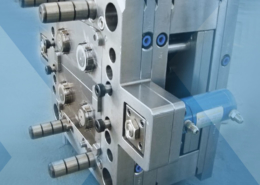
Polycarbonates(PC) injection molding properties and ... - polycarbonate injectio
Author:gly Date: 2024-10-15
Dealing with undercuts and complicated geometries in the molding process involves selective application of sophisticated tools and methods. One way to do this is by using collapsible cores or slides and lifters, which can be moved in and out of position so that the part can come out without damaging its fine details. By doing these it enables successful molding of parts with internal undercuts or complex shapes that otherwise cannot be produced using a traditional mold design.
LIke we can create a wire cut and strip machine for a wire, Also you can creating a mold for ABS plastic is an essential step in manufacturing various products, from toys to automotive parts. In this guide, we’ll explore the process of making a mold for ABS plastic in easy-to-follow steps. Whether you’re a hobbyist or a professional, understanding this process can empower you to produce custom plastic components with precision. From mold design to material selection and maintenance, we’ll cover all the crucial aspects to help you embark on your molding journey successfully. So, let’s start in and discover how to craft molds that bring your plastic creations to life!
Multi-pronged strategy is required to make plastic injection molding more efficient. These are the current recommended strategies from top industry sources:
Lightweight: ABS plastic is lightweight, which is advantageous in applications where weight reduction is essential, such as in the automotive and aerospace industries.
These systems make use of mechanical motion to drive the pin into the mold cavity. As the mold opens, a mechanism is synchronised with it, causing retraction of the pin that holds back and lets loose the molded part. They are known for their reliability and precision especially in high-volume production environments. The key merit is that they have a long life span and can operate at very high speeds but there may be need to carry out extensive maintenance because they wear out regularly.
Ease of Processing: You can process ABS plastic using various molding techniques such as injection molding and extrusion. This ease of processing reduces manufacturing time and costs.
Several trends are poised to redefine industry standards and practices as the sector of side action injection molding continues to develop. Integration of state-of-the-art automation and robotics, which enhances accuracy while reducing labor costs, stands out as a key trend. In addition, smart manufacturing technologies such as IoT and AI are on the rise thereby offering real-time monitoring, preventive maintenance capabilities that minimize downtime, and extend mold life. Moreover, innovation thanks to new high-performance materials has brought about more complicated and enduring components. Lastly, greener practices like biodegradable materials use and efficient energy consumption are being adopted due to sustainability focus. The overarching goal is improving the efficiency, quality and environmental responsibility in side action injection molding.
Customization: ABS plastic is available in a wide range of colors and can be easily painted or finished, allowing for creative and aesthetically pleasing designs in consumer products.
These side actions make possible complex high precision parts through intricate design otherwise not achievable by conventional two-part molds.
Chemical Resistance: ABS plastic is resistant to a wide range of chemicals, making it suitable for applications where exposure to various substances is common. This property is valuable in automotive, industrial, and medical settings.
Creating ABS plastic moldings is a detailed process that requires precision and careful attention to ensure the final products meet quality standards. Let’s break down each step in more detail:
ABS plastic, or Acrylonitrile Butadiene Styrene, is a common and tough thermoplastic material. It’s made by blending three components: acrylonitrile, butadiene, and styrene. ABS plastic excels in impact resistance, making it durable for everyday use.
The invention of plastic injection mold side actions has helped to make mold designs flexible and its functionality improved. Modern day side actions apply highly developed hydraulic and mechanical systems which allows core movements in the molding process as well as undercuts, aspects which are usually hard to pull off. These systems offer greater consistency, better precision and ensure that final products conform precisely to design requirements. Additionally, the recent developments have been driven by reducing cycle time while minimizing wear and tear on molds thus making them last longer and be more reliable as an instrument for injection molding. They have also seen the incorporation of real-time monitoring capability with smart sensors at peripheral devices that control these motions leading to efficient process control and scheduling with reduced downtime in case adjustments have to be made speedily. Manufacturers are now able to produce complex parts of high quality due to these improvements that meet various industries’ stringent criteria.
Collapsible cores are advanced molding mechanisms designed to facilitate the creation of complex internal geometries, particularly for parts with undercuts or intricate internal features. These cores collapse inward during the part’s ejection phase, allowing easy removal from the mold without damaging the part.
A: The cam pin method involves using a cam pin to move the core or lifter into position during the injection molding process. This is especially useful for producing internal threads and other intricate features.
In side action injection molding, when mold is closed, it forms the mould cavity with the help of cams or slides known as side actions. The movement is made possible by angle pins which push the side actions into a position where they become accurate. After this, hydraulic or mechanical actuators that control the molding cycle make the side actions go back hence leaving space for part ejection. This process ensures that undercuts intricate geometries are created such that it does not damage the part hence improving design opportunities and quality of injection molded products.
A: Side-action injection molding is a specialized process used to produce parts with complex geometries. It involves the use of movable components called side-actions to mold undercuts or features that are perpendicular to the main parting line of the mold.
Hydraulic systems use fluid pressure to control cam pins hence rendering them slow and graceful movements. Such designs are also suitable in scenarios where there is need for larger forces or more delicacy like very large parts or those with intricate details. Consistency and repeatability of movement attained by hydraulic cam pins is its most prominent benefit though they require more complex setups and could be expensive due integral hydraulic components as well as maintenance requirements.
To achieve efficiency and high-quality production, there are several considerations that should be made when optimizing part design for the injection molding process:
ABS plastic comes in many colors, allowing for creative designs. It’s cost-effective too. In a nutshell, ABS plastic is a versatile, strong, and budget-friendly material used widely in our daily lives.
Hydraulic cylinders are important in the production of intricate injection-molded parts that have special features which cannot be made by a two-plate mold. Side actions are needed to make undercut or those features which are perpendicular to the direction in which the mold opens. The hydraulic cylinders help to push side cores or sliders into position during the injection stage and withdraw them at ejection time. Employing hydraulic power guarantees accurate, repeatable motion that preserves the complexity of molded features. Their capability to handle high-force applications makes them suitable for industrial applications as they guarantee dependability and efficiency when manufacturing intricately designed plastic components.
Whenever it comes to the process of injection molding, side action mold design involves introducing lateral or side movements into molds which allows manufacturing of intricate parts having undercuts. This is done through the integration of cams or slides within the mold design which move sideways to the direction of opening and closing of a mold. These cams or slides are set into motion during a specific stage of a cycle when they enable formation and removal of parts that have challenging features which cannot be easily created through traditional straight-pull molds. The best suitable method for manufacture such parts could consist in projecting component surfaces at right-angles with respect to main mold parting line there could be projections, recesses or threads perpendicular to the main mold parting line on such molds
To address undercuts in mold design, side actions are important as they allow the creation of intricate geometries that could not be achieved through a standard two-part mold. These undercuts can make it impossible for a molded part to be removed from the mold without causing any damage due to their inward-facing angles or projections.
Several things must be thought of when comparing modular core compression side-action systems. These arrangements improve design flexibility and promote ease of use; in addition, they employ complex molding types and are used in high volume production plants. The systems are modular in nature, making it possible to quickly replace them so as to prevent long periods of repair. They are also known for performing well even when subjected to heavy molding pressures.
Inject the molten ABS plastic into the prepared mold cavity with high pressure. The pressure ensures that the plastic flows into all parts of the mold, taking on its intended shape.
In summary, choosing an appropriate type of a cam pin system depends on various factors including specifications related with molded article, complexity attached with mould and size of batch which has to be manufactured.
Regular cleaning and maintenance are vital. Clean the mold after each production run, and perform thorough maintenance every 10,000 to 100,000 cycles, depending on usage.
Modular mold base systems have revolutionized injection molding by providing greater flexibility, cost savings, and reduced lead times. One primary advancement is fast interchangeability of molds parts that decreases production time loss thus boosting productivity. These systems also make customization easier for each specific project with adaptability without necessarily needing a new set of molds for different requirements. Further precision engineering advancements have been made so that modular mold bases now achieve increased levels of precision and strength resulting in consistent product quality. Additionally, through incorporating advanced materials as well as cooling systems into these bases; it has led to better cycle times which optimize this process by ensuring proper temperature control during injection molded parts processing step.
Amidst contemporary manufacturing, the most widely used and efficient technique is injection molding for creating intricate and complicated components. Amongst the many techniques employed in injection molding, side action injection molding is specifically known for its ability to create complex geometries and undercuts that would be difficult or impossible using traditional methods. This blog post aims to explore side action injection molding in details by giving a comprehensive account of its procedure, advantages, and applications. By understanding these intricacies, manufacturers can utilize this specialized technique in order to better their products’ precision and functionality thereby leading to enhanced performance and innovation across different sectors.
On the whole, side-actions are very useful in expanding injection moulding capabilities by effectively addressing and controlling undercuts within mould designs so as to enable complex part creation.
Yes, skilled professionals can often repair damaged molds, depending on the extent of the damage. Prompt repairs help avoid production interruptions and reduce costs.
Another important technique is to have use of conformal cooling channels. The channels follow the geometry of the part allowing for even cooling as well as minimizing warping and defects. This approach also improves on the cycle time and general quality of the output.
After ejection, trim any excess material or imperfections from the molded part. You can use techniques like trimming, sanding, or machining to achieve the desired finish.
Electrical Insulation: ABS plastic exhibits good electrical insulation properties, making it suitable for electrical and electronic applications.
A: Considerations include the complexity of the part, the type of material used, the required precision, and the specific features that must be produced. Additionally, the chosen method should balance production efficiency with tooling costs.
The methods employed in injection molding to build part quality and consistency require a holistic approach involving process control, design, and material choice. Here are some common practices which help manufacturers achieve parts of high quality that have uniformity:
Allow the mold to cool while the ABS plastic inside solidifies. The cooling time varies depending on the size and thickness of the molded part.
All in all, modular core compression side-action systems offer distinguished advantages such as high precision, flexibility, minimal maintenance downtime thus making them ideal for modern injection molding applications.
GOLDSUPPLIER.COM expands globally, offering quality business opportunities, cost savings, convenience, and expertise in international trade. Trusted and recognized internationally.
The lifespan of an ABS plastic mold depends on factors like material, maintenance, and usage. Well-maintained molds can last for hundreds of thousands of cycles or more.
The detailed steps involved guarantee efficient production for high quality accurate parts through injection molding process every time it’s done consistently.In sum, proper execution of these stages gives assurance for cost-effective yet precise manufacture in good quantities consistently when performing injections molding operations at any given time
A: Tooling costs increase with part complexity. The need for specialized features like side-actions, cam pin actions, and intricate mold surfaces requires more advanced and expensive tooling capabilities.
A: The main types of injection molding methods include standard injection molding, double injection, insert molding, and specialized processes such as side-action injection molding and the cam pin method.
Moreover, advances in 3D printing technology have made it possible to produce molds with very complex geometries that correspond to specific features of a particular part. It allows designers to incorporate much finer details directly into their mold designs which greatly reduces subsequent machining or assembly operations.
A: Precise molding ensures that the injection molded parts meet the desired specifications and quality standards. This is critical when the part must fit perfectly with other components or perform a specific function in a given application.
Regularly maintain and clean the mold to ensure consistent and high-quality results over time. Mold maintenance is crucial for prolonging the life of the mold and maintaining product consistency.
Yes, but it’s essential to ensure that you design the molds for versatility and that the materials are compatible. Some molds are adaptable for multiple part designs.
Cost-Effective: ABS plastic is relatively inexpensive compared to some other engineering plastics, making it an economical choice for mass production.
Thus, by implementing them thoughtfully it will help designers build efficient molds with having side-actions, producing quality parts while maximizing production efficiencies themselves.
Through integration of these advanced techniques, manufacturers are able to address undercut challenges as well as complex geometries more effectively resulting in better quality products at lower cost.
The main benefit of collapsible cores is that they can form high precision and complex shapes which would be difficult or impossible to achieve through traditional methods of molding. They have proved most helpful in situations where there are complicated part designs especially in areas such as motor vehicle industry, medical sectors and consumer good industries.
These principles can be imbedded into mold designs whereby designers can come up with sturdy molds that give high quality parts repeatedly from cycle to cycle whilst shortening production cycle.
The spring-loaded type make it possible to hold cams pins in place while retracting them when necessary during die opening process by using springs.Therefore, one can argue that fixing these springs are less complicated compared to mechanical or hydraulic ones. The primary advantage derived from adopting such systems relates to low initial set up cost as well as ease of replacement although I think springs lack robustness exhibited by mechanical or hydraulic devices making them susceptible to wear down, hence limiting their applications under extreme conditions.
Thus these measures would enable manufacturers enhance their productivity, lowering costs as a result of more efficient plastic injection molding processes.
Whereas the use of collapsible cores can reduce secondary machining operations during injection molding process; thus saving time and costs. It also contributes to a better product quality as collapsing mechanism maintains delicate feature while ejecting it.
By focusing on these key design principles, manufacturers are able to optimize their injection molding process which consequently results in lowered production costs and improved quality and performance levels of molded parts generally.
Every injection molding has cam pin systems which are important elements that allow for the manufacturing of complex geometries and side actions in moulds. Their main function entails lateral movement of the mold components for undercut release or elimination of side features from a part. In this paper we shall look at three widely-accepted types of cam pin systems:
A: Modular systems allow for more flexible and cost-effective tooling. They enable the creation of multiple parts or different part designs using interchangeable mold components, thus reducing overall tooling costs.
Addressing these challenges through creative solutions allows manufacturers to better integrate them into their molding processes, thereby improving functionality while managing costs and increasing productivity.
To increase the ability for molding such complex parts, it is important to integrate advanced techniques and technologies. To begin with, multi-material injection moulding can greatly enhance functional capabilities and aesthetic appeal by forming materials having different properties into one part. On the other hand, before actual production takes place, High Performance Computing (HPC) simulations serve to optimize mold design as well as process parameters thereby reducing defects while improving general qualities. Finally, investing precision machining with high-accuracy CNC equipment ensure tighter tolerances as well as consistency in producing intricate features thus negating secondary operations; hence enhancing production efficiency.
A: Hydraulic pressure is often used to move the side-actions or cores during the injection process. It ensures that there is enough force to hold the core in place and produce parts with the required complexity without causing core deflection.
Consistent process control, proper mold design, and regular maintenance are key to preventing defects like warping, sink marks, or air bubbles in ABS plastic parts.
High Impact Resistance: People know ABS plastic for its remarkable impact resistance, enabling it to endure shocks and drops without breaking easily. Manufacturers find it ideal for products prone to rough handling or accidental drops.
The effectiveness of side actions in mold design mainly relies upon a few key principles that contain the latest thoughts from top resources:
Heat Resistance: ABS plastic retains its integrity at moderately high temperatures, making it suitable for applications demanding heat resistance, like automotive interiors and electrical enclosures.
One key benefit is its moldability when heated, making it perfect for 3D printing and injection molding. It’s found in various products like toys, appliances, car parts, and electronics casings due to its chemical and heat resistance.
The injection molds’ longevity and optimal performance can only be achieved through proper maintenance and timely troubleshooting. There are several approaches for solving common mold problems outlined below:
Generally, collapsible core enhances plastic injection molding flexibility and capabilities thereby enabling manufacturers to handle more sophisticated designs with efficiency and accuracy intact.
Side actions in undercut features are formed through motion from side action molds using cam mechanisms. These cams move laterally to position the sides accurately into the mold cavity because they are usually guided by inclined pins during die closure. In this way, misalignment is eliminated hence even complex geometry is correctly formed.
ABS plastic, a thermoplastic, signifies that it can melt and mold when heated. Load ABS pellets into an extruder, which will heat and melt them to the ideal temperature for molding.
Inspect the molded part for any defects or deviations from the specified tolerances and quality standards. This step ensures that the parts meet the required criteria.
A: Common challenges include managing the hydraulic pressure during injection, ensuring that the core deflection is minimized, and achieving precise molding to meet tight tolerances.
Following these key considerations assist designers and engineers in creating efficient, durable performance-oriented tools and moldings that result in high-quality components every time they are produced consistently throughout their lifecycle.
Start by designing the mold using computer-aided design (CAD) software. The mold represents the exact shape and specifications of the desired ABS plastic part.
By maintaining their molds using these practices of maintenance and repair activities, manufacturers can increase their lifespan thus reducing downtime costs together with producing high quality parts.
Thoroughly clean and prepare the mold’s surface to ensure it’s free from any contaminants or debris that could affect the molding process.
When molding process ends, these cam mechanisms enable the smooth retraction of side actions thus allowing safe removal of molded parts without any harm. This withdrawal relies on hydraulic or mechanical actuators to maintain uniformity and continue producing good quality end products. Generally, cam mechanisms make side action molds more functional and versatile so that intricate components can be obtained efficiently and accurately.
These approaches will allow manufacturers enhance their molded parts’ quality and consistency while improving performance and customer satisfaction.
A: Side-actions use hydraulic pressure or mechanical means to move the core during injection. This helps in forming features that are perpendicular to the main parting line and must be removed from the part without causing damage to the mold surfaces.
Manufacturers can address ejection and perpendicular undercut problems by using these strategies in integration towards increasing process reliability as well as effectiveness.
You can make the mold from materials like aluminum or steel, selecting them based on factors like expected production volume and complexity.
Once the ABS plastic has cooled and solidified, eject the part from the mold. You can do this manually or automatically using ejector pins.
ABS plastic molding offers numerous advantages, making it a popular choice in various industries. Let’s explore these benefits:
Choose the appropriate ABS plastic material, considering characteristics such as color, strength, heat resistance, and any specific requirements for your application.
Injection molding side actions are movable parts that slide in a direction perpendicular to the main axis of a mold. These cams or slides allow the creation of undercuts and other complex features found not in relation to the principal opening and closing direction of the mold. In injection molding cycle, these side actions engage at different positions to develop or release intricate characteristics on a part leading to production of components which would not be achieved through conventional techniques of molding. This helps in improving manufacturing advanced parts by increasing the design flexibility and accuracy in injecting molded products.
Versatility in Design: ABS plastic can be easily molded and shaped when heated. This flexibility in design allows for the creation of complex and intricate shapes, making it a top choice for manufacturing intricate components.
In the modern mold design, Computer Numerical Control (CNC) technology is vital in improving accuracy, speed, and complexity in the production process. The CNC technology allows for detailed machining of complex mold components through employment of sophisticated software and automated machinery thereby ensuring consistency and quality of the product. One significant advantage associated with CNC technology is that it can be used to quickly prototype and manufacture custom parts thus reducing lead times and leading to faster iterations in the design stage. Moreover, automation afforded by CNC systems helps in minimizing human error hence making sure that molds are made as per exact specifications and tolerances. Also, it favors use of a variety of materials such as high-performance alloys and composites necessary for making durable, high quality molds. For instance, with its ability to streamline production workflows while ensuring high levels of accuracy, CNC technology is indispensable in meeting the intricate demands of present-day injection molding industry during mold design phase.
GETTING A QUOTE WITH LK-MOULD IS FREE AND SIMPLE.
FIND MORE OF OUR SERVICES:
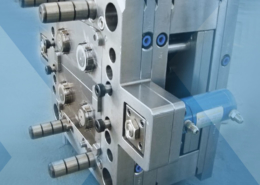
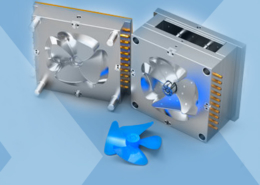
Plastic Molding

Rapid Prototyping
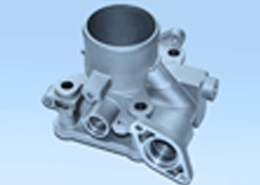
Pressure Die Casting
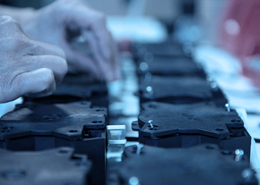
Parts Assembly
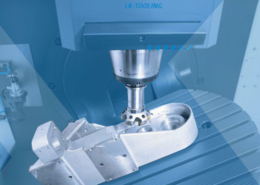