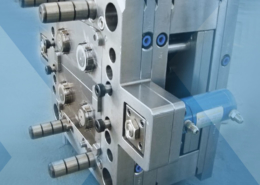
Polly Plastics Heat Moldable Plastic Sheets | 8-inch x 12- ... - plastic that ca
Author:gly Date: 2024-10-15
We optimize the production process, which results in lower costs and higher quality of the manufactured products. We will assign you a dedicated Project Manager who will ensure efficient service and answer all your questions. Fill out the form and you will receive a response from us within 1 hour.
Optional field. The maximum size of the attachment is 25MB. A maximum of 10 files can be uploaded. Acceptable attachment extensions are: pdf, step, igs, jpg, jpeg, stp, stl, dwg, png, zip, xlsx, docx, dxf, dwf, obj, 3ds. Other file extensions and attachments larger than the allowed size, please send directly to email: kontakt@plastipol.pl
Technical director at Plastipol Poland. Popularizer of knowledge about plastics processing. Industry experience gained through education at Scandinavian polytechnics, work in global corporations in the plastics industry, and by managing technical issues in a Polish company. Specialist in plastics batch and mass production technologies. Author of articles and industry texts for clients in various industry sectors. Training Advisor.
There is no doubt that the rotational molding industry has undergone changes and adapted its approach due to significant technological advancements in recent decades. Rotational molding has evolved from a manufacturing method perceived by many as a black art into a sophisticated process for creating high-quality products, some of which could not be produced using any other molding method.
The Einar® anti-static additives are the perfect choice for manufacturers looking for a more sustainable and safer alternative to their current additives as they are all plant-based and food-grade.
Rotational molding began its development in the early 20th century. However, it was only in the early 1960s, when LyondellBasell replaced plastisol resins with polyolefin resins, that rotational molding gained popularity in the industry. Over the next few years, the development of specially designed low and high-density polyethylene for rotational molding allowed it to enter markets where resin parts and processes could no longer compete. At the beginning of the 1970s. Networked and modified polyethylene types entered the rotational molding market. These new powders opened up more market areas, especially in the production of large containers. “Linear low-density polyethylene for rotomolding was developed in the late 1970s and 1980s.” They brought about a rapid increase in the use of non-polyethylene resins, including nylon, polypropylene, and polycarbonate, for rotational molding.
In summary, one of the most respected pioneers in the industry, Professor Roy Crawford, summarizes the rotational molding process with the following words:
Einar® offers both ethoxylated amine and amide-free general-purpose GMS and advanced bio-based and food-grade anti-static additives for PP injection moulding which also provide excellent mould release and denesting properties.
Rotational molding, also known as rotomolding or rotational casting, is one of the fastest-growing methods in the processing of plastics. It’s easy to understand why. Rotational molding techniques, combined with used polyolefin powders, can be employed to produce hollow objects of any size and diverse geometry – whether open or closed. In recent years, rotational molding technique has been extensively developed. On the production line, this process can now compete with or complement processing methods such as:
The main difference between rotational molding and other plastic molding techniques, such as blow molding, injection molding, vacuum forming, or lamination, is as follows:
The development of other polymers was hindered by the fact that the process is relatively long and thus aggressive towards polymers. However, there is some application of PVC (usually in the form of liquid plastisol), polypropylene, and polyamide (PA6, PA11, and PA12). Many of these non-polyethylene materials are challenging to grind, and most of them require processing into powder through cryogenic milling – a freezing grinding process that is more costly. There is a desired growth in research and development efforts to expand the range of materials available for the industry.
Would you like to improve the appearance and handling of your injection moulded PP products? This is possible with the anti-static additives in the Einar® product line which in addition to preventing build-up of static charge also provide mould release and denesting for easier production and handling.
PP is a very versatile polymer used for many different purposes including medical and food packaging, appliances and a broad portfolio of everyday products. All of which require anti-static properties in some form.
First, we will make sure we have all the information needed for the quotation. Then, after an internal analysis, we will prepare an offer for you. If you decide to work with us, we will handle the implementation of the project (which usually involves the production of the mold), and then we will set a production schedule.
Einar® additives will provide the necessary mould release and denesting properties when incorporated in both random copolymer and homopolymer PP at the recommended levels for good anti-static performance.
A good anti-static additive will secure an attractive appearance of the products towards the consumer – dust-free products are obtainable by the use of efficient migratory anti-stats that are able to build an additive concentration on the polymer surface which interacts with water in the air to form a conductive layer. This will enable the dissipation of static charges whereby dust and other fine particles will not be attracted.
Thanks to our large-scale application centre in Denmark, we can help you test the performance of our Einar® products and compare them to your current additives. In this way, you can see how they can match or improve the quality of your products.
The concept of rotational molding is very simple. The plastic, in powder form, is placed inside a hollow mold, typically made of cast aluminum or fabricated from steel sheet. The mold is closed and slowly rotated on two axes. The mold is then heated in an oven while rotating, and the polymer gradually melts and ‘coats’ the inside of the mold. After complete melting of the polymer powder, the mold is transferred to a cooling station and cooled typically with air, and sometimes with a fine mist of water. As the mold cools, the material solidifies. When the material cools sufficiently to release from the mold surface, the process is halted, and the product is removed from the mold.
Einar® 401 and Einar® 411 are suitable anti-static additives for demanding applications such as electronic packaging. They offer both short and long-term effects rivalling that of ethoxylated amine and amides while also providing mould release and density properties.
This exceptionally versatile technology can produce an incredible variety of products. There are thousands of rotationally molded products used in various sectors. Key areas include:
A good anti-static additive is required to deliver good and reliable anti-static performance, but it is also expected to work well as a mould release to ease processing. In the final moulded product, denesting properties are often requested and that functionality is also provided by anti-stats that lubricate the polymer surface and allow easy separation of stacked parts.
In addition to these traditional areas, there is a significant increase in demand for innovative, design-based objects, including interior and exterior artistic items, lighting, and high-quality decorative products.
Currently, the industry heavily relies on polyethylene (PE), with 97% of rotationally molded products being made from this material. Polyethylene is a versatile, easily moldable, and readily available polymer that has dominated the process. Rotomoulding is a casting technique where powder is almost always used instead of pellets, which means that the material must be ground. Polyethylene is relatively easy to grind at room temperature. The most commonly used types of polyethylene are:
Einar® 201, Einar® 207 and Einar® 306 are excellent general-purpose GMS anti-static additives for a broad range of PP injection moulding applications and will ensure clean, dust-free and attractive appearances of packaging, appliances and other household products. Recommended loading levels for homopolymer PP are 0.3 - 0.5% and for random copolymers 0.1 - 0.3%.
There are many variables that can affect production and the final product, such as ambient temperature and humidity, mold type, material specifications, and powder quality.
GETTING A QUOTE WITH LK-MOULD IS FREE AND SIMPLE.
FIND MORE OF OUR SERVICES:
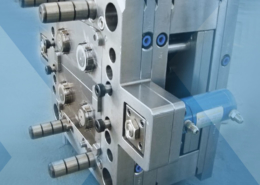
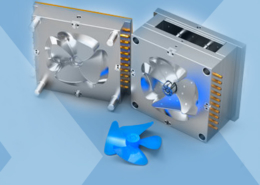
Plastic Molding

Rapid Prototyping
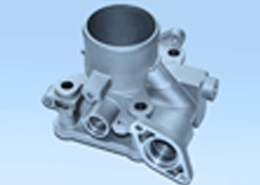
Pressure Die Casting
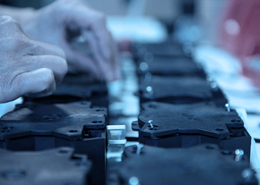
Parts Assembly
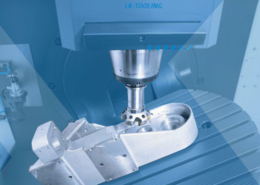