wide range of applications across various industries. It offers unique benefits for producing medical devices, automotive parts, and consumer electronics. Let’s delve into the different ways these industries benefit from this specialized manufacturing process.
Using small batch injection molds offers several advantages compared to other methods. Firstly, it enables faster production cycles since the mold can be set up quickly and efficiently once it has been fabricated. Secondly, this approach provides excellent repeatability and accuracy in part production, ensuring consistent quality throughout the manufacturing process.
One reason why the cost of a plastic injection mold has decreased is because of advancements in technology. In the past, molds had to be built by hand which was very time consuming and expensive. Today, molds can be built using CNC machines which are much faster and less expensive.
With all of these factors affecting the cost, it can be difficult to determine what is a “reasonable” price for a plastic injection mold. However, there are some general guidelines that can be followed.
The entire small batch plastic molding process relies heavily on precise control over temperature, pressure, and timing parameters throughout each step. Any deviation from the ideal conditions can result in defects or inconsistencies in the final product. Manufacturers continuously monitor and adjust these parameters to ensure high-quality output.
On the other hand, small batch injection molds in China focus primarily on the tooling aspect of manufacturing plastic parts. Injection molds are created specifically for each project and are designed to produce consistent and precise parts through an automated process.
Small batch plastic molding involves producing a limited quantity of plastic parts using various manufacturing techniques such as injection molding, blow molding, or rotational molding. This method is ideal for projects with lower volume demands, typically ranging from a few hundred pieces up to a few thousand.
When considering the size of a plastic mold, it is important to take into account the reasonable price for the project. Depending on the desired outcome, the size of the mold may need to be changed in order to accommodate for different parts.
When comparing small batch vs. small batch injection molds, it becomes evident that short run molds offer significant advantages. They are more affordable and require less lead time compared to regular molds. This makes them an ideal choice for businesses with tight budgets or time constraints.
The actual plastic injection molding starts with the injection molding machine. These industrial machines are specifically designed for this purpose and come in different sizes depending on the volume of production required. They consist of a hopper where plastic pellets are fed into, a heating unit that melts the plastic, and an injection mechanism that pushes molten plastic into the mold cavity.
Once the mold design is finalized, tooling is prepared to create an injection mold. This involves using metal molds that are carefully crafted to match the desired product specifications. The precision and quality of these molds play a crucial role in ensuring consistent and accurate production.
In general, small and simple molds can start at around $1,000, while larger and more complex molds can cost tens of thousands of dollars. The price of the mold is just a small part of the overall cost of manufacturing a product though. It is important to factor in the cost of materials, labor, packaging, and shipping when determining the final price of a product.
GETTING A QUOTE WITH LK-MOULD IS FREE AND SIMPLE.
FIND MORE OF OUR SERVICES:
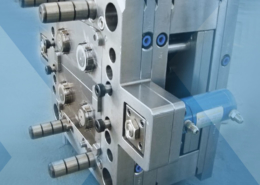
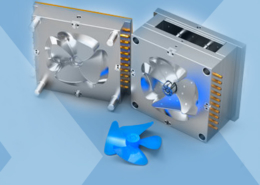
Plastic Molding

Rapid Prototyping
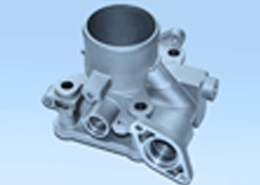
Pressure Die Casting
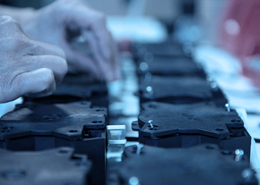
Parts Assembly
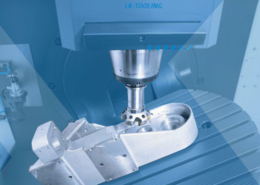