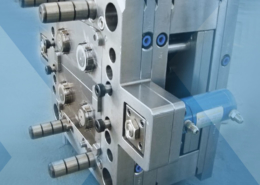
Polycarbonates(PC) injection molding properties and ... - polycarbonate injectio
Author:gly Date: 2024-10-15
Polyethylene is used in applications ranging for films, tubes, plastic parts, laminates, etc. in several markets (packaging, automotive, electrical, etc.). In fact, the majority of plastic products are made of polyethylene plastic injection mouldings. This is including containers, bottles, bags, and toys. Therefore, it is now one of the most widely used thermoplastic materials.
How safe are food-grade materials? Dive into the details and find out how ARRK Asia’s innovative approaches provide reliable solutions.
Obtaining the desired plastic product with ARRK Asia will provide a wide range of options to design for manufacturing with Injection molding in Malaysia, tooling in Singapore, or die casting in Malaysia processes. Each process must adhere to the specifications of your project to be assured of the desired end result. We are capable of providing thin-wall injection molding, double-shot molding, over-molding, insert molding, and transparent and high-polished molding.
What is the process of CNC machining? At ARRK Asia, we are experts in the benefits and challenges of this industrial method. Keep reading to learn more!
In other companies, you might find several roadblocks, such as design data modification without proper communication, making the product unusable, or forcing you to revise and delay plans due to unexpected outcomes. Besides not having the product right, components could take up longer than expected to complete, and if that is not bad enough, they have limited materials available.
The most advanced and efficient way of mass-producing plastic parts is through injection moulding. This process involves injecting plastic materials molten by heat into a steel mould, and then cooling and solidifying them. Products of complex shapes and various sizes can be produced with the following advantages:
HDPE, on the other hand, is widely used in building (for example, in its use in the fabrication of drain pipes). Medical devices and bulletproof vests are among the high-performance applications of ultrahigh molecular weight polyethylene (UHMW).
We have been established for many years and with our young and vibrant management team have vast experience in all aspects of plastic injection moulding – from the design stages through to the final packaged product.
Leading UK Manufacturers of plastic injection mouldings applications. At Stephens Plastics Mouldings, our engineers will be pleased to help you with any queries you have. There is a variety of plastics that you can use in you plastic injection moulding project, one being Polyethylene. Therefore, we can assist you to make sure you use the correct material with the suitable characteristics.
PE is a polymer that belongs to the polyolefin family and is distinguished by its density and branching. Polyethylene comes in a variety of forms, each one ideally suited for a specific set of tasks. In general, High-Density Polyethylene (HDPE) is much more crystalline than Low-Density Polyethylene (LDPE). In addition, it is used in completely different situations (LDPE). LDPE is commonly found in plastic packaging, such as shopping bags and plastic wrap.
Polyethylene is a lightweight, long-lasting thermoplastic with a crystalline structure that varies. It is one of the world’s most commonly used plastics (tens of millions of tonnes are produced worldwide each year).
Die casting is a process that inserts molten metal under high pressure into reusable molds called dies to produce high-quality components for multiple purposes. ARRK Asia can create complex, accurately dimensioned parts with this low-cost and effective solution as a die casting manufacturer.
The right method for a given low-volume order will depend on factors such as part application, material, and timeline. The entire production process is supported by our expert designers and engineers. By partnering with full-service manufacturing like ARRK Asia, it could be the best course of action taken by your company.
A good volume production service team would be able to offer the best advice on selecting from the different types of plastic manufacturing processes. So, now it would be crucial to select a method of creating low-volume plastic parts, from product design to the finished product.
Handling product development and choosing a low-volume plastic manufacturing process will give several options. But how should one decide?
ARRK is the global leader in product development and has an experienced team to evaluate your project requirements. There are many variables in providing pricing and our team is here to help guide you toward success.
PE is known as a “thermoplastic” (rather than a “thermoset”) because of how it reacts to heat. At their melting point, thermoplastic materials become liquid (110-130 degrees Celsius in the case of LDPE and HDPE respectively). Thermoplastics have the ability to be heated to their melting point, cooled, and reheated. All without any deterioration is a valuable feature. Thermoplastics like polyethylene liquefy rather than burning. Additionally, allowing them to be quickly injection moulded and then recycled.
Please contact us if you would like to receive a quotation and/or to find our more about how we can provide the service you are looking for.
As experienced providers for the industry, we offer custom tooling services that include fixtures, jigs, cutting tools and patterns, assembly jigs, gauges, molds, and dies, to mention a few.
Get insights into EV charger development and how ARRK Asia delivers quality enclosures and casings for effective charging stations.
To give your customers the best possible service when using your products, count on ARRK in Asia to reach your company’s production goals.
Furthermore, thermoset plastics, on the other hand, can only be heated once (typically during the injection moulding process). The first heating allows thermoset materials to set (much like a two-part epoxy). Therefore, resulting in an irreversible chemical shift. It would burn if you tried to heat a thermoset plastic to a high temperature a second time. This property makes thermoset products unsuitable for recycling.
Once you have this covered, selecting the right type of plastic materials is something to be communicated properly. The end-user, the manufacturing process, and other specifications would have the final say on which plastic compound can or should be used.
Some of the cookies we use are essential for the site to work. We also use some non-essential cookies to collect information for making reports and to help us improve the site. The cookies collect information in an anonymous form. To control third party cookies, you can also adjust your browser settings.
Requested serviceDesign ModelPrototyping3D PrintingUrethane CastingCNC MachiningMicrowave MoldingLighting PrototypeToolingInjection MoldingDie CastingEnd to End ServicesStyling Design CountryMalaysiaSingaporeThailandOther
By knowing the advantages of each low-volume manufacturing in Asia process available, it can give a better understanding of the end results possible.
GETTING A QUOTE WITH LK-MOULD IS FREE AND SIMPLE.
FIND MORE OF OUR SERVICES:
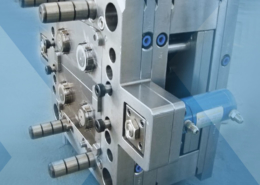
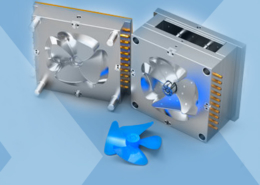
Plastic Molding

Rapid Prototyping
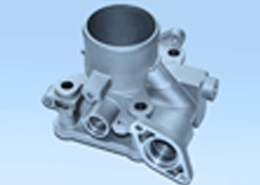
Pressure Die Casting
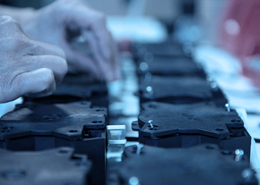
Parts Assembly
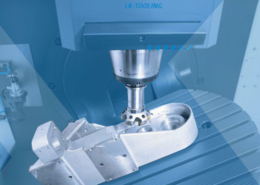