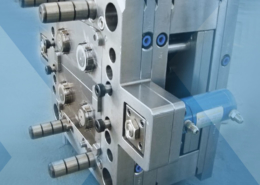
Polycarbonate Injection Molding - polycarbonate injection molding
Author:gly Date: 2024-10-15
In the medical device industry, where stringent regulations and precision are paramount, short run injection molding accelerates the development process for medical devices. It enables cost-effective production of small-batch components, making it suitable for niche applications or specialized medical devices that require limited quantities. Short run molding ensures high quality and reliability while meeting tight timelines and maintaining compliance with regulatory standards.
Molds are usually manufactured by an injection mold-maker from metal, usually steel or aluminum, and precision-machined. That is done so as to form the features of the required part after a product is conceived. The process is usually done by an industrial designer or an engineer in a company that provides a plastic injection molding service. Injection molding is a popular method used for producing a wide range of parts, from minor components to whole bodies.
Unlike many mold release brands, Stoner Molding Solutions formulates, manufactures, and distributes our own products. Check out our full line of mold releases, sealers, cleaners, rust preventatives, and lubricants. In stock products are ready to ship now!
Individuals still go for the DIY injection molding process because the prices involved are still less than the cost of a single metal mold. The time and money saved after you’re up and running will readily compensate for the initial effort.
Short run injection molding offers cost advantages compared to larger production runs. Since fewer parts are required, less expensive mold materials such as aluminum or lower steel grades can be used, reducing tooling costs. With lower upfront costs, short run injection molding becomes accessible to a broader range of customers with smaller budgets. Additionally, adjustments and modifications can be made without significant financial commitments, and prototypes may require less finishing than in 3D printing, saving both time and cost.
The specific strategy to DIY injection molding will differ depending on the intended design and volume but the following pointers can help you improve your chances of success.
The packaging industry benefits from short run injection molding by enabling the creation of unique packaging designs for limited-edition products. It allows companies to meet specific packaging requirements for new product launches, ensuring eye-catching and functional packaging solutions. Short run molding provides the flexibility to produce a limited number of parts while keeping options open for future design changes or additions.
Injection molding is used to make the vast majority of plastic products seen on the market today. Traditional CNC machined metal molds have very high prices and long lead times for low-volume production, despite being a perfect process for large-scale production needs.
We all agree that carrying out the injection molding process is not cheap. That is still the case in plastic injection molding at home. You will need a number of tools and materials to get started. It takes a good amount of cash to set up a system for DIY injection molding. On the other hand, getting the correct equipment and going through the whole learning process of how to use it will cost you both money and time.
There are a variety of injection mold makers around the globe but not all provide quality plastic injection molding services. FOW Mould offers a wide range of services, including plastic component and mold design, as well as mold making and molded part production. In case of any inquiries contact us.
Short run injection molding provides a game-changing solution for companies seeking efficient and cost-effective manufacturing processes for small-scale production. We have explored the numerous benefits of this innovative technique, from its ability to meet the demands of various industries to its flexibility in customization and rapid prototyping.
The electronics industry benefits from short run injection molding through rapid prototyping and quick production of consumer electronics. This fast-paced process allows companies to test and validate product designs before committing to large-scale manufacturing. Unlike 3D prototyping, which often limit sample quantities, short run molding offers the ability to produce more samples in less time, providing greater flexibility for design iterations and improvements.
It’s frustrating to have a brilliant product idea or a new project that requires rapid prototyping or small-batch production, but not having the capability to produce the test product. The lengthy and costly tooling process associated with conventional injection molding can be a significant roadblock, hindering innovative product development and market entry. Production delays can result in missed opportunities and potential loss of customers and market share.
By considering these factors and leveraging the benefits of short run injection molding, companies can achieve efficient and cost-effective production for their customized components prototypes.
Short run injection molding does not significantly restrict resin requirements due to the mold material. It allows for utilizing a wide range of resins available in higher volume molding processes. Material selection plays a critical role in determining the final product's quality, durability, and performance. Factors such as environmental conditions and specific requirements need to be considered when choosing the appropriate material. By carefully selecting the right material and considering design limitations, companies can ensure that the chosen material meets all necessary requirements while remaining cost-effective.
The advantages and benefits of short-run injection molding are numerous. First, it allows for quick turnaround times, enabling companies to bring their products to market faster. This fast process is particularly advantageous for industries where time-to-market is crucial. Additionally, short run injection molding is a cost-effective solution, eliminating the need for expensive tooling and molds associated with larger production runs. Companies with limited budgets can benefit from this approach without compromising on quality. Furthermore, this process allows flexibility and agility in design iterations and product improvements, making it ideal for companies that value innovation and adaptability.
By leveraging our advanced products experienced team, and commitment to excellence, we aim to make your production processes more efficient, cost-effective, and responsive to market demands. Contact us today to explore how our short run injection molding products can empower your business to create precise, high-quality parts quickly and easily.
Here's where short run injection molding offers a breath of fresh air. By leveraging advanced technologies and skilled expertise, short run injection molding provides a cost-effective and efficient solution for small-scale production. With reduced tooling costs, quick turnaround times, and the ability to produce quality parts in the thousands or even just a few hundred, short run injection molding empowers companies to respond swiftly to market demands, effectively manage product development, and seize opportunities.
Utilizing the right molding products is crucial to enhance the short run injection molding process. Mold sealers are commonly used to fill in the microporosity of molds, resulting in an even finish on the molded parts. Mold release agents aid in easily releasing items from the mold after the molding process is complete. Mold cleaners help maintain the cleanliness and longevity of molds, ensuring optimal performance over multiple production cycles.
Always make sure you compare the injection molder to your production needs before making any purchase. Industrial techniques will still be required for significant parts. This DIY injection molding process works best for creating small parts in limited quantities. Let us look at the items needed before you get started.
Injection molding is basically a manufacturing method that involves injecting molten material into a mold. Injection molding plastics at home can be carried out using various materials. They include metals, glassware, elastomers, confections, and, most typically, thermoplastic and thermosetting polymers. The part’s material is first supplied into a heated barrel, mixed, and then injected into a mold cavity. That is where it cools and hardens according to the cavity’s configuration.
3D printed injection molds are a time and cost-effective alternative for low-volume production. They are also less expensive than CNC machining. This article will guide you through the whole process of DIY injection molding and give you all of the tools and tips you will need to learn how to mold plastics at home.
When considering short run injection molding solutions, several factors come into play. These include cost factors and budget considerations, design limitations, material selection, and the use of the right molding products.
Short run injection molding finds application in various industries. Still, four key sectors stand out for reaping significant benefits from this manufacturing process: the automotive industry, the electronics industry, the medical device industry, and the packaging industry.
Many companies struggle with finding efficient ways to produce high-quality components in small quantities. Traditional injection molding processes may not be suitable due to high tooling costs, extended lead times, and the need for large production volumes. These limitations often hinder the ability to respond quickly to market demands, leaving businesses at a disadvantage.
In the automotive industry, short run injection molding plays a vital role in customizing parts for specific models. It enables manufacturers to produce limited quantities of high-quality components with precision, ensuring a perfect fit and finish. This top-tier quality is particularly valuable for luxury and exotic car manufacturers who offer high-end vehicles in limited numbers. By leveraging short run molding, they can maintain exceptional quality standards while meeting the demand for exclusivity.
ACIS®, Autodesk Inventor®, CATIA® V5,Creo™ Parametric, IGES, Parasolid®, Pro/ENGINEER®,Siemens PLM Software’s NX™, SolidEdge®, SolidWorks®, STEP
Short run injection molding refers to a manufacturing process that specializes in producing plastic parts in small quantities, typically ranging from a few hundred to a few thousand units. It offers a cost-effective solution for companies that require rapid prototyping, low-volume production, or customized components. In this process, a mold is created, and thermoplastic materials are injected into the mold cavity under high pressure. The mold is opened once the material cools and solidifies, and the finished part is ejected.
GETTING A QUOTE WITH LK-MOULD IS FREE AND SIMPLE.
FIND MORE OF OUR SERVICES:
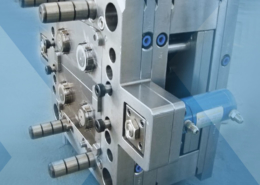
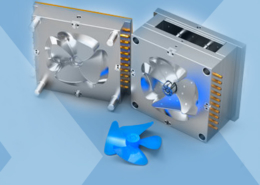
Plastic Molding

Rapid Prototyping
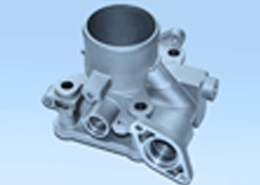
Pressure Die Casting
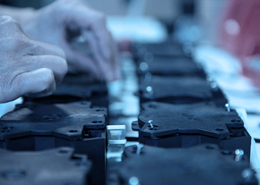
Parts Assembly
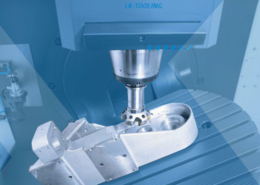