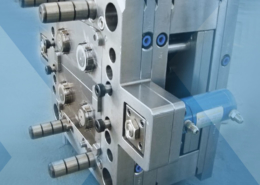
Polly Plastics Heat Moldable Plastic Sheets | 8-inch x 12- ... - plastic that ca
Author:gly Date: 2024-10-15
Diameters of runners range from 4 - 7.5 mm (typically 6 mm). Runner lengths should be as short as possible. All types of gates may be used. Gate lands should not exceed 0.75 mm in length. Ideally suited for hot runner molds; an insulated hot tip runner is preferred when there are frequent color changes.
20 - 95 C (68 - 194 F) (higher temperatures for wall thickness of up to 6 mm; lower temperature for wall thicknesses greater than 6 mm.) The cooling rate should be uniform to minimize shrinkage variations. For optimum cycle times, the cooling channel diameters should be at least 8 mm and must be within a distance of 1.3 d from the mold surface (where "d" is the diameter of the cooling channel).
Being a semicrystalline material, the molding shrinkage is high (order of 0.015 - 0.04 mm/mm or 1.5 - 4%). This is dependent on the degree of orientation and level of crystallinity in the part (which in turn are dependent on processing conditions and part design).
Containers in refrigeration units, storage vessels, household goods (kitchenware), seal caps, bases for PET bottles, etc. Major use is in blow-molding applications (packaging applications)
A wide variety of thermoplastics can be used for the “second shot,” or overmolding, of the substrate. These materials are typically more flexible or softer, and various additives can be used including foaming agents, colorants or other materials to achieve a desired texture, aesthetic or feel. These are used to address ergonomics, sound absorption, dampening of vibration, improved grip surface, the need for a water-type seal, or even electrical insulation.
Overmolding is typically plastic-over-plastic or a rubber-type resin over a plastic substrate providing a grip surface. Overmolding a plastic gear or cams onto a shaft are the most common application. Some examples of applications include small cams used in infusion pumps, plastic gears on bushings for ATM machines, mail processing, or in vending machines.
When designing a product, it can be challenging to determine the best solution to fit the application. This holds true when considering overmolding and insert molding. While the general concept of these terms are similar, there are differences between the two processes. Their application – and what you are looking to achieve – needs to be considered when deciding the right fit for your application.
The material flows easily and the MFR ranges from 0.1 - 28. Higher molecular weights (lower MFR grades) have better impact resistance.
Two important considerations when evaluating overmolding are volumes and speed. The upfront tooling investment for overmolding is higher than insert molding primarily because you are, in essence, making two parts; a substrate and the overmold. Forum’s tool financing can help address this upfront investment.
High density polyethylene is produced from polymerization of ethylene (lower temperature and pressure conditions are used compared to the production of low density polyethylene). The material is free from branching and this is made possible by the use of stereospecific catalysts. Because of molecular regularity, HDPE has a high level of crystallinity (compared to LDPE).
Overmolding is typically used when a product designer is trying to create a single part using a combination of two or more different thermoplastics. It involves multiple “shots” to create the one part. The “first shot,” also known as the substrate, is typically the more rigid of the two materials being combined. This mechanical bond creates a part that has both strength and durability.
We welcome the most challenging engineering requests. Start a partnership with Forum today by requesting a quote for your next project.
180 - 280 C (356 - 536 F); for high molecular weigh grades, the suggested melt temperature range is 200 - 250 C (392 - 482 F)
This process is faster because it is happening in parallel or at the same time – in comparison, overmolding can require two or even three shots. Some examples of this can be a gear onto a metal shaft, metal guide pins into a plastic part, or metal hooks that may need a plastic retainer.
Insert molding differs from overmolding because rather than joining two different materials, it involves encapsulating a product in molded plastic. Insert molding usually involves placing a metal insert, part or pin into the mold and overmolding plastic onto it. The process involves injecting melted plastic resin into a mold and then a plastic or metal component is inserted into the mold to create the encapsulated finished part.
PE is susceptible to environmental stress cracking, which can be minimized by reducing internal stresses by proper design and using the lowest MFR material at a particular density level. HDPE is soluble in hydrocarbons at temperatures greater than 60 C, but resistance to these materials is greater than that for LDPE.
Higher levels of crystallinity contribute to higher density, tensile strength, heat distortion temperature, viscosity, and chemical resistance. HDPE is more resistant to permeability than LDPE. The impact strength is lower. The properties of HDPE are controlled by the density, and molecular weight distributions. Injection molding grades typically have a narrow molecular weight distribution.
Insert molding typically requires a unique mold design to load, capture and verify that the insert is properly in-place. Forum has made the necessary equipment investments and typically uses our vertical shuttle press for insert molding, but a conventional molding machine can also be used.
When working with product designers, the considerations that need to be accounted for when choosing a substrate and TPE are:
High injection velocity is recommended; profile injection velocity can be used to reduce warpage in the case of components with a large surface area.
Form Plastics has extensive experience with insert molding, and we have worked with various materials including stainless steel pins and tubes. Forum has the ability and expertise to also overmold brass and bronze bushings. Our engineering team can work with you to determine feasibility and make recommendations on the best process and tool design.
Forum provides design for manufacturing support and will proactively make cost avoidance recommendations for any necessary changes to the insert to aid in overmolding or insert molding. Contact Doug Hungerford, Director of Engineering, to learn more about our capabilities and how we can support your product development.
When the density is 0.91 - 0.925 g/cm^3, the material is known as Type 1; Type 2 materials have densities in the range of 0.926 - 0.94 g/cm^3, and Type 3 materials have densities in the range of 0.94 - 0.965 g/cm^3.
HDPE injection molding processing condition Generic Class HDPE (High Density Polyethylene) Typical Applications Containers in refrigeration units, storage vessels, household goods (kitchenware), seal caps, bases for PET bottles, etc. Major use is in blow-molding applications (packaging applications) Injection Molding Processing conditions Drying Not normally necessary if stored properly. Melt Temperature 180 - 280 C (356 - 536 F); for high molecular weigh grades, the suggested melt temperature range is 200 - 250 C (392 - 482 F) Mold Temperature 20 - 95 C (68 - 194 F) (higher temperatures for wall thickness of up to 6 mm; lower temperature for wall thicknesses greater than 6 mm.) The cooling rate should be uniform to minimize shrinkage variations. For optimum cycle times, the cooling channel diameters should be at least 8 mm and must be within a distance of 1.3 d from the mold surface (where "d" is the diameter of the cooling channel). Material Injection Pressure 70 - 105 MPa Injection Speed High injection velocity is recommended; profile injection velocity can be used to reduce warpage in the case of components with a large surface area. Runners and Gates Diameters of runners range from 4 - 7.5 mm (typically 6 mm). Runner lengths should be as short as possible. All types of gates may be used. Gate lands should not exceed 0.75 mm in length. Ideally suited for hot runner molds; an insulated hot tip runner is preferred when there are frequent color changes. If you need high quality cutom aluminium casting parts Pls contact us sales@viewmold.com If you need high quality injection mold tooling, Contact us. Chemical and Physical Properties High density polyethylene is produced from polymerization of ethylene (lower temperature and pressure conditions are used compared to the production of low density polyethylene). The material is free from branching and this is made possible by the use of stereospecific catalysts. Because of molecular regularity, HDPE has a high level of crystallinity (compared to LDPE). Higher levels of crystallinity contribute to higher density, tensile strength, heat distortion temperature, viscosity, and chemical resistance. HDPE is more resistant to permeability than LDPE. The impact strength is lower. The properties of HDPE are controlled by the density, and molecular weight distributions. Injection molding grades typically have a narrow molecular weight distribution. When the density is 0.91 - 0.925 g/cm^3, the material is known as Type 1; Type 2 materials have densities in the range of 0.926 - 0.94 g/cm^3, and Type 3 materials have densities in the range of 0.94 - 0.965 g/cm^3. The material flows easily and the MFR ranges from 0.1 - 28. Higher molecular weights (lower MFR grades) have better impact resistance. Being a semicrystalline material, the molding shrinkage is high (order of 0.015 - 0.04 mm/mm or 1.5 - 4%). This is dependent on the degree of orientation and level of crystallinity in the part (which in turn are dependent on processing conditions and part design). PE is susceptible to environmental stress cracking, which can be minimized by reducing internal stresses by proper design and using the lowest MFR material at a particular density level. HDPE is soluble in hydrocarbons at temperatures greater than 60 C, but resistance to these materials is greater than that for LDPE. If you need to look for more plastic resin injection molding processing condition, could you please click it. If you need high quality plastic extrusion services, Pls contact us sales@viewmold.com If you need high quality sheet metal parts, Pls contact us sales@viewmold.com The following is other plastic processing condition: ABS injection molding processing condition, HDPE injection molding processing condition, LDPE injection molding processing condition, PA12 injection molding processing condition, PA6 injection molding processing condition, PBT injection molding processing condition, PC-ABS injection molding processing condition, PC-PBT injection molding processing condition, PEI injection molding processing condition, PETG injection molding processing condition, PMMA injection molding processing condition, POM injection molding processing condition, PPE injection molding processing condition, HDPE injection molding processing condition, PP injection molding processing condition, PS injection molding processing condition, PVC injection molding processing condition, SAN injection molding processing condition,
GETTING A QUOTE WITH LK-MOULD IS FREE AND SIMPLE.
FIND MORE OF OUR SERVICES:
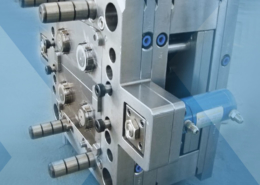
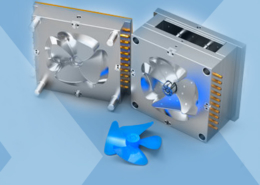
Plastic Molding

Rapid Prototyping
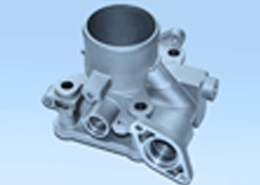
Pressure Die Casting
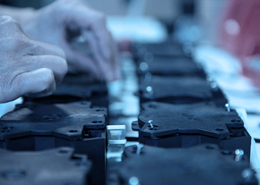
Parts Assembly
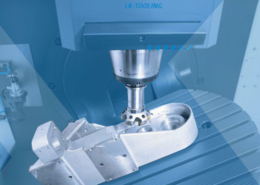