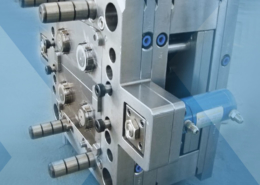
PMMA ACRYLIC INJECTION MOLDING PROBLEMS AND ... - acrylic injection molding
Author:gly Date: 2024-10-15
• Moderate volume production • Parts in 3-6 weeks • Capable of 300k+ cycles • Family and multi-cavity molds • Automatic undercut details • Automatic unscrewing molds • Fully automatic production
Yes, we have provided plastic product design services for over 30 years and have engineers on staff that are very knowledgeable about injection molded part design.
We provide injection molding services up to 1,200 tons in the US and up to 2,800 tons in Asia. The maximum part size will depend on the material selected and the part geometry, but as a general rule, injection molded parts may require 2-5 tons per square inch of projected surface area. For example, a 10"x10" part might require 200 to 500 tons of clamp force, depending on part geometry, nominal thickness, material selection and other factors.
There are 100s of available thermoplastic materials. These are just a few of the resins we stock. Many are also available with additives, like glass or carbon fibers, and fillers like talc.
We manufacture molds with all levels of complexity, everyday. Features like undercuts and internal or external threads are no problem. We can even incorporate these features into prototype molds. Molds that require multi-stage ejection, floating cores and cavities, reverse injection and ejection are all available to build your molds.
We take care to restrict access to your data/information to a need to know basis. Each customer that registers on our website is afforded these standard confidentiality terms. For more information, contact your CSE (Customer Service Engineer).
Prototype molds are constructed for use in our proprietary system and for that reason the customer does not own these mold inserts and only pays a "tooling setup fee".
Yes, 2D drawings in PDF format are acceptable for inspection and communication purposes, but cannot be used as a substitute for the 3D CAD formats listed above.
Nothing, the term "tool" is a broad term that could refer to many different types of tools or dies, but in our process it is interchangeable with the term "mold".
Yes, but selecting the plastic material for each application is the customer's choice and responsibility. We have engineers with decades of experience who can digest your requirements and make suggestions, as well as, provide technical data on various material, but in the end you will need to make this choice.
Home | Capabilities | Quality Assurance | Machines | Facility/Warehouse | Services | Customer Satisfaction | Contact Us | Employment 6247 State Route 233, Rome, NY 13440 | Ph: 315.736.2412 | Fax: 315.736.0486 | Email Sales ©2020 Molding Solutions, Inc. All Rights Reserved.
It is important to note that aluminum can become "shiny" and appear to have a mirror finish, but that does not qualify as an SPI A series finish. For this reason your average prototype mold may not actually meet your project requirements.
No, due to the limitations in accuracy associated with this file format it is not a viable option for building injection molds.
In our process, there is no tangible difference in the parts. Some prototype molders may take shortcuts, like rounding off corners or eliminating water lines in the mold in an effort to reduce costs. We do not make these compromises.
Bridge molding utilizes a bridge tool to accomplish low to moderate volumes of molded parts quickly and cost efficiently. There are small sacrifices in tool longevity with a bridge mold versus a production mold, but often times a bridge tool has more life than many projects need (300k+ cycles). Whereas rapid production molding spares no expense when it comes to tooling and is therefore the king of low cost, high-volume production injection molding.
Yes, we warehouse and maintain all molds in our possession for the life of the project. If the project becomes dormant for more than 12 months we will contact you to understand your intentions and future needs. We may charge a storage fee for molds held beyond reasonable dormant periods.
Yes, even when the design change is not a "steel safe" change. We build all of our molds from steel, as a result we can easily cut away more steel or "add" steel back in using modern welding techniques. This is a much more difficult task with aluminum and one of the many reasons we do not typically use aluminum to manufacture our molds.
Additionally, soft materials, like aluminum or mild tool steels, will not retain this "shiny" appearance after repetitive injection molding cycles. To truly provide an SPI A series finish, the mold requires special steel, like very specific grades of hardened 420SS with a very tight grain structure. Be sure to specify this finish requirement in your RFQ (Request For Quote) or discuss this with your CSE (Customer Service Engineer) before beginning your project.
• Low volume production • Parts in 2-4 weeks • Capable of 10k+ cycles • Undercuts & unscrewing details • Square corners • 55 to 1200 tons
If you need assistance with 3D CAD creation or modifying your part design for better results with injection molding, inquire with your CSE (Customer Service Engineer).
Since 1981, Molding Solutions, Inc., has consistently produced high quality injection molded components at globally competitive prices to industries that demand a greater accountability and qualification from their vendor sources. At MSi we believe manufacturing in the United States of America. is making a comeback. More often now companies that once moved off shore are "reshoring," with the confidence that American workers are more efficient, better trained and more knowledgeable. With those American standards at the core of our operation, MSI has grown to be one of the largest injection molding facilities in Upstate New York with an industry-wide reputation of delivering products at globally cost-effective prices -- with domestic supplier communication. MSi is committed to investing here in the U.S., where our manufacturing base is as strong and viable as anywhere in the world.
Rapid Molding prides itself on swift turnarounds. Typically prototype injection molding lead-times are are 2-4 weeks. Whereas bridge tooling and production tooling lead-times can run 3 to 8 weeks depending on the size and complexity of the parts. In general, we typically deliver production molds 50% to 70% faster than industry standards, ensuring your projects hit the market without unnecessary delays.
Yes, all production molds, and most prototype molds, are eligible for acid-etched textures using dozens of industry standard patterns.
No. In the 1990s we experimented for several years with aluminum molds. We found that modern high-speed machining techniques can actually remove more steel per hour than aluminum! This is due to the amount of energy released in ultra-high-speed machining. When removing high volumes of aluminum the energy actually makes the aluminum soft, nearly melting it to a liquid form. As a result the aluminum reaches a point of diminishing returns and UHS cutting of steel surpasses the removal rate of aluminum.
Yes, in 2023 we changed our branding to better reflect the full-service nature of our business, which is building rapid molds and providing rapid injection molding services.
If you need assistance making your payment ask your CSE (Customer Service Engineer) to connect you with our orders department.
• High volume production • Parts in 4-8 weeks • Capable of millions of cycles • Unlimited part complexity • Optimized automatic production • Highly competitive pricing
Yes, we are a full-service, custom injection molder, as such we offer assembly services and a wide array of secondary services from printing to sonic welding.
Absolutely! We have decades of experience with complex molding projects. We are well equipped to handle even the most intricate molds. We've successfully tackled diverse projects, providing precision and efficiency for both simple and highly complex parts.
Get prototype injection molded parts fast! With Rapid Molding you won’t break the bank doing it. Components ranging from 0.5″ x 0.5″ up to 20″ x 20″ have never been less expensive. Get a prototype injection molding quote right now, simply upload your 3D CAD file and answer a few questions.
Yes, we have several good suppliers that we partner with for retail packaging. For more information, contact your CSE (Customer Service Engineer).
Many prototype molders only apply sand or bead blast textures. While we do offer this services, acid etching is more accurate and will last for many, many more cycles.
Additionally, steel molds are much more durable, can survive fully automatic molding and are much easier to modify. If cost is driving you to consider aluminum molds, submit an RFQ and see what we can do for you.
GETTING A QUOTE WITH LK-MOULD IS FREE AND SIMPLE.
FIND MORE OF OUR SERVICES:
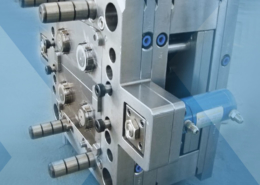
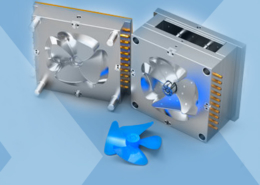
Plastic Molding

Rapid Prototyping
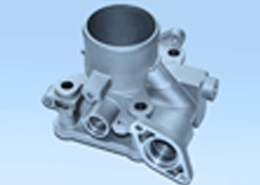
Pressure Die Casting
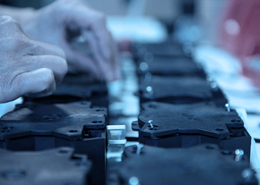
Parts Assembly
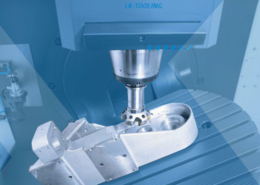