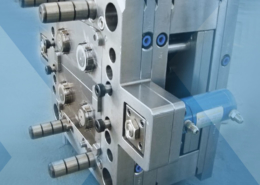
Polyethylene Injection Molding | PE Plastic - high density polyethylene injectio
Author:gly Date: 2024-10-15
The major deviation from the plans is the temperature control. In the original design, you have to watch a dial thermometer while fiddling with a bimetal thermostat. Going with something more modern is well worth the effort.
The injection lever (D) pivots on a½”-diameter steel rod (E). I beefed this up by drilling larger holes in the frame and turning some steel bushings (F) on my lathe to support the rod. The bushings also keep the lever centered over the injection piston (G).
This plastic injection molding supplier is known for creatively enhancing the required products. B&C Plastics is based in Brisbane, Australia, and they have access to a vast range of machinery and an extensive workforce. Their team creates edgy plastic injection molding designs that appeal to the market to accumulate the best results.
There are lots of variables that have to be taken into consideration when choosing the right injection molding supplier for your business. Here are five key steps you can take to ensure you make the best decision for your company:
They serve a variety of industries such as agriculture, engineering industries, healthcare, warehousing, logistics, automotive, mining, railway, and construction.
Now I’m making test-tube caps for my science experiments. I started out by drawing a sketch for the mold in my project notebook. The test tubes are 16mm in diameter so I started with that dimension and chose arbitrary dimensions for the height of the cap and thickness of the plastic. I added a lip to the cap to make it easier to pull off.
The services of Sneddon & Kingston Plastic are plastic product design, prototyping, injection molding, mold design, and mold manufacturing. The injection moulded plastic parts produced are mainly used in automobiles, packaging, medical, and building construction.
The proficient team has got its hands on the 3D CAD software, which allows them to have a practical insight into creative plastic design. They closely examine the usability of the finished product before its manufacture and estimate the possible modifications.
A Plus Plastics, an Australian-based injection molding supplier, has adequate machinery to manufacture every sized product. The brand mostly deals in bulk orders for the warehousing, medical, automotive industry, and agriculture industries.
Having worked with some of the most prestigious brands like Telstra, Ergon, Hutchinsons & Lendlease, they’ve gained the reliability of industry leaders. B&C Plastics usually works on contract-based projects that involve the customization of products to turn the market dynamics.
Amec Plastics has been manufacturing a diverse range of products for food packaging, medical industry, caps, closures, and everyday household appliances. It is a great addition to their esteem that Amec Plastics has been approved by HAAPC for more than 10 years now!
With its head office at Adeline, South Australia, Lincoln Plastics has been dispatching plastic molds since 1959. Their experience counts for 63 years in the industry, being a skilled producers of various quality plastic products.
Australian Injection Moulding shop have been shipping their elegant designed products worldwide! To go heads up with their leading competitors like China and the USA, Australian plastics industry are bringing advanced machinery and larger manufacturing space.
Australia has a large market that supplies all countries in Oceania. Compared to the countries in its region, it has some of the best injection molding companies.
Once you know what you’re looking for, you can start doing some research on potential suppliers. Look at their websites, read customer reviews, Ask their injection molding process, and see if they have any industry awards or accreditations. This will give you a good idea of which companies are reputable and which ones you should avoid.
Jim Hannon retired recently after 39 years as an electrical engineer for Rockwell Collins. Now he can concentrate on amateur science projects and on making things in his woodworking and machine shop — especially things that are too expensive to buy, or that just don’t exist.
Are you searching for the best custom injection molding supplier? Then look no further because W&S plastics is an ideal and trusted company when it comes to customized solutions. The company has been in the business for 44 years, situated at Moorebank NSW 2170, Australia.
The manufacturing capabilities of A Plus plastic range from the production of small and complex plastic components, all the way up to large injection molded parts, with the ability to producing parts weighing up to 8kg using A variety of resin moulds.
The companies in our list that have been in the business for more than 30 years can be trusted for their knowledge and skill set! By providing a dedicated team to focus on completing each bulk order, they have retained the interests of each client that comes across their venture. Undoubtedly, Australian suppliers have set a benchmark for their offshore competitors in every aspect, and a good percentage of clients can be seen shifting towards their manufacturing units.
Although we are a factory from China, our founder graduated from the University of Denmark, and he has 5 years of working experience in The UK, which ensures that we can complete any way of communication with customers in the UK. We usually confirm product details with customers quickly by video conference for urgent orders.
With their growing offshore client base, they successfully managed to establish another unit in Johor, Malaysia. This venture was set up in 2016, and since then, W&S Plastics Pty Ltd has been domestically serving there as well. It can be deemed that this brand puts extraordinary efforts into designing and produce creative products that appeal to a target audience.
Through Aria’s online quotation system (app.madearia.com), you can quickly get a quote for your injection moulding project.
Fewer brands are equipped with a stunning facility like Amec plastics. To provide the best service to their clients, they operate 24×7 so that all their shipments can be met at the earliest! The brand is located at Burleigh Heads and was established in 1987.
By following these steps, you can be sure that you’ll find the best injection molding supplier for your business. And once you’ve found a good supplier, you can focus on growing your business and achieving your goals.
Their main focus is to produce creative prototypes that meet the client’s requirements without disrupting their budget. Due to its skilled workforce, A Plus Plastics delivers durable and highly efficient plastics that are valued highly.
Sometimes there’s a tool you want to buy, but you can’t justify the cost. In that case, why not make it? For me, a plastic injection molding machine fell into that category — and it turns out they’re not hard to make.
Plastic injection molding has been around since thermoplastics were invented. It’s a great way to make many copies of a part quickly, and what I like best is that it’s easy to reuse old plastic objects to make new ones.
Being an engineer, I couldn’t resist making improvements. The plans call for a 1″×1½”×4″ piece of cold rolled steel for the heater block (A), where the plastic is heated before being injected into the mold. I used a leftover piece of 1″×2″ hot rolled steel instead. The wider block allowed me to add a second cartridge heater (B), so my machine warms up quicker and can get hotter.
Advantages: Design Support, Strong supply chain, Factory Price, Instant Quote Online, On-demand Order, Plus plastics manufacturing capabilities
To try it out I cut some ⅜”-wide strips of polyethylene from an old plastic tote lid, set the controller to 380°F and fed the plastic strips into the cylinder. After the cylinder is filled with sufficient molten plastic, the mold is placed under the nozzle and raised into place. (If the mold in put in place while the plastic is being loaded some of the plastic will dribble out of the nozzle and clog the sprue of the mold.)
Gavin Leo is a technical writer at Aria with 8 years of experience in Engineering, He proficient in machining characteristics and surface finish process of various materials. and participated in the development of more than 100complex injection molding and CNC machining projects. He is passionate about sharing his knowledge and experience.
Once the sketch is made, I’m off to the machine shop to cut some metal. Two little blocks of 6061 aluminum make up the halves of the mold. First, two 0.124″ holes are drilled through both blocks to hold guide pins that will ensure the mold halves are properly aligned. Two ⅛” guide pins are pressed into one half of the mold, and the other holes are reamed out just slightly to 0.126″. Then the parts are machined on the lathe to form the cavity for the cap. Finally a sprue hole is drilled and countersunk.
Once you’ve considered all of the factors above, you should be ready to make your final decision. Choose the supplier that you feel offers the best combination of price, services, and support for your specific needs.
I used an inexpensive digital temperature controller (H) from Auber Instruments (auberins.com). These controllers use PID (proportional-integral-derivative) feedback control and can bring the temperature up to the exact setting quickly without any overshoot. I mounted mine in a separate enclosure and added a solid-state relay to handle the high-power heaters. A thermocouple sensor (I) comes with the controller; it screws into a tapped hole in the heater block near the nozzle (J). It is really nice to be able to set the desired temperature on the controller, turn on the heaters and watch the temperature rapidly climb to the setting.
Looking for a top-quality injection molding supplier in Australia? Look no further! In this article, we will discuss the 10 best suppliers in the country. Each of these companies offers excellent products and services, so you can be sure to find the right one for your needs. Keep reading to learn more about each supplier and discover which one is the best fit for your business.
This project should cost between $100 and $200. It depends a lot on where the metal is purchased. I had a lot of the metal already, left over from other projects. Try to find a friendly local iron dealer, rather than getting the metal online or from a hardware store. They’ll often let you pick through their cut-off pile and sell it for almost scrap prices.
Jim Hannon retired recently after 39 years as an electrical engineer for Rockwell Collins. Now he can concentrate on amateur science projects and on making things in his woodworking and machine shop — especially things that are too expensive to buy, or that just don’t exist.
My favorite fastener for projects is Allen head cap screws so I used #10-24 cap screws instead of 1/4-20 bolts to mount the heater block and guide block to the frame. They’re at least as strong as ungraded 1/4-20 bolts and should conduct a little less heat from the heater block to the frame.
Our websites use cookies to improve your browsing experience. Some of these are essential for the basic functionalities of our websites. In addition, we use third-party cookies to help us analyze and understand usage. These will be stored in your browser only with your consent and you have the option to opt-out. Your choice here will be recorded for all Make.co Websites.
This experienced injection molding supplier is known for its qualified team of designers who work with creative ideas to construct prototypes. Following the latest trends, the technical team keeps themselves updated about the customers’ changing interests and demands. Henceforth, the prototypes are made with a precise understanding of the target audience.
Don Gilchrist founded Precimax Plastics in 1970. With over 35 employees and 19 plastic injection moulding machines, It is one of the largest Plastics manufacturers in Adelaide.
Once you’ve narrowed down your list of potential suppliers, the next step is to get quotes from each one. This will give you a good idea of who is offering the best price for the services you need. Be sure to also ask about any hidden fees or charges that may not be included in the initial quote.
Their injection molding equipment ranges from 60 tons to 900 tons and can produce plastic products ranging from 1.5 grams to 6.5 kilograms. Their excellent work and experience have been acknowledged globally, and thus they continue to create several plastic products irrespective of their weight and size.
The stunning feature of Edplas Australia Pty Ltd is that they create unique and stunning plastic items in bulk, irrespective of the size. Numerous heavy machinery for injection molding has been installed at their manufacturing units. This allows the technical team to work on diverse products without worrying about their size.
I wanted to make solid plastic parts for some of my amateur science experiments. There are a number of ways to make things out of plastic, each with its advantages and disadvantages. Often just cutting raw material to the desired shape works best. Some plastics can be cast by pouring a liquid resin with hardener into a mold (see “DIY Rotocaster,” Make: Volume 41). Vacuum forming works well for making things out of thin sheets of plastic (see “Kitchen Floor Vacuum Former,” Make: Volume 11). I considered making a 3D printer, but for the few plastic parts I envisioned needing, it wasn’t worth the time and money.
You didn’t read it wrong, Dongguan is not in the United Kingdom, but there is a reason why I placed Aria Manufacturing Limited on the list. Having great success in over a decade with millions in sales, I had to use us as an example of a great injection moulding manufacturer.
For now, I’m limited to simple molds I can make with a lathe or mill, but I’m adding CNC capability to my lathe, and thinking about a CNC router. That would open all sorts of possibilities.
So I built an injection molder based on the plans in Vincent R. Gingery’s book Secrets of Building a Plastic Injection Molding Machine. David Gingery could be considered a forerunner of the Maker Movement — he and his son Vincent have written a whole series of books on building tools for the machine shop.
I wouldn’t recommend this project for someone who has no metalworking experience. I made full use of my machine shop: mill drill, lathe, stick welder, horizontal band saw, ½” reamer, and various taps. You can get by with a drill press and various hand tools. I welded most of the assembly together but the book calls for screws, except for one weld (which you could have someone else do if you don’t have a welder).
Jim Hannon retired recently after 39 years as an electrical engineer for Rockwell Collins. Now he can concentrate on amateur science projects and on making things in his woodworking and machine shop — especially things that are too expensive to buy, or that just don’t exist.
Precimax can support young entrepreneurial businesses to realize their dreams by assisting in the manufacturing process from design, processing, molding, assembly, testing, and packaging.
Serving the clients since 1980, Edplas Australia is a master of homemade, agriculture, and healthcare products. The company is based in Peakhurst, Australia, and its business remains a family-owned venture.
They each have their areas of expertise. If you’re looking for a reliable supplier in Australia, check them out! Thanks for reading! I hope this was helpful. before you selected a supplier, you can get a free quote for reference from a Chinese injection molding company ( Aria Manufacturing Limited). You will get an instant quotes for your injection moulding project by submitting your design drawings on Aria’s online quotation platform.
I compiled a list of the top 10 injection molding suppliers in Australia based on thorough research. Being in the industry for many years now, I’m experienced enough to find the best.
By producing quality injection molding products for the last 60 years, Sneddon & Kingston Plastic has become a top choice of clients! The brand is based in Preston, Melbourne, and its wide range of services keeps a check on complete satisfaction.
I tried out the cap mold with some of the tote lid plastic I used for the test pellets. The caps turned out nice, but they were a bit stiff and difficult to put on. A more flexible plastic was needed. Then I made some caps with LDPE (low-density polyethylene) lids from oatmeal boxes. The caps made with the LDPE work just fine.
Using the machine is easy. The book recommends making a test mold that will make two ½”-diameter pellets of plastic. These pellets are then used to feed the machine when making real parts.
These heavily engineered robotics have been installed to precisely match the number of products that need to be manufactured. Depending upon the clients, the size and count of an item could vary, so the expert team at Supa-Peg provides prototyping, plastic injection molding, Dye-casting, and post-sales support for every client!
The frame (C) in the Gingery design is mostly angle and flat iron held together with bolts and nuts, but two connections needed to be welded. So I decided to weld most of the frame and avoid drilling so many bolt holes.
Supa-Peg Australia was established in 1975 and is currently situated in Yatala, Queensland. Their main production considers outdoor industry and involves the manufacturing of fencing, agriculture & defense items. The units of Supa-Peg are equipped with diverse machinery.
(One modification I tried didn’t work out so well. The heater block and guide block need to be spaced out from the frame a bit, to isolate the hot heater from the frame and put the parts into proper alignment with the piston. The plans call for washers, but I tried using some leftover fiber ceramic insulation sheet instead. It was too soft — it allowed the heater block and guide block to move out of alignment, preventing the piston from operating smoothly.)
In addition to price, you also need to compare the different services that each supplier offers. What kind of support do they provide? What is their turnaround time? Do they offer any guarantees? The answers to these questions can help you narrow down your list even further.
Before you even start looking at different suppliers, you need to first sit down and define your specific needs. What kind of products do you need to be produced? What is the volume that you need? What are your deadlines? Once you have a good understanding of your own needs, you can start looking for suppliers who will be a good fit.
Learn more: Secrets of Building a Plastic Injection Molding Machine by Vincent R. Gingery (David J. Gingery Publishing, 1997), ISBN 1-878087-19-3
GETTING A QUOTE WITH LK-MOULD IS FREE AND SIMPLE.
FIND MORE OF OUR SERVICES:
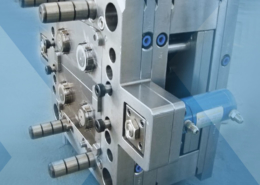
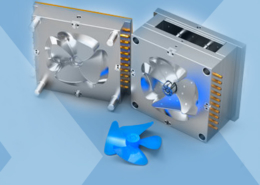
Plastic Molding

Rapid Prototyping
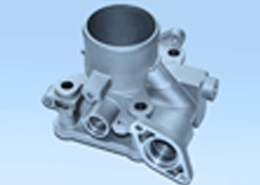
Pressure Die Casting
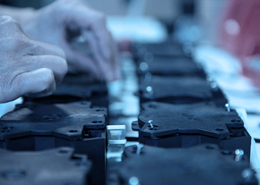
Parts Assembly
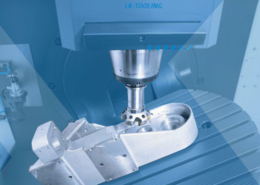