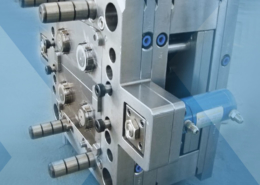
Polycarbonate Injection Molding - polycarbonate injection molding
Author:gly Date: 2024-10-15
Scientific molding practices can also be used to optimize tool design or to optimize poorly designed tools. It is essential for injection molds to be evaluated for their performance in the production of consistent, defect-free parts. Engineers should examine every aspect of a mold’s mechanical functionality, using the appropriate material settings.
Are you interested in learning more about scientific molding and how it can benefit your custom part? Learn how Plastic Components, Inc. will strive to be your best supplier and a team you can count on.
According to Kip Doyle, author of an article on the Top 10 Reasons Why Molders Fail at Scientific Molding, many molders can’t get past a “machine-focused” approach and mold from the plastic’s “point of view.” He cites that many articles have been written on the four primary plastic variables (plastic temperature, plastic flow, plastic pressure, and plastic cooling rate and time), and a scientific molder must understand this approach and the process optimized from the perspective of the plastic.
Gilero provides a range of manufacturing services, including plastic injection molding and injection mold tool building. We focus solely on the medical device and drug delivery markets. Our medical injection molding facilities follow strict design protocols and process controls to ensure that all products meet the required specifications. Depending on client needs and product requirements, we can offer manual or fully automated production lines for molding and assembly.
Equipment and software that help monitor real-time production processes guide the scientific molding stages and provide a critical advantage. In addition, quality control issues can be avoided by having automated containment control and traceability for specific applications. From collecting data to machine maintenance, process development to resin characteristics, and much more – scientific molding helps identify efficiencies which result in greater value and better parts for customers.
The choice of material will depend on the specific requirements of the part being produced, such as its mechanical properties, chemical resistance, and environmental factors like temperature and humidity.
Rosti works with some of the world’s leading producers to face up to the manufacturing challenges in e-mobility. This is a sector with rapid growth – driven by environmental pressures…
Injection molders should understand how to avoid designing a part, building the tooling, and beginning the molding process only to find out that the design does not work in production. Scientific molding can help manufacturers steer clear of this situation.
Design engineers should lean on past learnings and expertise in optimizing part design for unique applications. Scientific molding elements associated with part design may incorporate using the latest software and technology including computer aided engineering, mold flow, and prototype development that will validate the part’s end use.
How does scientific molding benefit product manufacturers and OEMs? When implemented methodically by an injection molder, scientific molding results in better parts and fewer rejects.
In comparison to other manufacturing practices, plastic injection molding for medical devices is very flexible and allows for full customization of components. It is used in high volume situations to fulfill injection molded medical device and drug delivery devices with high accuracy and precision. From an operational perspective, plastic injection molded medical devices are produced with low labor costs, are positioned to be scalable as the client grows in sales, and are more environmentally friendly due to the extended life of the product and reduction of waste.
Our facility utilizes high-precision plastic injection molding and injection mold tool building equipment. In-house injection molding machines range in tonnage from 30-Ton to 250-Ton. Injection molding capabilities range from single cavity, pre-production injection molds to high cavitation molding using a hot runner system. The injection molding equipment used by Medacys is manufactured by some of the most trusted brands in the industry, including Sumitomo (SHI) Demag, Toyo Machinery, and Haitian International.
Gilero stands out as an excellent choice for medical device injection molding manufacturing. Medacys, our joint-venture facility in Shenzhen, China, spans 36,000 square feet and is equipped with cutting-edge technology. The skilled team, comprising manufacturing technicians, tooling designers, quality engineers, and engineering project managers, specializes in the medtech and biomedical sectors. This specialization ensures a deep understanding of the unique requirements and regulatory standards in these fields. Gilero offers dedicated areas for various manufacturing processes, including tooling, molding, assembly, and laboratories. We maintain environmentally controlled cleanrooms for precision. Our in-house injection molding machines range from 30-Ton to 250-Ton, and they use equipment from trusted brands like Sumitomo (SHI) Demag, Toyo Machinery, and Haitian International.
Recorded data can be used to assess quality control and make any necessary tweaks to tooling – improving overall part quality. Once all quality parameters have been met, the implementation of scientific injection molding practices help to greatly streamline the production process. These actions can be so effective that less involvement is needed by both machines and operators. In fact, cutting-edge injection molders have begun instituting revolutionary lights-out manufacturing practices. This is where factories and production facilities are equipped with innovative and automated machinery to conduct tasks that would normally need the presence of a human.
Plastic variables require understanding the nature of the material to be molded and its preferred molding conditions. When a material’s key characteristics, behavior, and response to processing is understood, scientific molders can optimize the molding process to produce the most consistent part possible.
Scientific molding involves using data to develop a process that produces repeatable results with little to no variation. Through resin expertise and testing, dimensional or mechanical characteristics of a molded part can be optimized. Often achieved through the use of SOLIDWORKS® Plastics Premium software (mold flow simulation) and RJG eDart® process control systems, predictive insight, process validation and complete process documentation are vital to producing demanding parts.
Located in Shenzhen, China, is Medacys – Gilero’s joint venture toolmaking and medical injection molder. This state-of-the-art injection molding facility spans 36,000 square feet and is staffed by manufacturing technicians, tooling designers, quality engineers, and engineering project managers. The expertise of the Medacys team focuses largely on the medtech and biomedical industries. With dedicated tooling, molding, assembly, and lab areas, along with environmentally monitored and controlled cleanrooms, our Shenzhen facility provides plastic injection molding services for companies across the globe.
It’s not hard to understand how computing and innovation have positively impacted industries of all types over the past 35 plus years. The injection molding industry is no exception. Plastic…
This guide will walk you through a comprehensive overview of the plastic injection molding process from design through production – including essential elements of molding.
This guide will help you understand the importance of DFM, and how to partner with your injection molder during the design validation process prior to tooling kick-off.
This guide will help you understand the metal to plastic conversion process, its benefits, and how to partner with your injection molder to collaborate on all design for manufacturability elements.
As it continues to evolve, scientific molding has helped optimize injection molding production processes in a way that now allows manufacturers to lean on technology that creates an even greater global competitive advantage.
Testing can then be applied to check for any imbalances among cavities. When this analyzation is complete, a gate seal study can be performed to gather data on where the gates seal fully, and at what points in the mold cavities. Recording findings and making recommendations for adjustments in the process or tooling, is essential to correcting potential defects.
GETTING A QUOTE WITH LK-MOULD IS FREE AND SIMPLE.
FIND MORE OF OUR SERVICES:
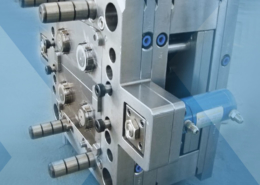
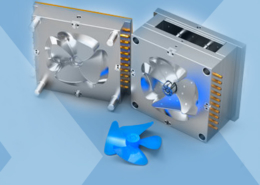
Plastic Molding

Rapid Prototyping
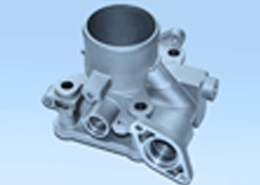
Pressure Die Casting
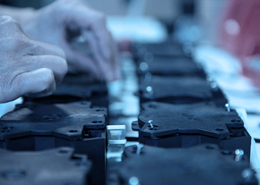
Parts Assembly
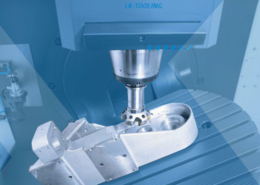